355 Sango Court Case Study
The Project
Sango Court is an affordable apartment rental development in Milpitas, CA. The 102-unit, transit-friendly location is about a half mile from the nearest BART station, and close to parks, shopping, schools, dining, and numerous employers. This made it a potential gem in a high-rent area where affordable housing is desperately needed.
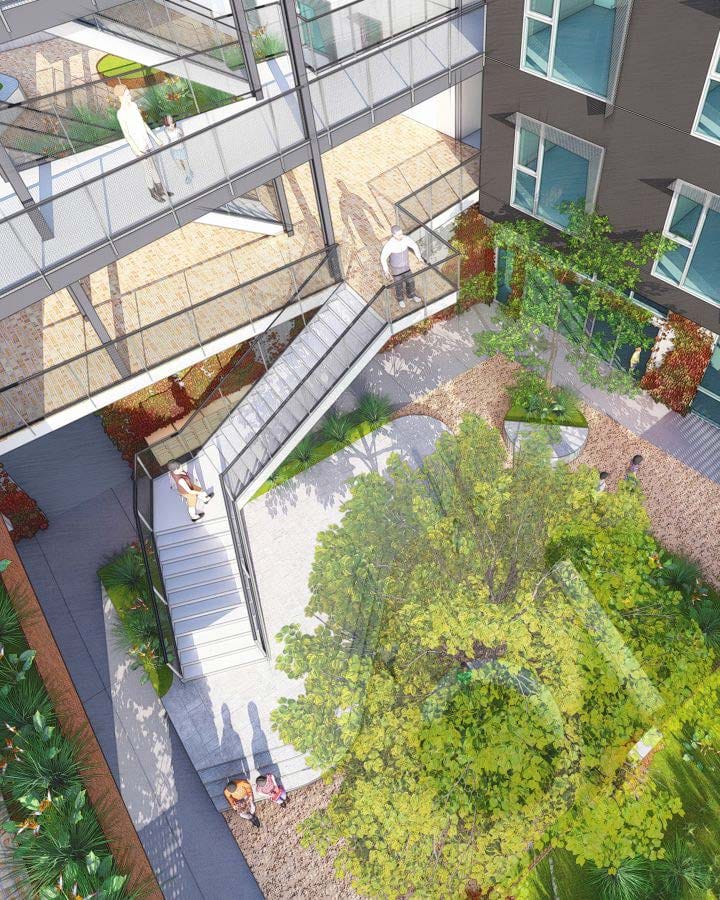
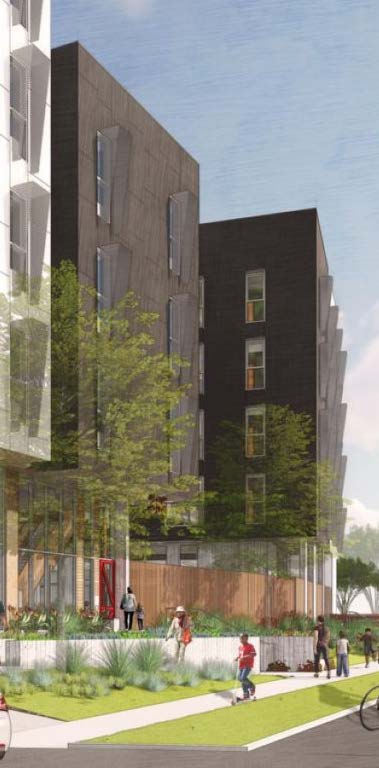
Sango Court, designed by David Baker Architects, brings a very open and livable design to its Bay Area residents.
The Challenge
Autovol, considered by many to be America’s most technologically advanced multifamily modular operation, was still fairly new on the scene. Up to this point, the unique human-robot team of the three-years-young operation had built projects for just one customer. Autovol’s heavily automated approach had been quickly proven by successfully completing 6 multifamily projects for TPC in just two years. Now the factory would be put to the test with its second-ever customer, one who was new to modular construction, with an already designed project, on a tight timeframe.
Mission Critical Preconstruction
Autovol had pioneered the use of automation and robotics to enhance modular construction by doing the heavy lifting and adding machine-level precision to repetitive framing tasks. The logic-intensive preconstruction method demanded of automated modular brought extra benefits to the Sango Court project. Autovol had worked side by side with preconstruction innovator Prefab Logic to create a digital twin modeling approach and a sprint process as advanced as the Autovol factory. The Prefab Logic approach is to build a project down to the finest detail as a digital twin, involving all stakeholders upfront. The data built into the digital twin drives everything in execution: robotic instruction code, clash detection programs, VR and AR 3D models for approvals and to guide tradespeople, as well as material procurement and takeoff lists. The sprint model was designed to force collaborative decision making upfront, when changes can be made digitally. This prevents changes later that can cause orders of magnitude more cost impacts and schedule delays once the physical building is being executed. Tim Mathson, Prefab Logic Operations Manager during preconstruction, said the team really leaned into this approach to solve a variety of unique aspects of the building design.
“To make sure the things being built in the factory and onsite aligned, everything had to be spot on, down to about a quarter inch,” Mathson says. “A lot of things had to be coordinated very quickly on a design that had been years in the making, with a factory that had very specific requirements for robotic framing, but also very standardized design and materials approaches that optimize cost and efficiency.”
Design Challenges
Some of the inventive features designed to make Sango Court unique and livable for residents posed challenges: A large laundry room requiring special venting. Large fresh air ducts in rooms. Open sloping corridors. Lack of a chase compartment for mechanical, electrical, and plumbing through corridors. An exterior facade featuring “sawtooth windows” (a feature that was removed through design revisions). These and other design elements required modeling not only for the factory build, but to guide subcontractors onsite.

Go Time
Total time online in the factory, aside from prototyping, was about 9 weeks. During that time, all 102 units were framed, wired, plumbed, floored, insulated, and inspected. All appliances and interior finishes were completed. The project included studios, as well as 1-, 2-, and 3-bedroom units. Each module was carefully planned to be pieced together in a precise sequence onsite.
Go Inside 355 Sango Court
Click on the link below to download the in-depth interactive case study:
Check out Sango Court set highlights as well as a 3D architectural tour of the kitchen and bathroom.
More from Modular Advantage
How BIM & AI are Improving Modular Construction Outcomes Across Europe
Digitalization and ever-advancing project modelling software have been aiding traditional manufacturers, builders, and designers for years. More recently, tech-savvy modular and offsite construction stakeholders have also embraced these tools, adding their own knowledge and data to create newer, faster, more efficient ways of building. Together with new BIM- and AI-powered tools, these builders are now pushing the boundaries of what’s possible with offsite construction and energy management.
Oregon’s Prevailing Wage Proposal: A Wake-Up Call for Modular Construction
Should House Bill 2688A become law, building projects would increase in price, face longer completion timelines, and produce significantly more waste. The bill also incentivizes contract awards to out of state businesses who would not reinvest their earnings into the local Oregon economy.
Behind the Design of Bethany Senior Terraces, NYC’s First Modular Passive House Senior Housing Project
As more developers seek to meet new regulations for energy efficiency, the team at Murray Engineering has set a new record. With the Bethany Senior Terraces project, Murray Engineering has helped to develop NYC’s first modular structure that fully encompasses passive house principles — introducing a new era of energy efficiency in the energy-conscious city that never sleeps.
How LAMOD is Using Modular to Address Inefficiency, Sustainability, and the Future of Construction
As developers, designers, and contractors seek to understand the evolving needs of the modular industry, no one is as well-versed in the benefits of going modular as Mārcis Kreičmanis. As the co-founder and CBDO of LAMOD in Riga, Latvia, Mārcis has made it his ultimate goal to address the inefficiencies of traditional construction.
From Furniture Builder to ‘Activist Architect’: Stuart Emmons’ Unique Journey
Stuart Emmons was fascinated by buildings at a young age. He remembers building sand cities with his brother during trips to the Jersey shore. His father gave him his first drawing table at the age of ten. Today, he is an experienced architect who received his FAIA in June 2025. The road he took is unique, to say the least.
Forge Craft Architecture + Design: Codes, Contracts, and Intellectual Property
Founding Principal and Director of Modular Practice for Forge Craft Architecture + Design, Rommel Sulit, discusses the implications of codes, contracts, and intellectual property on
modular construction.
Eisa Lee, the “Bilingual” Architect
Now as the founder of XL
Architecture and Modular Design in Ontario, Canada, she applies not just her education as a traditional architect but an entire holistic view on modular design. It’s this expansive view that guides her work on being a true partner that bridges the gap between architects and modular factories as they collaborate on the design process.
Tamarack Grove Engineering: Designing for the Modular Sector
The role of a structural engineer is crucial to the success of a modular project, from initial analysis to construction administration. Tamarack Grove offers structural engineering services — project analysis, plan creation, design creation, and construction administration — for commercial, manufacturing, facilities, public services, and modular. Modular is only one market sector the company serves but it is an increasingly popular one.
Engineer Masters the Art of Listening to His Customers
Since founding Modular Structural Consultants, LLC. in 2014, Yurianto has established a steady following of modular and container-based construction clients, primarily manufacturers. His services often include providing engineering calculations, reviewing drawings, and engineering certification
Inside College Road: Engineering the Modules of One of the World’s Tallest Modular Buildings
College Road is a groundbreaking modular residential development in East Croydon, South London by offsite developer and contractor, Tide, its modular company Vision Volumetric (VV), and engineered by MJH Structural Engineers.