HHI Corporation Develops & Donates State-of-the-Art Mobile Triage Unit
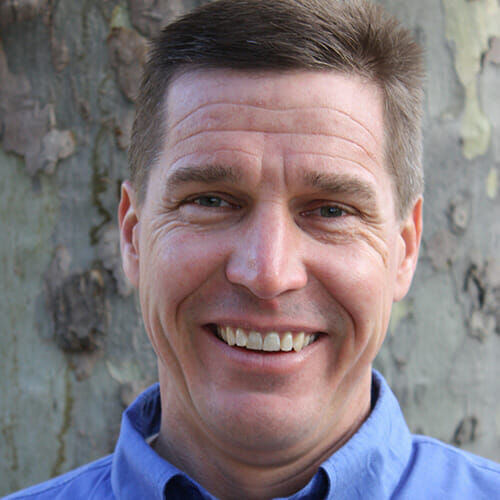
Cliff Hokanson’s parents founded HHI Corporation in 1971. Hokanson studied civil engineering at Utah State University, and during that time, he worked for a couple of years at a nonprofit research corporation that developed defense and space technologies. He joined the family business full-time in 1996. Hokanson is now the Executive Vice President of HHI Corporation, based in Utah, USA.
Before COVID-19, there was Ebola
HHI has extensive experience with precision engineering in the defense and aerospace industries, including manufacturing aircraft maintenance stands for 15 years. They’ve been doing industrial construction for 48 years for the U.S. Department of Defense and other clients. And they have 30 years of experience with biological and chemical containment.
In 2014-2016, there was an outbreak of the deadly infectious disease, Ebola, in west Africa. When American medical professionals treating Ebola patients were infected and became sick, they were flown back to the United States for treatment. However, to keep the flight crew and other passengers safe from the virus, it was necessary for the sick patients to travel inside biocontainment units called Containerized Bio-Containment Systems (CBCS).
The CBCS units had to be manufactured so that even if there was loss of pressure inside the plane, the virus wouldn’t seep out of the box and into the rest of the airplane. Working with MRIGlobal, a nonprofit research lab, HHI was tasked with designing and manufacturing these units.
“This is something that had never been done before and we had to do it in six months!” says Hokanson. “We designed it, fabricated and built it, and got it third-party tested, all in about 190 days.”
HHI built a total of four of these biocontainment pods for the U.S. Department of State. The units involve complex, precision engineering and were manufactured to a significantly higher standard than Biosafety Level 4 (BSL-4), the CDC’s highest standard for biocontainment. “The entire door system is a new invention. We had to make sure that patients would be safe, even if the units were sitting on the tarmac for 12 hours. So they each have their own power source, HVAC system, and adequate air flow,” Hokanson explains. “Medical-grade oxygen needed to be available. And the staff inside the unit needed to be able to communicate with the outside.”
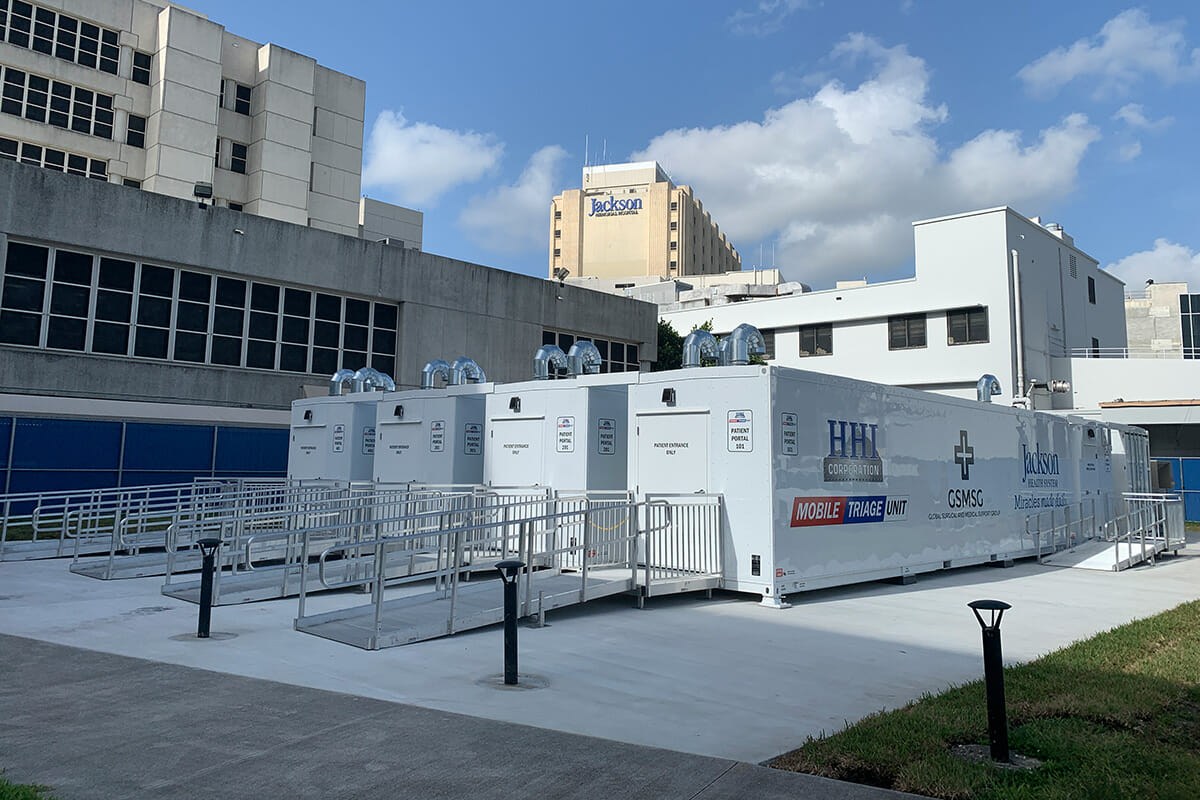
The layout of HHI Corporations' Mobile Triage Unit (MTU)—seen here outside the Jackson Memorial Hospital in Florida—includes four patient rooms with three beds each, nurses stations and support equipment. Systems include UPS power circuits, insulated wall and ceiling panels, hospital grade flooring with welded joints, two 1,500 gallon tanks for fresh and waste water, HVAC system with 18 air exchanges per hour, visual air flow sensors, single pass air system, HEPA filters, seven days of power via diesel generator, and fire alarm system with dialer. It also includes a HIPAA-approved networking package to integrate with existing hospital/medical facilities communications.
The COVID-19 Cruise Ship
Then, this year, Hokanson happened to see those same CBCS pods on TV — this time on flights bringing home COVID-infected patients from the Diamond Princess cruise ship, which had been quarantined off the Japanese coast.
He felt both proud and inspired.
HHI had the experience and skills to do something significant to help during the COVID-19 pandemic. So the team put their heads together and designed the Mobile Triage Unit. Once they developed the prototype, they got feedback and tweaked the design.
A press release from HHI describes the details of the MTU:
The layout of the MTU includes four patient rooms with three beds each, nurses stations and support equipment. Systems include UPS power circuits, insulated wall and ceiling panels, hospital grade flooring with welded joints, two 1,500 gallon tanks for fresh and waste water, HVAC system with 18 air exchanges per hour, visual air flow sensors, single pass air system, HEPA filters, seven days of power via diesel generator, and fire alarm system with dialer. It also includes a HIPAA approved networking package to integrate with existing hospital/medical facilities communications.
“I’m pretty sure the MTU is the first of its kind. It’s mobile, can be completely set-up within a couple of days, and can withstand hurricane-force winds.”
Related Listening:
Modular Triage Units for COVID-19 w/ HHI Corporation
In this episode, MBI marketing director John McMullen talks with Cliff Hokanson, Executive VP of HHI Corporation, about HHI's new Mobile Triage Units. Cliff walks listeners through the layout of the units, describes their functions, and talks about the requirements for building modular healthcare facilities.
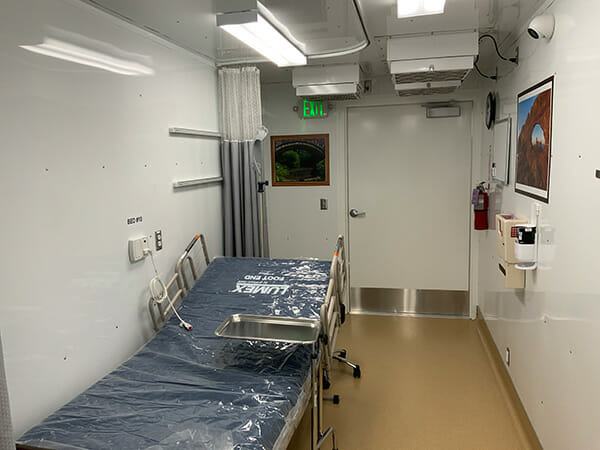
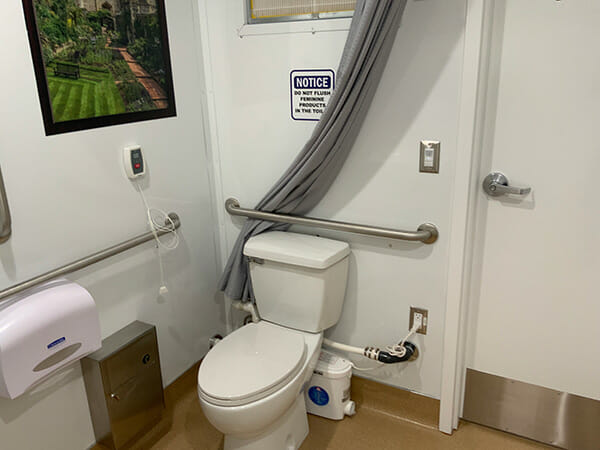
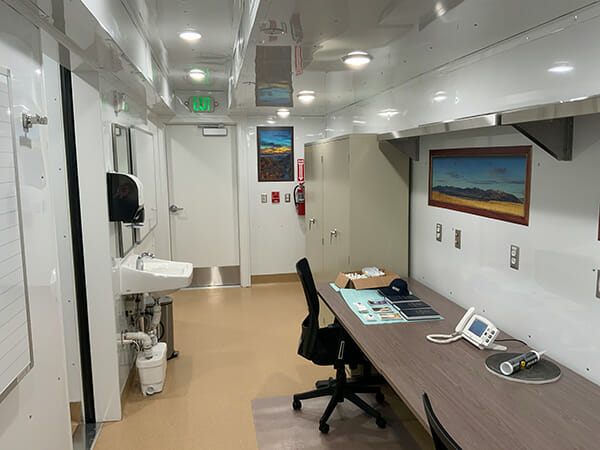
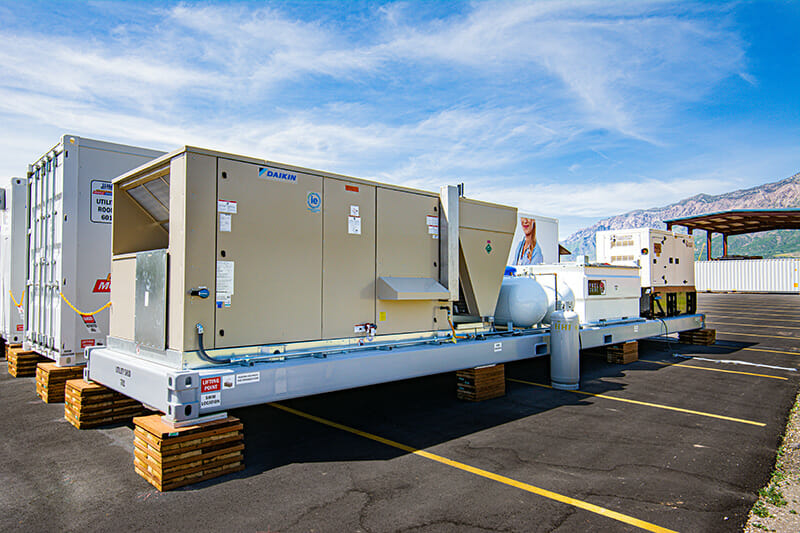
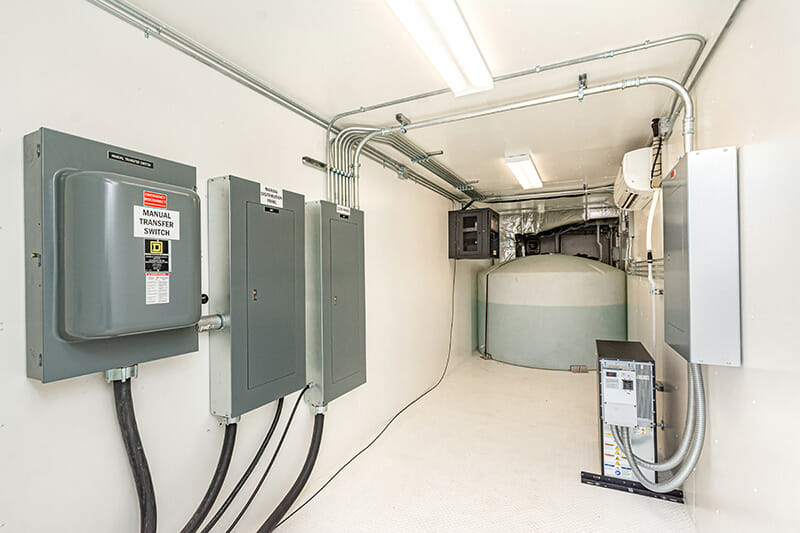
Supply Chain Challenges
Like other manufacturers, though, HHI struggled with disrupted supply chains. “Ordinarily, we have lots of suppliers for HEPA filters. These are a crucial component of the MTU because they capture the viruses as the air moves through them,” explains Hokanson. “But it was hard for suppliers to get enough of them, because factories were getting shut down and not making them.”
In fact, one of HHI’s usual suppliers was unavailable because she was sick with COVID-19 herself. Eventually, one supplier who knew what HHI was trying to do decided to put a hold on a delivery to another customer whose project wasn’t as urgent, and to prioritize HHI’s more urgent need.
“We had similar things happen for the generators, aluminum sheet stock, and flooring material,” says Hokanson. “Companies said they would work overtime shifts to get us what we needed. People really wanted to be part of this project.”
Inspiration
Instead of selling the first MTU, Hokanson decided to donate it to a healthcare facility that could make good use of it.
“I’m sure later in the year my accountant will say, ‘What were you thinking? Don’t you know how to add!’” laughs Hokanson. “But I believe in inspiration and I was inspired to donate it.”
Hokanson sent out an email to all his contacts and asked them to email all their contacts to find a suitable recipient for the MTU. In the end, HHI selected the Global Surgical Medical Support Group. The Jackson Memorial Hospital in Florida is housing the unit — and the medical staff are thrilled with the state-of-the-art addition to their facility.
HHI has a couple more MTUs that are close to completion. They’ll be ready to deliver in less than 6 weeks. Hokanson notes that we were unprepared for this pandemic, even though experts had been warning us for years. The MTU is a way that healthcare systems can be better prepared for outbreaks of future infectious diseases — as well as helping them cope this time around.
The MTU can also be used for other health crises — hurricanes and earthquakes to car accidents and mass shootings. They’re built to withstand hurricane force winds up to 185mph (298km/hr), and are designed to comfortable in outside temperatures between -20F to 110F (-29C to 43C). If necessary, they can be self-sufficient at full capacity for up to 7 days.
“We built it. But it’s inspiration and a lot of collective brainpower that made it happen.”
About the Author: Zena Ryder is a freelance writer, specializing in writing about construction and for construction companies. You can find her at Zena, Freelance Writer or on LinkedIn.
More from Modular Advantage
Samantha Taylor: Leading the (Modular) Design of Tomorrow
“With modern technology and the way we’ve all embraced things like BIM, file sharing, and video conferencing since COVID, it’s easy to collaborate with companies in Austria, or Singapore, or anywhere else in the world.”
Greg DeLeon: Military Engineering to Modular Design
Greg DeLeon, a structural engineer at ISE Structural Engineers in Temecula, California, can tell you not only how large a beam needs to be to support a house, but also how much explosives you’ll need to take it down, thanks to his unique combination of professional and military experience.
To Remake North Minneapolis, Devean George Swaps Basketball for Buildings
He’s lived in Los Angeles, Dallas, and San Francisco (to name a few). He’s delivered championships with the Los Angeles Lakers and made career-defining moves with the Dallas Mavericks and the Golden State Warriors. No matter the wins, the championships, or even the seemingly impossible 3-pointers, Devean George has always returned to where it all started for him: Minneapolis.
Chelsi Tryon: Making the World a Better Place
For Chelsi Tryon, Director of Environmental, Social, and Governance (ESG) for WillScot Mobile Mini, nothing is more enjoyable than increasing the
company’s sustainability efforts while simultaneously doing her bit to save the environment.
Joshua Hart: Pushing Boundaries
Joshua Hart, P.E., vice president at Modular
Solutions, can sum up his job responsibilities in one sentence: “I do whatever needs to be done.” Hart thrives on the variety and the opportunity to be involved in every aspect of the company. And it shows! You might say Hart has come full circle.
Jamie Metzger: From Construction to Apparel and Back Again
Growing up in a blue-collar city like Edmonton, Alberta, Canada, it’s no surprise that Jamie Metzger spent some time working labor jobs on construction sites. It’s one of the most common summer jobs in the city. But that’s probably the last predictable thing about this particular story.
Victor Masso: Expanding Modular in Puerto Rico
Victor Masso joined 2 Go Storage, a company started by his grandfather and father, in 2018 to develop a modular building division in the wake of the devastation caused by Hurricane Maria in 2017. Prior to joining the company, he had worked in the industry for about four years focusing on pharmaceutical, commercial, and government projects.
Eliyah Ryals: Finding the Perfect Fit
It’s not common for people to find their perfect career fit straight out of college. It’s even less common to find it in the town you grew up in. But that’s exactly what happened when Eliyah Ryals was told about vacancies at Panel Built and made the decision to apply.
Through It All, It’s Still About the Workers
By February 2024, the number of available, unfilled construction job openings had reached an all-time high. At some point, interest rates will fall, creating another surge in demand for such workers. In short, solving the nation’s skilled worker shortage issue has never been more important.
Navigating Insurance Challenges in the Modular Construction Industry
Utilizing practical written minimum insurance and indemnity requirements, along with monitoring certificates of insurance by someone who has COI training will not yield a perfect risk transfer strategy, but the exposure will be managed much better than it likely is currently.