How Air Caster Technology Has Helped Improve Modular Building Manufacturing
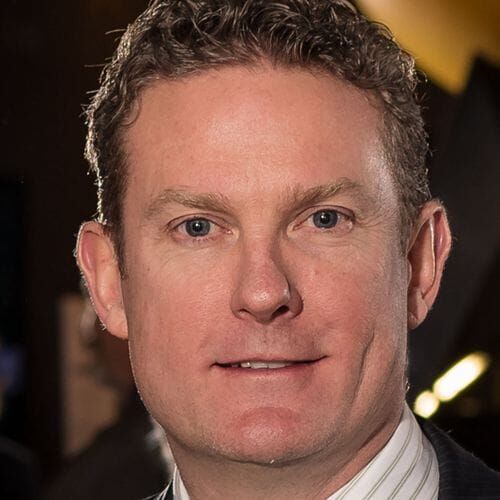
John Massenburg is the President and CEO of AeroGo, Inc.
By manufacturing houses and doing it repetitively, Fading West, a Colorado-based firm, has kept costs down and produced houses more quickly. To accomplish this goal, the company designed a manufacturing facility that can turn around hundreds of modular units, using a breakthrough process that utilizes the adoption of air casters, a low-profile material handling system inspired by hovercraft technology. Traditional systems, like cranes and forklifts, lack the capacity for larger modules, while rail systems are too inflexible and immobile.
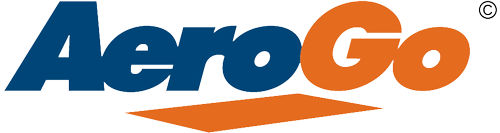
At Fading West, the company uses an unconventional U-shaped production line with nine stations down one row, one in the middle, and nine more stations up the other row. As a result, Fading West doubled its throughput and minimized travel and other forms of waste with consistently positive results.
Transforming the Construction Industry
Modular housing construction firm Fading West Development is anything but fading away. Indeed, the Buena Vista, Colorado-based company, named after an album from American rock band Switchfoot, has seen its success skyrocket in housing construction since its inception. That’s due to its clever and innovative solution to a massive and growing problem: building modular homes, apartments, and other value-engineered residential products in a factory setting to address the nationwide crisis in housing affordability. “I came here to Fading West to ask how we can revolutionize the construction industry to create more affordable housing and get it into the marketplace,” says Sean Brown, Fading West’s vice president of factory operations.
Revolutionize it they did. The Colorado Sun newspaper described Fading West as “a solution to the housing crisis.” Time Magazine even recognized Fading West as one of the 100 Most Influential Companies of 2022—ranking it alongside Amazon and Pfizer.
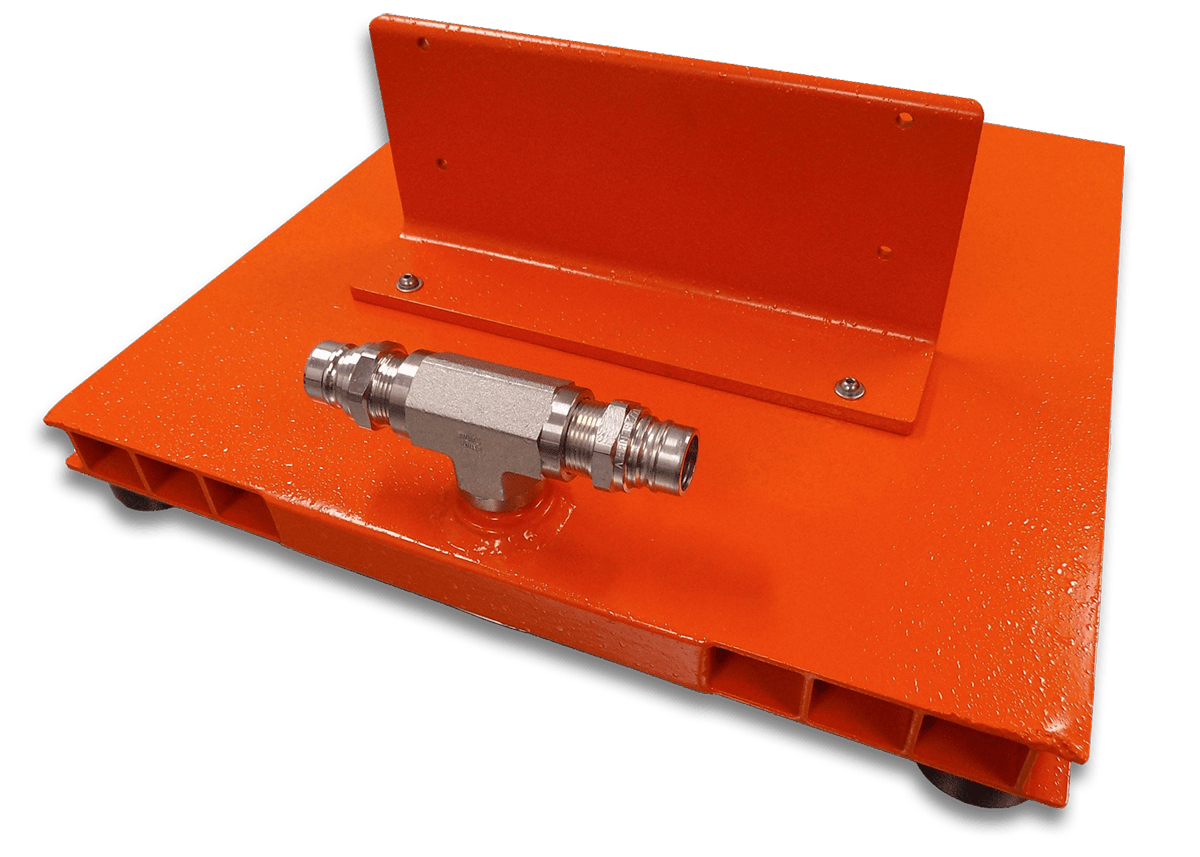
Typical load module for the modular industry allows for quick bolting to the structure through the pre-drilled holes.
What accounts for its stellar success? Efficiency. “By manufacturing houses and doing it in a repetitive fashion, we can keep costs down and we can get the number of houses out quicker,” Eric Schaefer, vice president of sales and strategic partnerships, told the Sun. The result is the company can build a modular three-bedroom home up to five times faster than a traditional stick-built house, with construction costs 15-30 percent lower and market costs at least 25 percent less expensive than comparable stick-built homes.
But what drives that efficiency? The answer might be surprising.
Turning Housing Structures into Hovercraft
The main obstacle for Fading West was designing a manufacturing facility that could turn around hundreds of these modular units, sometimes called “boxes,” quickly and efficiently. Since the company built its 110,000-square-foot factory in Buena Vista in 2021, it had an opportunity to design the perfect manufacturing process from the ground up.
Unfortunately, traditional material handling methods proved intractable in meeting its desired goals. Either they wouldn’t work in the way Fading West wanted, or they wouldn’t work at all. For example, cranes and forklifts lacked the capacity for larger modules, while rail systems were too inflexible and immobile. Fading West didn’t want a straight-line manufacturing process because that would require too large a facility and place incoming and outgoing areas on opposite ends of the facility, necessitating two staging areas. It also would force unnecessary travel for workers to monitor the process or move equipment or resources.
The breakthrough came with the adoption of air casters, a low-profile material handling system inspired by hovercraft technology. By inflating a series of donut-shaped bags with compressed air, the massive modules can hover above the ground, allowing for easy, nearly frictionless maneuverability. “In a 38-foot-long-house, we use six air casters,” says Brown. “With 40 psi, we lift the house up and, with four people, one at every corner, we just push the house across the stages. It is not difficult to move entire houses very smoothly.”
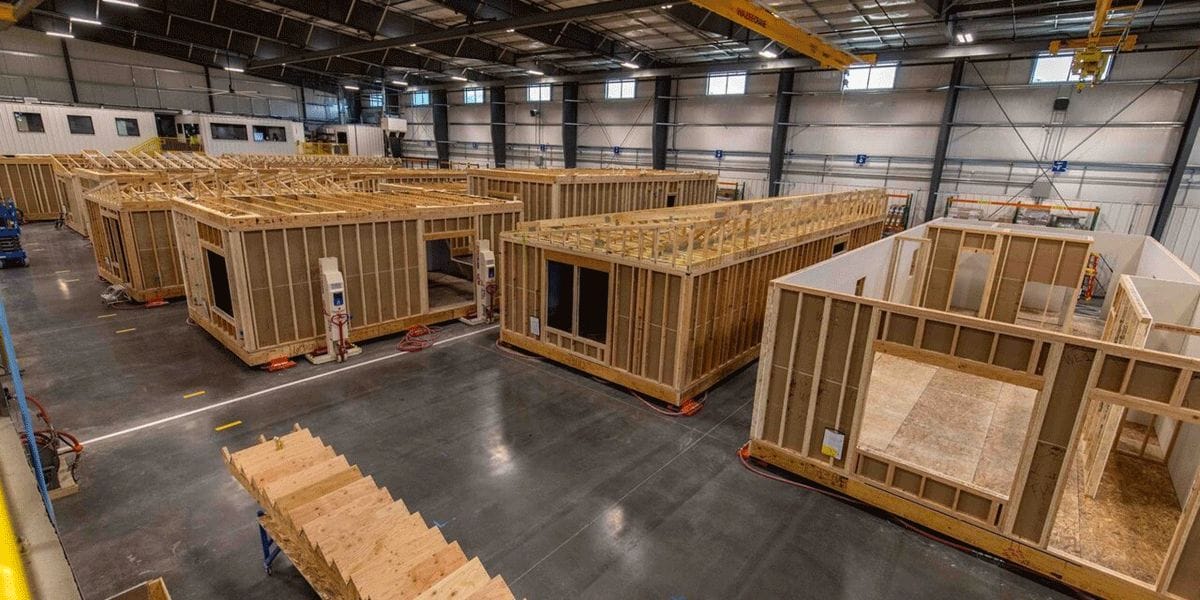
Fading West’s production line can be moved safely and efficiently while floating on air.
U-shaped? You Bet
Better yet, the air casters made it possible to create an unconventional U-shaped production line with nine stations down one row, one in the middle, and nine more stations up the other row. That way, Fading West could double throughput, minimize travel and other forms of waste, and move structures in and out through the same opening. “We can move the entire factory through all 19 stations in the line in under 30 minutes,” says Brown. It enabled Fading West to build the assembly process around a central mezzanine holding tooling and other resources, with elevated offices offering complete visibility over the whole manufacturing line, all at once.
Notably, air casters also mean flexibility, not just in terms of movement but also in terms of change. For example, one structure might be 56-feet-long and another 76-feet-long. Air casters allow the company to easily accommodate a variety of shapes and sizes of boxes and then make changes on the fly. Even better, if Fading West needs to pause production on one unit to handle one-off issues, it can simply float the box to the side and allow the remainder of the production line to continue moving uninterrupted. When ready, employees can seamlessly float the unit back into production.
Solving Real-world Problems While Floating on Air
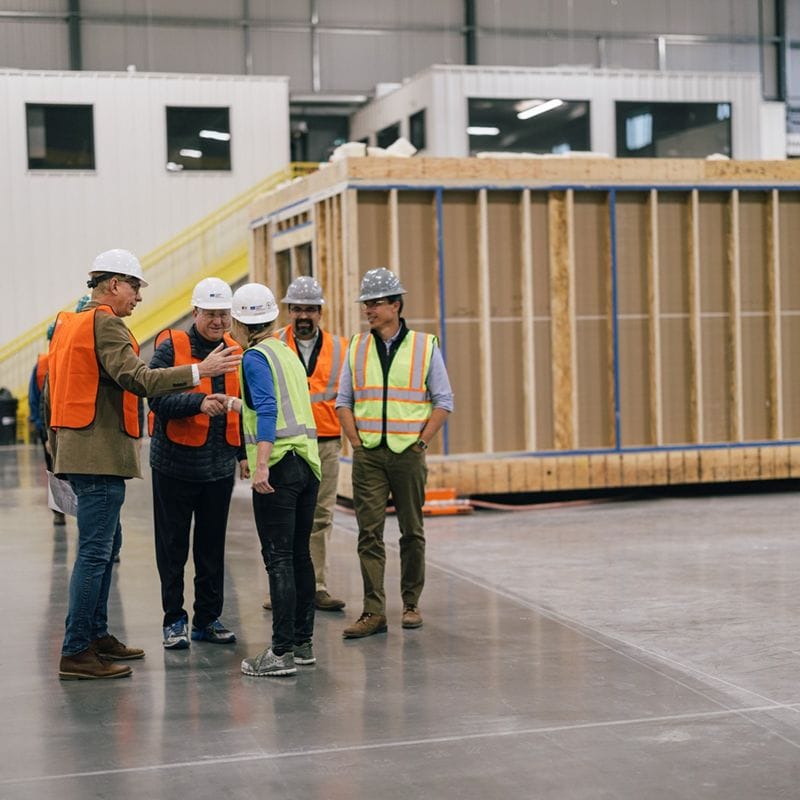
The team at Fading West discusses their efficient production line.
Tackling housing affordability is an ambitious goal, but with its ingenious manufacturing setup, Fading West has found the formula to produce high-quality housing quickly and affordably. Air casters play a quiet but critical role in this formula for success. With their ease of use, low cost, and unbeatable flexibility, Fading West designed a factory from the ground up that could maximize output and adaptability without disruption while minimizing waste. Ultimately, using air casters means Fading West can produce over 700 modular homes and apartments annually.
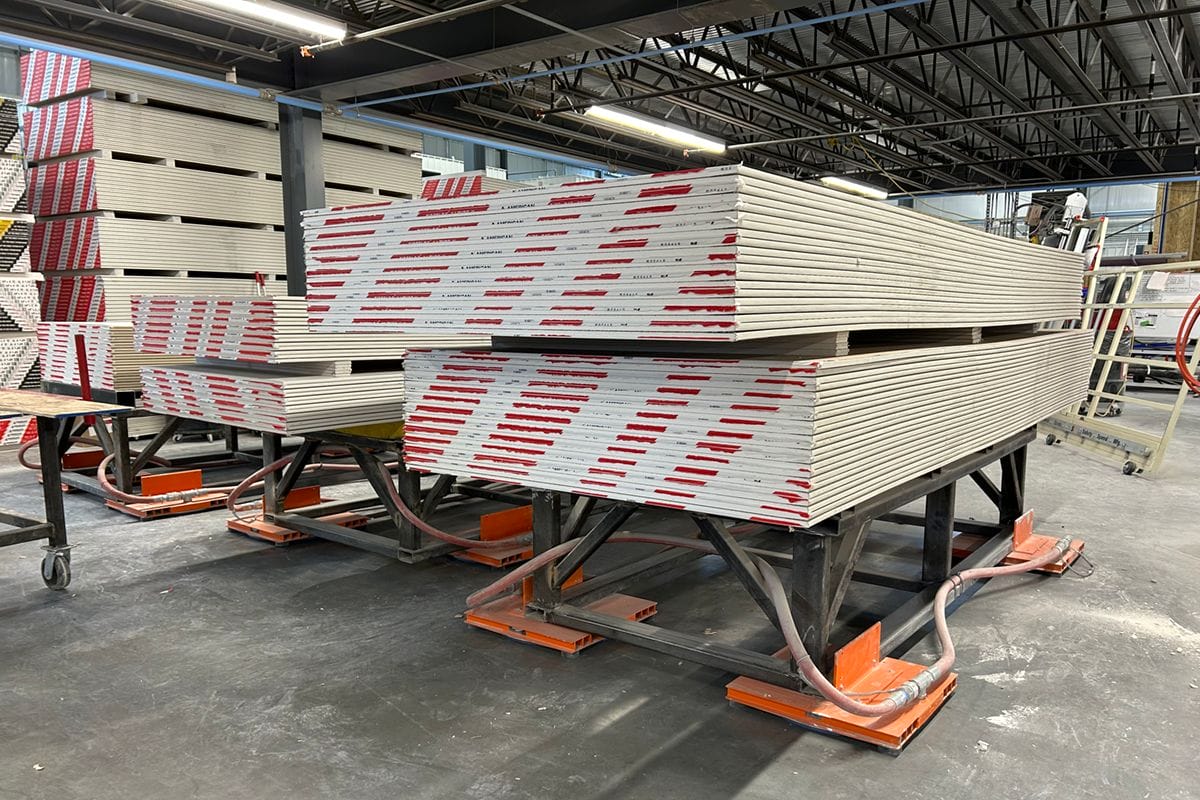
Moving building materials across the shop floor with air bearings.
It’s not just air casters themselves that matter; it’s also the company that provides them. “AeroGo was the only partner that could meet all of our needs,” says Brown. “I wish they could have provided everything in this plant. AeroGo is the only one who delivered what was promised and on time.”
AeroGo has made an impression—and not just on factory workers. “The AeroGo product is so nice, so unique, it’s commented on by every single person that walks through the factory,” says Brown. Playing a part in making housing affordable again and impressing passers-by? That’s just the everyday reality of AeroGo air casters making otherwise impossible moves happen.
Facilitating Growth with Air Caster Technology
Competition in the construction industry is fierce. Historically, two out of these three customer demands—economy, speed, and quality—were adequate. In today’s world, everyone wants all three and then some. Using modern air caster technology in the modular building sector is one way to help meet the fast-moving, high-demand expectations of the industry and its expected growth through 2024 and beyond.
More from Modular Advantage
Oregon’s Prevailing Wage Proposal: A Wake-Up Call for Modular Construction
Should House Bill 2688A become law, building projects would increase in price, face longer completion timelines, and produce significantly more waste. The bill also incentivizes contract awards to out of state businesses who would not reinvest their earnings into the local Oregon economy.
Behind the Design of Bethany Senior Terraces, NYC’s First Modular Passive House Senior Housing Project
As more developers seek to meet new regulations for energy efficiency, the team at Murray Engineering has set a new record. With the Bethany Senior Terraces project, Murray Engineering has helped to develop NYC’s first modular structure that fully encompasses passive house principles — introducing a new era of energy efficiency in the energy-conscious city that never sleeps.
How LAMOD is Using Modular to Address Inefficiency, Sustainability, and the Future of Construction
As developers, designers, and contractors seek to understand the evolving needs of the modular industry, no one is as well-versed in the benefits of going modular as Mārcis Kreičmanis. As the co-founder and CBDO of LAMOD in Riga, Latvia, Mārcis has made it his ultimate goal to address the inefficiencies of traditional construction.
From Furniture Builder to ‘Activist Architect’: Stuart Emmons’ Unique Journey
Stuart Emmons was fascinated by buildings at a young age. He remembers building sand cities with his brother during trips to the Jersey shore. His father gave him his first drawing table at the age of ten. Today, he is an experienced architect who received his FAIA in June 2025. The road he took is unique, to say the least.
Forge Craft Architecture + Design: Codes, Contracts, and Intellectual Property
Founding Principal and Director of Modular Practice for Forge Craft Architecture + Design, Rommel Sulit, discusses the implications of codes, contracts, and intellectual property on
modular construction.
Eisa Lee, the “Bilingual” Architect
Now as the founder of XL
Architecture and Modular Design in Ontario, Canada, she applies not just her education as a traditional architect but an entire holistic view on modular design. It’s this expansive view that guides her work on being a true partner that bridges the gap between architects and modular factories as they collaborate on the design process.
Tamarack Grove Engineering: Designing for the Modular Sector
The role of a structural engineer is crucial to the success of a modular project, from initial analysis to construction administration. Tamarack Grove offers structural engineering services — project analysis, plan creation, design creation, and construction administration — for commercial, manufacturing, facilities, public services, and modular. Modular is only one market sector the company serves but it is an increasingly popular one.
Engineer Masters the Art of Listening to His Customers
Since founding Modular Structural Consultants, LLC. in 2014, Yurianto has established a steady following of modular and container-based construction clients, primarily manufacturers. His services often include providing engineering calculations, reviewing drawings, and engineering certification
Inside College Road: Engineering the Modules of One of the World’s Tallest Modular Buildings
College Road is a groundbreaking modular residential development in East Croydon, South London by offsite developer and contractor, Tide, its modular company Vision Volumetric (VV), and engineered by MJH Structural Engineers.
Design for Flow: The Overlooked Power of DfMA in Modular Construction
Unlocking higher throughput, lower costs, and fewer redesigns by aligning Lean production flow with design for manufacturing and assembly.