What is an Air Balance? The Comfort Zone
An "air balance" is a useful process for measuring the performance of a simple or complex hvac system, and for providing the occupants with a comfortably conditioned space. To understand how this process works, let's first look at the different types of air balance by defining the two extremes: Comfort Balance and AABC Certified Air Balance.
A "comfort balance" is simply checking to see whether the room feels comfortably conditioned. It may be as easy as walking from room to room, holding a hand up to the ceiling to see if sufficient air is coming out of the registers, and asking the occupants if they are comfortable. If they are not, your journey starts to discover how to resolve the HVAC problems associated with the situation. It may involve adjusting/moving registers, installing restrictors/dampers after the fact, or just insuring the air doesn't blow directly on an occupant. Many occupant complaints are associated with air circulation: too much and too little.
At the other end of the spectrum is the AABC Certified Air Balance. The purpose of this type is to insure all components of the hvac (heating, ventilating, air conditioning) system are working in harmony, at their optimum performance, providing total occupant comfort. While the journey toward a certified air balance starts before the testing stage, let's begin ours with the mechanical engineer.
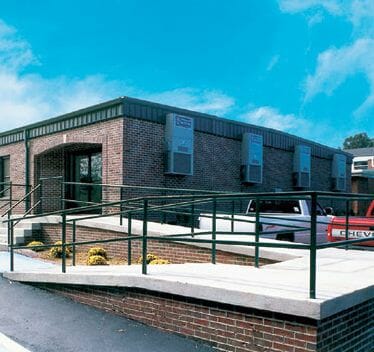
A mechanical engineer develops specifications and a set of mechanical drawings from a mix of occupant desires, local codes, ASHRAE standards, and many years of training. The correct ducting, airflow, registers, and unit performance are brought together with consideration for ventilation requirements and building exhaust needs.
The most important part of the mechanical plans used by the certified balance company is the list of "cfm" requirements next to each supply, return, intake, exhaust and ventilation opening. Without this important information a certified balance is not possible.
To conduct an AABC Certified Air Balance, the building must first be totally sealed/enclosed. Therefore this process would fall under the modular dealer's scope of work. If your project is complex, or your customer includes a certified air balance in the bid specs, be sure to include the following cost allowances on the front end:
- A mechanical engineer
- A system with products capable of a certified balance
- The cost for a balancing company
- An HVAC contractor on site during balance.
The HVAC contractor is advisable because, according to their association, a true AABC certified balance contractor must not be affiliated with any mechanical contractors, design engineers, or equipment manufacturers. So if the HVAC unit needs service during the air balance process, and an HVAC contractor is not on site, the balance will most likely stop.
A total air balance requires an opposed blade damper (OBD) behind the face of each intake and exhaust opening in each room and of the building. Other balancing dampers are required at all branch locations of the duct system.
At the building site prior to occupation, the certified balance technician will change all of the filters in the system, and insure that all dampers are fully open. Readings are taken at every opening inside, on the roof, etc. Slowly the dampers are closed in an effort to meet the cfm requirements set by the mechanical engineer. Adjusting one damper changes the cfm at all other openings. The air balance technician returns to every opening, making new adjustments and readings based on the changes from the previous one. Registers, grills, exhaust fans, and fresh air must all "balance" to meet the system performance requirements.
After the technician believes the system is all in tune, he locks down all of the dampers and other devices, so that the settings will not change. While this should keep the system "balanced," the system can be thrown out of balance by such things as dirty filters, the occupants changing the register setting, office remodeling, and reconfiguring registers and ducting.
The cost to do an AABC Certified Air Balance ranges from $75-150 per opening. You're paying for time, labor, expertise, equipment, and a Certified Balance Report. A building with five supply openings, five return openings, one exhaust fan, and one OSA intake has 12 openings to verify. Depending on the complexity and location of the openings, you can expect to pay $900-$2,000 for an AABC Certified Balance.
Is it worth it on large projects? Definitely. Remember, to avoid wasting money on your balance, be sure to install registers that the occupants cannot adjust.
Hiring a good air balance company with skillful technicians is also important. Visit www.aabchq.com for more information on the Associated Air Balance Council and a member list. The website also lists the requirements for membership, the types of certified technicians, their code of ethics, and their performance guarantee.
We have looked at the simple and the perfect air balance types, just hitting the high spots toward explaining certified air balance requirements and results. This understanding may help you avoid the temptation to put only $50 in your bid when you see your customer specifications requiring an AABC Certified Air Balance. The $50 only covers the cost of the "waving the hand" comfort balance.
More from Modular Advantage
Samantha Taylor: Leading the (Modular) Design of Tomorrow
“With modern technology and the way we’ve all embraced things like BIM, file sharing, and video conferencing since COVID, it’s easy to collaborate with companies in Austria, or Singapore, or anywhere else in the world.”
Greg DeLeon: Military Engineering to Modular Design
Greg DeLeon, a structural engineer at ISE Structural Engineers in Temecula, California, can tell you not only how large a beam needs to be to support a house, but also how much explosives you’ll need to take it down, thanks to his unique combination of professional and military experience.
To Remake North Minneapolis, Devean George Swaps Basketball for Buildings
He’s lived in Los Angeles, Dallas, and San Francisco (to name a few). He’s delivered championships with the Los Angeles Lakers and made career-defining moves with the Dallas Mavericks and the Golden State Warriors. No matter the wins, the championships, or even the seemingly impossible 3-pointers, Devean George has always returned to where it all started for him: Minneapolis.
Chelsi Tryon: Making the World a Better Place
For Chelsi Tryon, Director of Environmental, Social, and Governance (ESG) for WillScot Mobile Mini, nothing is more enjoyable than increasing the
company’s sustainability efforts while simultaneously doing her bit to save the environment.
Joshua Hart: Pushing Boundaries
Joshua Hart, P.E., vice president at Modular
Solutions, can sum up his job responsibilities in one sentence: “I do whatever needs to be done.” Hart thrives on the variety and the opportunity to be involved in every aspect of the company. And it shows! You might say Hart has come full circle.
Jamie Metzger: From Construction to Apparel and Back Again
Growing up in a blue-collar city like Edmonton, Alberta, Canada, it’s no surprise that Jamie Metzger spent some time working labor jobs on construction sites. It’s one of the most common summer jobs in the city. But that’s probably the last predictable thing about this particular story.
Victor Masso: Expanding Modular in Puerto Rico
Victor Masso joined 2 Go Storage, a company started by his grandfather and father, in 2018 to develop a modular building division in the wake of the devastation caused by Hurricane Maria in 2017. Prior to joining the company, he had worked in the industry for about four years focusing on pharmaceutical, commercial, and government projects.
Eliyah Ryals: Finding the Perfect Fit
It’s not common for people to find their perfect career fit straight out of college. It’s even less common to find it in the town you grew up in. But that’s exactly what happened when Eliyah Ryals was told about vacancies at Panel Built and made the decision to apply.
Through It All, It’s Still About the Workers
By February 2024, the number of available, unfilled construction job openings had reached an all-time high. At some point, interest rates will fall, creating another surge in demand for such workers. In short, solving the nation’s skilled worker shortage issue has never been more important.
Navigating Insurance Challenges in the Modular Construction Industry
Utilizing practical written minimum insurance and indemnity requirements, along with monitoring certificates of insurance by someone who has COI training will not yield a perfect risk transfer strategy, but the exposure will be managed much better than it likely is currently.