Touring Japan’s Offsite Construction Industry: An Interview with James Haas, Offsite Construction Sales Manager for Nichiha
Nichiha USA, a premier provider of building envelope solutions and member of the Modular Building Institute (MBI), recently partnered with MBI for a trip to Japan to visit the Nichiha home office in Nagoya as well as several other offsite manufacturers around the country. Besides learning about different offsite building methodologies and systems, the trip was an excellent chance for both MBI and Nichiha to create closer ties with potential industry partners in Japan.
MBI was represented by its executive director, Tom Hardiman, CAE, while Nichiha USA was presented by James Haas, one of its US-based
offsite construction sales managers. I recently had a chance to catch up with James and talk about his travels.
John McMullen: Tell me about Nichiha & Nichiha USA. How does your company serve the commercial modular construction market?
James Hass: In the modular construction market, we provide cladding solutions that help small and large businesses maximize their ROI, providing them with durable, aesthetically pleasing exteriors that install simply and endure the test of time.
John McMullen: How would you describe Japan’s modular industry? How does it compare to the industry here in the U.S.?
James Hass: Japan’s modular industry, recognized for its high quality and efficiency, provides a compelling model for us. Japan’s modular industry is outstanding and highly sought-after. This is why modular construction makes up the majority of the Japan’s building approach and, culturally, is widely accepted. The practice also addresses Japan’s local compliance and seismic demands.
Stateside, we have to do a bit more work to help clients and stakeholders better understand the value of modular construction. But this is where Nichiha can shine. Our Japanese roots can be seen in our designs and clever installation methods. Our fiber cement cladding is elegant, but simple, and reflects a common design taste between our two nations. Nichiha is a natural fit for modular projects.
By integrating what we have learned from our Japanese counterparts, particularly in installation techniques and efficiency, we strive to elevate the entire modular construction landscape in the U.S., ensuring it can meet the industry’s future demands effectively.
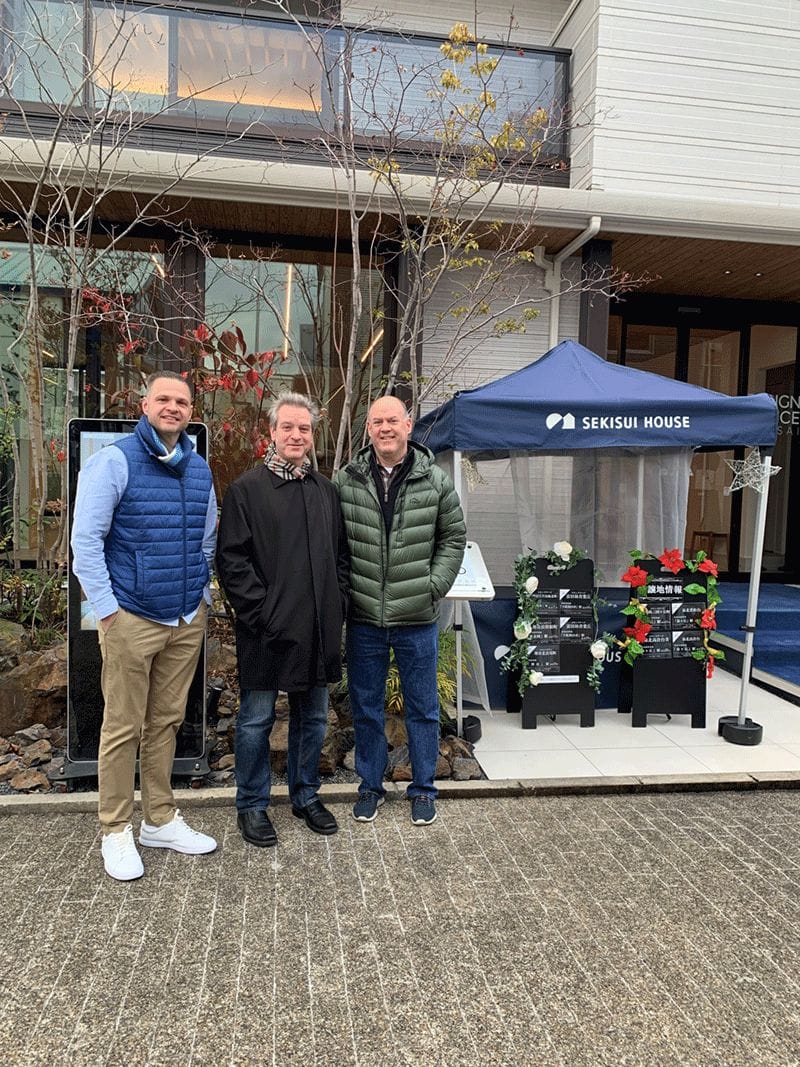
James Hass, consultant Jim Ivanoff, and Tom Hardiman visited Sekisui House to learn about its automated manufacturing processes.
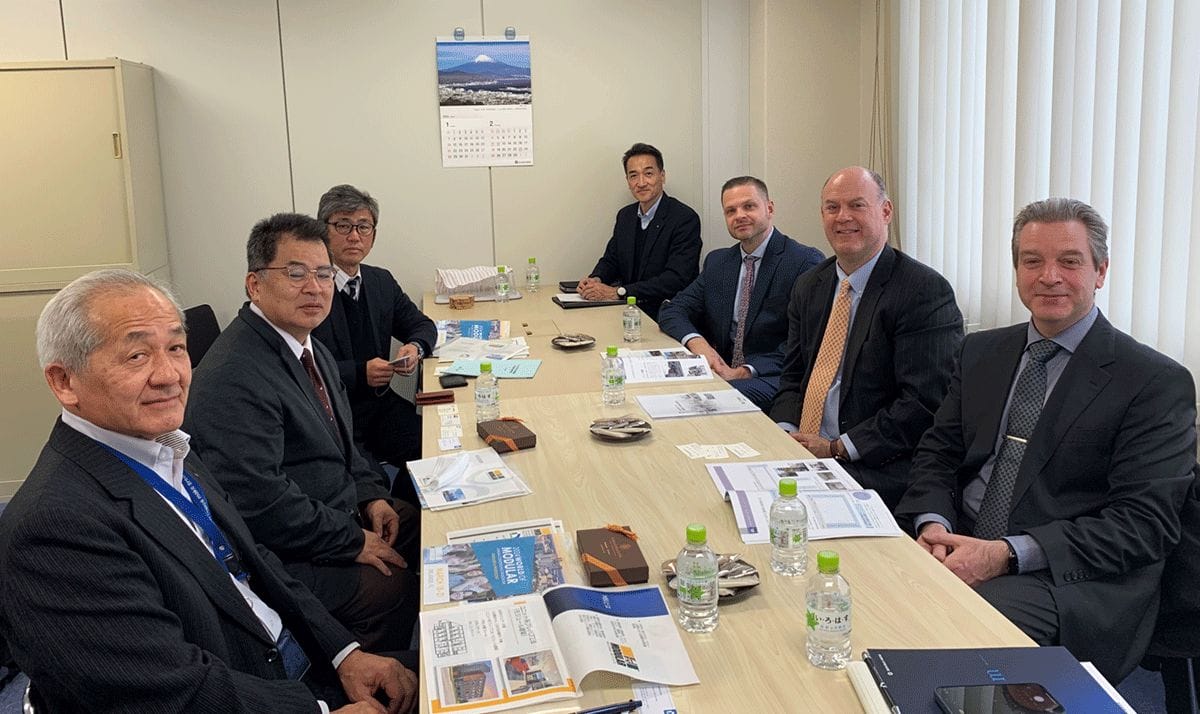
Tom Hardiman, CAE, and James Haas attend a meeting with leaders from the Japanese Prefab Association during their recent trip.
John McMullen: Walk me through your recent visit to Japan.
James Hass: I was able to accompany MBI’s executive director, Tom Hardiman, during meetings with multiple manufacturers. We were even able to take some manufacturing tours and see first-hand how modular construction is approached in Japan.
Because Nichiha and MBI were able to join forces on the trip, it helped us gain insight from more than one perspective. Seeing a polished and refined modular industry helped our individual and collective efforts to expand the approach in the United States.
Installation techniques were a big takeaway for me personally. Seeing a variety of applications and how they’re installed really helped elevate my own level of confidence to become more of an advocate for the benefits of modular construction as a whole rather than solely Nichiha-specific applications.
John McMullen: How was MBI involved in this trip?
James Hass: MBI was instrumental in setting up all of these insightful visits and I very much appreciate their assistance. Having Tom with us was valuable for both Nichiha and MBI too, as it allowed each of us to elevate the way we approach modular construction back in the United States.
John McMullen: What was the overarching goal of the trip?
James Hass: The goal was twofold. The first goal was to promote MBI and explore how to expand it from a US-based entity to one that takes a more global approach. Secondly, we wanted to gain a more comprehensive background in modular construction approaches to help promote awareness of offsite and modular construction.
For myself, it was stellar real-world training. Being able to see and experience a well-established modular construction industry will help me better communicate with domestic manufacturers to expand the approach here in the States.
John McMullen: What was the overarching goal of the trip?
James Hass: The goal was twofold. The first goal was to promote MBI and explore how to expand it from a US-based entity to one that takes a more global approach. Secondly, we wanted to gain a more comprehensive background in modular construction approaches to help promote awareness of offsite and modular construction.
For myself, it was stellar real-world training. Being able to see and experience a well-established modular construction industry will help me better communicate with domestic manufacturers to expand the approach here in the States.
John McMullen: What manufacturers did you visit?
James Hass: We visited SEKISUI HOUSE, Sekisui Heim, Panasonic Homes, Daiwa House Industry and we were able to tour the manufacturing facilities of three of those.
While we were there, we also visited Nichiha’s Japanese headquarters where we met with the international sales team. It was a rewarding experience and opportunity to see how we as an organization are approaching sales opportunities across the world. In doing so, I was able to begin working on two opportunities for Nichiha in Taiwan and Colombia respectively.
John McMullen: What did you learn or take away from each visit?
James Hass: These visits really helped us learn about various modular installation techniques. Specifically, we were able to learn a lot about mate-line installation and how to properly connect adjoining modular units while retaining aesthetic and watertight properties in the process.
We were also given the opportunity to learn about the impact of seismic activity, associated codes, and cultural traditions as well. What resulted is more confidence in promoting modular construction practices for both commercial and residential applications.
John McMullen: What is Nichiha’s role in the Japanese market versus the U.S. market?
James Hass: In Japan, Nichiha is the fiber cement market leader. But in the United States, we have a slightly
John McMullen: What was the overarching goal of the trip?
James Hass: The goal was twofold. The first goal was to promote MBI and explore how to expand it from a US-based entity to one that takes a more global approach. Secondly, we wanted to gain a more comprehensive background in modular construction approaches to help promote awareness of offsite and modular construction.
For myself, it was stellar real-world training. Being able to see and experience a well-established modular construction industry will help me better communicate with domestic manufacturers to expand the approach here in the States.
John McMullen: What manufacturers did you visit?
James Hass: We visited SEKISUI HOUSE, Sekisui Heim, Panasonic Homes, Daiwa House Industry and we were able to tour the manufacturing facilities of three of those.
While we were there, we also visited Nichiha’s Japanese headquarters where we met with the international sales team. It was a rewarding experience and opportunity to see how we as an organization are approaching sales opportunities across the world. In doing so, I was able to begin working on two opportunities for Nichiha in Taiwan and Colombia respectively.
John McMullen: What did you learn or take away from each visit?
James Hass: These visits really helped us learn about various modular installation techniques. Specifically, we were able to learn a lot about mate-line installation and how to properly connect adjoining modular units while retaining aesthetic and watertight properties in the process.
We were also given the opportunity to learn about the impact of seismic activity, associated codes, and cultural traditions as well. What resulted is more confidence in promoting modular construction practices for both commercial and residential applications.
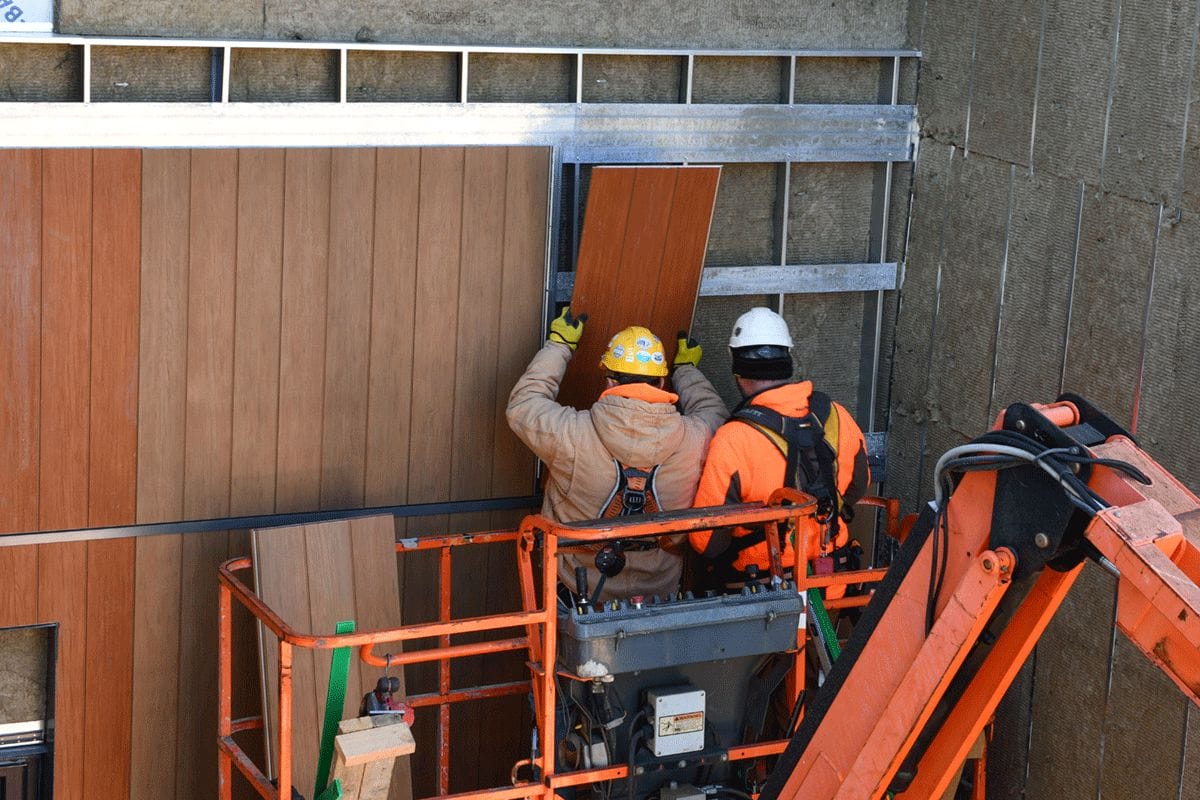
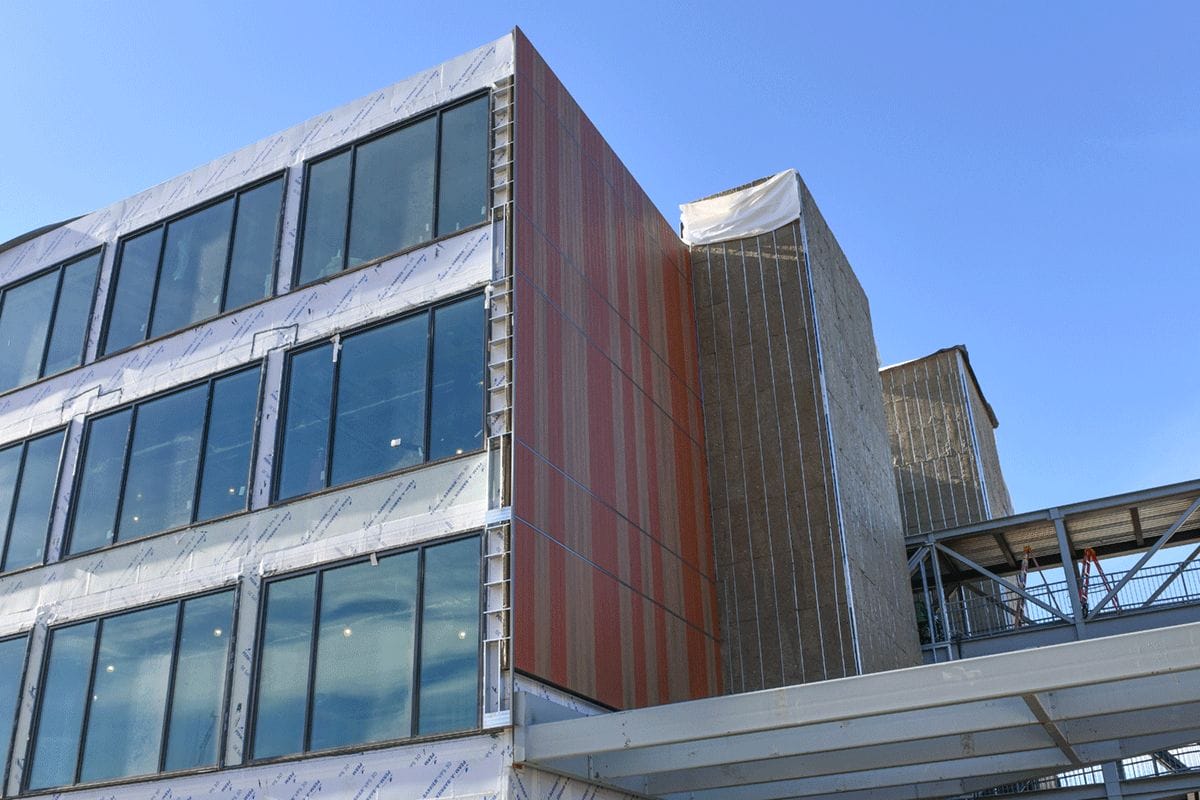
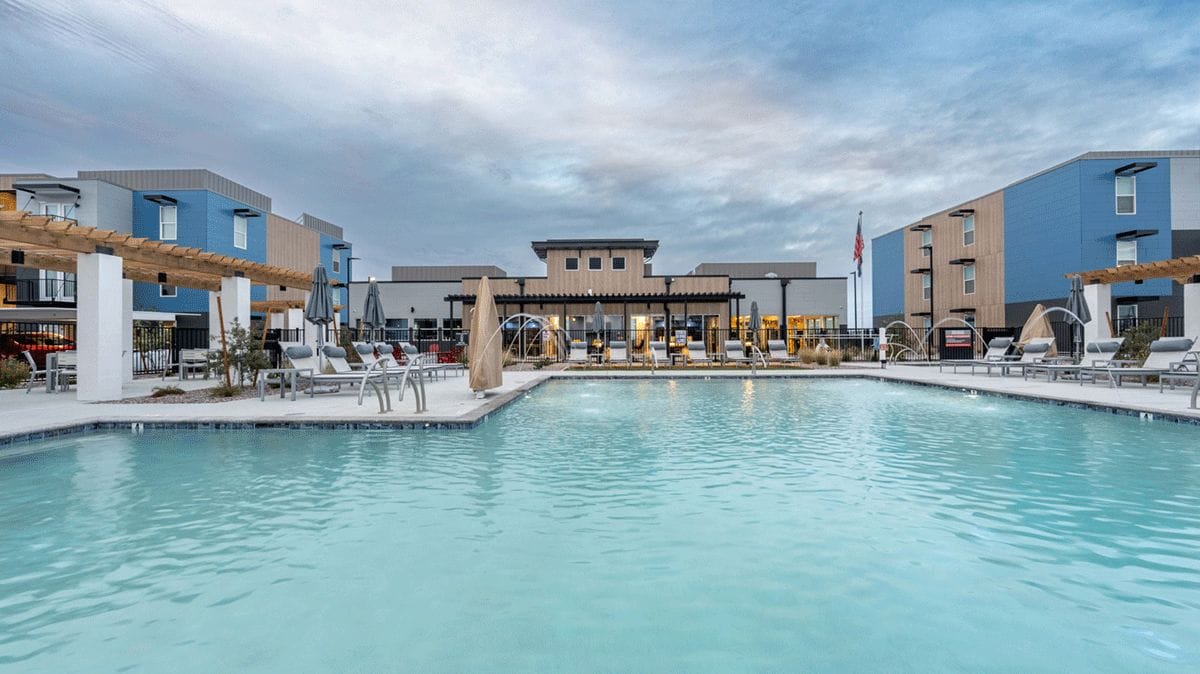
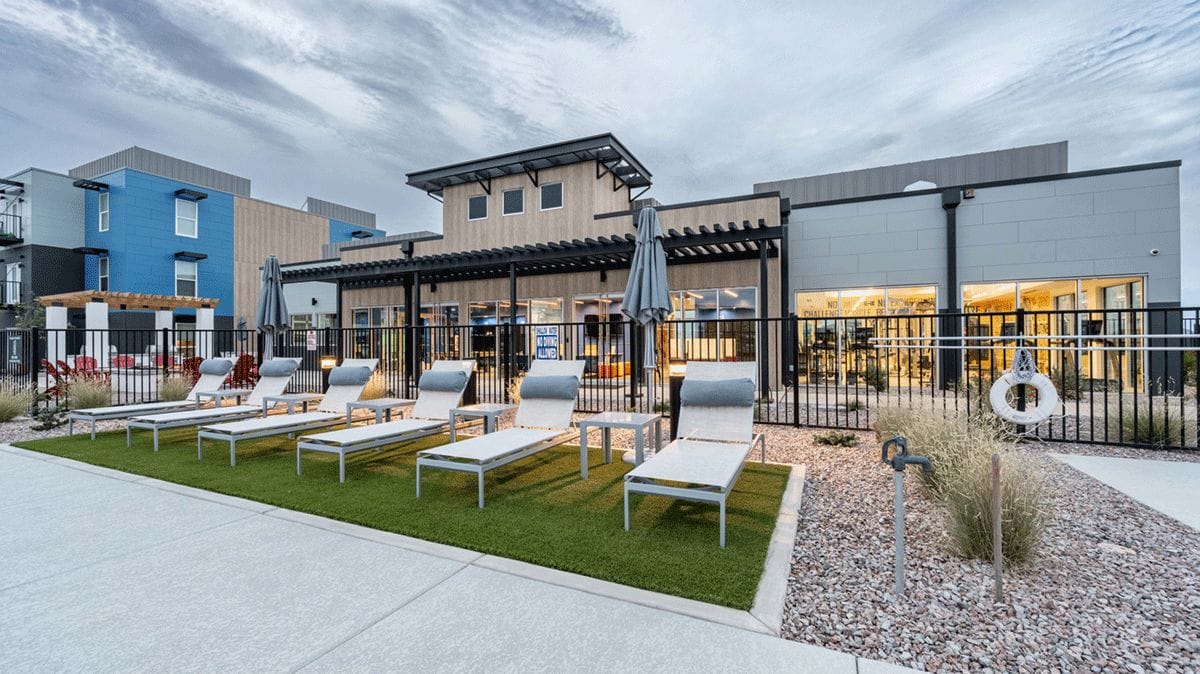
Nichiha and Nichihas USA provide industry-leading exterior cladding solutions that help small and large businesses around the world.
John McMullen: What is Nichiha’s role in the Japanese market versus the U.S. market?
James Hass: In Japan, Nichiha is the fiber cement market leader. But in the United States, we have a slightly smaller stake in the market but are continuing to grow our market share. This is why the trip to Japan was so valuable. It will help us adapt Nichiha’s top selling points for a domestic audience.
John McMullen: Are they roughly the same or are there differences?
James Hass: There are quite a few differences between domestic projects and those in Japan. In Japan, modular is a highly sought-after construction method. And rightfully so—it offers, among other benefits, high-quality builds that are quick to market and resilient.
We spent a lot of time discussing worker safety. Compared to on-site construction, modular builds are generally safer approaches, resulting in fewer worker injuries. Addtionally, there is typically less waste, more efficient build speeds. Knowing what is possible and positive about the Modular industry should help us scale the modular approach in America.
John McMullen: In your view, what can US manufacturers learn from the industry in Japan?
James Hass: Be steadfast with confidence. There is a tremendous amount of growth potential for offsite construction in the United States. It is vital that we look forward to what the future holds for the US construction market as a whole.
Problems like labor shortages in the industry can be aided by modular construction. Workers would report to a central location and build in safe, controlled spaces. This is just one example. But keeping our eyes open to the state of the industry and the future will be vital.
John McMullen: For those not familiar with Nichiha, how can manufacturers/designers best leverage Nichiha’s products?
James Hass: Nichiha’s building products deliver on all fronts – eye-catching aesthetics, the look of natural material, the durability and reliability of fiber cement siding, and a simplified installation process.
Our products mimic the looks of traditional building materials like wood, stucco, brick, concrete, and more but without all the maintenance and upkeep. They’re built to last.
For homeowners, builders, designers, and architects, this means boundless customization options that achieve a precise design vision for a building’s façade. Our products all install similarly and without the need for specialized labor. Depending on the product specified, all our proprietary coatings are factory-applied, ensuring, consistent and warranted performance throughout the country meeting client expectations without variability and requiring less job site labor. Several Nichiha offerings are available in custom colors with no additional cost or minimum quality. Nichiha is committed to this industry with solutions designed to add value to our AEC partners.
About the Author: John McMullen, PCM, is the marketing director for the Modular Building Institute. You can reach him directly at mcmullen@modular.org or on LinkedIn.
More from Modular Advantage
Oregon’s Prevailing Wage Proposal: A Wake-Up Call for Modular Construction
In early February, 2024, the Massachusetts Board of Building Regulations and Standards (BBRS) released its proposed 10th Edition building codes. This draft included several amendments targeting modular construction that would have created an extremely difficult environment for the entire modular industry and could have eliminated the industry entirely in the state.
Behind the Design of Bethany Senior Terraces, NYC’s First Modular Passive House Senior Housing Project
As more developers seek to meet new regulations for energy efficiency, the team at Murray Engineering has set a new record. With the Bethany Senior Terraces project, Murray Engineering has helped to develop NYC’s first modular structure that fully encompasses passive house principles — introducing a new era of energy efficiency in the energy-conscious city that never sleeps.
How LAMOD is Using Modular to Address Inefficiency, Sustainability, and the Future of Construction
As developers, designers, and contractors seek to understand the evolving needs of the modular industry, no one is as well-versed in the benefits of going modular as Mārcis Kreičmanis. As the co-founder and CBDO of LAMOD in Riga, Latvia, Mārcis has made it his ultimate goal to address the inefficiencies of traditional construction.
From Furniture Builder to ‘Activist Architect’: Stuart Emmons’ Unique Journey
Stuart Emmons was fascinated by buildings at a young age. He remembers building sand cities with his brother during trips to the Jersey shore. His father gave him his first drawing table at the age of ten. Today, he is an experienced architect who received his FAIA in June 2025. The road he took is unique, to say the least.
Forge Craft Architecture + Design: Codes, Contracts, and Intellectual Property
Founding Principal and Director of Modular Practice for Forge Craft Architecture + Design, Rommel Sulit, discusses the implications of codes, contracts, and intellectual property on
modular construction.
Eisa Lee, the “Bilingual” Architect
Now as the founder of XL
Architecture and Modular Design in Ontario, Canada, she applies not just her education as a traditional architect but an entire holistic view on modular design. It’s this expansive view that guides her work on being a true partner that bridges the gap between architects and modular factories as they collaborate on the design process.
Tamarack Grove Engineering: Designing for the Modular Sector
The role of a structural engineer is crucial to the success of a modular project, from initial analysis to construction administration. Tamarack Grove offers structural engineering services — project analysis, plan creation, design creation, and construction administration — for commercial, manufacturing, facilities, public services, and modular. Modular is only one market sector the company serves but it is an increasingly popular one.
Engineer Masters the Art of Listening to His Customers
Since founding Modular Structural Consultants, LLC. in 2014, Yurianto has established a steady following of modular and container-based construction clients, primarily manufacturers. His services often include providing engineering calculations, reviewing drawings, and engineering certification
Inside College Road: Engineering the Modules of One of the World’s Tallest Modular Buildings
College Road is a groundbreaking modular residential development in East Croydon, South London by offsite developer and contractor, Tide, its modular company Vision Volumetric (VV), and engineered by MJH Structural Engineers.
Design for Flow: The Overlooked Power of DfMA in Modular Construction
Unlocking higher throughput, lower costs, and fewer redesigns by aligning Lean production flow with design for manufacturing and assembly.