Plug-and-Play: The Emergence of Modular Data Centers
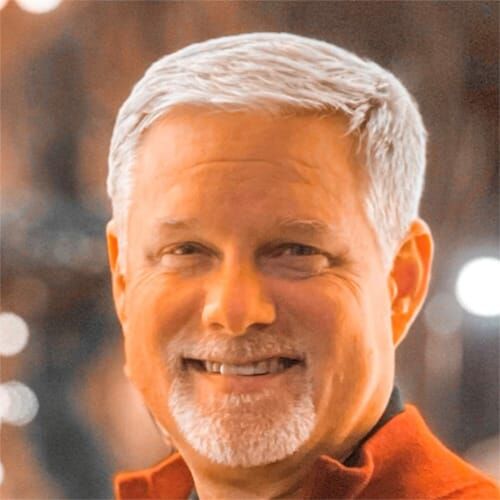
Kent Anderson is the Senior Business Development Manager at Wesco Distribution.
As organizations across industries rapidly push to digitize and modernize their operations, buildings and factories — embracing IoT and AI along the way — they need to ensure their data center capacity can keep pace and do so quickly. After all, these innovative applications require a certain level of computing power to run. That demand is fueling the rapid rise of data center construction projects. According to research from McKinsey, U.S. data center growth is expected to increase 10 percent per year through 2030.
However, simply adding more computing power is not as straightforward as it seems. Traditional data centers can take anywhere from 12 months to two years or more to design, build and begin operating. Plus, organizational complexities and ongoing supply chain challenges can hinder a rollout, especially in more remote areas where logistics and labor availability are especially challenging. As a result, modular data centers have emerged as a workaround for a variety of applications.
These structures are built offsite and fully assembled, complete with HVAC and electrical. Once completed and inspected, modular data centers can be delivered to the jobsite ready to support the speed, volume and data capacity requirements that organizations so desperately need. All that’s left to do is simply drop in the hardware.
Let’s take a closer look at why the “plug and play” capabilities of a modular data centers matter right now.
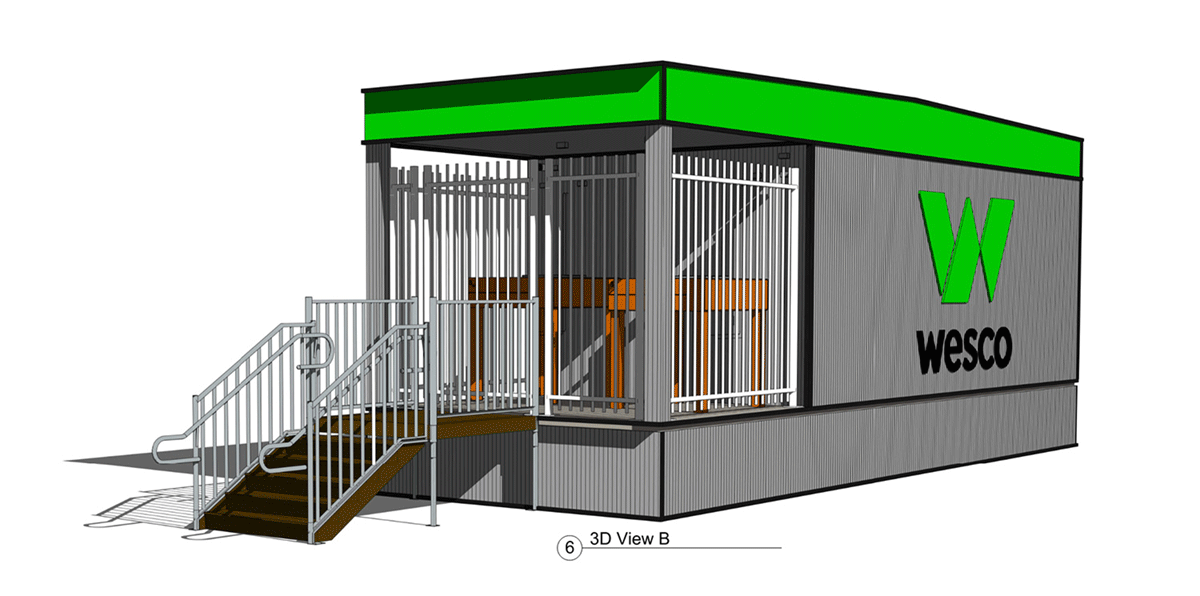
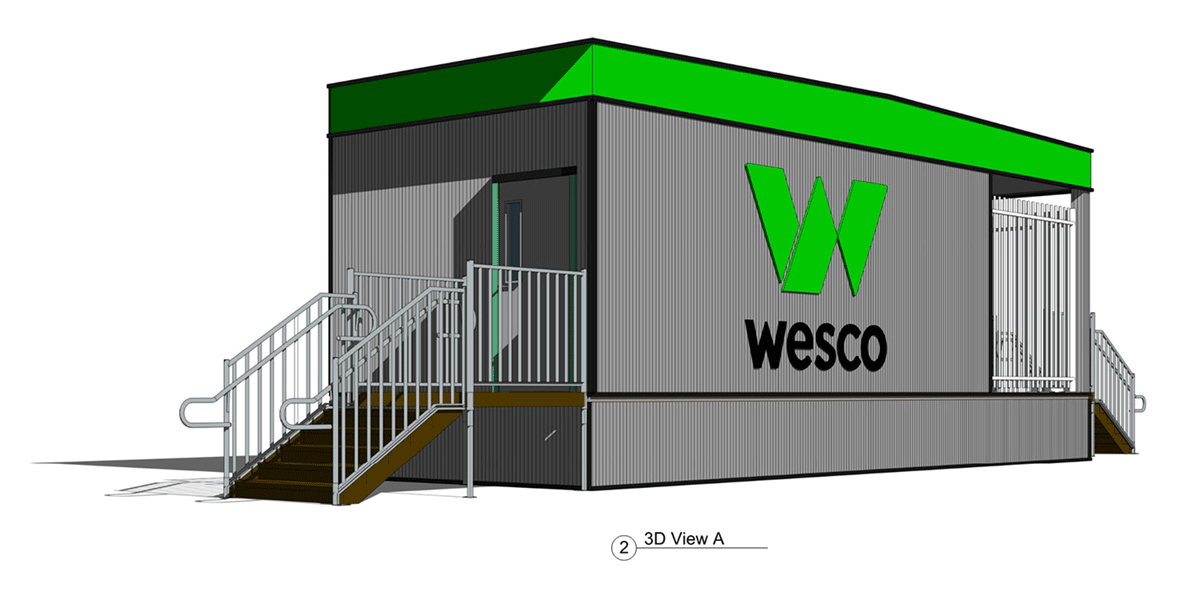
Renderings of a modular data center from Wesco Distribution.
1. Daunting Data Demands
If an organization identifies the need for more computing power, they also probably recognize they need it immediately. However, customized data centers have lengthy lead times and speed of deployment matters if organizations are to truly embrace the efficiency and competitive advantages that come with digitization and AI innovation. Waiting two years to build a data center with the necessary processing power isn’t a viable option.
Modular data centers can alleviate that burden two to three times faster and help companies prepare for future data demands as well. Customizable and built with flexibility in mind, these structures can be relocated to another location to meet evolving data needs or (given their inherent ease and speed of deployment) simply re-ordered to grow the system and enhance processing power as required.
This is especially valuable in locations where space is at a premium such as major metropolitan areas, healthcare and higher-education campuses, or office spaces. Modular data centers can be leveraged as expansion is occurring, and relocated as it completes, seamlessly addressing evolving data demands.
2. Supply Chain Constraints Remain a Constant
The pandemic may be over, but the effect on the supply chain is long-lasting. Sourcing materials is more complicated, more unpredictable, and more expensive than in years past. For data centers, this is especially true as certain equipment or materials —
specifically electrical gear — currently have long lead times. Any delays tied to material availability (or lack thereof) will obviously hinder construction. The longer a project takes, the more capital investment is required to see it through to completion — and all the while data demands are still not being met.
Modular data centers can bypass many of those concerns. Since they’re produced offsite, they arrive almost fully assembled, making them essentially plug and play. This virtually eliminates the potential scenario of waiting onsite for critical or scarce components to arrive.
However, this underscores the need to bring partners in early when considering modular data centers. Whether the equipment is produced offsite or onsite, there is still the potential to run into supply chain challenges for important parts or materials. Bringing in partners early on can help avoid these challenges by ensuring you have the equipment and materials you need, when you need it.
3. Labor Concerns
Skilled labor continues to be a challenge across the construction industry. Employing the right set of people to ensure the data center deployment process is done as quickly as possible is essential. In remote areas, sourcing labor is especially difficult. Crews must be meticulously scheduled and provided with the correct tools and resources to be successful.
Modular construction can help avoid these issues. Skilled workers are already on staff at the production facility, so there’s no need to source additional labor, or compete with other companies for skilled workers who are in high demand. Also, having those skilled workers on staff helps ensure consistency and familiarity with the overall product assembly.
These factors and others are driving organizations to circumvent the traditional approach to data center construction projects and evaluate a new product -- modular structures. Built with speed, flexibility, and redundancy in mind, modular data centers provide the plug-and-play computing power organizations need amidst innovation, uncertainty and more.
More from Modular Advantage
Oregon’s Prevailing Wage Proposal: A Wake-Up Call for Modular Construction
Should House Bill 2688A become law, building projects would increase in price, face longer completion timelines, and produce significantly more waste. The bill also incentivizes contract awards to out of state businesses who would not reinvest their earnings into the local Oregon economy.
Behind the Design of Bethany Senior Terraces, NYC’s First Modular Passive House Senior Housing Project
As more developers seek to meet new regulations for energy efficiency, the team at Murray Engineering has set a new record. With the Bethany Senior Terraces project, Murray Engineering has helped to develop NYC’s first modular structure that fully encompasses passive house principles — introducing a new era of energy efficiency in the energy-conscious city that never sleeps.
How LAMOD is Using Modular to Address Inefficiency, Sustainability, and the Future of Construction
As developers, designers, and contractors seek to understand the evolving needs of the modular industry, no one is as well-versed in the benefits of going modular as Mārcis Kreičmanis. As the co-founder and CBDO of LAMOD in Riga, Latvia, Mārcis has made it his ultimate goal to address the inefficiencies of traditional construction.
From Furniture Builder to ‘Activist Architect’: Stuart Emmons’ Unique Journey
Stuart Emmons was fascinated by buildings at a young age. He remembers building sand cities with his brother during trips to the Jersey shore. His father gave him his first drawing table at the age of ten. Today, he is an experienced architect who received his FAIA in June 2025. The road he took is unique, to say the least.
Forge Craft Architecture + Design: Codes, Contracts, and Intellectual Property
Founding Principal and Director of Modular Practice for Forge Craft Architecture + Design, Rommel Sulit, discusses the implications of codes, contracts, and intellectual property on
modular construction.
Eisa Lee, the “Bilingual” Architect
Now as the founder of XL
Architecture and Modular Design in Ontario, Canada, she applies not just her education as a traditional architect but an entire holistic view on modular design. It’s this expansive view that guides her work on being a true partner that bridges the gap between architects and modular factories as they collaborate on the design process.
Tamarack Grove Engineering: Designing for the Modular Sector
The role of a structural engineer is crucial to the success of a modular project, from initial analysis to construction administration. Tamarack Grove offers structural engineering services — project analysis, plan creation, design creation, and construction administration — for commercial, manufacturing, facilities, public services, and modular. Modular is only one market sector the company serves but it is an increasingly popular one.
Engineer Masters the Art of Listening to His Customers
Since founding Modular Structural Consultants, LLC. in 2014, Yurianto has established a steady following of modular and container-based construction clients, primarily manufacturers. His services often include providing engineering calculations, reviewing drawings, and engineering certification
Inside College Road: Engineering the Modules of One of the World’s Tallest Modular Buildings
College Road is a groundbreaking modular residential development in East Croydon, South London by offsite developer and contractor, Tide, its modular company Vision Volumetric (VV), and engineered by MJH Structural Engineers.
Design for Flow: The Overlooked Power of DfMA in Modular Construction
Unlocking higher throughput, lower costs, and fewer redesigns by aligning Lean production flow with design for manufacturing and assembly.