One Federal Code for Modular Construction: What It Could Mean for the Industry
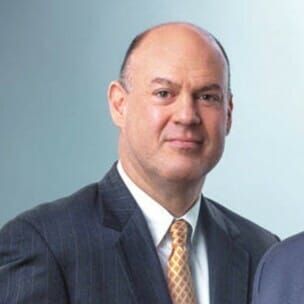
About the author: Tom Hardiman is the executive director of the Modular Building Institute.
Recently I was asked what it would take to grow the modular construction industry to 10% or even 15% of all new construction starts. Let’s start with this – we’re getting there! Seven years ago, volumetric modular construction accounted for 2.14% of the value of all new construction starts in North America (excluding single family). For the year-end 2022, MBI has calculated that figure at 6.03% - nearly triple the market share from 2015. This figure does not include single family modular homes, nor HUD Code, panelized, or tiny homes.
NAHB data puts the number of SF modular homes in the U.S. at around 10,000 annually. Our calculations in 2021 had the number a little higher but was based on less data, so let’s go with the NAHB figure. Including single family modular residential (estimated at around $3 billion annually) the total modular construction industry in North America checks in around $20 billion annually.
Barriers to Greater Adoption of Modular Construction
I’ve said this often – everything about the construction industry was written from the assumption that the building would be constructed in a “conventional” manner (i.e., on site). And each of these aspects represents a potential barrier to growth. A modular construction project presents different risk characteristics than a traditional project. And for many people, understanding and mitigating these differences is a barrier in and of itself.
Let’s discuss a few of these barriers.
Procurement
Design-bid-build (DBB) is the most widely used project delivery method in the United States, according to the Lean Construction Institute of America. Under this method, an owner contracts separately with a designer, who provides complete design documents, and a contractor, who provides the most attractive price bid to execute that design. The modular manufacturer is too far removed from the design and decision-making process with DBB projects. A move towards more Design Build projects and Integrated Project Delivery is more conducive to modular participation.
Contracts
The two most commonly used set of construction document templates come from AIA Docs and Consensus Docs. Until recently, none of these templates addressed the unique circumstances and risk profile associated with modular projects. Over the past three years, MBI worked with Consensus Docs to develop two new “prefabrication” contract templates – the first of their kind.
Financing
The construction cash flow profile for a modular project is perhaps the biggest difference between onsite and offsite. Six years ago, the Canadian Mortgage Housing Corp along with Fannie Mae were reluctant or outright refused to underwrite loans for modular multifamily projects due to a lack of understanding of this difference. Modular projects typically require more cash up front as the manufacturer (often acting as a “super sub-contractor”) must acquire ALL the materials needed to get the building under roof, including paint, carpeting, and fixtures. While construction begins at the factory, onsite work progresses at its typical rate.
Lenders often issue draws based on a percentage of completion and that is often based on what they see on site. Some lenders feel uncomfortable extending more money with a majority of work in the factory. Securing the loan during prefabrication was also cited as a concern. It should not fall to the modular manufacturer to carry the costs of materials well into a project’s completion. Led by MBI’s Government Affairs team, numerous calls and meetings were held with both CMHC and Fannie Mae to help them understand and ultimately overcome these concerns.
The History of MBI's Partnership with CHMC
- In 2018, the Canada Modular Housing Corporation (CMHC) did not finance any modular projects.
- MBI's Government Affairs Director, Jon Hannah-Spacagna, worked with then-CEO, Evan Siddal, to remove that barrier and CMHC agreed to finance commercial and single-family modular projects.
- In 2020, CMHC contacted MBI to assist with their launch of the Rapid Housing Initiative (RHI). This initiative committed $1.7 billion to finance affordable housing projects across Canada using only modular construction and to be completed in 24 months.
- The RHI program received so may quality requests, CMHC increased their funding to $3.2 billion to finance all the requests they received. The result was 10,000 housing units built in 24 months.
- In 2022, CMHC announced a third round of funding for the RHI program, which included an additional $1.5 billion, beginning in 2023.
- Also in 2022, Scotiabank and Bank of Montreal partnered with CMHC and announced their commitment of $10 billion and $12 billion respectively, to support affordable housing development over the next 10 years.
- Jon Hannah-Spacagna is working closely with both banks' leadership teams to help them craft their dispersant criteria on how these funds will be utilized. Both are still finalizing those plans.
One Code to Rule Them All…?
But none of this is to suggest that our industry would be better off with one federal building code similar to the manufactured housing HUD code. It is difficult enough to educate code officials and end users about the differences between modular and HUD code homes. Pulling modular projects out of the IRC/IBC and creating a new federal code would add significantly to that confusion. In fact, I would contend that, ultimately, modular would be absorbed into the HUD code. To me, one of the biggest threats to the modular industry is for HUD to expand its scope to include modular projects.
MBI has a great working relationship with the ICC and will continue to develop tools and resources for code officials to better understand this industry. Which leads to the next point.
Inspection Process
Modular projects must meet the same local building code requirements as their site-built counterparts – most commonly a version of the state adopted IRC or IBC. Given that significant portions of construction occur at the offsite factory location and building modules arrive on site “closed” (electrical, plumbing installed covered by drywall), there needs to be an inspection process to determine code compliance BEFORE the modules arrive to avoid destructive inspections by the local AHJ on site. Thirty-six states and one Canadian province have administrative programs detailing how the inspection process must work. Fourteen states and the other provinces still rely on local inspections. It is imperative that these local code officials understand how our industry works, so they can better understand how to inspect us.
Zoning/HOAs
While not a huge barrier to modular, we continue to see Home Owners Association (HOA) bylaws or even city zoning ordinances that prohibit “mobile, manufactured, and modular homes.” This stems from decades old misconceptions and misunderstanding of the differences between modular and manufactured homes. I think our country needs to address the zoning restrictions on manufactured housing, but that’s not my fight. I’m certain that the three “C” manufacturers that control 80+% of that industry will address this issue. But it is yet another reason against a federal modular building code, as we would likely get swept into this debate.
Adding to these barriers are:
Industry Standards – Five years ago, the issue was that there were no industry standards. Now there are, but the issue is getting more states to adopt them - specifically ICC/MBI 1200 and 1205. These standards will help make the review and approval process much more uniform, driving down costs.
Industry Capacity – Realistically, there simply are not enough modular factories to reach 15+% yet. But more factories are coming online. Aside from the number of factories, company owners need to invest in their people and processes to improve their efficiency and productivity. This will help increase industry capacity. Investment in the industry preferably, would be by the industry. I’ve seen too many cases of outside equity money flooding into the industry, looking to streamline operations, increase profitability, and make a fat ROI within five years or less.
Lack of Government Support – The Canadian Mortgage Housing Corporation (CMHC) went from avoiding loans for modular projects, to approving them, and ultimately embracing modular to address their housing crisis. CHMC launched its Rapid Housing Initiative and funded it with $1.7 billion. In the first round, projects had to be modular and had to be completed in 12 months.
After receiving an overwhelming number of project applications, CMHC added another $1.5 billion for the second round. They have since dropped the modular requirement for their third round but still require projects to be finalized in a timely manner (a requirement which obviously favors the modular industry). Several private banks including Scotia Bank, have jumped on board earmarking as much as $22 billion into the housing initiative. One step to fund $1.5 billion in housing has led to nearly $30 billion invested in similar programs.
No such initiative exists in the U.S. Not only is our federal government drowning in its own red tape, but its solution to housing is also to either throw more money at it or worse, implement programs that are counter-productive, such as the recent rule to expand Davis-Bacon (DB) rates to modular factories.
How the U.S. Federal Government Can Actually Help
Step one would be for the U.S. government policies to “do no more harm.” Representatives from MBI will meet with Congressional leaders later this month to discuss the negative impact that DB will have on our industry. And we plan to take legal action against the USDOL when the final rule is published.
Step two is implementing programs and policies that incentivize greater production of affordable housing. It’s not necessary to earmark modular construction specifically. But the feds COULD incentivize shorter schedules, more sustainable practices, and repeatable designs.
If any political leader is looking for a “moonshot” to address affordable housing, consider this:
For one billion dollars (remember, Canada has invested $30 billion already) offer $10 million in federal tax deductions and credits in the form of accelerated/bonus depreciation for machinery, equipment, or property for any factory that opens or expands specifically to build affordable housing units. Limited to 100 companies, this alone might incentivize the employment of 15,000 factory workers, building 40,000 – 50,000 affordable homes annually. Add additional incentives for the hiring of women, minorities, the disabled, and historically underserved populations. Certainly, this alone wouldn’t solve our housing problem, but it’s a good step in the right direction!
There is no single barrier or issue holding our industry back. Likewise, there is no “silver bullet” solution to help us grow. It will require a collective and cumulative effort on the part of everyone in this industry.
I look forward to continuing these conversations as our industry continues to grow.
More from Modular Advantage
Oregon’s Prevailing Wage Proposal: A Wake-Up Call for Modular Construction
Should House Bill 2688A become law, building projects would increase in price, face longer completion timelines, and produce significantly more waste. The bill also incentivizes contract awards to out of state businesses who would not reinvest their earnings into the local Oregon economy.
Behind the Design of Bethany Senior Terraces, NYC’s First Modular Passive House Senior Housing Project
As more developers seek to meet new regulations for energy efficiency, the team at Murray Engineering has set a new record. With the Bethany Senior Terraces project, Murray Engineering has helped to develop NYC’s first modular structure that fully encompasses passive house principles — introducing a new era of energy efficiency in the energy-conscious city that never sleeps.
How LAMOD is Using Modular to Address Inefficiency, Sustainability, and the Future of Construction
As developers, designers, and contractors seek to understand the evolving needs of the modular industry, no one is as well-versed in the benefits of going modular as Mārcis Kreičmanis. As the co-founder and CBDO of LAMOD in Riga, Latvia, Mārcis has made it his ultimate goal to address the inefficiencies of traditional construction.
From Furniture Builder to ‘Activist Architect’: Stuart Emmons’ Unique Journey
Stuart Emmons was fascinated by buildings at a young age. He remembers building sand cities with his brother during trips to the Jersey shore. His father gave him his first drawing table at the age of ten. Today, he is an experienced architect who received his FAIA in June 2025. The road he took is unique, to say the least.
Forge Craft Architecture + Design: Codes, Contracts, and Intellectual Property
Founding Principal and Director of Modular Practice for Forge Craft Architecture + Design, Rommel Sulit, discusses the implications of codes, contracts, and intellectual property on
modular construction.
Eisa Lee, the “Bilingual” Architect
Now as the founder of XL
Architecture and Modular Design in Ontario, Canada, she applies not just her education as a traditional architect but an entire holistic view on modular design. It’s this expansive view that guides her work on being a true partner that bridges the gap between architects and modular factories as they collaborate on the design process.
Tamarack Grove Engineering: Designing for the Modular Sector
The role of a structural engineer is crucial to the success of a modular project, from initial analysis to construction administration. Tamarack Grove offers structural engineering services — project analysis, plan creation, design creation, and construction administration — for commercial, manufacturing, facilities, public services, and modular. Modular is only one market sector the company serves but it is an increasingly popular one.
Engineer Masters the Art of Listening to His Customers
Since founding Modular Structural Consultants, LLC. in 2014, Yurianto has established a steady following of modular and container-based construction clients, primarily manufacturers. His services often include providing engineering calculations, reviewing drawings, and engineering certification
Inside College Road: Engineering the Modules of One of the World’s Tallest Modular Buildings
College Road is a groundbreaking modular residential development in East Croydon, South London by offsite developer and contractor, Tide, its modular company Vision Volumetric (VV), and engineered by MJH Structural Engineers.
Design for Flow: The Overlooked Power of DfMA in Modular Construction
Unlocking higher throughput, lower costs, and fewer redesigns by aligning Lean production flow with design for manufacturing and assembly.