Designing One of the Nation's Largest Modular Multifamily Housing Structures w/ Cuningham [podcast transcript]
Designing One of the Nation's Largest Modular Multifamily Housing Structures w/ Cuningham
Dave Stahl, associate AIA and principal at Cuningham, joins the podcast to discuss the design of Pentagon Village Apartments, a 244,000-sqft rental community in Minnesota which is on track to become one of the largest volumetric modular multifamily developments in the country. Dave talks about how his designs evolved from the project's inception, how the building's modular construction influenced the façade, and his team's goals for the project in general.
Dave also gives advice to designers entering the industry and looks ahead to the possible modular design trends of the next few years..
John McMullen
Hello and welcome to Inside Modular, the podcast commercial modular construction, brought to you by the Modular Building Institute.
Welcome everyone. My name is John McMullen and I'm the Marketing Director here at MBI. Today I'm talking with Dave Stahl, associate AIA and principal at Cuningham. Dave is here to talk about the design and development of one of the largest multifamily volumetric modular projects in the country.
Dave, thanks for being here.
Dave Stahl
Thanks for having me. I'm very excited.
John McMullen
So, tell me about yourself. Dave, what's your background? And how did you get started as an architect?
Dave Stahl
So, I started actually in engineering and found that while doing the math, I often doodled on the side and thought, why am I swimming upstream? Let's explore the art side more and very glad I did that.
I went into architecture and graduated about 28 years ago. So I've been doing this for a while. I've always been at the front-end design side. I think that engineering spirit actually helps Well, in the genre I work in I work in multifamily, which is about numbers and how to do things efficiently and where to focus our design efforts and where other things that work well to repeat them.
So, actually, what's interesting is the modular aspect plays into it very well, it is how do we make this machine work and versus trying to make the machine fit, predestined vision that we had before. So that's kind of my architectural background.
I've been with Cunningham for 18 years in two different stints. I started here, had to look out a different window for a while, like all of us need to do and like so much I came back.
John McMullen
Well, that's awesome. I love the story about doodling in the margins while you were in math class. That was the entirety of my career in math class: doodling. Which leads me to ask, were there any new skills or techniques that you needed to learn going from engineering into architecture? Did you have to rethink everything was could you apply a lot that you had already learned?
Dave Stahl
I think a lot of the skill sets and I've told this to most engineers, I know and architects, it's like, you could probably you have the skill sets within you to probably do either one. It's whatever your interests dry you. My wife's a graphic designer and does a lot of things. And I tell her it's like, there's again, a lot of overlap and skill sets, there are nuances and details specific set.
Like, for instance, if I had to calculate the load carrying capacity on a beam today, I might have to reference a book or two to get through that. But I do think it's a, we you come with a set of skills that then get honed as you practice or go to school. So, I think I had most of them. And I just am a lot happier doing the creative front end versus figuring out what others have done.
John McMullen
I hear you. So how about modular design? Did you start out with that? Or was that something that you had to add to your toolkit as you went on?
Dave Stahl
Well, it's new-ish to my world, I think the first modular building I looked at with a group was probably three years ago. So it's not like I have this 20 years back. So like any good designer, it's learning the skills and what that specific modular fabricator did. And instead of trying to form it to my whims, it's learning. What is it that this does well, and let's propagate that and make sure we express that because that's where you're gonna get the advantages.
So, did that but right now, like you mentioned, we have a large one under construction, finally, huzzah! But I've probably done half dozen to eight buildings quite thoroughly, that three are hopefully starting and the rest, you know, we're one of those “Oh, that was a good exercise.” And for reasons A, B and C, don't go forward.
John McMullen
Well, let's talk about the project that you're working on, the very large modular multifamily project. Tell me about how that project evolved, how it started, what was your goal, and how was that project coming along?
Dave Stahl
So, it started via an architectural RFP. They asked a number of firms to propose an interview. I think what gave us the advantage is I was looking at a different modular project in a different city with a developer and was they were looking at Rise Modular, the developer for the project, and work on they were looking at using their factory.
So, before I got started, I talked to the folks there and said, “Give me the beats. What do I do?” Well, what should I do? What should I not do, and kind of learned and we looked at a bunch of different options, some that fit the modular cell that they used well, others, they even explored, like a California wrap around a parking structure. And I remember going well, this is certainly a round peg getting jammed in, too, as well. I'm betting This one doesn't pencil. And sure enough, because you could only use half-length mods, we lost a lot of advantages, but it was an exercise.
Anyway, I got to know the folks at Rise comfortably enough. So, when we went in to the interview, we I knew the right questions to ask, I knew what their strengths were. And then we could spend the time actually getting a couple of steps ahead, for instance, saying, if you're giving me free reign, my whole goal is to give you a building that people say that's a lovely building. And then afterward when you say that's modular, they no kidding. I wouldn't have guessed that. That's my whole goal. Yeah, versus saying yes, I can see it the way it's put together.
John McMullen
So tell me about the building specifically. Where is it? How many mods are in it? What's the overall shape and size of it?
Dave Stahl
Okay. Yep, it's in Edina, Minnesota, in the kind of, for those that maybe local, it's the intersection of highways 494, and 100 will be visible from the highway, which is always nice. For those of us that have projects. It is 205 mods, and I believe 210 units. A lot of it is not micro units, for instance. A lot of them have multiple, like they're two or three mods wide for units.
So, it is a market rate has two bedrooms, one bedrooms and efficiencies. And…trying to think…it's a podium project. It's five storys over a precast base for the parking is contained. On top of that podium is a lovely pool amenity deck. And the shape of the building is essentially an asymmetric H shape, almost the sea. But just again, we wanted to make sure that there was articulation and braking. So, of the three wings, the central one that connects to it is pulled back to give some articulation along the street edge make for a better pedestrian experience.
John McMullen
Did this building go through several iterations? Was it always sort of conceived of as that shape?
Dave Stahl
Well, there was a master plan that roughly denoted you know, the overall extents of the building, it could have been a C, it could have been two L's you know, there was some of that. But early on, we wanted to make sure that there is some efficiency. So for instance, two L shaped buildings on a podium means two different sets of elevators, extra stair towers required that sort of thing. So we kind of knew it wanted to be one building. And which way the podium oriented, do we want it facing south in the sun? Or did we want it facing toward the rest of the development? This is part of a larger master plan that'll include hotels and restaurants and things. So there was some talk, but we landed on it relatively quickly, because there was a lot of that makes sense.
John McMullen
So, what was the process of working with the guys at Rise Modular? They’ve been on this podcast; they're great guys. How did you and your team at Cuningham interface with him? What was that process like?
Dave Stahl
Well, it's actually been really comfortable. Because we all have the end goal in mind to build a nice project, optimize the efficiency of the system they've come up with. We toured the site, I know what it does well, and it's been great. Because we do have that same goal. So whenever there are, huh, this isn't working well, instead of saying, Well, that's what I drew. And we're gonna stick with it. Like, some architects are kind of known. It's like, okay, well, let's work this out and what else you got? Because here are the drivers, let's make sure that we keep those in mind. But how do these buildings, for instance, intersect one wing to the next? There's six ways to do that. Let's come up with one we both like. So, it's been a lot of fun.
And even we've had a former coworker, coincidentally, left here and started working there. Shortly before we got the project, and it's just another friendly face that you're comfortable They left on good terms, you know, people check things out. So, it's been really, it's been very comfortable.
John McMullen
Awesome, awesome. Tell me about the exterior design features on this project. I mean, you made some very cool choices. How are your design choices affected by this project being modular? Or were they?
Related Reading:
Mayfair: A Modular Case Study
Previously used as a surface parking lot for commuters accessing public transit, the Mayfair development on a city-owned block in El Cerrito, Calif. brings 223 new housing units to a long-neglected stretch near the El Cerrito del Norte Bay Area Rapid Transit (BART) Station.
Named for the grocery chain that once occupied the block, The Mayfair project received its first stacked module unit October 2020 and reached its full building height of six stories after ten days of assembly.
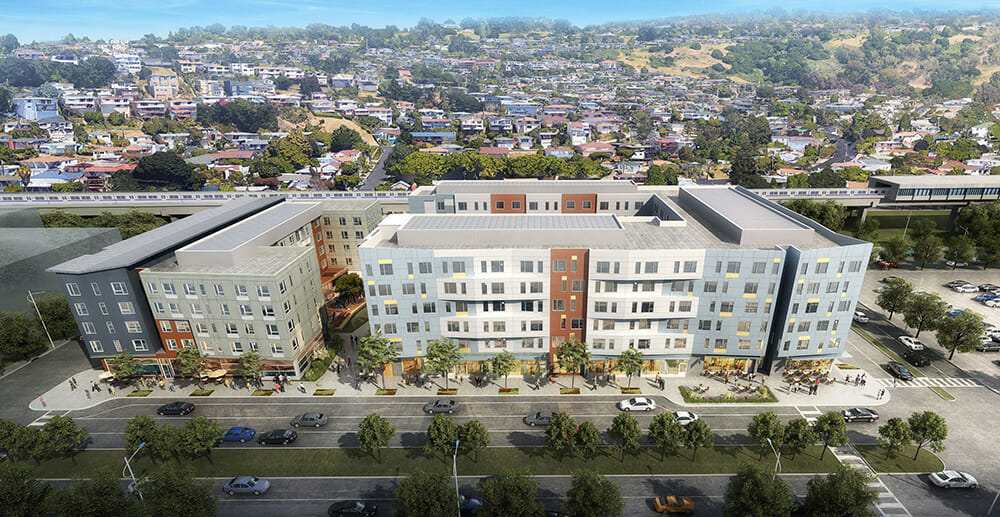
Dave Stahl
Well, there are. So, for instance, early on talking to rise, we talked about exterior facade, and we wanted to make sure there was articulation, because there are some prototypical modular buildings that are simple. And we wanted to make sure there was enough articulation. But on the other hand, you know, this is a multifamily building and its revenues generated by the rent. So you can't build something that you can't pay for, like, for instance, a hospital pays for itself by the beds inside and what's going on. There are realities, if it costs more than you can ever get rent, guess what building doesn't get built?
So, our first generation did every mod, kind of did a stagger back and forth, like, oh, wow, no one's ever going to know this is modular? And just how all of those outside edges would have to come together. Can you do it? Yes. Was it a good use and optimizing how they go together? No. So we focus it, where does your eye go in most buildings, they go to the corners.
So, we have some simple fields. And all of our attention and articulation goes toward the corners. So we have brows and we have some vertical moves that are built after the fact on the outside, again, with the intent to if you can now, realize this as modular we haven't done enough. So that is the nice thing the mods want to be is done is they can be, but the skin, at least with the rise version is done afterwards. So you cover all the seams, you can do moves that span multiple mods and blur that area behind. So I guess, to repeat: articulation happens at the corners. And then the way the wings meet, we spent quite a bit of time on how they bumped up into each other because we wanted to make sure that we weren't covering rentable square footage with other excuse me, other rooms, and we wanted to kind of a light touch so it's almost throats down to Skyway-like connections, although there is rentable space there, but we wanted to kind of narrow it down. Again, maximizing how the mods intersect.
John McMullen
What stage is this project in now?
Dave Stahl
So they are starting to fabricate the mods. And here's some Rise tidbits, a refresher if they've already been on, but it takes about 13 days, I'm told, between start of rough pieces to completed mod. While it's 13 days start to finish, their goal is to a day. So that's the route they come on, they have a large space, they essentially get like a boat wrap, shrink wrap, and they get set outside, right in their facility and wait for the time.
They have started the podium. We're still about I believe it's a month or two away from setting mods. But when the mods do come, they're hoping to get between 10 and 12 a day. And they're going to build it with the center link wing first, and then build the left and right afterward because building vertical…they prefer that versus doing all one level and then going to the next…I think it's basically the race to get the roof on.
John McMullen
Gotcha. With your experience—and you have a lot of it both with modular now and with regular stick built—what are the differences from your perspective, from an architecture point of view and designing traditional stick-built versus modular…What skills have you picked up? What skills have you realized maybe you don't use as much…What's the what are the differences you’ve found?
Dave Stahl
Well, I'm planning ahead. It's I can't emphasize how certain things we've all heard of projects being fast tracked where you get the foundation permit and you go and you're still designing some of the upper parts. We can certainly get going on some of this but since there is no “in the field, we'll get to that later”, they're putting as much in the mods including light fixtures and appliances and everything as much as they can get in and ship it to. Whether that helps because it's less in and out there less cleaning and that sort of thing afterward. It's really getting your ducks in a row before you run the “Ready Aim Fire” really applies because we've all had clients where it's “ready fire aim”, and “we'll figure it out…we have a good crew, we’ll get there.” Planning ahead. Absolutely getting it all figured out, then going,
John McMullen
Are there differences with a big modular structure like this one—using just over 200 mods, it's a huge place—designing a big structure like this versus smaller projects, are there differences in how you design for those?
Dave Stahl
So most of the ones that I personally have been working with have been of a larger scale, and that but I can, just knowing what is going along. There are things about, you know, you want artistic articulation. But the unit behind that should be repeatable. And like I said, you since you have to plan out everything, it would be nice not to have a onesie-twosie unit like this is a unique one. And we took just as long time versus the one next to it that there's a lot of so our opposite corners, you can't see them at the same time, have the same units and articulation and it because we wanted to get some mileage out of that planning and thought process and that sort of thing.
Again, it's about efficiency. We have our areas that are unique, our amenity spaces, our entries, the areas where everyone comes together, all unique when it comes to the unit's hey, if that one bedroom works great there. Let's not have 10 different plans for one bedrooms, let's have two.
John McMullen
What was the biggest challenge for this project? I mean, obviously, it's a very big and required lots of planning and coordination, the “Ready Aim Fire” as you put it. But was there a specific obstacle that you needed to figure out how to overcome?
Dave Stahl
To me the hardest was you don't have to match the units across the corridor. Because and I don't I don't mean to repeat what your audience knows. But the mods typically are semi-truck trailer size, and typically spanned from outside wall across the corridor to opposite outside wall.
The part that was new going from a traditional multifamily world was you don't have to have this exact same unit across the way. But those party walls in that mod do have to line up and the way they drop in. So making sure as you go down a hallway and turn a corner. Everything on both sides works together. And sometimes like “Oh, it'd be great. Well put the stair here. Oh, wait, the stair towers, you know, four feet thinner than the mod needs to be. So let's reconfigure it so we're using the space.” So, I think that was where at the beginning. Most of the mental gymnastics were happening. It's kind of like optimizing your Tetris.
John McMullen
What were some of the takeaways that you took from this project? And what are you going to apply next time you do one of these large multifamily buildings?
Dave Stahl
Certainly not reinventing the wheel again. So, there are some units that are fantastic. In the future of projects, I'm hoping that we can use them again and everything stays the same. And the, you know, there might be a change to how the mods are made. And there's an improvement. But there's some that it's like these are worth doing again. So take Yeah, taking the best parts, and then building on that and continually improving. So I look forward to getting some mileage out of some that were, you know, you put a lot of thought into it. And they're very nice.
John McMullen
Very good. What advice do you have for architects, designers, maybe even engineers who are looking into the modular industry, do you have any words of inspiration or warning?
Dave Stahl
Well, I do have a little event that happened some years ago. And when I was going through this modular process, I'm like, this follows this trajectory quite well. And I'll try to be super brief.
About 20 years ago, the Minnesota AIA had a competition out at the Mall of America for a Lego competition, you know, they call up all the bigger architecture firms and said, Come on out. And what you're gonna build is you're gonna build a bridge. It has to be it has to span 18 inches. That's it.
Other than that, you can do whatever you want. And it's like, okay, well, what will you have was my first question. Oh, we'll have this huge pile of every conceivable part you want and like, “Okay, will you have just the standard bricks, the two by four?” You know, day one, like, “oh, yeah, we'll have those two color coordinated.” Like, all I needed to know. So we got back, we planned a very elaborate, very strenuous hike, it had a s curving thing. There wasn't a straight line on it. But we knew our commodity pieces that two by four brick was on constant. And we planned around just that everything we had to do. And we printed out plans that were to scale. So we could just go on top of it, there was no “What should we do? I think we should do this.” We had pre planned.
So the day of the event, we hit the ground running, and within minutes already had things building up where most teams were discussing and looking at what pieces could do it. To cut to the end. We creamed everybody. There wasn't even a close second, because it was that plan plan plan, then we planned, than we did it.
So the advice would be whichever modular manufacturer are working with, and they are the drivers, learn their system, figure out what they do what it does best, and embrace it. Optimize, go with that, versus “Hey, have you ever tried doing an L shaped mod? Because I have this idea…” No. That's you're just going to take time and money and stuff like that really make a good? And like I said, with that simple, the boring, the most boring Lego piece we had far and away the most interesting design, because we figured out how to use it in a fun way.
John McMullen
Well, I love that story. I think it's great advice, I was really concerned there that they were going to have no two by four bricks. And you'd have to invent something on the fly. But I'm glad your story had a happy ending.
Dave Stahl
Yes. And very applicable to a good trajectory for a modular building: embrace it, live it, don't try to “Hey, you know, it'd be cool…Let's try something different.” If they suggested and you work together, great, but for the most part, they're set up for some pretty straightforward approach. You use it to its advantage.
John McMullen
So now that you've been in the industry for a little while, you've done several modular designs, you got some on the horizon…Do you foresee any changes in designing for modular over the next few years? Are there trends that you see coming or going? What's your, what's your fingers in the wind sense?
Dave Stahl
Right now, what's really nice about modular projects is, they're built in a controlled environment. You can you can build a car in a parking lot by laying the pieces out, but it's a lot nicer to do it inside with everything organized, and that sort of thing. That's really nice.
Now, that being said, the quality goes up, because the workers are doing the same kind of approach. If you're making cookies, if you're doing 100 of them, you're going to be more consistent than “Hey, this is my first batch, let's see how they turn out.”
I look forward to when some of that might become automated, and therefore offer some more complexity. Because right now, complexity does slow down the process. Let's say you want to chamfer to an outside wall, you can certainly do that. But it's not what the crew is set up to do. And it's a unique thing. I'd like to see some more unique mods that if they if there were certain steps in the process that were automated, would become then much more easy. That would be nice. And also right now, due to how you want self-contained and quality…There's quite a bit of material. It has to be strong. It has to be shipped transported.
It would be nice to see if some very smart engineers, smarter than me, could look at it. And oh, you know, “We can get it just as strong by eliminating 10% of the wood” still because right now, it's beefy. But that's, you know, it does come at…It's about speed. It's not how do you build the building cheaper. It's how do you build it faster? It would be nice. And I do think it will go that way. Once we get the system down better. We'll start optimizing materials and things like that.
John McMullen
Well, I just want to thank you for your time. Thank you for joining MBI I thought this is a great conversation. I can't wait for the completion of your project. I'm looking forward to seeing much more from you and from Cuningham in the months and years to come. Thanks again.
Dave Stahl
Well, thank you very much. It's been a real pleasure.
John McMullen
My name is John McMullen. And this has been another episode of Inside Modular: the Podcast of Commercial Modular Construction. Until next time.