Modular Construction to the Rescue!
The Inspira Oncology Center in Woodbury, NJ urgently needed to service cancer patients in the surrounding communities. The decision to develop a new type of facility comprised of modular technologies allowed for a faster construction to more quickly deliver medical treatments to those in need. It was determined early in the design process that the patients and their families’ health and comfort would take precedence. Considering the schedule and the speed at which the center would start providing services, the owners concluded the facility could be designed to reflect a higher level of design and construction quality.
The oncology center was comprised of various spaces common to most medical facilities such as offices, reception area, conference rooms, waiting rooms, exam rooms, lounge and supporting facilities. The center was given an open feeling by using a clerestory and entrance curtain wall to maximize natural lighting. Innovative and attractive facades were implemented around the exterior of the building to advance the buildings aesthetics. Unique art sculptures were commissioned and located around the facility amongst the beautiful landscaping surrounding the center.
Additionally, this center included a CT SIM Room to allow for quicker patient imaging at the center and a LINAC Room to conduct proton therapy where high energy x-rays or electrons are used to combat tumors and destroy cancer cells. Specialized control rooms adjoining the respective therapy spaces were incorporated in the construction.
Sustainable Modular Management Inc., with support from fabricator Southeast Modular Manufacturing, was able to work with Inspira Health Network Group to design, develop, and finally construct a highly technical, sophisticated, innovative and welcoming medical center in less than one year!
This article originally appeared in the Modular Advantage Magazine - Second Quarter 2019 released in May 2019.
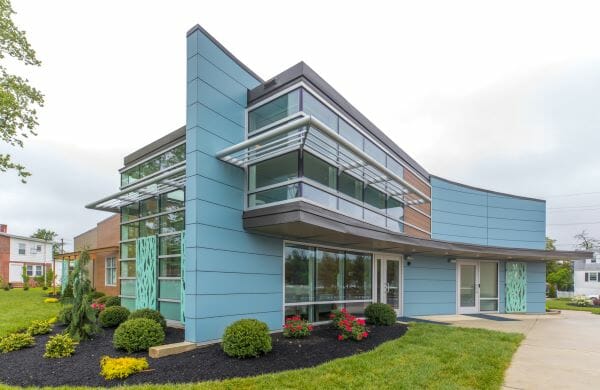
Exterior of the Inspira Oncology Center / Source: Sustainable Modular Management Inc.
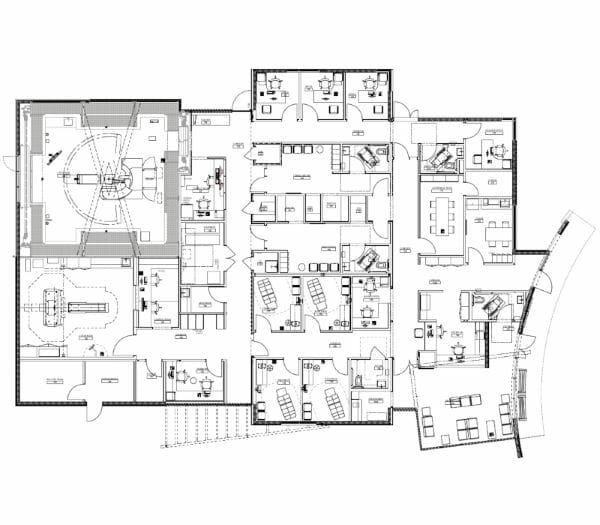
Floorplan of the Inspira Oncology Center / Source: Sustainable Modular Management Inc.
More from Modular Advantage
Samantha Taylor: Leading the (Modular) Design of Tomorrow
“With modern technology and the way we’ve all embraced things like BIM, file sharing, and video conferencing since COVID, it’s easy to collaborate with companies in Austria, or Singapore, or anywhere else in the world.”
Greg DeLeon: Military Engineering to Modular Design
Greg DeLeon, a structural engineer at ISE Structural Engineers in Temecula, California, can tell you not only how large a beam needs to be to support a house, but also how much explosives you’ll need to take it down, thanks to his unique combination of professional and military experience.
To Remake North Minneapolis, Devean George Swaps Basketball for Buildings
He’s lived in Los Angeles, Dallas, and San Francisco (to name a few). He’s delivered championships with the Los Angeles Lakers and made career-defining moves with the Dallas Mavericks and the Golden State Warriors. No matter the wins, the championships, or even the seemingly impossible 3-pointers, Devean George has always returned to where it all started for him: Minneapolis.
Chelsi Tryon: Making the World a Better Place
For Chelsi Tryon, Director of Environmental, Social, and Governance (ESG) for WillScot Mobile Mini, nothing is more enjoyable than increasing the
company’s sustainability efforts while simultaneously doing her bit to save the environment.
Joshua Hart: Pushing Boundaries
Joshua Hart, P.E., vice president at Modular
Solutions, can sum up his job responsibilities in one sentence: “I do whatever needs to be done.” Hart thrives on the variety and the opportunity to be involved in every aspect of the company. And it shows! You might say Hart has come full circle.
Jamie Metzger: From Construction to Apparel and Back Again
Growing up in a blue-collar city like Edmonton, Alberta, Canada, it’s no surprise that Jamie Metzger spent some time working labor jobs on construction sites. It’s one of the most common summer jobs in the city. But that’s probably the last predictable thing about this particular story.
Victor Masso: Expanding Modular in Puerto Rico
Victor Masso joined 2 Go Storage, a company started by his grandfather and father, in 2018 to develop a modular building division in the wake of the devastation caused by Hurricane Maria in 2017. Prior to joining the company, he had worked in the industry for about four years focusing on pharmaceutical, commercial, and government projects.
Eliyah Ryals: Finding the Perfect Fit
It’s not common for people to find their perfect career fit straight out of college. It’s even less common to find it in the town you grew up in. But that’s exactly what happened when Eliyah Ryals was told about vacancies at Panel Built and made the decision to apply.
Through It All, It’s Still About the Workers
By February 2024, the number of available, unfilled construction job openings had reached an all-time high. At some point, interest rates will fall, creating another surge in demand for such workers. In short, solving the nation’s skilled worker shortage issue has never been more important.
Navigating Insurance Challenges in the Modular Construction Industry
Utilizing practical written minimum insurance and indemnity requirements, along with monitoring certificates of insurance by someone who has COI training will not yield a perfect risk transfer strategy, but the exposure will be managed much better than it likely is currently.