Oldivai on 31st – Modular Housing, Rinse and Repeat
What Makes Oldivai Different?
Fast and high-quality construction rarely go together—until now. Oldivai on 31st (aka Project Zero) redefined modular housing by combining speed with exceptional standards. Developed as the inaugural project for Oldivai Capital, this 7,280-squarefoot, three-story complex wasn’t just designed to address Spokane’s growing housing shortage, it was created to serve as a prototype for scalable, repeatable workforce housing solutions.
With a “kit-of-parts” approach, Oldivai on 31st demonstrated how a predesigned layout could deliver consistent programming and rapid deployment. This project didn’t just match the site; it set a standard for matching the design to sites across multiple locations. With five additional projects and a larger multi-unit complex slated for 2025, this proof of concept has already paved the way for future developments.
Quick Facts
- Project Name: Oldivai on 31st
- Location: Spokane, Washington
- Building Type:
Multifamily Apartments - Number of Units: 10
- Number of Modules: 15
- Total Area: 7,280 square feet
- Timeline:
- Groundbreaking: July
31, 2023 - Modular Set: Jan. 29 – Feb. 1, 2024 (4 days)
- (TCO) Substantial
Completion: July 2, 2024 (310 days from site start)
- Groundbreaking: July
- Total Construction Cost: $2,692,850
Why Modular? Why Now?
Traditional construction simply can’t keep up with the rising demand for housing. Modular construction offers not just a faster solution but a smarter one. Oldivai on 31st tackled inefficiencies head-on, sidestepping weather delays and labor shortages to deliver a completed project in under a year. But this wasn’t just about speed. The real challenge was scalability: could modular construction deliver consistent quality across future developments? Project Zero answered that with a resounding yes, setting a new standard for efficiency, precision, and repeatability in multifamily housing.
Designing for Precision and Efficiency
At Oldivai on 31st, efficiency meant doing things right from the start. Every stage of the process was optimized to maximize quality while minimizing delays. Building modules in a climate-controlled factory protected materials from Spokane’s unpredictable weather. This method reduced waste, ensured tighter tolerances, and allowed interiors, mechanical systems, and finishes to be 80% complete before shipping. Modules arrived on-site nearly move-in ready. Plumbing, electrical systems, and finishes were pre-installed, leaving minimal onsite labor. The modules were craned into place in just four days, bypassing typical delays caused by weather or onsite inefficiencies. From groundbreaking to substantial completion, Oldivai was finished in 310 days, shaving weeks off traditional construction timelines.
Challenges and Lessons Learned: Smarter Construction Every Step of the Way
Every challenge faced during the development of this project became an opportunity to refine modular construction processes. These obstacles not only shaped the Project Zero’s success but also established a framework for improving future developments.
Think Lifecycle, Build Smarter
The journey from factory fabrication to tenant move-in requires planning for every phase of a building’s lifecycle. At Oldivai, the team embraced a “start with the end in mind” philosophy. Features like standardized crawl space and attic access simplified future maintenance, ensuring the building functioned efficiently long after completion. This forward-thinking approach highlighted the importance of designing for long-term usability—not just immediate results.
Streamlining Communication
Early misalignments between architectural and modular plans caused delays and confusion, underscoring the need for clear documentation and communication.
- Solution: A unified labeling system and centralized digital repository ensured that all stakeholders—from architects to contractors—worked from the same, up-to-date information.
- Result: Improved consistency across teams, reduced miscommunication, and faster resolutions to onsite challenges.
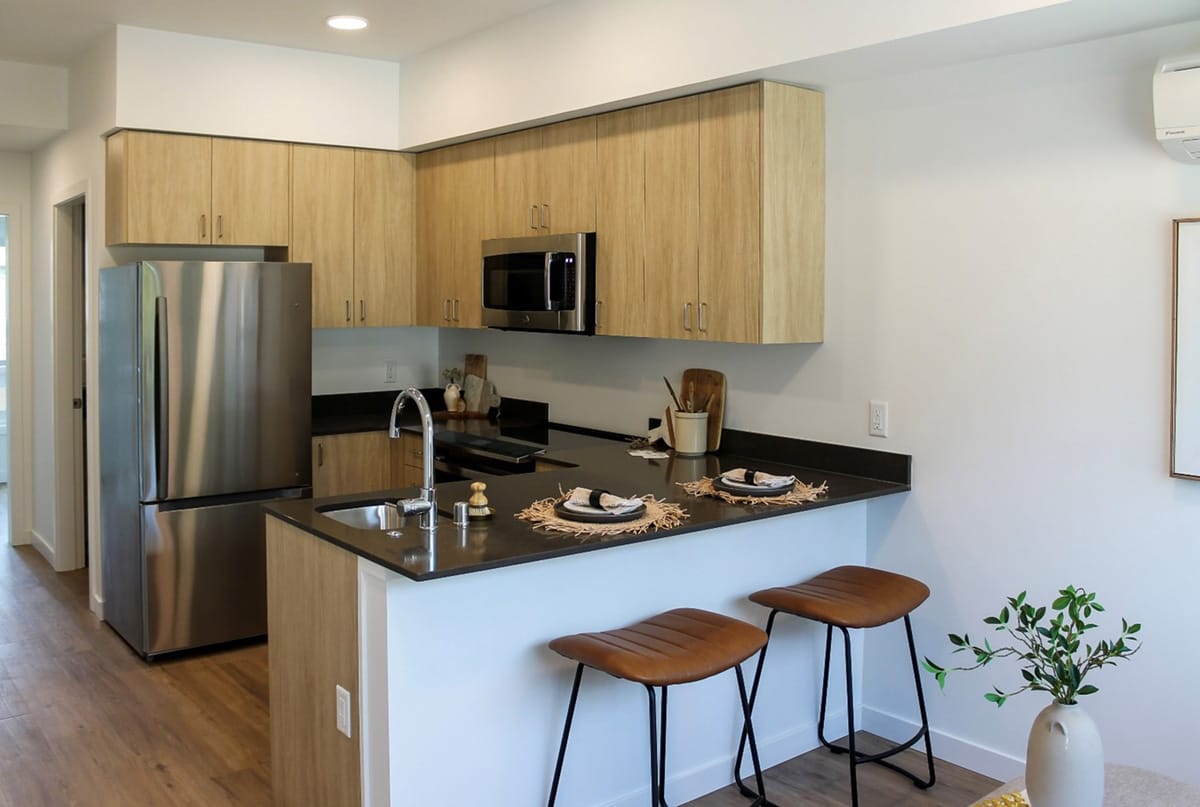
Fire Safety and Critical Systems Coordination
Ensuring compliance with fire safety requirements was a recurring challenge. Factory and onsite integration revealed the need for better coordination in critical systems like plumbing and fire suppression.
- Solution: The team expanded zones for fire suppression systems and standardized plumbing bays to simplify installation. Detailed firestopping designs were also integrated into the architectural set to meet inspection standards.
- Result: These adjustments avoided costly delays and have become a new standard for future modular projects.
Continuous Improvement
Modular construction thrives on iteration. Every success and setback at Oldivai informed a scalable framework for the future. Lessons weren’t just learned—they were applied, proving that modular isn’t just about speed but about smarter, more reliable results.
- Standardization for Simplicity: Consistent fixtures, finishes, and system designs reduced variability and accelerated production.
- Flexibility for the Unexpected: Challenges like fire safety revisions reinforced the importance of adaptability, ensuring that future projects are equipped to handle surprises.
Continuous Improvement
The insights from Oldivai on 31st offer practical guidelines for future modular developments:
- Design for the Lifecycle: Plan beyond completion—incorporate features that simplify maintenance, upgrades, and tenant satisfaction.
- Invest in Systems: Clear documentation, precise Oldivai on 31st Level 1 Floorplan labeling, and real-time updates prevent errors and build trust across teams.
- Standardize for Scalability: Uniformity in fixtures and finishes ensures consistent quality and reduces variability in production.
- Embrace Feedback: Every project provides lessons. Use them to refine processes and create smarter solutions.
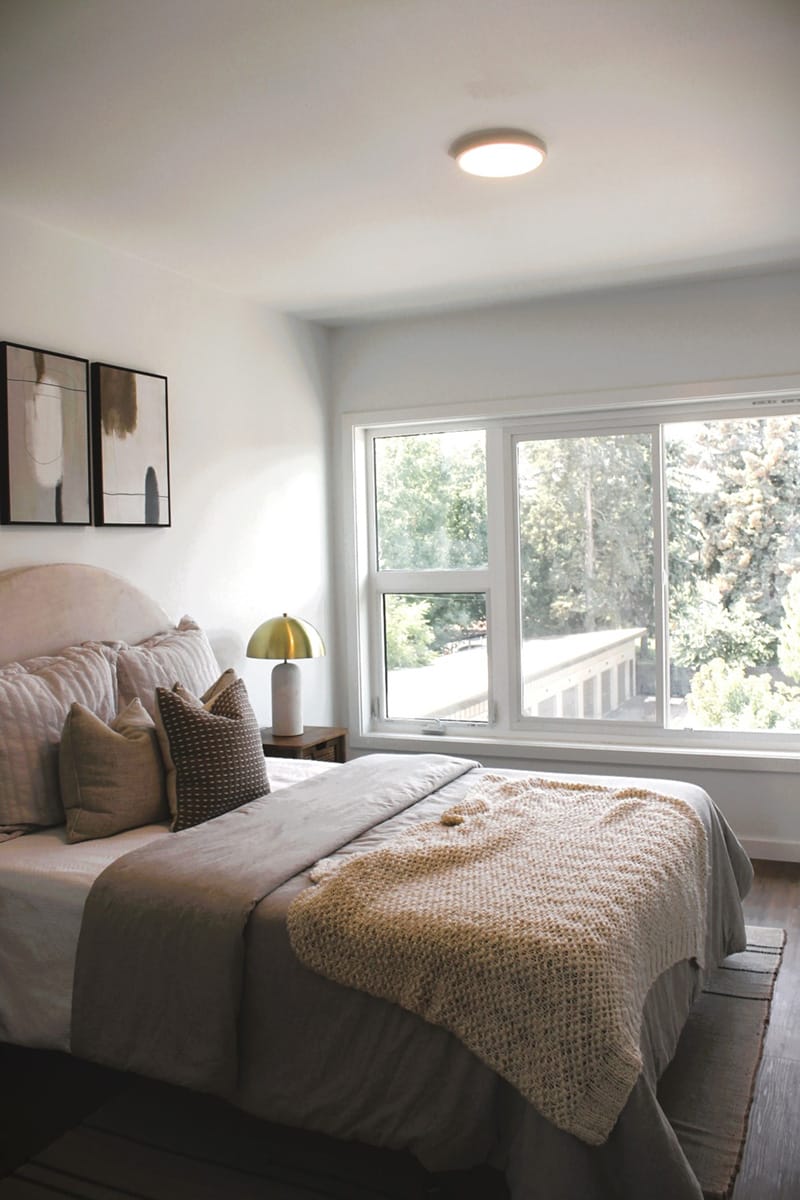
Cost Effectiveness
With a total cost of $2,692,850, Oldivai on 31st demonstrated that cost savings don’t come from cutting corners—they come from doing things right. Time is money, and Project Zero proved that faster construction saves both.
Conclusion: Building Better, Smarter, and Faster
For Jackson | Main Architecture and Oldivai Capital, Project Zero isn’t just a success—it’s a promise. This project demonstrates that better, faster, and smarter construction is achievable without compromising durability or design. For tenants, it offers a home they can trust, built to the highest standards. More than a single modular project, Oldivai on 31st is the foundation of a larger vision—one that extends far beyond Spokane and will shape housing solutions for years to come.
More from Modular Advantage
Oregon’s Prevailing Wage Proposal: A Wake-Up Call for Modular Construction
Should House Bill 2688A become law, building projects would increase in price, face longer completion timelines, and produce significantly more waste. The bill also incentivizes contract awards to out of state businesses who would not reinvest their earnings into the local Oregon economy.
Behind the Design of Bethany Senior Terraces, NYC’s First Modular Passive House Senior Housing Project
As more developers seek to meet new regulations for energy efficiency, the team at Murray Engineering has set a new record. With the Bethany Senior Terraces project, Murray Engineering has helped to develop NYC’s first modular structure that fully encompasses passive house principles — introducing a new era of energy efficiency in the energy-conscious city that never sleeps.
How LAMOD is Using Modular to Address Inefficiency, Sustainability, and the Future of Construction
As developers, designers, and contractors seek to understand the evolving needs of the modular industry, no one is as well-versed in the benefits of going modular as Mārcis Kreičmanis. As the co-founder and CBDO of LAMOD in Riga, Latvia, Mārcis has made it his ultimate goal to address the inefficiencies of traditional construction.
From Furniture Builder to ‘Activist Architect’: Stuart Emmons’ Unique Journey
Stuart Emmons was fascinated by buildings at a young age. He remembers building sand cities with his brother during trips to the Jersey shore. His father gave him his first drawing table at the age of ten. Today, he is an experienced architect who received his FAIA in June 2025. The road he took is unique, to say the least.
Forge Craft Architecture + Design: Codes, Contracts, and Intellectual Property
Founding Principal and Director of Modular Practice for Forge Craft Architecture + Design, Rommel Sulit, discusses the implications of codes, contracts, and intellectual property on
modular construction.
Eisa Lee, the “Bilingual” Architect
Now as the founder of XL
Architecture and Modular Design in Ontario, Canada, she applies not just her education as a traditional architect but an entire holistic view on modular design. It’s this expansive view that guides her work on being a true partner that bridges the gap between architects and modular factories as they collaborate on the design process.
Tamarack Grove Engineering: Designing for the Modular Sector
The role of a structural engineer is crucial to the success of a modular project, from initial analysis to construction administration. Tamarack Grove offers structural engineering services — project analysis, plan creation, design creation, and construction administration — for commercial, manufacturing, facilities, public services, and modular. Modular is only one market sector the company serves but it is an increasingly popular one.
Engineer Masters the Art of Listening to His Customers
Since founding Modular Structural Consultants, LLC. in 2014, Yurianto has established a steady following of modular and container-based construction clients, primarily manufacturers. His services often include providing engineering calculations, reviewing drawings, and engineering certification
Inside College Road: Engineering the Modules of One of the World’s Tallest Modular Buildings
College Road is a groundbreaking modular residential development in East Croydon, South London by offsite developer and contractor, Tide, its modular company Vision Volumetric (VV), and engineered by MJH Structural Engineers.
Design for Flow: The Overlooked Power of DfMA in Modular Construction
Unlocking higher throughput, lower costs, and fewer redesigns by aligning Lean production flow with design for manufacturing and assembly.