STAAT MOD Patient Bed Expansion at M Health Fairview – St. John’s Hospital
Emergency Department (ED) and inpatient medicine teams at M Health Fairview St. John’s Hospital in Maplewood have tirelessly confronted this challenge, facing a 5 percent rise in inpatient visits and a staggering 12 percent increase in ED visits since 2022. With limited capacity and space, and a commitment to improve patient care while visits are only expected to grow, teams at St. John’s devised a strategy for improving patient flow by expanding the emergency department, reorganizing existing services, and — now — opening a new, purpose-built “short-stay and observation unit” to support newly developed workflows.
Construction firm The Boldt Company, and interdisciplinary design firm, HGA were engaged by St. John’s Hospital to deliver a 16-bed ICU patient observation wing onto the existing facility, built to over 90 percent completion offsite in Appleton, Wisc., then seamlessly transported and installed on the St. John’s campus – the first of its kind in the state of Minnesota. The fully structural volumetric modular building added 16 observation rooms, two staff support areas, patient bathrooms, staff toilet rooms, soiled and clean utility, equipment storage, medication room, nourishment alcove, P-Tube station, AHU mechanical yard and I.T., and water and electrical rooms.
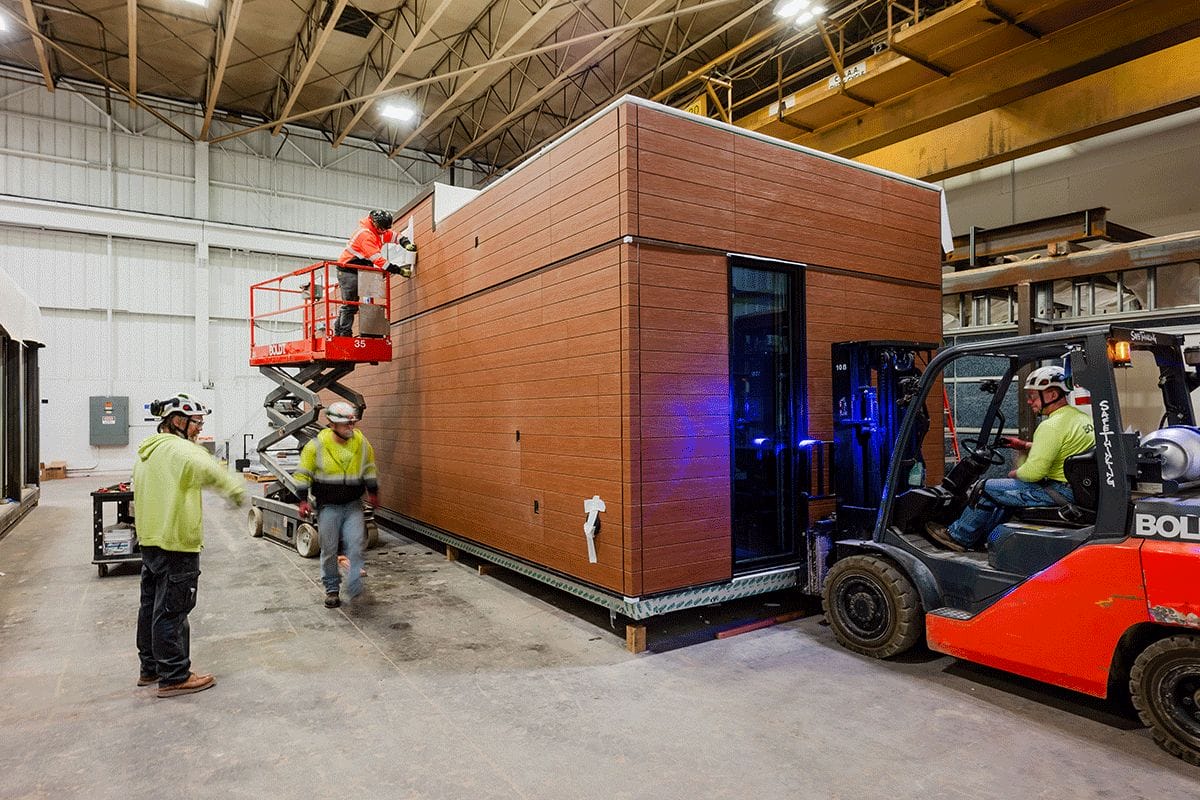
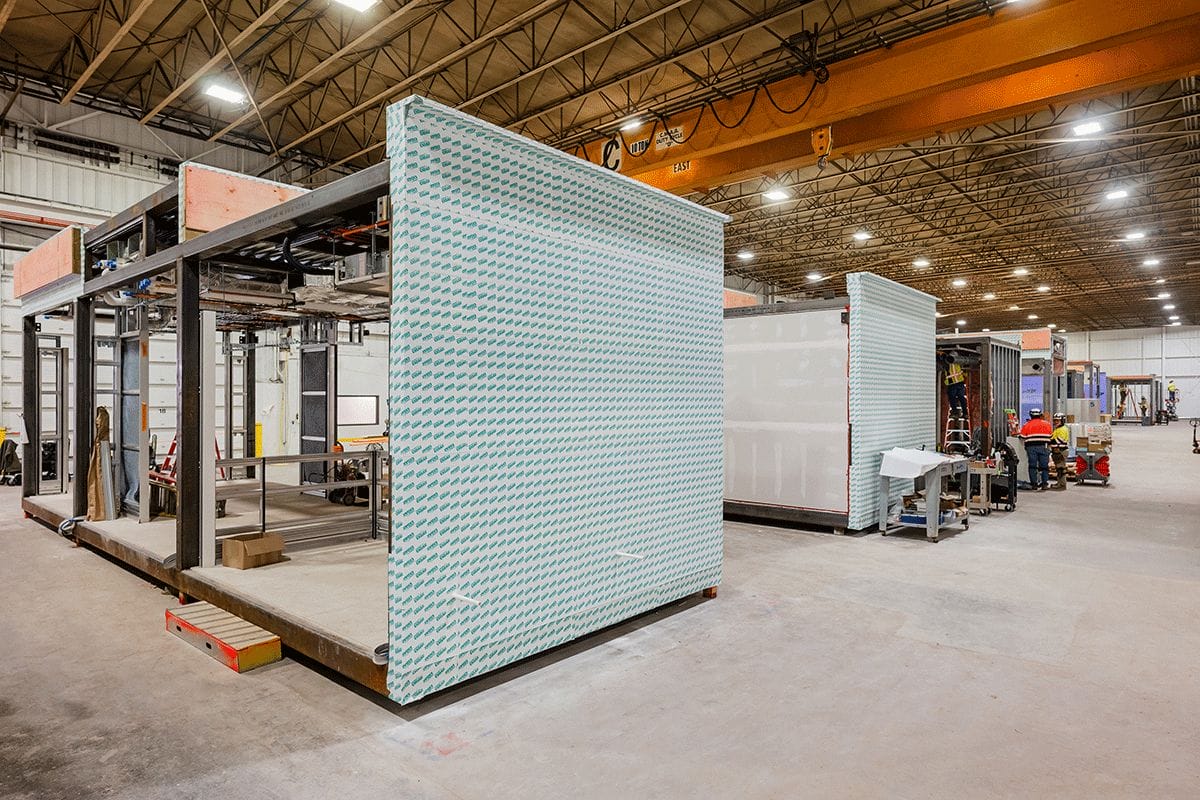
“In the face of escalating patient visits, our ED and inpatient medicine teams have been proactive and innovative in their response,” said Will Nicholson, MD, vice president of medical affairs for M Health Fairview St. John’s, Woodwinds, and Bethesda hospitals. “This approach is a game-changer. It allows us to rapidly develop the needed space without impeding current operations.”
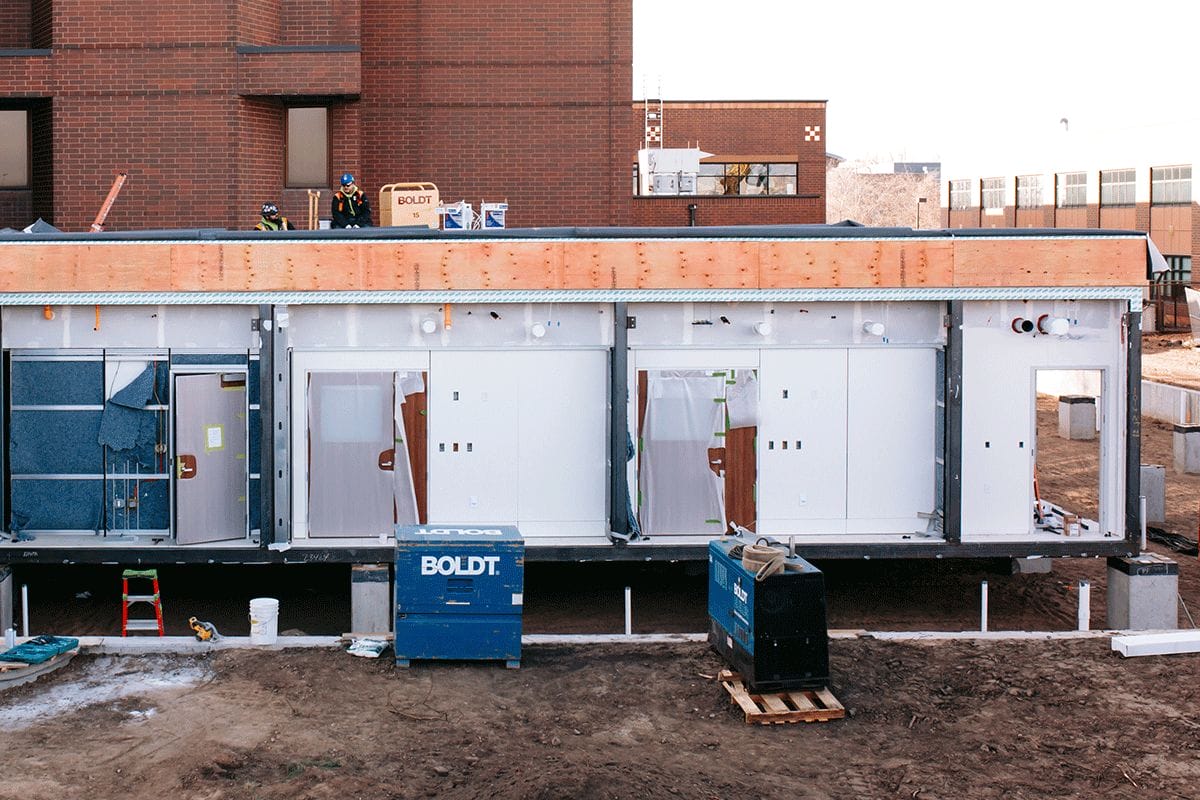
Construction of the unit began offsite in September. Crews delivered the prefabricated unit to St. John’s in late November, and teams completed final construction and furnishing, opening the addition to patients in mid-January.“We’re facing a very real need for patient bed space in our country right now.” said David Thomack, chief operating officer with Boldt. “Every day that is spent in planning, design, or construction is another day that hospitals and patients must do without those beds. Using a modular approach, we’re delivering that space in half the time traditional construction would take, without sacrificing durability, quality, or affordability, allowing healthcare providers to see patients months sooner.”This project represents the latest iteration of Boldt and HGA’s award-winning STAAT MOD product. Originally designed to help healthcare providers meet surging demand due to the COVID-19 pandemic, STAAT MOD has evolved beyond its initial temporary design, into a permanent, high-quality, and aesthetically pleasing modular healthcare solution.
More from Modular Advantage
Oregon’s Prevailing Wage Proposal: A Wake-Up Call for Modular Construction
Should House Bill 2688A become law, building projects would increase in price, face longer completion timelines, and produce significantly more waste. The bill also incentivizes contract awards to out of state businesses who would not reinvest their earnings into the local Oregon economy.
Behind the Design of Bethany Senior Terraces, NYC’s First Modular Passive House Senior Housing Project
As more developers seek to meet new regulations for energy efficiency, the team at Murray Engineering has set a new record. With the Bethany Senior Terraces project, Murray Engineering has helped to develop NYC’s first modular structure that fully encompasses passive house principles — introducing a new era of energy efficiency in the energy-conscious city that never sleeps.
How LAMOD is Using Modular to Address Inefficiency, Sustainability, and the Future of Construction
As developers, designers, and contractors seek to understand the evolving needs of the modular industry, no one is as well-versed in the benefits of going modular as Mārcis Kreičmanis. As the co-founder and CBDO of LAMOD in Riga, Latvia, Mārcis has made it his ultimate goal to address the inefficiencies of traditional construction.
From Furniture Builder to ‘Activist Architect’: Stuart Emmons’ Unique Journey
Stuart Emmons was fascinated by buildings at a young age. He remembers building sand cities with his brother during trips to the Jersey shore. His father gave him his first drawing table at the age of ten. Today, he is an experienced architect who received his FAIA in June 2025. The road he took is unique, to say the least.
Forge Craft Architecture + Design: Codes, Contracts, and Intellectual Property
Founding Principal and Director of Modular Practice for Forge Craft Architecture + Design, Rommel Sulit, discusses the implications of codes, contracts, and intellectual property on
modular construction.
Eisa Lee, the “Bilingual” Architect
Now as the founder of XL
Architecture and Modular Design in Ontario, Canada, she applies not just her education as a traditional architect but an entire holistic view on modular design. It’s this expansive view that guides her work on being a true partner that bridges the gap between architects and modular factories as they collaborate on the design process.
Tamarack Grove Engineering: Designing for the Modular Sector
The role of a structural engineer is crucial to the success of a modular project, from initial analysis to construction administration. Tamarack Grove offers structural engineering services — project analysis, plan creation, design creation, and construction administration — for commercial, manufacturing, facilities, public services, and modular. Modular is only one market sector the company serves but it is an increasingly popular one.
Engineer Masters the Art of Listening to His Customers
Since founding Modular Structural Consultants, LLC. in 2014, Yurianto has established a steady following of modular and container-based construction clients, primarily manufacturers. His services often include providing engineering calculations, reviewing drawings, and engineering certification
Inside College Road: Engineering the Modules of One of the World’s Tallest Modular Buildings
College Road is a groundbreaking modular residential development in East Croydon, South London by offsite developer and contractor, Tide, its modular company Vision Volumetric (VV), and engineered by MJH Structural Engineers.
Design for Flow: The Overlooked Power of DfMA in Modular Construction
Unlocking higher throughput, lower costs, and fewer redesigns by aligning Lean production flow with design for manufacturing and assembly.