Silverking Student Housing, Selkirk College
Architectural Excellence
ROC Modular was proud to deliver a much-needed new permanent modular Student Housing Residence for Selkirk College, located at the Silverking Campus in Nelson BC. The project is a 3-storey, 12-module 38-student bed building with a mass-timber main common area for student amenities. Modular construction was chosen as the ideal solution to provide high-quality, fast-track affordable housing for students. The project is located in Beautiful Nelson BC, a community in the Kootenay region of Interior British Columbia, Canada. The project houses students attending Selkirk College, each dorm unit has a shared washroom, and the building also has a number of communal areas including kitchen, study areas, meeting rooms and laundry rooms. The project integrated mass-timber into the main common areas for the project, which provided open spans and beautiful architectural details, this hybrid method blended seamlessly together to create a stunning project.
Technical Innovation & Sustainability
360 VCM spearheaded this innovative partnership with Scott Builders Inc. as the GC and ROC Modular as the modular supplier. The project achieved step-code 4 of the BC Energy code, receiving exceptional ratings for energy efficiency and environmental design. Utilizing a modular construction process allowed for a faster schedule while minimizing waste and maximizing efficiency during construction. The project was designed to achieve a high level of energy performance by applying passive design principles, and the goal for the project was to increase the overall performance of the building through sustainable construction materials and improved energy efficiency. The hybrid integration of modular and mass timber for the project provided technical innovation and a beautiful architectural design for the finished building.
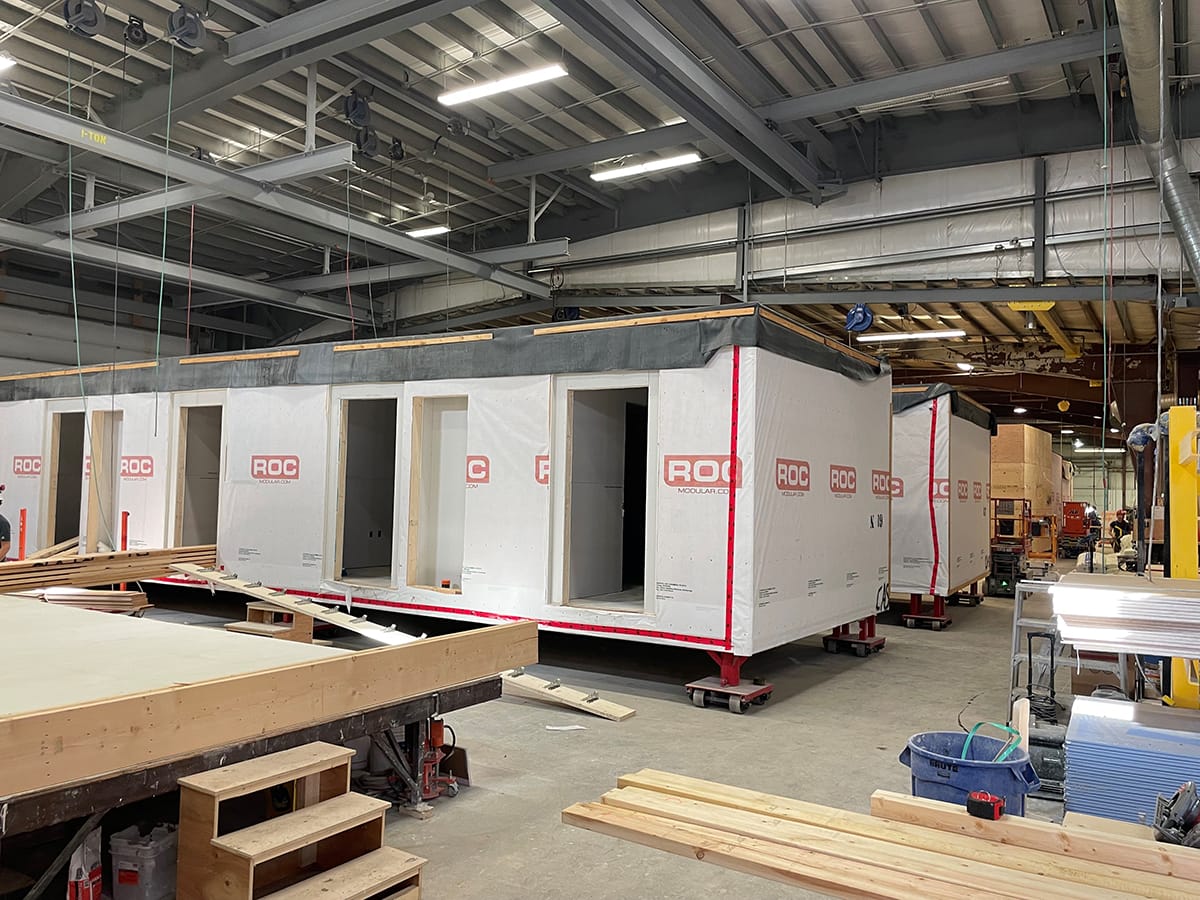
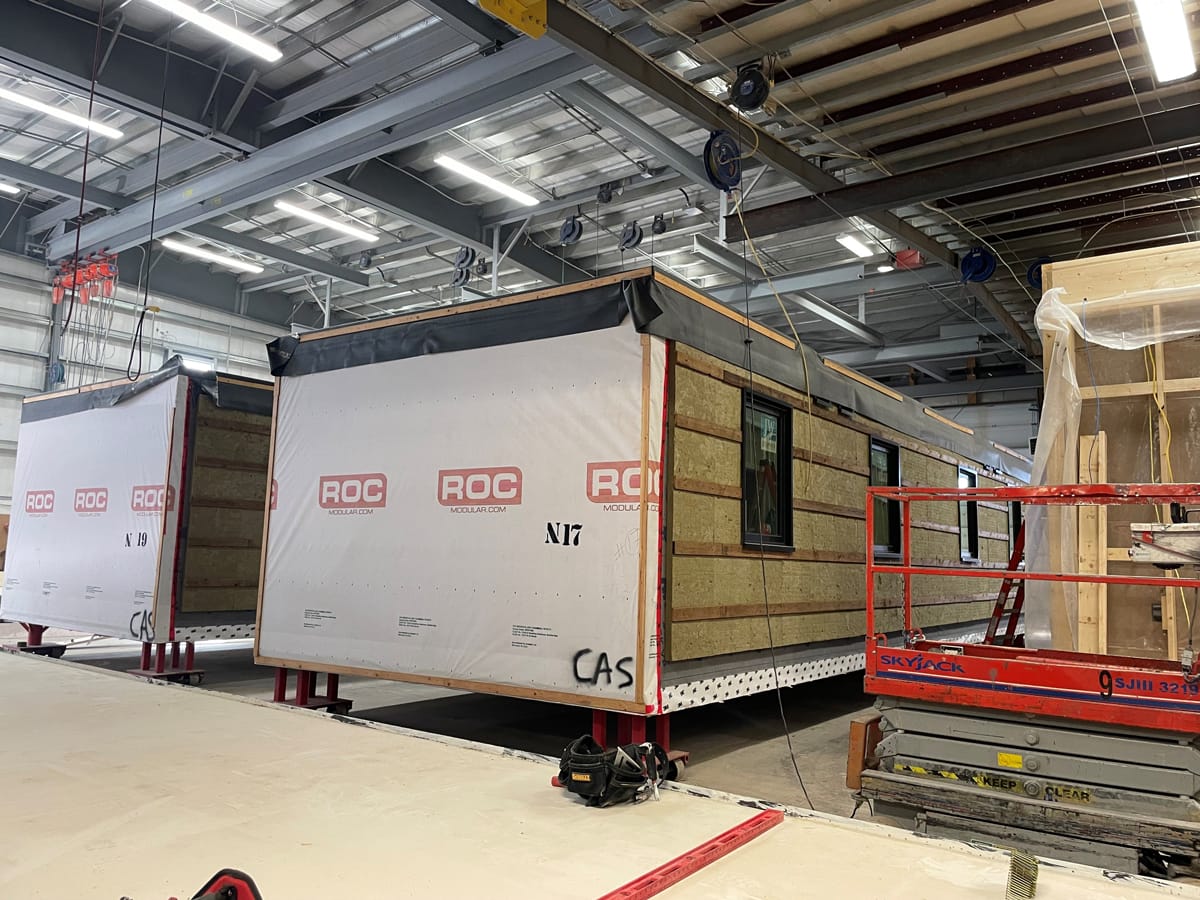
Cost Effectiveness
Modular construction provided a fast-track schedule which reduced overall project cost and enabled Selkirk College to meet the needs of both students and the community. High-quality modular student housing is a critical element for learner success and the completed project will result in better outcomes across the institution. Due to the Interior BC location of this project and a lack of trade availability in the area, modular construction provided the best option and lots of design consideration was given to completing as much in the factory as possible. Building in the ROC Factory reduced the need for trade workers and allowed the project to be completed faster and more cost-effectively. All interior finishes were completed in the factory before delivery, and all furnishings were installed, with a high degree of finish.
More from Modular Advantage
Oregon’s Prevailing Wage Proposal: A Wake-Up Call for Modular Construction
Should House Bill 2688A become law, building projects would increase in price, face longer completion timelines, and produce significantly more waste. The bill also incentivizes contract awards to out of state businesses who would not reinvest their earnings into the local Oregon economy.
Behind the Design of Bethany Senior Terraces, NYC’s First Modular Passive House Senior Housing Project
As more developers seek to meet new regulations for energy efficiency, the team at Murray Engineering has set a new record. With the Bethany Senior Terraces project, Murray Engineering has helped to develop NYC’s first modular structure that fully encompasses passive house principles — introducing a new era of energy efficiency in the energy-conscious city that never sleeps.
How LAMOD is Using Modular to Address Inefficiency, Sustainability, and the Future of Construction
As developers, designers, and contractors seek to understand the evolving needs of the modular industry, no one is as well-versed in the benefits of going modular as Mārcis Kreičmanis. As the co-founder and CBDO of LAMOD in Riga, Latvia, Mārcis has made it his ultimate goal to address the inefficiencies of traditional construction.
From Furniture Builder to ‘Activist Architect’: Stuart Emmons’ Unique Journey
Stuart Emmons was fascinated by buildings at a young age. He remembers building sand cities with his brother during trips to the Jersey shore. His father gave him his first drawing table at the age of ten. Today, he is an experienced architect who received his FAIA in June 2025. The road he took is unique, to say the least.
Forge Craft Architecture + Design: Codes, Contracts, and Intellectual Property
Founding Principal and Director of Modular Practice for Forge Craft Architecture + Design, Rommel Sulit, discusses the implications of codes, contracts, and intellectual property on
modular construction.
Eisa Lee, the “Bilingual” Architect
Now as the founder of XL
Architecture and Modular Design in Ontario, Canada, she applies not just her education as a traditional architect but an entire holistic view on modular design. It’s this expansive view that guides her work on being a true partner that bridges the gap between architects and modular factories as they collaborate on the design process.
Tamarack Grove Engineering: Designing for the Modular Sector
The role of a structural engineer is crucial to the success of a modular project, from initial analysis to construction administration. Tamarack Grove offers structural engineering services — project analysis, plan creation, design creation, and construction administration — for commercial, manufacturing, facilities, public services, and modular. Modular is only one market sector the company serves but it is an increasingly popular one.
Engineer Masters the Art of Listening to His Customers
Since founding Modular Structural Consultants, LLC. in 2014, Yurianto has established a steady following of modular and container-based construction clients, primarily manufacturers. His services often include providing engineering calculations, reviewing drawings, and engineering certification
Inside College Road: Engineering the Modules of One of the World’s Tallest Modular Buildings
College Road is a groundbreaking modular residential development in East Croydon, South London by offsite developer and contractor, Tide, its modular company Vision Volumetric (VV), and engineered by MJH Structural Engineers.
Design for Flow: The Overlooked Power of DfMA in Modular Construction
Unlocking higher throughput, lower costs, and fewer redesigns by aligning Lean production flow with design for manufacturing and assembly.