Leading the Way with ICC/MBI Offsite Construction Standards: An Interview with Brian Hilderbrand of the Virginia Department of Housing and Community Development
As the demand for housing and infrastructure continues to outpace traditional construction methods, Virginia has taken proactive steps to modernize its building processes by embracing modular construction. One of the most significant milestones in this effort was the state's early adoption of the ICC/MBI Offsite Construction Standards—a move that has positioned Virginia as a national leader in the offsite construction sector.
A Strategic Move Toward National Consistency
Virginia's decision to adopt the ICC/MBI offsite building standards stemmed from a desire to address two of the most pressing challenges in the building industry: housing affordability and production capacity. Offsite construction, particularly modular methods, offers a scalable solution to both. However, the fragmented regulatory landscape across states has long created roadblocks for manufacturers and builders.
"Virginia, like the rest of the nation, is always looking for ways to address the challenges of producing enough housing to keep up with demand and making housing more affordable," said Brian Hilderbrand, Construction Regulation Administrator at the State Building Codes Office in the Virginia Department of Housing and Community Development.
“Offsite construction plays a critical role in addressing these challenges, but navigating the patchwork of regulatory requirements related to offsite construction across the country has long been identified as a major barrier for the offsite construction industry. Implementation of a national standard for the approval of offsite construction is an important step in addressing this barrier.”
By adopting a nationally recognized standard, Virginia helped eliminate this inconsistency. The state played a key role in developing the standards and became one of the first to implement them.
“The standards have improved our program by formalizing many of the policies and practices we had in place and ensuring that the requirements are clear and consistent. Our industry customers regularly express their appreciation for Virginia’s offsite program and for our willingness to be a leader in addressing the barriers they face.”
continued below...
ICC/MBI Standards for Off-Site Construction
Published in partnership with the ICC, these off-site standards bring clarity to the off-site and modular construction processes.
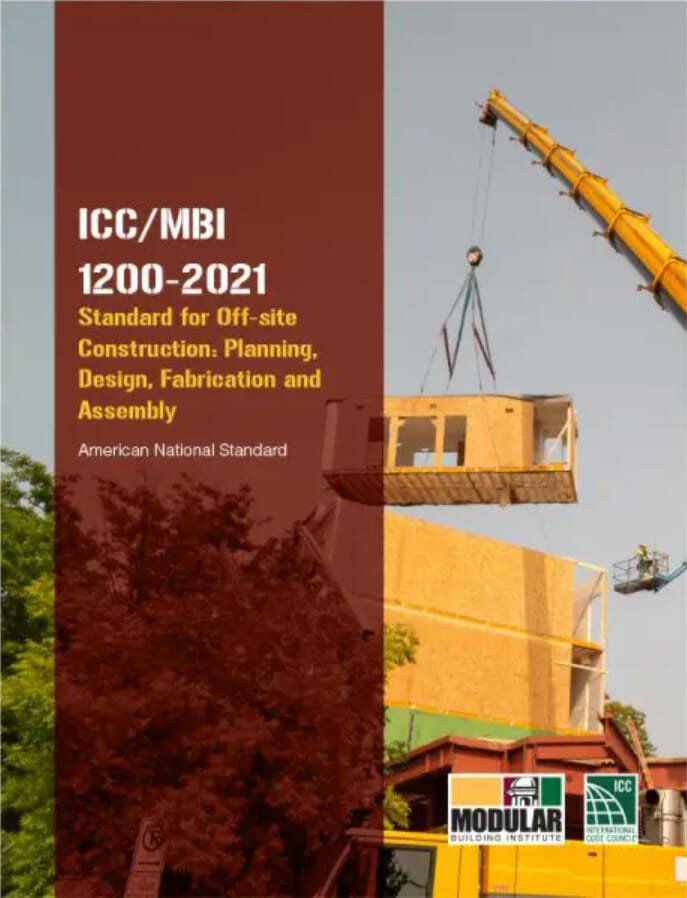
ICC/MBI 1200-2021 Standard for Off-site Construction: Planning, Design, Fabrication and Assembly
This first edition standard provides planning and preparation requirements such as: the role of the architect, modular manufacturer, construction manager, and general contractor; location of plant vs. construction site; and material procurement and lead times.
ICC/MBI 1200-2021 includes requirements for:
- A controlled manufacturing environment.
- Supply chain integration.
- Structural modular vs. nonstructural modular.
- The fabrication process and on-site assembly.
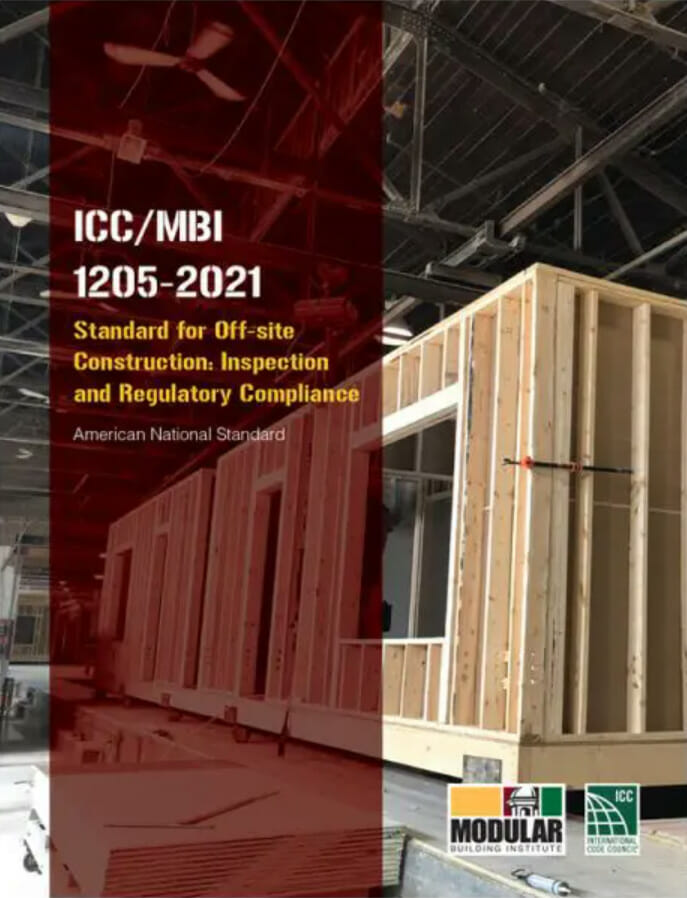
ICC/MBI 1205-2021 Standard for Off-site Construction: Inspection and Regulatory Compliance
The scope of this first edition standard is to provide minimum requirements to safeguard the public health, safety and general welfare and address societal and industry challenges for the inspection and regulatory compliance of off-site and modular construction. It addresses the inspection, approval and regulatory compliance of off-site residential and commercial construction components as well as their assembly and completion at the final building site.
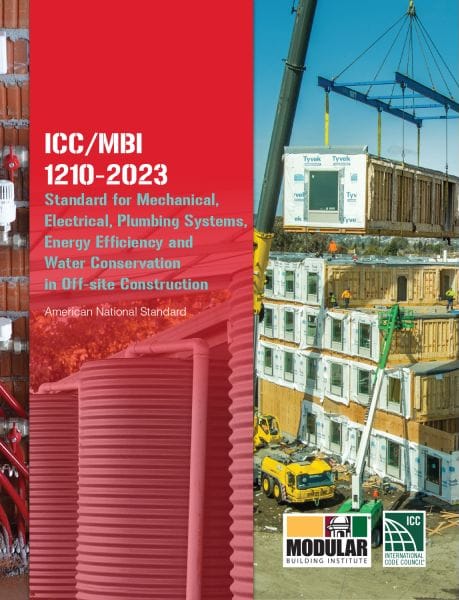
ICC/MBI 1210-2023 Standard for Mechanical, Electrical, Plumbing Systems, Energy Efficiency and Water Conservation in Off-site Construction
The scope of this standard is to provide minimum requirements to safeguard the public health, safety, general welfare and address societal and industry challenges for the energy efficiency and water conservation of off-site construction projects and the planning, designing, fabricating, transporting, and assembling, of commercial and residential building mechanical, electrical and plumbing (MEP) system elements. This includes the componentization and modularization of elements of MEP systems, the incorporation of MEP systems in componentized, panelized or modularized building elements, and the achievement of energy efficiency and water conservation requirements in off-site construction.
Rapid Growth of Commercial Modular Construction Since 2019
Virginia has witnessed a surge in commercial modular construction projects over the past several years.
"By a significant margin," said Hilderbrand, "utility type accessory structures have increased the most. This would include control rooms for substations and cell towers, gensets, switchgear enclosures, etc., followed by guard shacks and construction trailers. There has also been a significant increase in educational buildings for both schools and private companies."
A growing trend has also emerged around modular bathroom pods. In fact, one Virginia-based manufacturer recently produced 314 pods for a hotel in the southwest region of the state, with another producer preparing to deliver a similar quantity for a hotel project in Central Virginia.
"I believe the primary reason for the sustained growth is the increase in awareness of the availability and versatility of these structures at a considerably more affordable cost," commented Hilderbrand. "Registered design professionals are seeing the advantages to incorporating these structures into their designs, saving their customers time and money while increasing quality.
"Based on conversations with local building departments, contractors and other stakeholders, we anticipate significant increases for the foreseeable future in not only the utility occupancies but in R-2, A-3, and E occupancies as well."
Driving Factors Behind Continued Growth
The sustained expansion of modular construction in Virginia can be attributed to increasing awareness of the benefits these structures offer. Cost efficiency, time savings, and improved quality control have made modular systems a preferred option for many design professionals. Architects and engineers are now more inclined to integrate modular components into their plans, which has translated to greater adoption across sectors.
In Hilderbrand's opinion, "the most impactful [reason modular construction is growing in Virginia] is plan review."
"In Virginia," he said, "the CAA’s review the drawings in accordance with the Virginia Uniform Statewide Building Code, comment on non-compliances, and approve compliant drawings, evidenced by their seal on each page. The CAA is then required to submit 20% of all Virginia Plans they approve each month (minimum of 1) to the SBCO for a cursory review. This eliminates a common bottleneck caused by the state reviewing and approving the drawings causing significant delays, which discourages the use of modular units."
Even during the challenges posed by the COVID-19 pandemic, the upward trajectory continued—a testament to the resilience and appeal of modular construction.
Promoting a Modular-Friendly Environment
Another vital initiative has been education. Many local officials initially lacked a clear understanding of modular construction and its rigorous quality assurance processes. Confusion between manufactured homes and industrialized modular buildings further complicated acceptance.
"So many of the local officials do not have a clear understanding of modular and the multiple layers of quality assurance checks required before seals are affixed," said Hilderbrand. "There are some that still do not understand the difference between Manufactured Homes and Industrialized Buildings. Here in Virginia, we provide an 8-hour class in localities throughout the state every year on offsite construction. Through these efforts, we have seen a significant increase in awareness leading to considerably greater acceptance and even appreciation of modular buildings."
Virginia’s embrace of modular construction and its adoption of the ICC/MBI standards serve as a compelling example of how states can modernize their building codes, support industry innovation, and meet urgent construction needs. Through strategic planning, regulatory clarity, and public education, the Commonwealth is not just responding to today's challenges—it's building for the future.
About the Author: John McMullen, PCM, is the marketing director for the Modular Building Institute. You can reach him directly at mcmullen@modular.org or on LinkedIn.
More From Modular Advantage
Oregon’s Prevailing Wage Proposal: A Wake-Up Call for Modular Construction
Should House Bill 2688A become law, building projects would increase in price, face longer completion timelines, and produce significantly more waste. The bill also incentivizes contract awards to out of state businesses who would not reinvest their earnings into the local Oregon economy.
Behind the Design of Bethany Senior Terraces, NYC’s First Modular Passive House Senior Housing Project
As more developers seek to meet new regulations for energy efficiency, the team at Murray Engineering has set a new record. With the Bethany Senior Terraces project, Murray Engineering has helped to develop NYC’s first modular structure that fully encompasses passive house principles — introducing a new era of energy efficiency in the energy-conscious city that never sleeps.
How LAMOD is Using Modular to Address Inefficiency, Sustainability, and the Future of Construction
As developers, designers, and contractors seek to understand the evolving needs of the modular industry, no one is as well-versed in the benefits of going modular as Mārcis Kreičmanis. As the co-founder and CBDO of LAMOD in Riga, Latvia, Mārcis has made it his ultimate goal to address the inefficiencies of traditional construction.
From Furniture Builder to ‘Activist Architect’: Stuart Emmons’ Unique Journey
Stuart Emmons was fascinated by buildings at a young age. He remembers building sand cities with his brother during trips to the Jersey shore. His father gave him his first drawing table at the age of ten. Today, he is an experienced architect who received his FAIA in June 2025. The road he took is unique, to say the least.
Forge Craft Architecture + Design: Codes, Contracts, and Intellectual Property
Founding Principal and Director of Modular Practice for Forge Craft Architecture + Design, Rommel Sulit, discusses the implications of codes, contracts, and intellectual property on
modular construction.
Eisa Lee, the “Bilingual” Architect
Now as the founder of XL
Architecture and Modular Design in Ontario, Canada, she applies not just her education as a traditional architect but an entire holistic view on modular design. It’s this expansive view that guides her work on being a true partner that bridges the gap between architects and modular factories as they collaborate on the design process.
Tamarack Grove Engineering: Designing for the Modular Sector
The role of a structural engineer is crucial to the success of a modular project, from initial analysis to construction administration. Tamarack Grove offers structural engineering services — project analysis, plan creation, design creation, and construction administration — for commercial, manufacturing, facilities, public services, and modular. Modular is only one market sector the company serves but it is an increasingly popular one.
Engineer Masters the Art of Listening to His Customers
Since founding Modular Structural Consultants, LLC. in 2014, Yurianto has established a steady following of modular and container-based construction clients, primarily manufacturers. His services often include providing engineering calculations, reviewing drawings, and engineering certification
Inside College Road: Engineering the Modules of One of the World’s Tallest Modular Buildings
College Road is a groundbreaking modular residential development in East Croydon, South London by offsite developer and contractor, Tide, its modular company Vision Volumetric (VV), and engineered by MJH Structural Engineers.
Design for Flow: The Overlooked Power of DfMA in Modular Construction
Unlocking higher throughput, lower costs, and fewer redesigns by aligning Lean production flow with design for manufacturing and assembly.