Enthusiasm for Modular Construction Grows in Ukraine as Rebuilding Efforts Take Shape
The future of Ukraine may be uncertain, but one thing isn’t: rebuilding will be a monumental task.
Bruce Talley, Chief Operating Officer at MBI member company OFC Incorporated, is trying ensure that Ukraine’s eventual rebuilding efforts are based in a technology known for its speed and adaptability: modular construction.
During his most recent visit to Ukraine, Talley was invited to share his knowledge of the industry at several building conferences. His first stop: KyivBuilds.
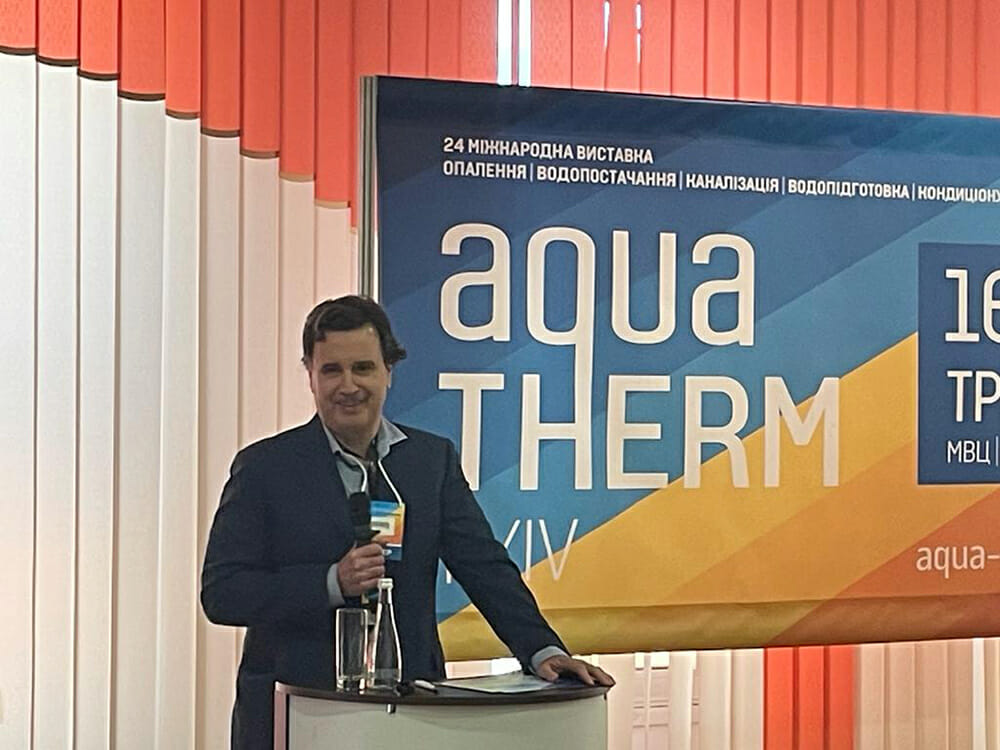
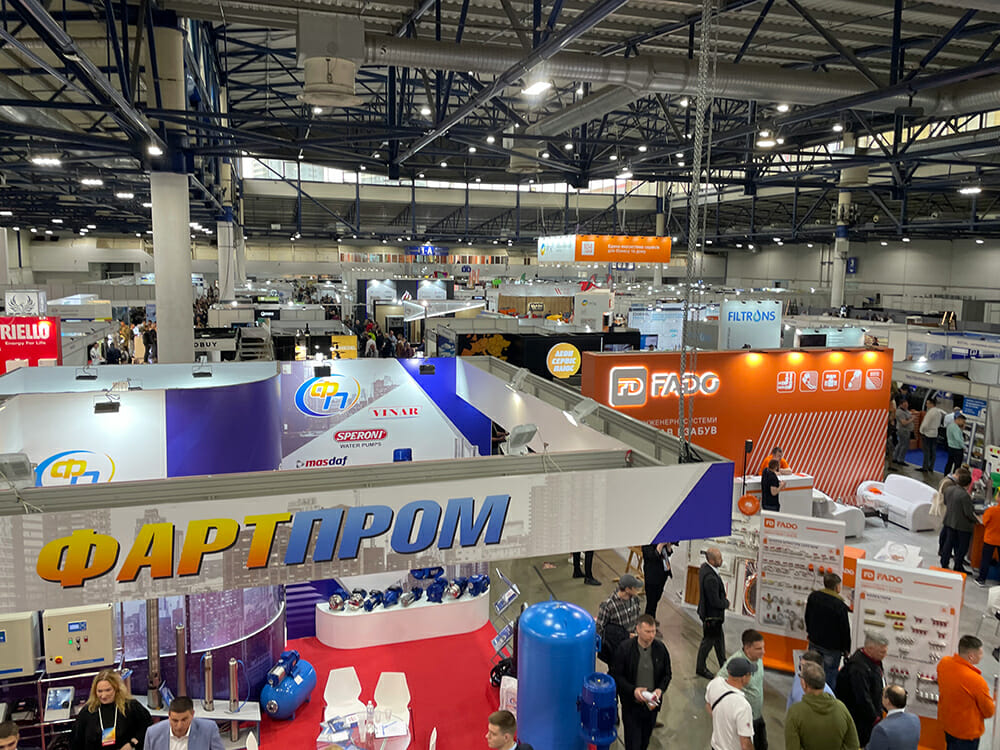
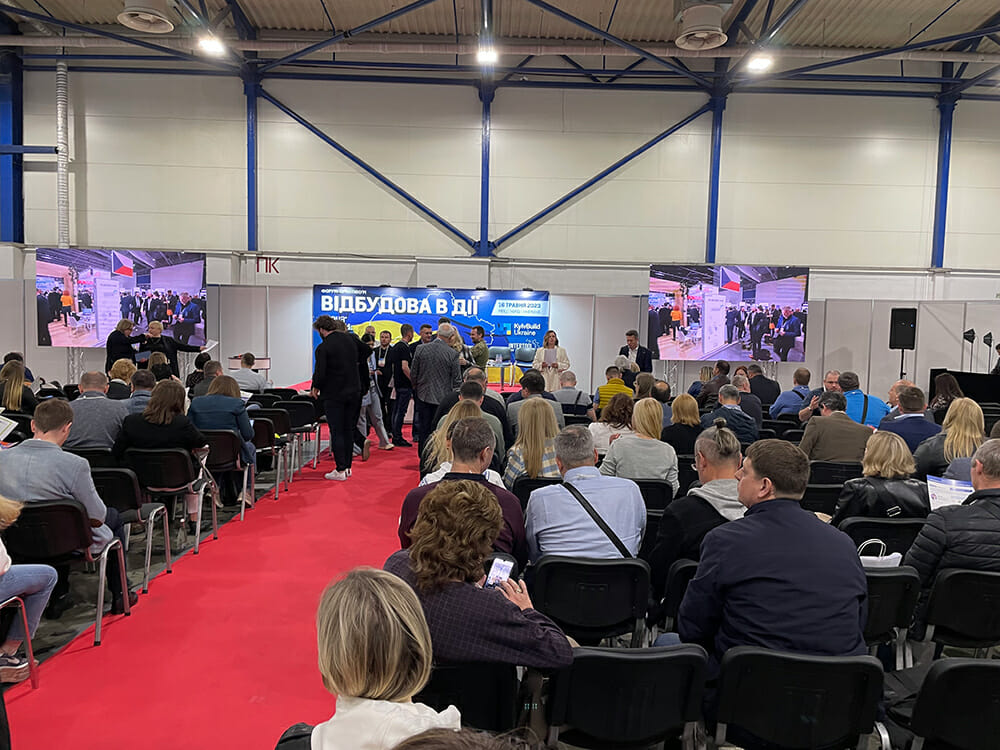
Bruce Talley, chief financial officer at OFC Inc., speaks at KyivBuilds in May, 2023.
Hosted in Ukraine’s capitol May 16-17, the KyivBuilds conference was attended by over 7,300 people with 161 companies exhibiting. There Talley spoke to a group of Ukrainian mayors, developers, and architects about modular housing. Talley then traveled to Irpin and Zhytomyr to talk about modular building applications in those cities.
“The quality of modular building and the uses are much greater than I realized. Modular building will be in great demand in Ukraine to solve housing,” said Oleksandr Markushin, Mayor of Irpin.
“I learned a lot from Bruce's presentation. I think modular building will be very important for Ukraine's rebuilding,” said Artem Shira, director of Nerex, a water treatment and purification company.
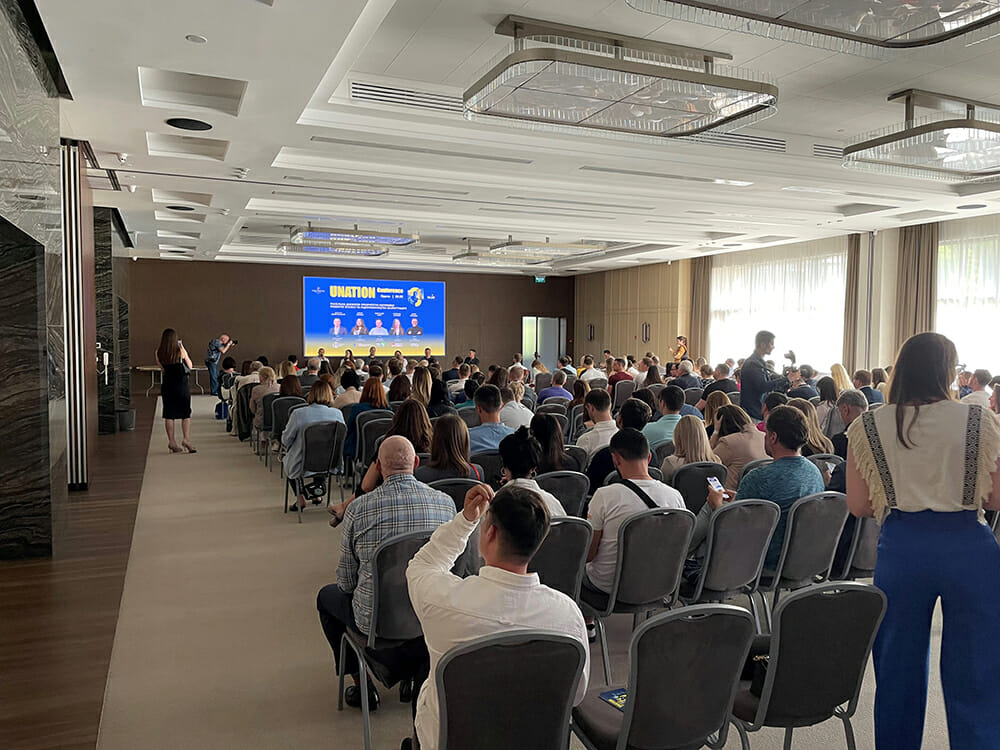
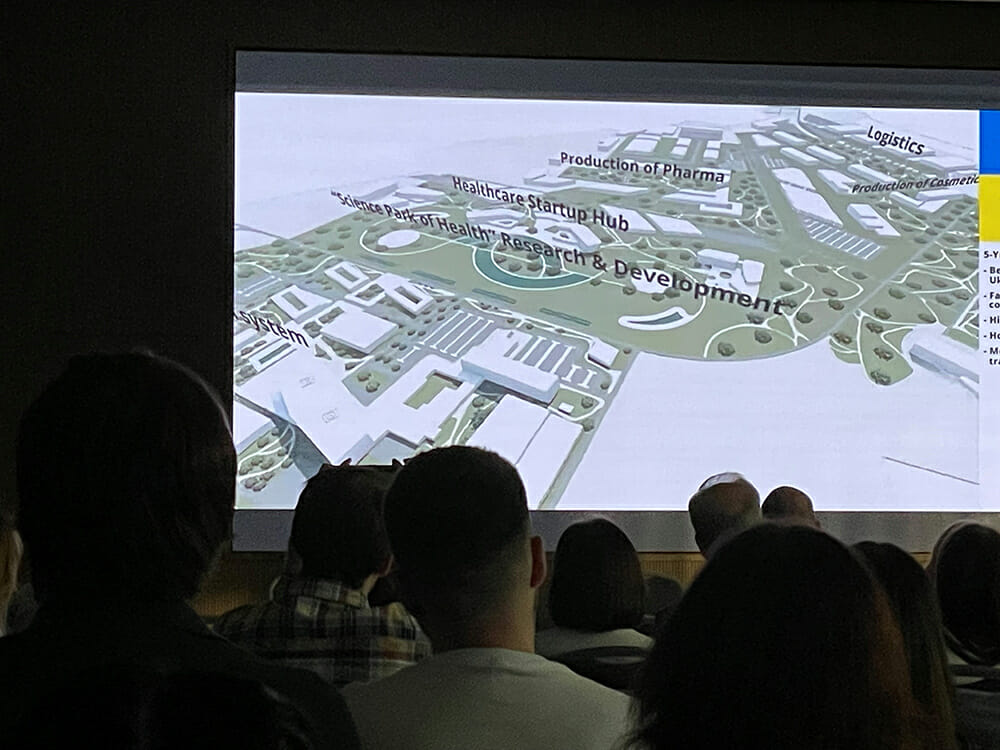
Bruce also presented at the UNation conference in Odesa on May 20, 2023.
Following his talks in Kyiv, Irpin, and Zhytomyr, Talley attended the UNation conference on May 20th in Odesa. Topics included rebuilding, tech incubators, and the reforms that Ukraine needs to instate to attract foreign investment, as well as regional issues affecting Odesa. Also discussed were several large business parks to be developed in Ukraine, with retail, housing, Olympic training, medical, offices, and redevelopment of an airport.
Related Listening:
Rebuilding Ukraine: What Modular Manufacturers, Dealers, and Developers Need to Know w/ OFC, Inc
Bruce Talley, chief operating officer of OFC Inc., discusses the current conditions inside Ukraine, including the state of its infrastructure and housing, and recounts his personal experience and observations from recent visits. Bruce also shares important information for modular companies looking to help in the relief and rebuilding efforts.
The opportunities for modular construction in Ukraine, it seems, are boundless. But for the industry to make an impact, inroads will need to be made.
“In general,” said Talley, “I’m in Ukraine to meet with people, look at potential production sites (especially in western Ukraine, but not limited to there), and discuss modular housing and container conversion applications for apartments, homes, retail, offices, schools, and hospitals. Everyone is interested in solutions that will save time and money and control costs and outcome. Clearly, employment is driving a lot of thought. However, at each event I have attended that has been a lot of discussion around Smart Cities and sustainable development. So much has been damaged in some areas, that instead of rebuilding like it was, cities will look and work differently with new infrastructure.”
It's early yet to make predictions on when rebuilding efforts can be made in earnest, but Talley sees an opportunity for the global industry to get involved when the time is right. That said, it won’t be a cake walk.
“When we're talking about getting involved in Ukraine, there is a steep learning curve," says Talley. "There are cultural and legal barriers that will be new to many, especially to North American companies. So, it's possible. But if a manufacturer or builder wants to acquire our abilities, our knowledge, our culture, cultural understanding and language skills, and ability to bridge that gap, I think we can do that very well.”
About the Author: John McMullen, PCM, is the marketing director for the Modular Building Institute. You can reach him directly at mcmullen@modular.org or on LinkedIn.
More from Modular Advantage
Oregon’s Prevailing Wage Proposal: A Wake-Up Call for Modular Construction
Should House Bill 2688A become law, building projects would increase in price, face longer completion timelines, and produce significantly more waste. The bill also incentivizes contract awards to out of state businesses who would not reinvest their earnings into the local Oregon economy.
Behind the Design of Bethany Senior Terraces, NYC’s First Modular Passive House Senior Housing Project
As more developers seek to meet new regulations for energy efficiency, the team at Murray Engineering has set a new record. With the Bethany Senior Terraces project, Murray Engineering has helped to develop NYC’s first modular structure that fully encompasses passive house principles — introducing a new era of energy efficiency in the energy-conscious city that never sleeps.
How LAMOD is Using Modular to Address Inefficiency, Sustainability, and the Future of Construction
As developers, designers, and contractors seek to understand the evolving needs of the modular industry, no one is as well-versed in the benefits of going modular as Mārcis Kreičmanis. As the co-founder and CBDO of LAMOD in Riga, Latvia, Mārcis has made it his ultimate goal to address the inefficiencies of traditional construction.
From Furniture Builder to ‘Activist Architect’: Stuart Emmons’ Unique Journey
Stuart Emmons was fascinated by buildings at a young age. He remembers building sand cities with his brother during trips to the Jersey shore. His father gave him his first drawing table at the age of ten. Today, he is an experienced architect who received his FAIA in June 2025. The road he took is unique, to say the least.
Forge Craft Architecture + Design: Codes, Contracts, and Intellectual Property
Founding Principal and Director of Modular Practice for Forge Craft Architecture + Design, Rommel Sulit, discusses the implications of codes, contracts, and intellectual property on
modular construction.
Eisa Lee, the “Bilingual” Architect
Now as the founder of XL
Architecture and Modular Design in Ontario, Canada, she applies not just her education as a traditional architect but an entire holistic view on modular design. It’s this expansive view that guides her work on being a true partner that bridges the gap between architects and modular factories as they collaborate on the design process.
Tamarack Grove Engineering: Designing for the Modular Sector
The role of a structural engineer is crucial to the success of a modular project, from initial analysis to construction administration. Tamarack Grove offers structural engineering services — project analysis, plan creation, design creation, and construction administration — for commercial, manufacturing, facilities, public services, and modular. Modular is only one market sector the company serves but it is an increasingly popular one.
Engineer Masters the Art of Listening to His Customers
Since founding Modular Structural Consultants, LLC. in 2014, Yurianto has established a steady following of modular and container-based construction clients, primarily manufacturers. His services often include providing engineering calculations, reviewing drawings, and engineering certification
Inside College Road: Engineering the Modules of One of the World’s Tallest Modular Buildings
College Road is a groundbreaking modular residential development in East Croydon, South London by offsite developer and contractor, Tide, its modular company Vision Volumetric (VV), and engineered by MJH Structural Engineers.
Design for Flow: The Overlooked Power of DfMA in Modular Construction
Unlocking higher throughput, lower costs, and fewer redesigns by aligning Lean production flow with design for manufacturing and assembly.