Top Five Benefits of Modular Office Space
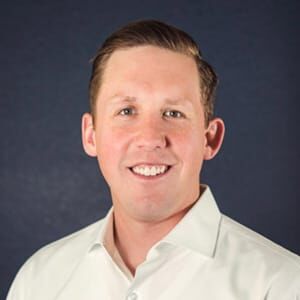
Joshua Nabb, PE, is the Vice President & General Manager at ATCO Structures & Logistics (USA), Inc.
Modular office spaces are transforming how businesses think about their work environments. These innovative structures offer a mix of flexibility, efficiency, and sustainability, making them a smart choice for companies looking to gain an advantage.
Here are five benefits of choosing modular office spaces:
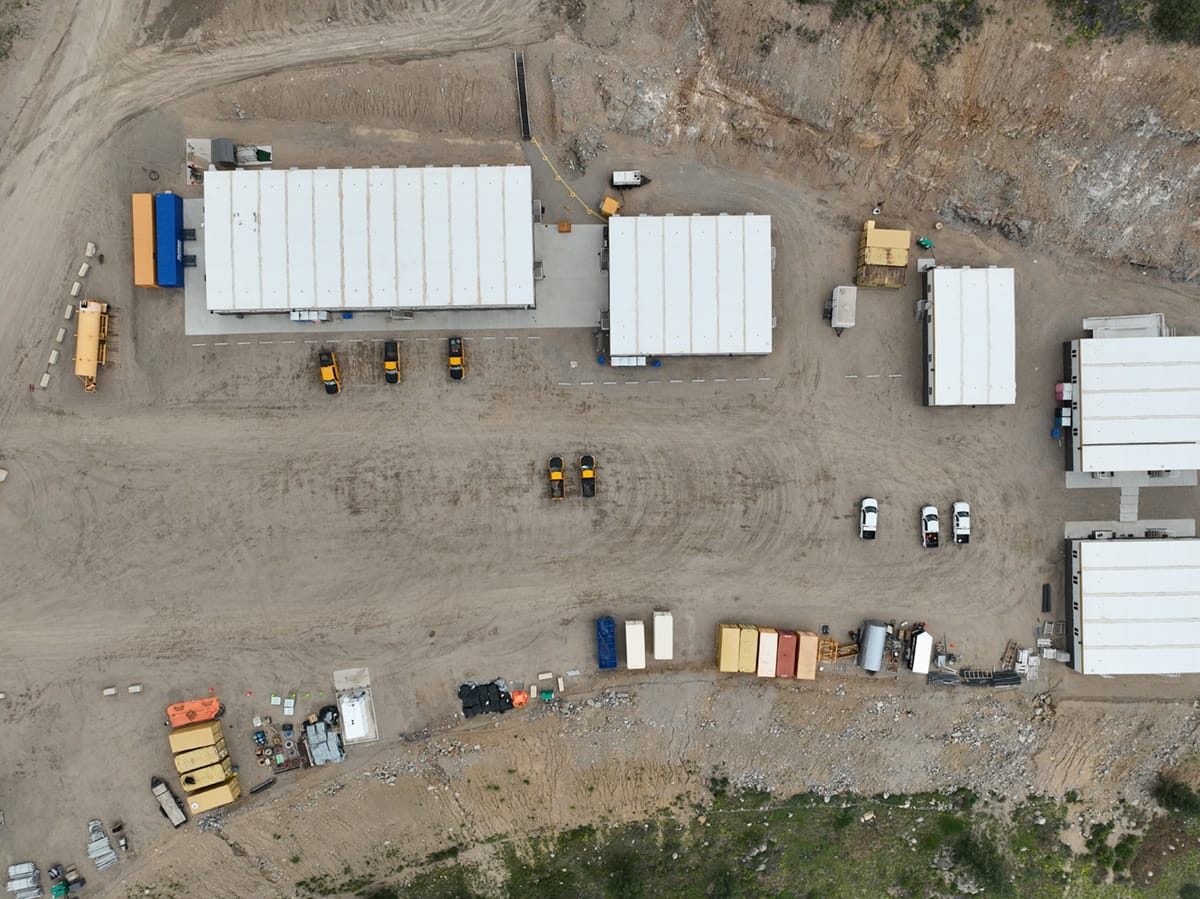
1. Speed to Market: Quick Installation
Modular construction can significantly speed up project timelines. According to the McKinsey Modular Construction Report 2019, modular projects are completed 20-50 per cent faster than traditional construction. This speed is a result of factory-based construction, avoiding weather and site-related delays.
2. Lower Costs: Save Time and Money
Modular construction can potentially lower costs by streamlining three key areas:
Shortening Construction Timelines
Modular buildings are prefabricated in a controlled factory environment, which fast-tracks the overall construction process. This expedited timeline means quicker project completion, enabling businesses to commence operations sooner.
Lowering Labor Expenses
Modular construction requires less labor to get the job done, decreasing the number of workers required onsite, making the building process both more economical and faster, especially in areas governed by prevailing wages.
Minimizing Material Waste
The repeatable, factory-controlled production process for modular buildings allows for more precise material usage and reduces over-ordering. Materials are kept and used in ideal conditions, reducing waste or damage.
3. Flexibility: Easy Reconfiguration
Modular offices are designed for adaptability, making it easy to modify floorplans according to changing business needs. In the ever-evolving business landscape, being able to quickly expand, downsize, or modify your office space without major construction is a key advantage.
Another standout feature of modular offices is their portability. If you need to move your business, your office space can move with you. This mobility ensures that your office space investment continues to pay off, no matter where your business takes you.
4. Smooth Integration: Minimal Disruption
Modular building installation minimizes workplace interference, ensuring daily operations remain largely undisturbed during the installation process.
5. Sustainable
Modular offices are environmentally friendly, use materials more efficiently, and generate less waste than conventional office building construction.
At ATCO Structures, our site offices are built to local building codes, come in a variety of shapes and sizes, and can be installed in any climate or terrain. Learn more about our durable and portable mobile offices.
Case Study: Gross Reservoir, Colorado Project
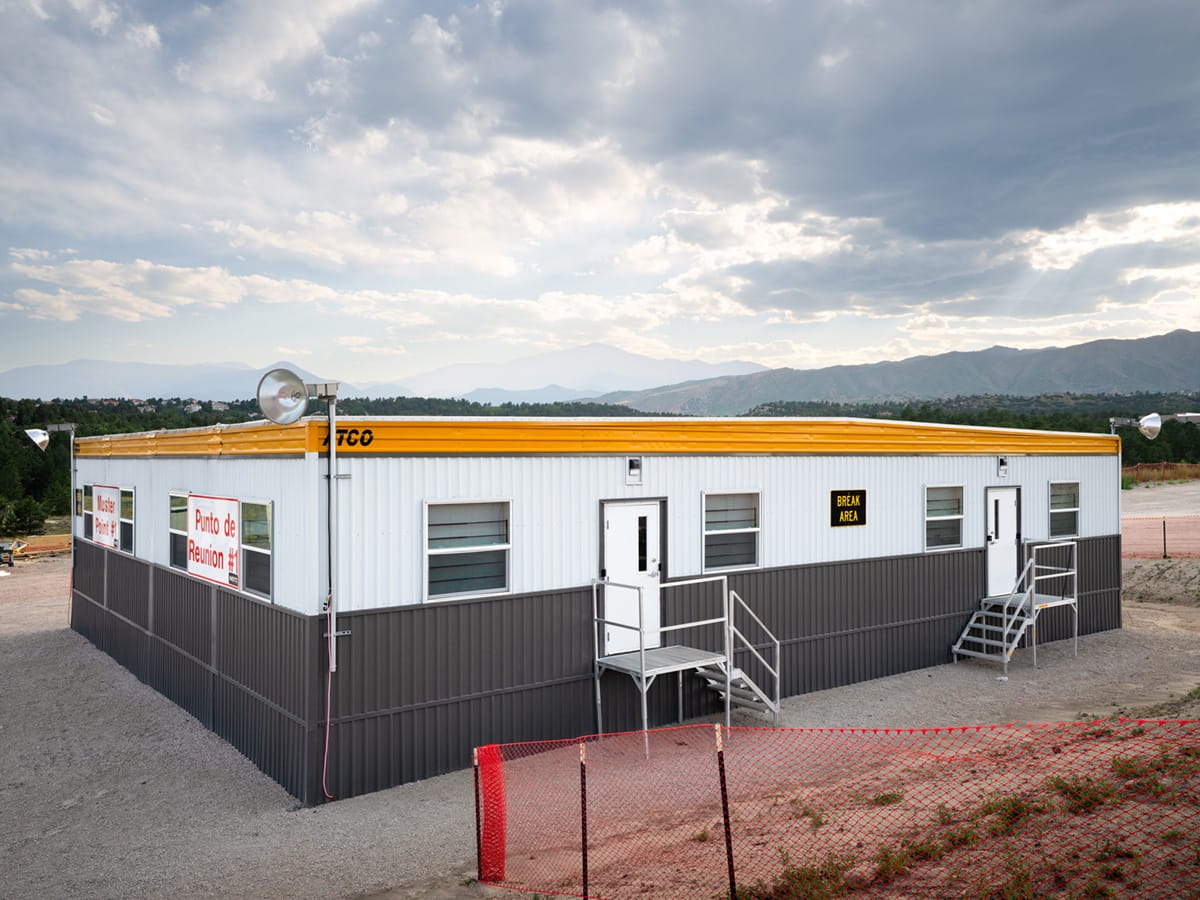
ATCO successfully designed, manufactured, and installed a leased temporary office compound for a major General Contractor involved in a long-term reservoir infrastructure project in Colorado’s Rocky Mountains. The modular units were specifically designed to endure high winds, wildfires, and rugged terrain.
The office compound comprised of 12x60 office units, 12x60 restroom units, and modular office complexes ranging from 3 units (36x60) to 12 units (144x60) in size. In total, 39 units (13 separate office complexes) were designed, manufactured, and installed for the project.
Upon the contractor’s request, ATCO swiftly completed fully engineered and compliant drawing packages, securing Colorado Division of Housing (DOH) approval within four weeks. ATCO’s in-house design and engineering capabilities, with experience across nearly all 50 states, enable ATCO to expediently design modular spaces for any application and geographic location.
Key design features of this project included:
- 170mph wind rating for all units and complexes
- Impact-resistant 3M film on all windows
- 90-minute fire rating throughout the entire building
- 60psf snow load capacity
- Construction with 100% fire-retardant lumber
- Seismic Class D compliance
- 60ft steel clear span roof truss construction
- Metal exterior cladding
- White 60 mil EPDM roof membrane
- Bluetooth LED lighting throughout
Following state design package approval, ATCO manufactured the custom units within eight weeks at our 100,000 sq-ft East Texas manufacturing facility. Our facility, capable of delivering up to 500 units annually, ensures no project is too big or too small.
ATCO’s turnkey modular services enabled the completion of this project from inception to fully installed and occupiable complexes within four months. ATCO’s ability to design modular products to meet any requirements, combined with fully owned and operated manufacturing plants and locally staffed sales and operations branches across the US, positions ATCO uniquely to deliver high-quality, compliant, and timely modular solutions for any application or location.
More from Modular Advantage
Oregon’s Prevailing Wage Proposal: A Wake-Up Call for Modular Construction
Should House Bill 2688A become law, building projects would increase in price, face longer completion timelines, and produce significantly more waste. The bill also incentivizes contract awards to out of state businesses who would not reinvest their earnings into the local Oregon economy.
Behind the Design of Bethany Senior Terraces, NYC’s First Modular Passive House Senior Housing Project
As more developers seek to meet new regulations for energy efficiency, the team at Murray Engineering has set a new record. With the Bethany Senior Terraces project, Murray Engineering has helped to develop NYC’s first modular structure that fully encompasses passive house principles — introducing a new era of energy efficiency in the energy-conscious city that never sleeps.
How LAMOD is Using Modular to Address Inefficiency, Sustainability, and the Future of Construction
As developers, designers, and contractors seek to understand the evolving needs of the modular industry, no one is as well-versed in the benefits of going modular as Mārcis Kreičmanis. As the co-founder and CBDO of LAMOD in Riga, Latvia, Mārcis has made it his ultimate goal to address the inefficiencies of traditional construction.
From Furniture Builder to ‘Activist Architect’: Stuart Emmons’ Unique Journey
Stuart Emmons was fascinated by buildings at a young age. He remembers building sand cities with his brother during trips to the Jersey shore. His father gave him his first drawing table at the age of ten. Today, he is an experienced architect who received his FAIA in June 2025. The road he took is unique, to say the least.
Forge Craft Architecture + Design: Codes, Contracts, and Intellectual Property
Founding Principal and Director of Modular Practice for Forge Craft Architecture + Design, Rommel Sulit, discusses the implications of codes, contracts, and intellectual property on
modular construction.
Eisa Lee, the “Bilingual” Architect
Now as the founder of XL
Architecture and Modular Design in Ontario, Canada, she applies not just her education as a traditional architect but an entire holistic view on modular design. It’s this expansive view that guides her work on being a true partner that bridges the gap between architects and modular factories as they collaborate on the design process.
Tamarack Grove Engineering: Designing for the Modular Sector
The role of a structural engineer is crucial to the success of a modular project, from initial analysis to construction administration. Tamarack Grove offers structural engineering services — project analysis, plan creation, design creation, and construction administration — for commercial, manufacturing, facilities, public services, and modular. Modular is only one market sector the company serves but it is an increasingly popular one.
Engineer Masters the Art of Listening to His Customers
Since founding Modular Structural Consultants, LLC. in 2014, Yurianto has established a steady following of modular and container-based construction clients, primarily manufacturers. His services often include providing engineering calculations, reviewing drawings, and engineering certification
Inside College Road: Engineering the Modules of One of the World’s Tallest Modular Buildings
College Road is a groundbreaking modular residential development in East Croydon, South London by offsite developer and contractor, Tide, its modular company Vision Volumetric (VV), and engineered by MJH Structural Engineers.
Design for Flow: The Overlooked Power of DfMA in Modular Construction
Unlocking higher throughput, lower costs, and fewer redesigns by aligning Lean production flow with design for manufacturing and assembly.