Affordable Housing Reimagined
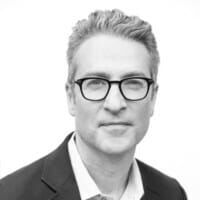
Aaron Holm is the co-founder and co-CEO at Sacramento-based Blokable.
Blokable, a Sacramento-based company, is transforming the housing market, not by addressing how buildings are constructed, but by changing housing development altogether. From site selection to financing, their manufacturing-inspired model is getting rave reviews from the renewable energy community and could permanently change how housing development occurs in this country.
Blokable Roots
Blokable was started by partners Aaron Holm and Nelson Del Rio, who both experienced housing insecurity when they were young. The pair came together to solve the problems of housing and housing development. The company brings together their collective experience with product and technology development, manufacturing, finance, and law, and sees product development and manufacturing as a way to drive down the cost of housing development.
Holm says their purpose is to “change development and the way housing is built.” They believe the real issue with housing, and affordable housing in particular, is the development model. “Construction is sort of an input into the development process, the real issue that needs to be addressed is development. If you take that perspective, it changes everything because it all serves the development process, not construction per se.”
Holm believes that driving down the cost of housing development is the “holy grail” for affordable housing. Blokable set out to prove this with their flagship development, Phoenix Rising, in Washington.
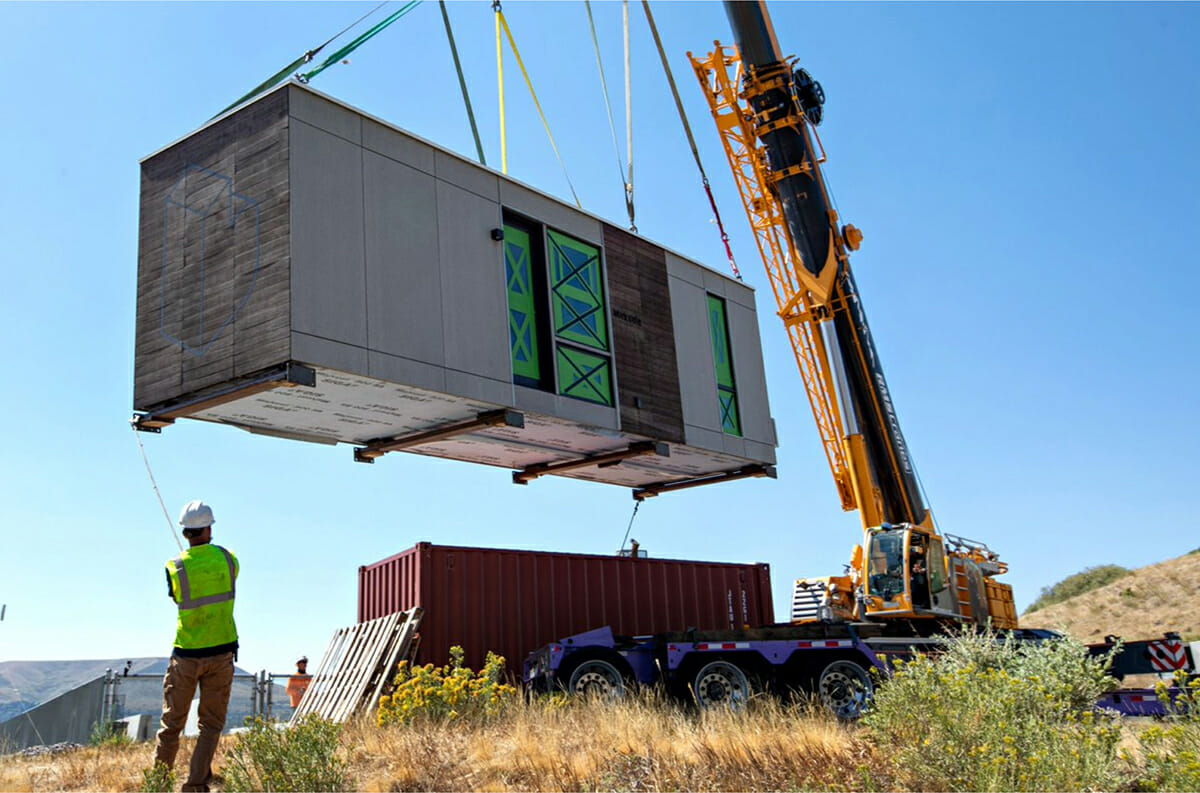
Arrival of Blokable unit at National Renewable Energy Laboratory in Golden, Co.
Phoenix Rising Project
Blokable began their transformation of the development process with a small project to test and validate their next generation structural and mechanical systems. They found a site that would allow them to build twelve connected multi-family buildings for a not-for-profit behavioral health clinic that works with teenagers recovering from substance abuse, Valley Cities.
Holm sees the lack of innovation in affordable housing as a symptom caused by the way projects are funded and go to market. Large projects don’t have the funds to pay companies to do R & D on new technologies or construction methods. And the RFP process ensures that modular construction is very rarely an option. So Holm and Del Rio had to be inventive when it came to securing financing for the project. It took a direct appropriation of funds in the state’s capital budget to ensure that the monies would go to the Valley Cities project.
Partnership with NREL
The National Renewable Energy Lab (NREL) and Wells Fargo teamed up to create a program called the Innovation Incubator (IN2). The goal of the incubator is to advance clean tech companies to market by providing up to $250,000 in technical and research support. The year Blokable got involved, the focus was on energy efficiency and multi-family development.
At the completion of the project and their research, Blokable and NREL worked together to author a report entitled, “Decarbonization During Predevelopment of Modular Building Solutions.” It’s considered groundbreaking in terms of what it points to in regards to how the industry can move towards net zero, all electric, and decarbonized multi-family development.
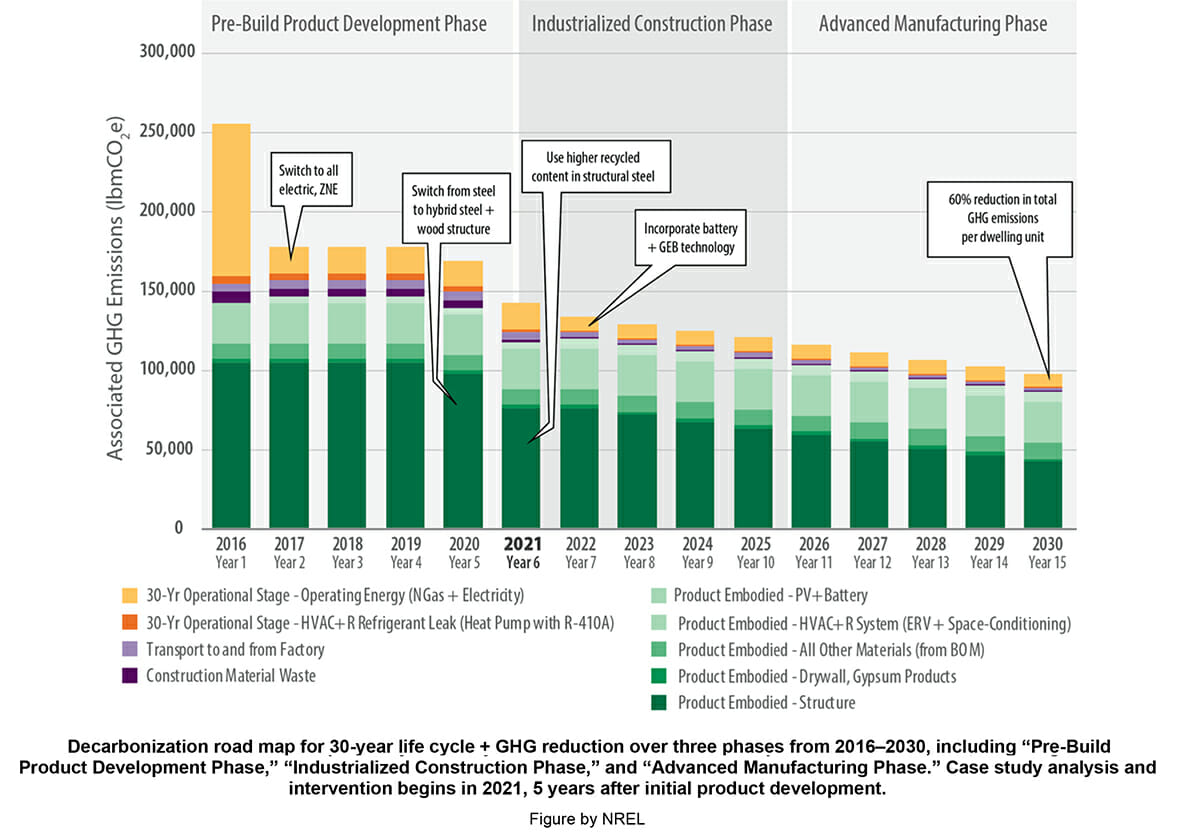
Outcomes of the Study
The biggest outcome of the research is the finding that when pairing construction and manufacturing, reducing energy use and decarbonizing construction doesn’t have to cost more. For the Phoenix Rising project, NREL projected the future costs of energy and the carbon impact of the dwelling units using life cycle assessment strategies. Blokable was able to achieve a projected 60% carbon reduction with essentially zero incremental cost by 2030.
The report also highlighted the fact that once a development builds to net zero energy, the next focus should be on reducing embodied carbon and adding grid-enabled technology to keep the environmental impact moving forward.
Holm believes that to continue to get these kinds of results, the industry must pivot to a manufacturing process, not a construction process.
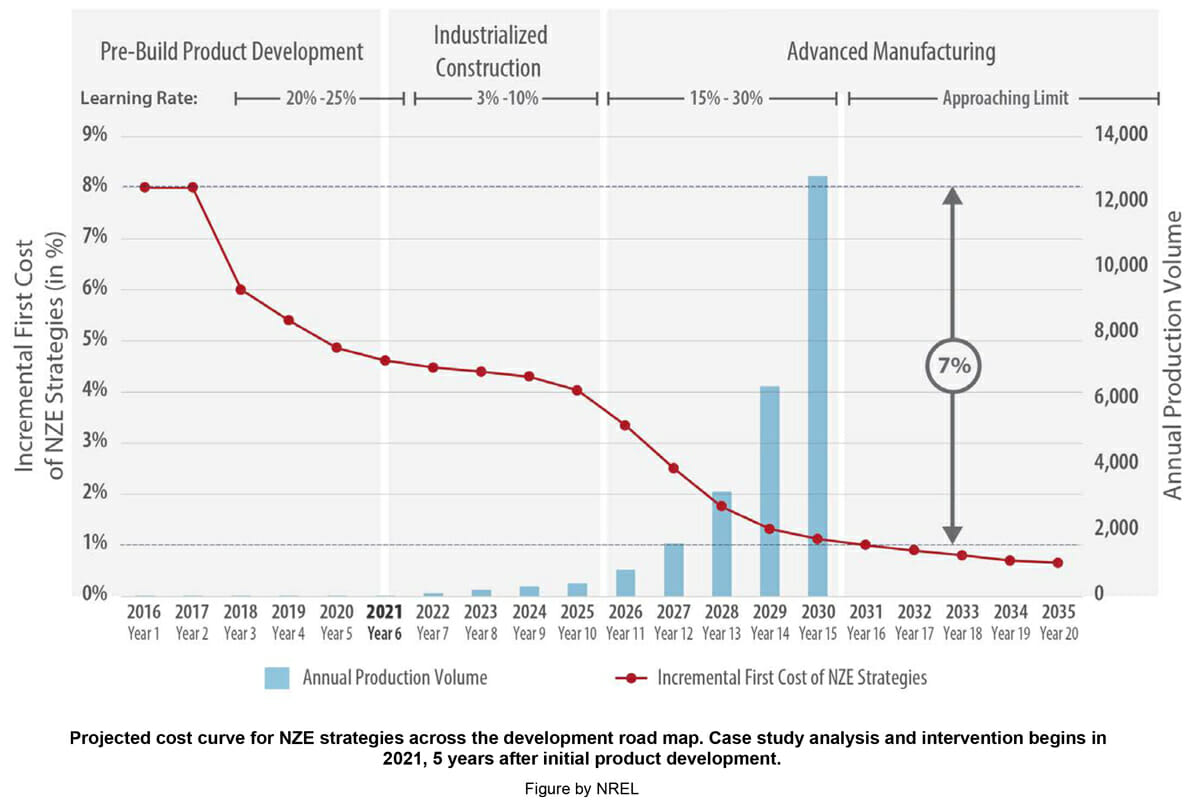
Future of Affordable Housing Development
Based on their results, Blokable sees the future of affordable housing development as using manufacturing processes to drive costs down, then using those savings to create more compelling real estate investments.
The problem is, they didn’t get there overnight. In fact, Blokable's approach is informed by a model that Blokable's other Co-CEO Nelson del Rio successfully pioneered in commercial development in Los Angeles 30 years ago.
“The key was to spend years and a lot of money on the engineering of a building system that can be manufactured using advanced manufacturing assembly technologies, but at the same time can create really flexible floor plans and buildings that meet the market from a housing and real estate perspective,” says Holm. “The next challenge is carving out the financing and the time for early-stage prototyping, so that you know your performance before you start to scale.”
The current development model often creates incentives to provide cheap housing in order to meet the required ROI on affordable housing projects. This leaves those who can least afford it with living spaces that require a lot of energy and aren’t very healthy. By designing high quality housing units that don’t require much energy and are healthy for tenants, this new model can save developers money, requiring less subsidies and making financing easier to find. When the market provides the incentive, there will be more opportunities for modular construction like Blokable provides.
The next step for Blokable is beginning development in California, a state with some of the strictest structural and energy codes in the country. They’ve invested time and money since the Phoenix Rising project to improve the engineering of their manufacturable building system to meet California code. They are set to provide high quality housing for less cost than conventional construction methods. Their goal is to be able to provide affordable housing that leads to home ownership and equity for the residents. This builds communities and can change whole neighborhoods. In fact, they’ve seen that transformation in Washington near their first development. The corner has transformed from a crime-ridden, rough area, to one that’s lit at night, safer, and that provides the best housing for miles around.
Report: Decarbonization During Predevelopment of Modular Building Solutions
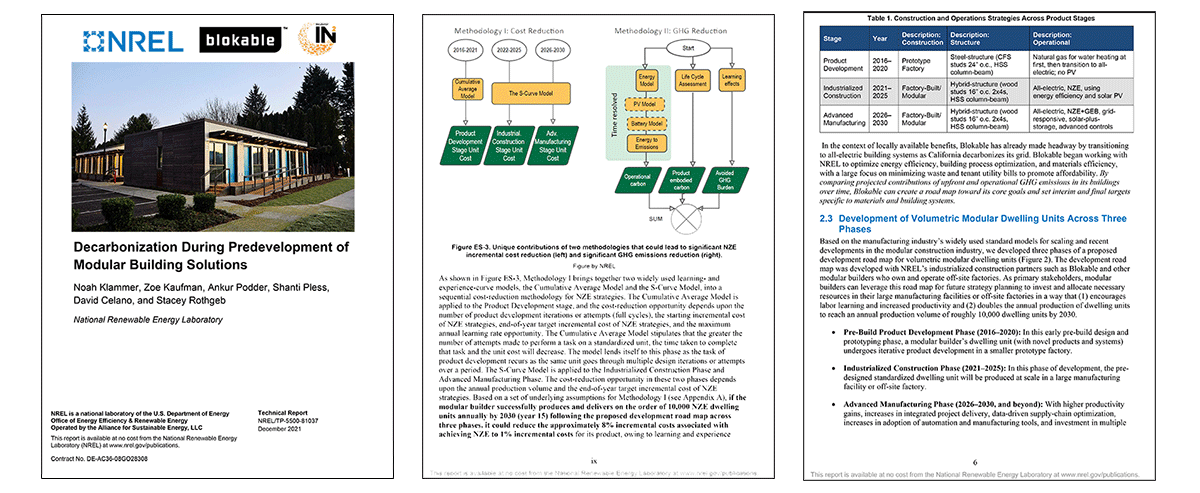
To date, net zero energy (NZE) has served as a tangible preliminary target for high-performance building in both voluntary certification programs and, now, building energy codes. Industrialized construction is one approach to efficiently achieve affordable housing that implements NZE strategies. These dwelling units are often all-electric and outfitted with rooftop solar arrays, and they produce at least as much energy through on-site renewable resources as they consume each year, enhancing energy affordability.
However, the full potential of affordable, NZE housing has not yet been tapped, due in part to incremental costs of NZE strategies surpassing traditional budgets for affordable housing projects. Additionally, as new construction becomes more energy efficient, the greenhouse gas (GHG) emissions from the construction industry play a proportionately larger role in environmental impact and must be considered when evaluating methods of construction.
There has been limited investigation into the trade-offs between site-built and industrialized construction buildings from the perspective of reducing the incremental cost of NZE strategies and reducing GHG emissions resulting from upfront and operational emissions that are “embodied” in the building’s life.
This report details actionable pathways for the industry to leverage advanced building construction, reduce NZE incremental costs, and achieve significant GHG emissions reduction by 2030. Download the complete report at nrel.gov.
About the Author: Dawn Killough is a freelance construction writer with over 25 years of experience working with construction companies, subcontractors and general contractors. Her published work can be found at dkilloughwriter.com.
More from Modular Advantage
Oregon’s Prevailing Wage Proposal: A Wake-Up Call for Modular Construction
Should House Bill 2688A become law, building projects would increase in price, face longer completion timelines, and produce significantly more waste. The bill also incentivizes contract awards to out of state businesses who would not reinvest their earnings into the local Oregon economy.
Behind the Design of Bethany Senior Terraces, NYC’s First Modular Passive House Senior Housing Project
As more developers seek to meet new regulations for energy efficiency, the team at Murray Engineering has set a new record. With the Bethany Senior Terraces project, Murray Engineering has helped to develop NYC’s first modular structure that fully encompasses passive house principles — introducing a new era of energy efficiency in the energy-conscious city that never sleeps.
How LAMOD is Using Modular to Address Inefficiency, Sustainability, and the Future of Construction
As developers, designers, and contractors seek to understand the evolving needs of the modular industry, no one is as well-versed in the benefits of going modular as Mārcis Kreičmanis. As the co-founder and CBDO of LAMOD in Riga, Latvia, Mārcis has made it his ultimate goal to address the inefficiencies of traditional construction.
From Furniture Builder to ‘Activist Architect’: Stuart Emmons’ Unique Journey
Stuart Emmons was fascinated by buildings at a young age. He remembers building sand cities with his brother during trips to the Jersey shore. His father gave him his first drawing table at the age of ten. Today, he is an experienced architect who received his FAIA in June 2025. The road he took is unique, to say the least.
Forge Craft Architecture + Design: Codes, Contracts, and Intellectual Property
Founding Principal and Director of Modular Practice for Forge Craft Architecture + Design, Rommel Sulit, discusses the implications of codes, contracts, and intellectual property on
modular construction.
Eisa Lee, the “Bilingual” Architect
Now as the founder of XL
Architecture and Modular Design in Ontario, Canada, she applies not just her education as a traditional architect but an entire holistic view on modular design. It’s this expansive view that guides her work on being a true partner that bridges the gap between architects and modular factories as they collaborate on the design process.
Tamarack Grove Engineering: Designing for the Modular Sector
The role of a structural engineer is crucial to the success of a modular project, from initial analysis to construction administration. Tamarack Grove offers structural engineering services — project analysis, plan creation, design creation, and construction administration — for commercial, manufacturing, facilities, public services, and modular. Modular is only one market sector the company serves but it is an increasingly popular one.
Engineer Masters the Art of Listening to His Customers
Since founding Modular Structural Consultants, LLC. in 2014, Yurianto has established a steady following of modular and container-based construction clients, primarily manufacturers. His services often include providing engineering calculations, reviewing drawings, and engineering certification
Inside College Road: Engineering the Modules of One of the World’s Tallest Modular Buildings
College Road is a groundbreaking modular residential development in East Croydon, South London by offsite developer and contractor, Tide, its modular company Vision Volumetric (VV), and engineered by MJH Structural Engineers.
Design for Flow: The Overlooked Power of DfMA in Modular Construction
Unlocking higher throughput, lower costs, and fewer redesigns by aligning Lean production flow with design for manufacturing and assembly.