Hearst Elementary School Case Study
The Hearst Elementary School is a public school located in Washington, DC. It is focused on providing a rigorous curriculum integrated with exposure to the arts and prides itself on reaching a diverse audience of students. Wilmot Modular, featured in MBI member profiles, was hired to consult and provide what was originally a two-story classroom expansion project. The school district wanted the building to match nearby buildings on the campus, and fit in a steeply graded, small site. There were also budget constraints that had to be managed.
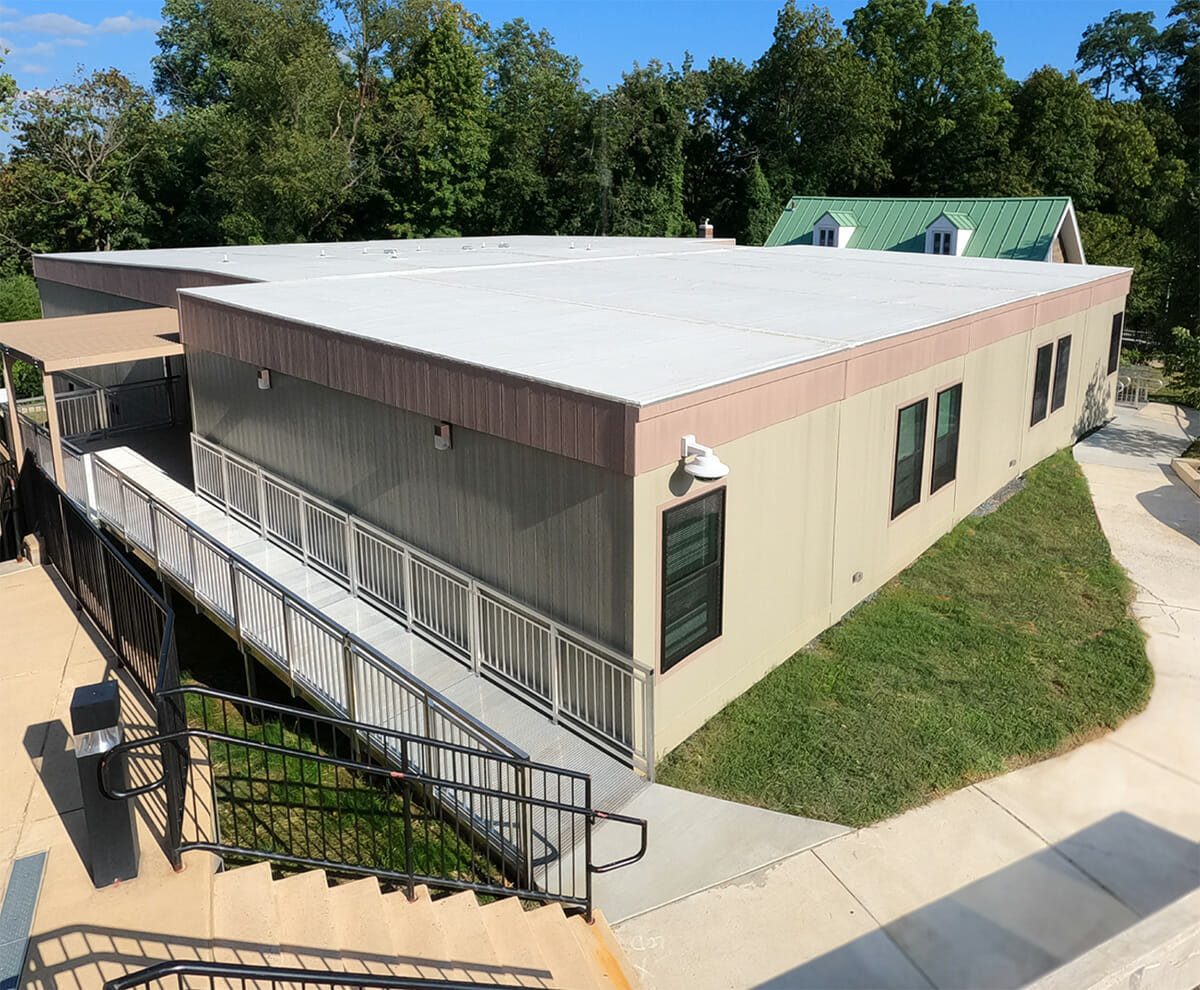
Wilmot worked with the District’s design team to design and furnish a one-story modular building that met all the District’s needs. The building was completed as a design-build project to save both time and money - reducing approximately 18 months from the original two-story project schedule.
The building includes six 32-person classrooms and restroom facilities. Due to the siting and construction of the building, the requirement for fire sprinklers was waived, saving the District about $100,000. Sprinklers may be required in new structures for a variety of reasons. Because of the new building’s proximity to existing structures, a 1HR fire-rated assembly was needed on the left and right elevations and a main corridor. A historic building was within close proximity to the new structure that could not be moved or modified. Its consideration was taken into account and instrumental to meet code requirements.
The modular structure is designed specifically to fit in with the rest of the campus, both in architectural style and technologically. Exterior color and
material selections aesthetically blend with surrounding buildings and interior tech ensures that the classrooms remain connected to the school’s infrastructure.
Architecture and Design
Due to site size constraints and the topography of the land, Wilmot revised the District’s plan for a two-story building to a one-story modular building,
saving the District approximately $400,000 and about 18 months of construction time. A two-story building would have required too much disturbance to the school’s operations, as well as cost significantly more. The resulting modular building was designed to match nearby buildings and fit in with the overall campus. To address the extreme slope of the site (about 12 feet of elevation change sloping down from front to back), the foundations utilized poured concrete footings and formed piers with steel reinforcement to minimize site disturbance. A traditional foundation would have cost the District significantly more in concrete and excavation costs.
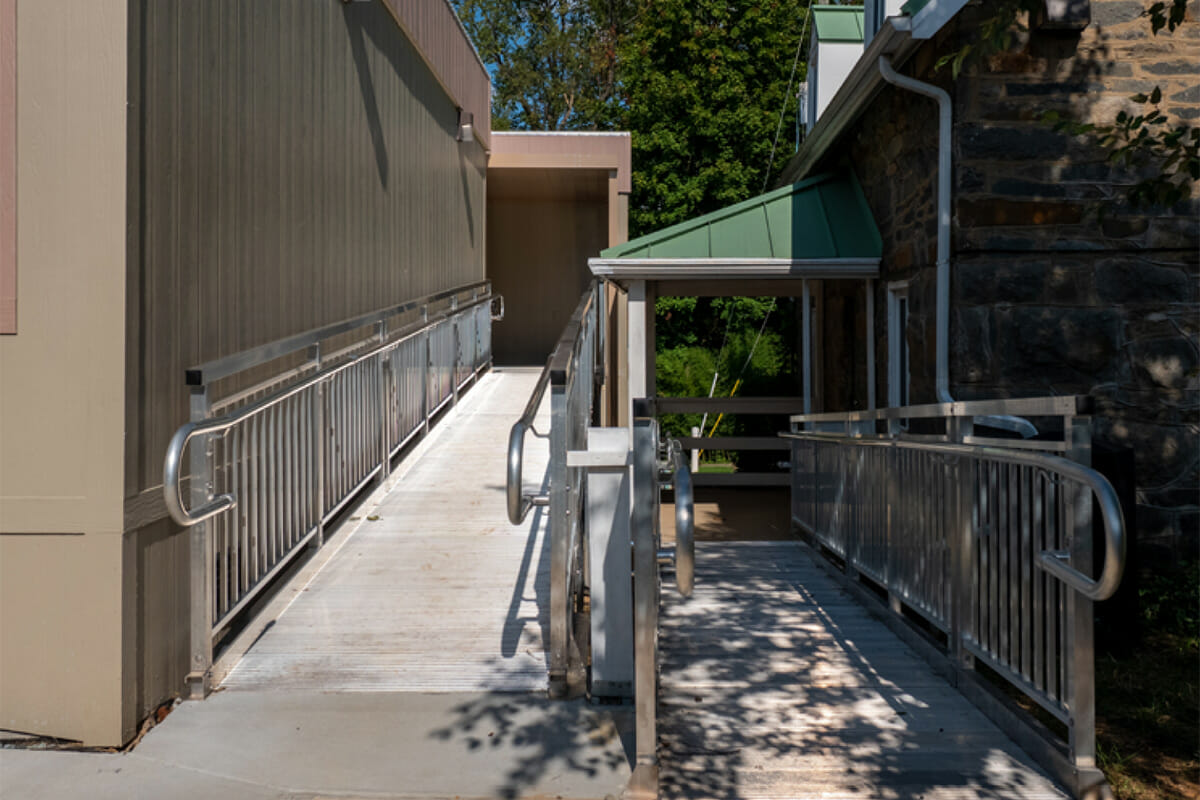
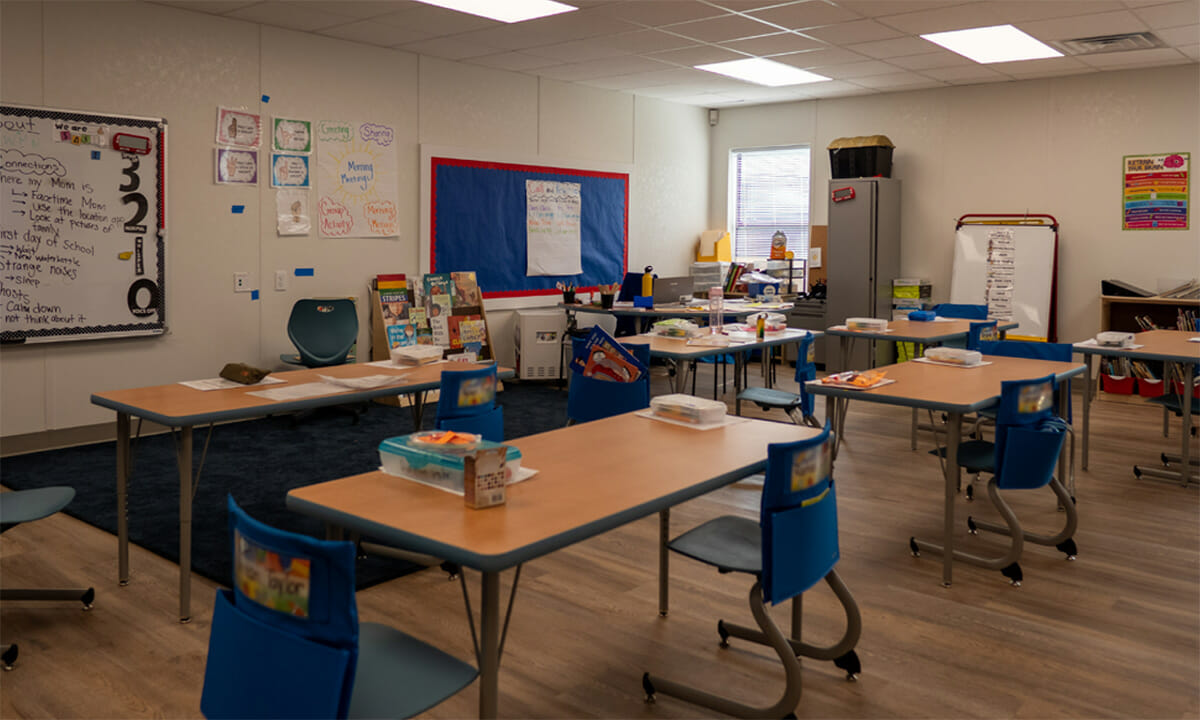
The exterior design included Hardipanel siding, recessed entries, and seamless gutters and downspouts to give the building a permanent look. In addition, metal canopies and ADA ramps were included at both entry points, with a central corridor for efficient access to classrooms and facilities.
The interior finishes included site-installed Corlon flooring, vinyl gypsum wallboard, and acoustical T-grid ceilings with LED lighting. Security cameras and card readers were installed for added security, and integrated with the school’s existing systems.
Technical Innovation
The Hearst Elementary classroom building was designed with an exterior envelope that was energy efficient to meet both code and District requirements. Measures included a reflective white membrane roof and low-E tinted windows to help prevent solar heat gain and prevent glare.
The design included state-of-the-art technology, including digital communication, IT, and security/access controls. The building systems were integrated with the main school building and adjacent classrooms, including smart boards, ensuring that teachers had access to the necessary resources and technology for modern learning. The design included high-quality HEPA filtration in the restrooms, in addition to touchless sanitary items as per COVID-19/school guidelines. The lighting system is made up of high-efficiency LED fixtures with adjustable controls, conserving energy and providing natural lighting when possible.
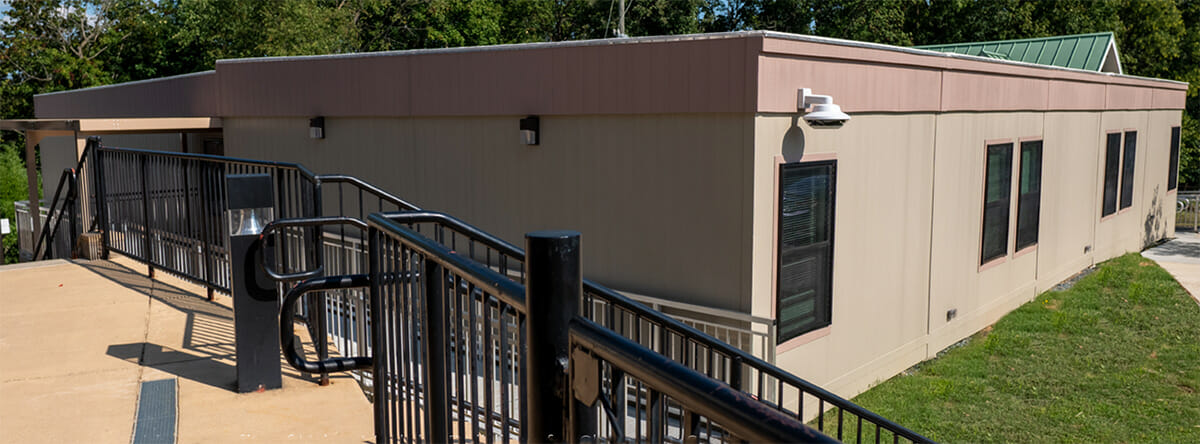
Estimated Savings
- Site and stormwater management improvements that weren’t required due to building siting - $80,000
- Fire rated exterior walls, removing the need for a fire sprinkler system - $100,000
- Value engineering two-story plan to one-story - $400,000 + 18 months from schedule
More from Modular Advantage
Oregon’s Prevailing Wage Proposal: A Wake-Up Call for Modular Construction
Should House Bill 2688A become law, building projects would increase in price, face longer completion timelines, and produce significantly more waste. The bill also incentivizes contract awards to out of state businesses who would not reinvest their earnings into the local Oregon economy.
Behind the Design of Bethany Senior Terraces, NYC’s First Modular Passive House Senior Housing Project
As more developers seek to meet new regulations for energy efficiency, the team at Murray Engineering has set a new record. With the Bethany Senior Terraces project, Murray Engineering has helped to develop NYC’s first modular structure that fully encompasses passive house principles — introducing a new era of energy efficiency in the energy-conscious city that never sleeps.
How LAMOD is Using Modular to Address Inefficiency, Sustainability, and the Future of Construction
As developers, designers, and contractors seek to understand the evolving needs of the modular industry, no one is as well-versed in the benefits of going modular as Mārcis Kreičmanis. As the co-founder and CBDO of LAMOD in Riga, Latvia, Mārcis has made it his ultimate goal to address the inefficiencies of traditional construction.
From Furniture Builder to ‘Activist Architect’: Stuart Emmons’ Unique Journey
Stuart Emmons was fascinated by buildings at a young age. He remembers building sand cities with his brother during trips to the Jersey shore. His father gave him his first drawing table at the age of ten. Today, he is an experienced architect who received his FAIA in June 2025. The road he took is unique, to say the least.
Forge Craft Architecture + Design: Codes, Contracts, and Intellectual Property
Founding Principal and Director of Modular Practice for Forge Craft Architecture + Design, Rommel Sulit, discusses the implications of codes, contracts, and intellectual property on
modular construction.
Eisa Lee, the “Bilingual” Architect
Now as the founder of XL
Architecture and Modular Design in Ontario, Canada, she applies not just her education as a traditional architect but an entire holistic view on modular design. It’s this expansive view that guides her work on being a true partner that bridges the gap between architects and modular factories as they collaborate on the design process.
Tamarack Grove Engineering: Designing for the Modular Sector
The role of a structural engineer is crucial to the success of a modular project, from initial analysis to construction administration. Tamarack Grove offers structural engineering services — project analysis, plan creation, design creation, and construction administration — for commercial, manufacturing, facilities, public services, and modular. Modular is only one market sector the company serves but it is an increasingly popular one.
Engineer Masters the Art of Listening to His Customers
Since founding Modular Structural Consultants, LLC. in 2014, Yurianto has established a steady following of modular and container-based construction clients, primarily manufacturers. His services often include providing engineering calculations, reviewing drawings, and engineering certification
Inside College Road: Engineering the Modules of One of the World’s Tallest Modular Buildings
College Road is a groundbreaking modular residential development in East Croydon, South London by offsite developer and contractor, Tide, its modular company Vision Volumetric (VV), and engineered by MJH Structural Engineers.
Design for Flow: The Overlooked Power of DfMA in Modular Construction
Unlocking higher throughput, lower costs, and fewer redesigns by aligning Lean production flow with design for manufacturing and assembly.