UNB OCRC Student Off-Site Design Competition Crowns 2023 Winners
For the third year in a row, the University of New Brunswick’s Off-Site Construction Research Centre (OCRC), a research group dedicated to optimizing alternate solutions to on-site construction, presented its Off-site Construction Student Design Competition. This competition—presented again by the Modular Building Institute (MBI)—showcased student design innovation in modular, prefabricated, panelized, and other types of off-site construction and featured entries from dozens of interdisciplinary collegiate teams across Canada.
The objective of the competition was simple: to introduce students to offsite construction and to encourage interdisciplinary collaboration. It was also an opportunity to showcase how offsite construction’s many benefits, including reduced construction timelines, improved safety, and improved construction quality, can benefit the construction industry.
The Challenge
For this most recent competition, teams were tasked with developing a modular design for a housing unit that will be ‘open source’ and be used by manufacturers to meet the demand for affordable housing in New Brunswick. The design needed to focus on a repeatable volumetric module that could be used to combat the “missing middle housing” problem.
The Winners
First Place: Transition
Team members: Kateryna Stokoz, Luke De Bartolo, Stefan Giro (Toronto Metropolitan University)
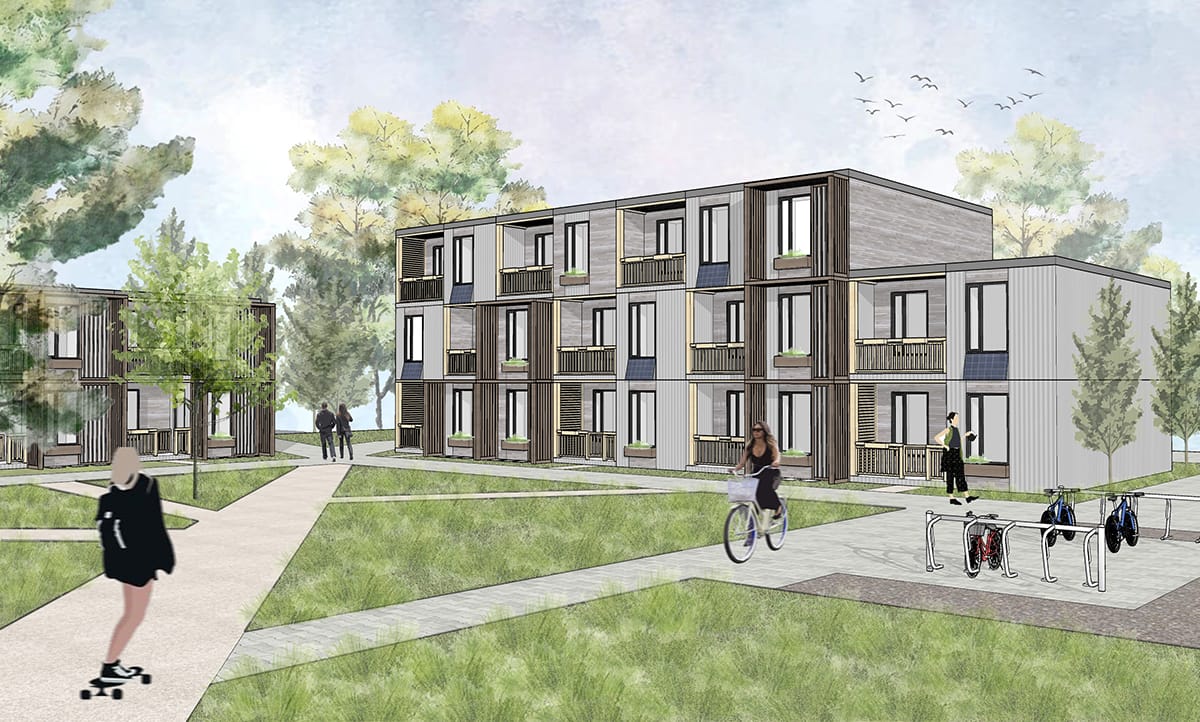
The first-place prize in 2023 went to Transition, a project from a three-student team from Toronto Metropolitan University. The team’s idea aims to revolutionize the concept of transitional housing for youth leaving the child welfare system. It goes beyond traditional social housing models, offering young individuals a nurturing space to grow and thrive.
“Our approach started with a thorough understanding of New Brunswick's specific needs for affordable housing – aiming for a tailored solution that also aligned with the principles of open-source development,” said team member Kateryna Stokoz. “When we learned about young adults' struggles leaving the child welfare system, it became clear that our focus should be on designing affordable housing specifically for this demographic.”
“We approached the design process in two parts: the individual units and the building complex,” continued team member Luke De Bartolo. “From the beginning, our vision for the building complex revolved around fostering a diverse community where different groups could coexist and mutually benefit from each other. We're talking about families next to older folks, doctors living near patients, and teachers among their students. Imagine a young adult who grew up in the foster system living among successful adults in this modular community. It's a setup where they can feel more included and have role models to look up to. For us, it was about creating a community where everyone benefits.”
“Participating in this competition was a great learning experience for our team,” said team member Stefan Giro. “It helped us gain a deeper understanding of modular housing. While developing our design, we discovered various logistical challenges and opportunities for creative problem-solving, from the initial stages to the on-site construction of modules.
“One significant lesson we've taken away is the crucial role of off-site modular construction in addressing housing shortages,” concluded Giro. “Our focus on New Brunswick highlighted the potential for adaptability of modular housing to be used in other areas facing housing needs more efficiently than traditional construction methods.”
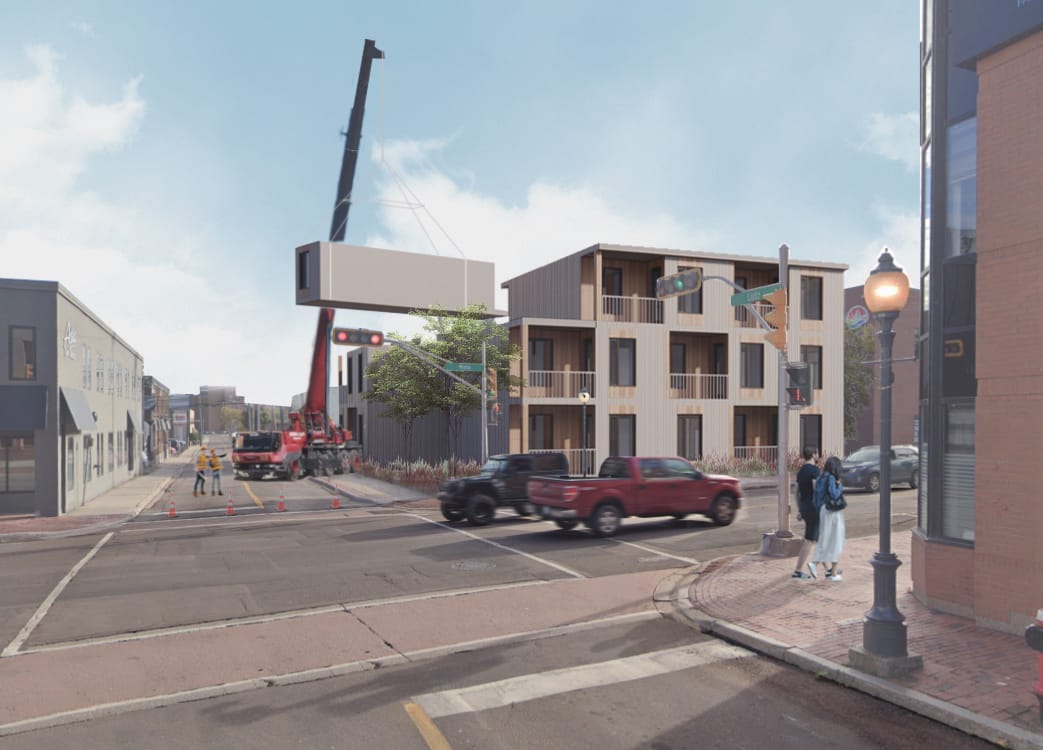
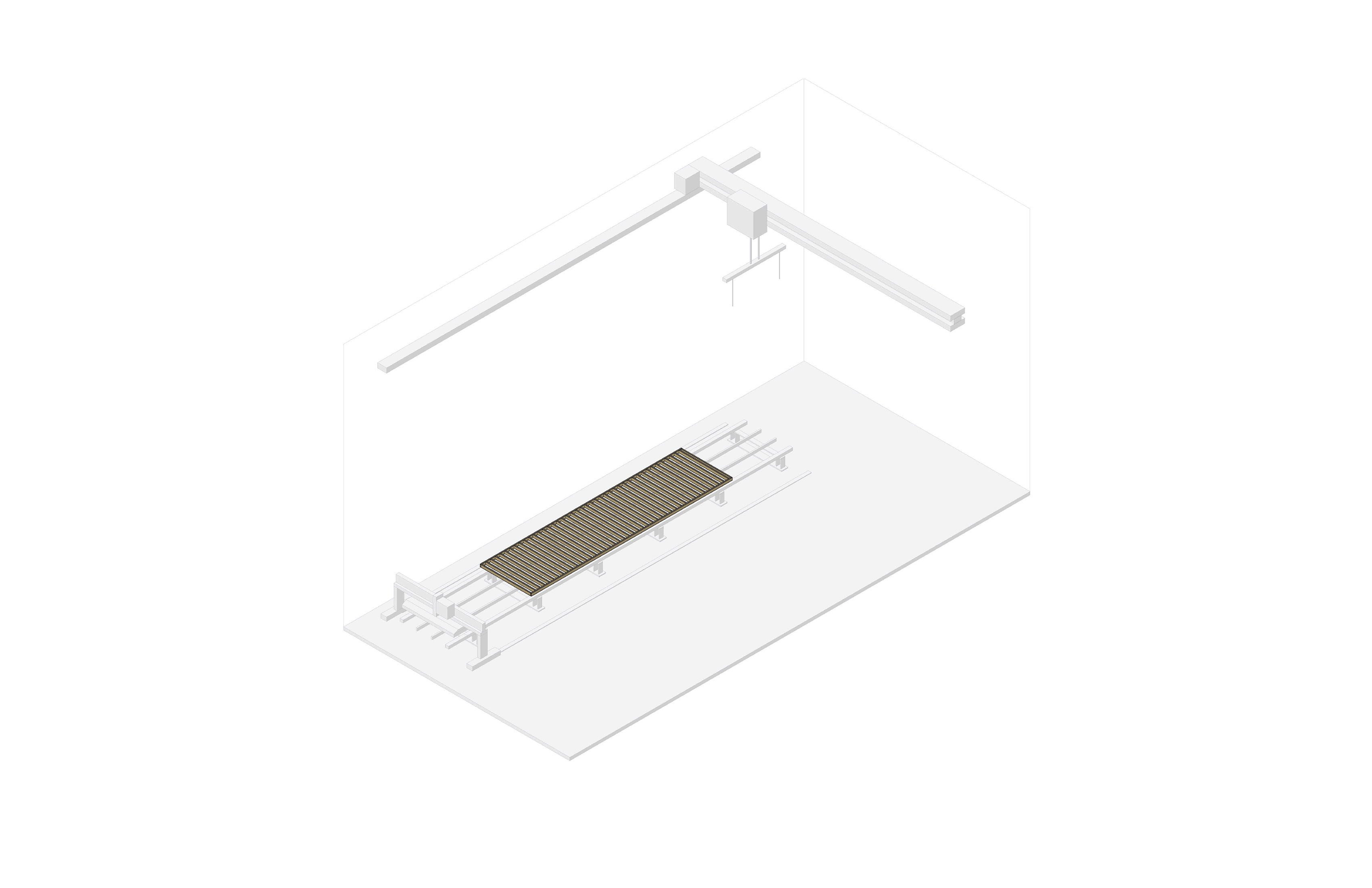
Second Place: Simplex
Team members: Til Schmitt-Ulms, Aryan Star, Gashtiyar Fathullah (University of New Brunswick)

With perhaps the most professional experience of the participating teams, this three-student group brought diverse experiences to the table. Gashtiyar Fathullah and Aryan Star, both recent graduates of the University of New Brunswick and now involved in Kent Homes, have direct experience in modular construction and automation. Til Schmitt-Ulms, a civil engineering student at University of British Colombia, contributed a fresh academic perspective and hands-on experience from Stack Modular.
“The focus for this project,” said team member Til Schmitt-Ulms, “was on reducing transportation costs and enabling modular manufacturers to access a larger market by developing standardized modules (wet modules with MEPs and normal modules) with shipping container sizes so that they can be transported by trucks, trains, and ships.”
“We believe affordability comes by creating more units on a smaller piece of land rather than independent unit on each plot of land,” continued team member Aryan Star. “We tried to design a multiplex with 12 apartments to show our beliefs, each apartment has one wet modules for kitchen and bathroom with multiple bedrooms and in suit laundry with access to two private balconies acting as terrace on the roof of your neighbor downstairs.”
“I think the future of housing lies in modular construction,” concluded team member Gashiyar Fathullah, “especially in cold climates which makes business sense because of the lack of workers. I see a future where you can order your house on your mobile and it updates you on how it’s going, just like a car.”
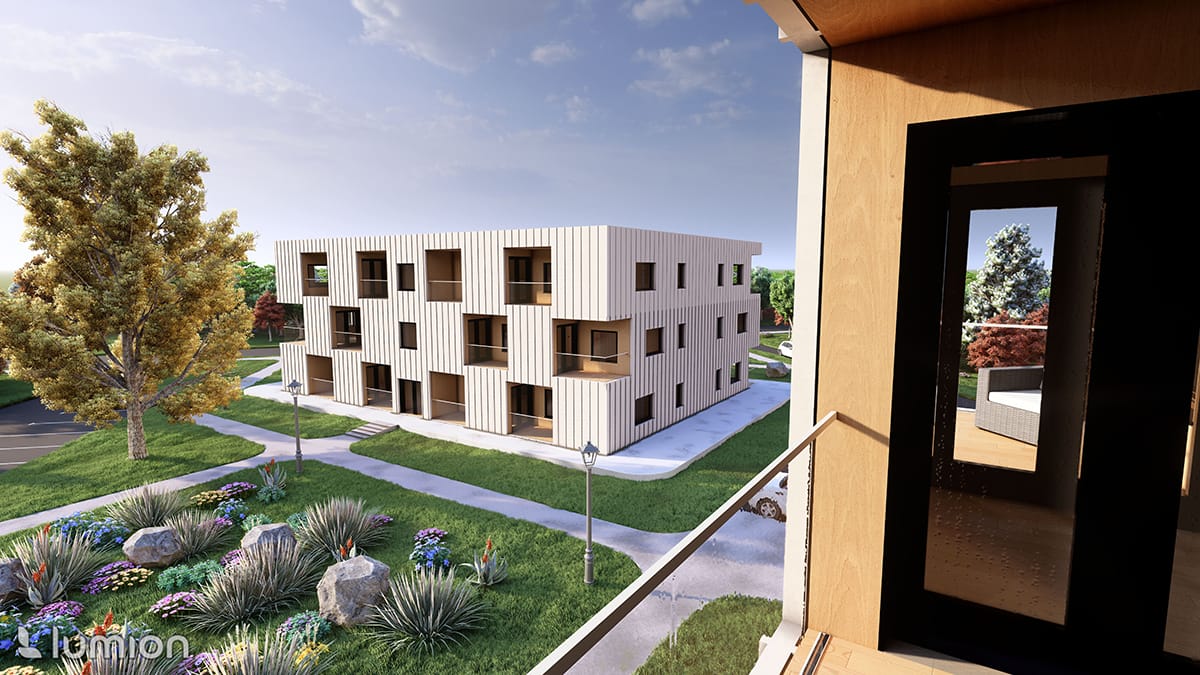
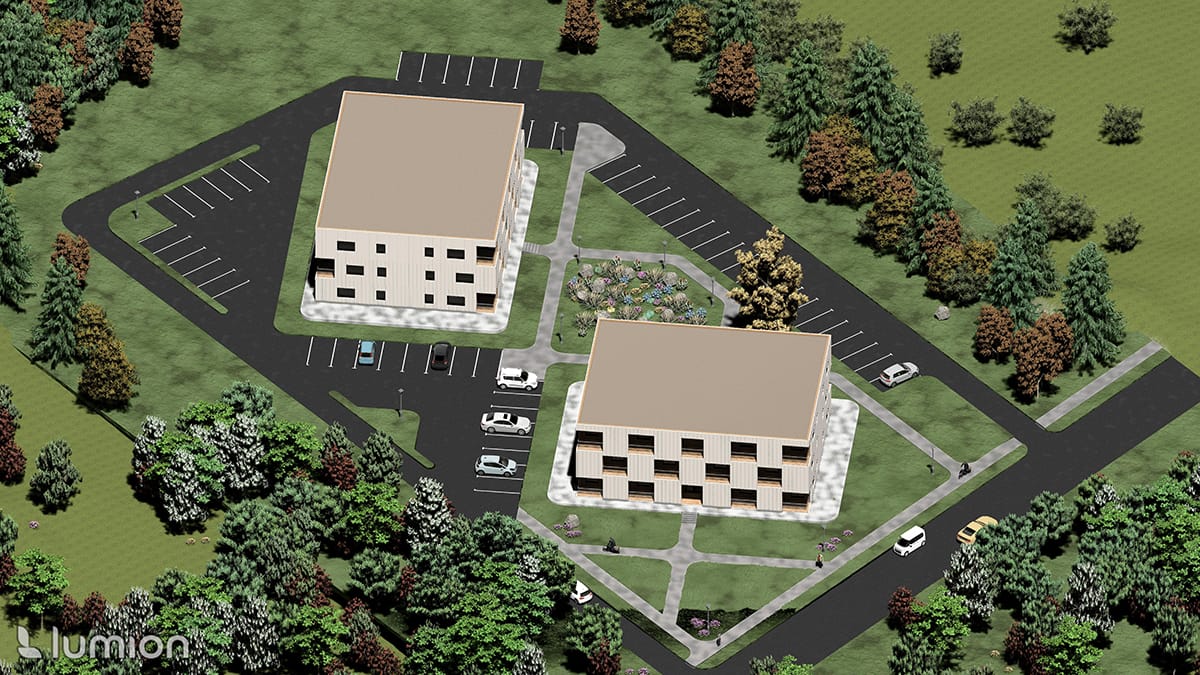
Presenting the Industry's Future
MBI is proud of its continued sponsorship of the University of New Brunswick's Off-Site Construction Research Centre's annual Off-site Construction Student Design Competition. Besides the opportunity to share exciting new ideas about how to implement modular and offsite construction to address current needs, the contest is chance to showcase the industry's rapidly growing pool of young talent.
"We look forward to this contest every year," said John McMullen, PCM, marketing director at MBI. "It's great to work with UNB to showcase these projects, and we love the opportunity to support students and young professionals interested in modular construction. It's a huge win-win."
Congratulations again to all of 2023 Competition entrants!
About the Author: John McMullen, PCM, is the marketing director for the Modular Building Institute. You can reach him directly at mcmullen@modular.org or on LinkedIn.
More from Modular Advantage
Oregon’s Prevailing Wage Proposal: A Wake-Up Call for Modular Construction
In early February, 2024, the Massachusetts Board of Building Regulations and Standards (BBRS) released its proposed 10th Edition building codes. This draft included several amendments targeting modular construction that would have created an extremely difficult environment for the entire modular industry and could have eliminated the industry entirely in the state.
Behind the Design of Bethany Senior Terraces, NYC’s First Modular Passive House Senior Housing Project
As more developers seek to meet new regulations for energy efficiency, the team at Murray Engineering has set a new record. With the Bethany Senior Terraces project, Murray Engineering has helped to develop NYC’s first modular structure that fully encompasses passive house principles — introducing a new era of energy efficiency in the energy-conscious city that never sleeps.
How LAMOD is Using Modular to Address Inefficiency, Sustainability, and the Future of Construction
As developers, designers, and contractors seek to understand the evolving needs of the modular industry, no one is as well-versed in the benefits of going modular as Mārcis Kreičmanis. As the co-founder and CBDO of LAMOD in Riga, Latvia, Mārcis has made it his ultimate goal to address the inefficiencies of traditional construction.
From Furniture Builder to ‘Activist Architect’: Stuart Emmons’ Unique Journey
Stuart Emmons was fascinated by buildings at a young age. He remembers building sand cities with his brother during trips to the Jersey shore. His father gave him his first drawing table at the age of ten. Today, he is an experienced architect who received his FAIA in June 2025. The road he took is unique, to say the least.
Forge Craft Architecture + Design: Codes, Contracts, and Intellectual Property
Founding Principal and Director of Modular Practice for Forge Craft Architecture + Design, Rommel Sulit, discusses the implications of codes, contracts, and intellectual property on
modular construction.
Eisa Lee, the “Bilingual” Architect
Now as the founder of XL
Architecture and Modular Design in Ontario, Canada, she applies not just her education as a traditional architect but an entire holistic view on modular design. It’s this expansive view that guides her work on being a true partner that bridges the gap between architects and modular factories as they collaborate on the design process.
Tamarack Grove Engineering: Designing for the Modular Sector
The role of a structural engineer is crucial to the success of a modular project, from initial analysis to construction administration. Tamarack Grove offers structural engineering services — project analysis, plan creation, design creation, and construction administration — for commercial, manufacturing, facilities, public services, and modular. Modular is only one market sector the company serves but it is an increasingly popular one.
Engineer Masters the Art of Listening to His Customers
Since founding Modular Structural Consultants, LLC. in 2014, Yurianto has established a steady following of modular and container-based construction clients, primarily manufacturers. His services often include providing engineering calculations, reviewing drawings, and engineering certification
Inside College Road: Engineering the Modules of One of the World’s Tallest Modular Buildings
College Road is a groundbreaking modular residential development in East Croydon, South London by offsite developer and contractor, Tide, its modular company Vision Volumetric (VV), and engineered by MJH Structural Engineers.
Design for Flow: The Overlooked Power of DfMA in Modular Construction
Unlocking higher throughput, lower costs, and fewer redesigns by aligning Lean production flow with design for manufacturing and assembly.