Newest Line of Container Buildings Broadens Modular’s Reach
Wilmot Modular’s newest line of mobile storage and office buildings is set to expand the reach of modular buildings into remote locations. Their Smart Line – Hybrid Series of container offices and storage buildings provides almost instant connectivity and power in locations that are off-grid, on-grid, or anywhere in between. With a robust solar power generation and storage system, they can be placed nearly anywhere there is access to sunlight and can provide enough power to remain self-sufficient.
Wilmot partnered with Prospect Solar, bringing their modular expertise and combining it with the latest in solar power generation and storage technologies to create a new line of solar powered container offices and storage buildings. Early interactions between the two revealed a strong alignment between their core values, paving the way for a fruitful collaboration.
The Smart Line models come in two sizes: 20 feet and 40 feet. The 20-foot model comes with 13 solar panels that generate 410 watts each, for a total of approximately 5.33 kW. It comes with an 18.4 kWh lithium phosphate battery. The 40-foot model comes with 25
panels at 410 watts each, for a total of approximately 10.25 kW. Depending on how many batteries are installed, it can store 36.8 to
73.6 kWh. Excess power generated by the solar arrays can be used to recharge the batteries, supply power to other modular units, or
potentially can be fed back into the grid, subject to local regulations and grid capabilities.
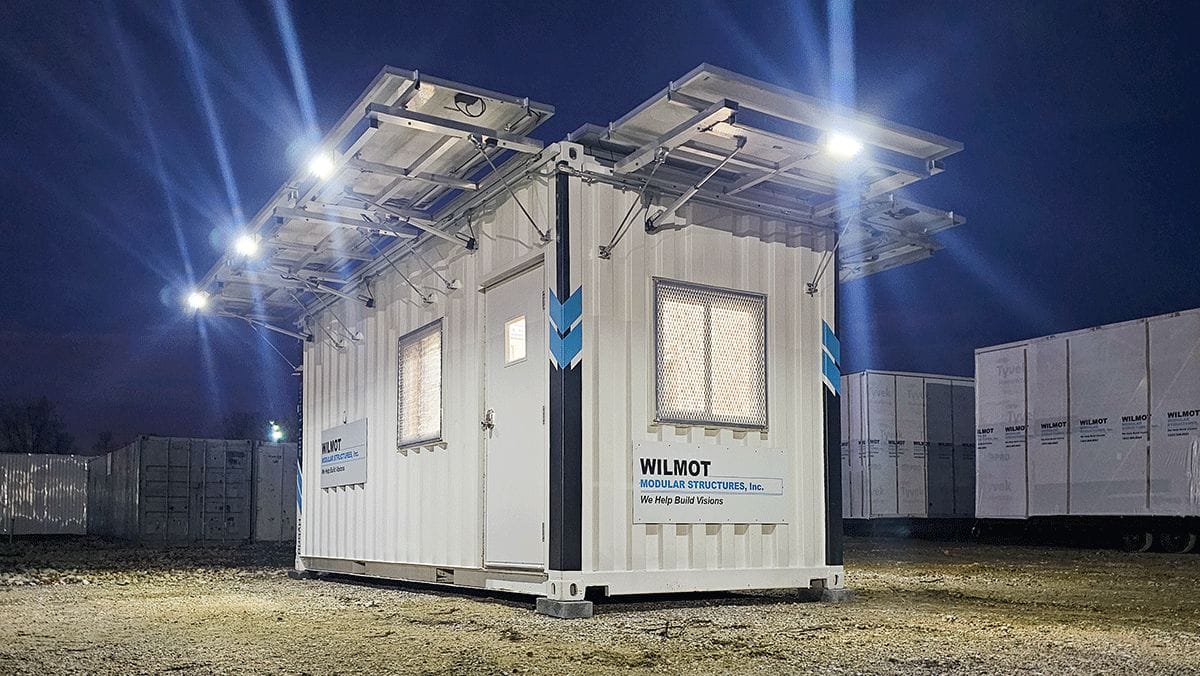
The basis for the Smart Line design was driven by Wilmot’s commitment to environmental responsibility and their ambition to provide innovative solutions within the industry. They began by recognizing the need for efficient, sustainable, and rapidly deployable solar powered office and storage solutions, especially in remote locations. Through the design process, they were able to successfully integrate solar power into shipping containers, and created a product that can be operational within minutes of being deployed. This feature can be particularly valuable in remote areas, where setting up grid connections can be time-consuming, often taking weeks or months.
Shipping containers were chosen as the foundational structures for these specialty units because of their structural integrity, modularity, sustainability, and cost effectiveness. The initial Smart Line – Hybrid Series (version 1) effectively powered the HVAC and lighting systems, but it faced certain operational challenges. Specifically, the side panels or “wings” – essential for increasing solar panel area – had to be retracted in winds exceeding 35 mph, and they were deployed manually, which was cumbersome.
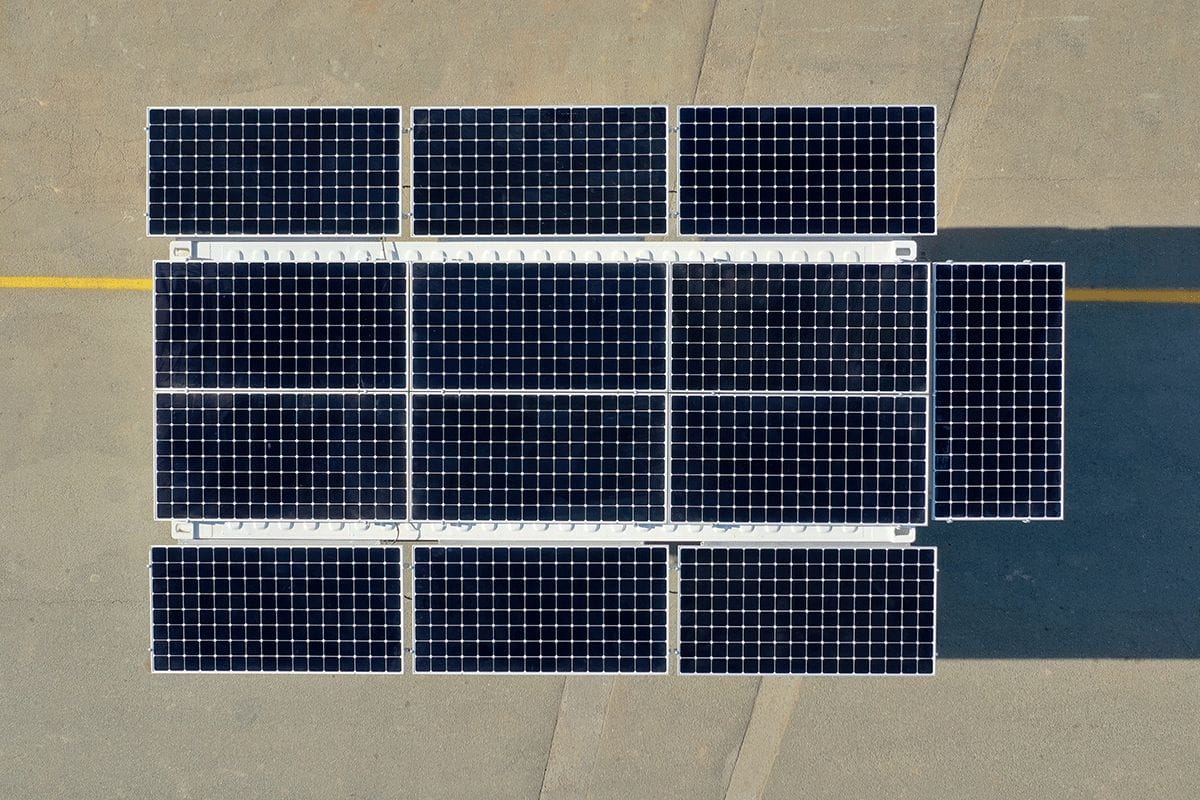
In response, version 2 was developed with significant design enhancements. The improved wing design now withstands higher wind conditions, up to 115 mph, without the need for retraction. Additionally, an automated electronic system for wing deployment was developed. This innovation simplifies the deployment process, minimizes labor efforts, and enhances safety. Overall, these developments have substantially boosted the operational efficiency and strength of the units.
There are several advantages to using Smart Line units. They offer substantial energy generation capabilities, enough to power key functions (HVAC and lighting), especially in the larger 40’ unit with its increased panel count and battery capacity. By significantly reducing or even eliminating reliance on external power sources, customers can also achieve notable savings in energy costs. Additionally, the units offer multiple power options, including solar, battery, optional generator, and a grid power inlet. This versatility and flexibility help ensure consistent power even in remote or unstable grid situations. The units can help customers meet their environmental and sustainability targets through qualification for incentives or tax credits. (Wilmot will be pursuing LEED certification for the units in the near future.) Finally, investing in solar-powered units now can be offset by long-term energy savings and potential financial incentives.
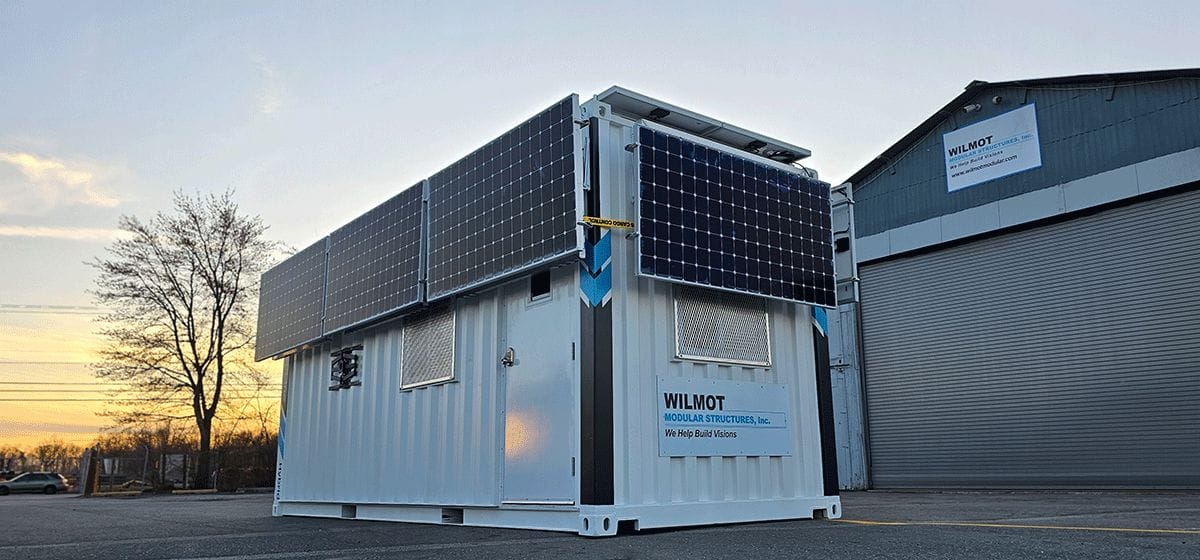
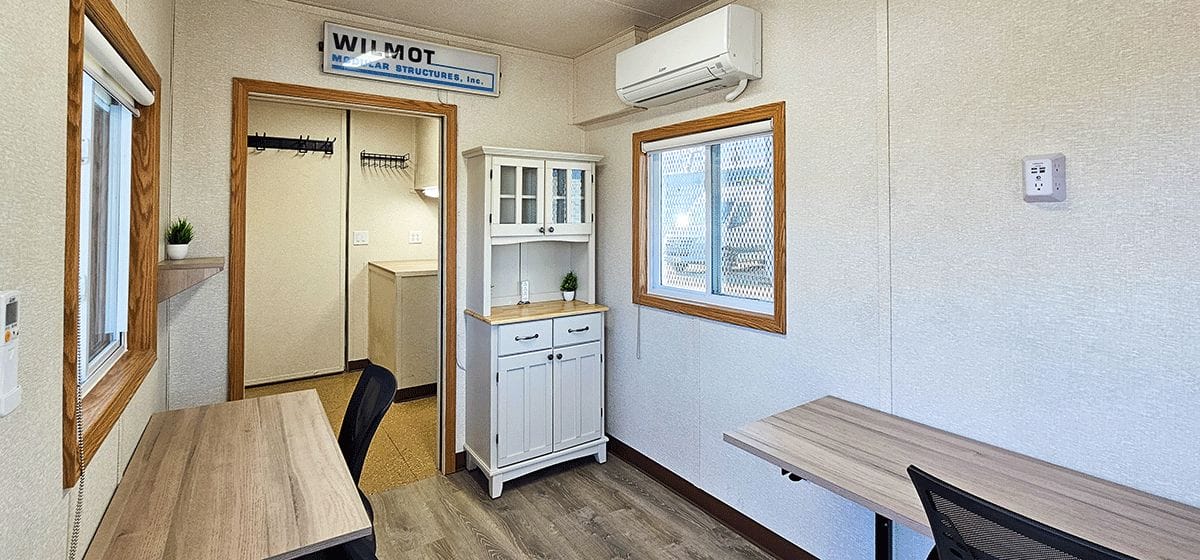
Wilmot is a long-standing family-run business that has always lead by being at the forefront of modular and container buildings technology. Chris Wilmot, Marketing Director, and Kevin Wilmot, Sales Director, have both learned the business from the ground up, starting by working in the field. They’ve watched the steady growth of the company started by their parents, Mike and Kathy Wilmot. Chris began his career after high school when he worked in fleet maintenance. He worked his way up to Manager while earning his marketing degree. He was promoted to Marketing Director in 2022. Kevin also started his career in fleet maintenance after high school. He then moved to field installations, until transferring to sales about ten years ago.
Both say they have learned a lot experiencing the industry from the ground up. Backed by decades of watching the ebb and flow of the industry, they are poised to continue innovating to keep their market edge. Chris said, “Witnessing the growth of our family business from a simple trailer to a major regional player has been a journey of inspiration, rooted in our parents’ dedication and hard work.” “We’ve both seen what happens when the economy has a downturn and fleet units start flooding back into the yard,” said Kevin. “We’ve also seen the good times when we run out of fleet because of high demand. Our parents have allowed us to grow in the business and have always explained the reason for different decisions so we can understand how to run a business. Our shared legacy, founded on the solid groundwork laid by our parents, motivates us to continue pushing the boundaries in the modular construction industry.”
The company provides a range of modular options, from state-of-the-art modular buildings and versatile mobile offices to practical office containers and storage solutions, like plant mezzanines. Their goal is always to cater to the diverse needs of their customers with excellence and efficiency.
The primary objective of this new partnership with Prospect Solar is to revolutionize the perception and functionality of typical mobile offices and storage spaces. Together they are focused on offering solutions that are not only sustainable, but also convenient and cost effective. The line is targeted to those who prioritize sustainability and eco-friendliness without compromising efficiency and cost effectiveness. This includes businesses and individuals seeking practical, portable solutions that are both environmentally responsible and adaptable to a variety of uses.
Wilmot hopes to continue its innovation into 2024. They are looking forward to a suite of offerings that will not only emphasize customization but also set new industry standards in efficiency and eco-responsibility, solidifying their standing as leaders in the modular building industry.
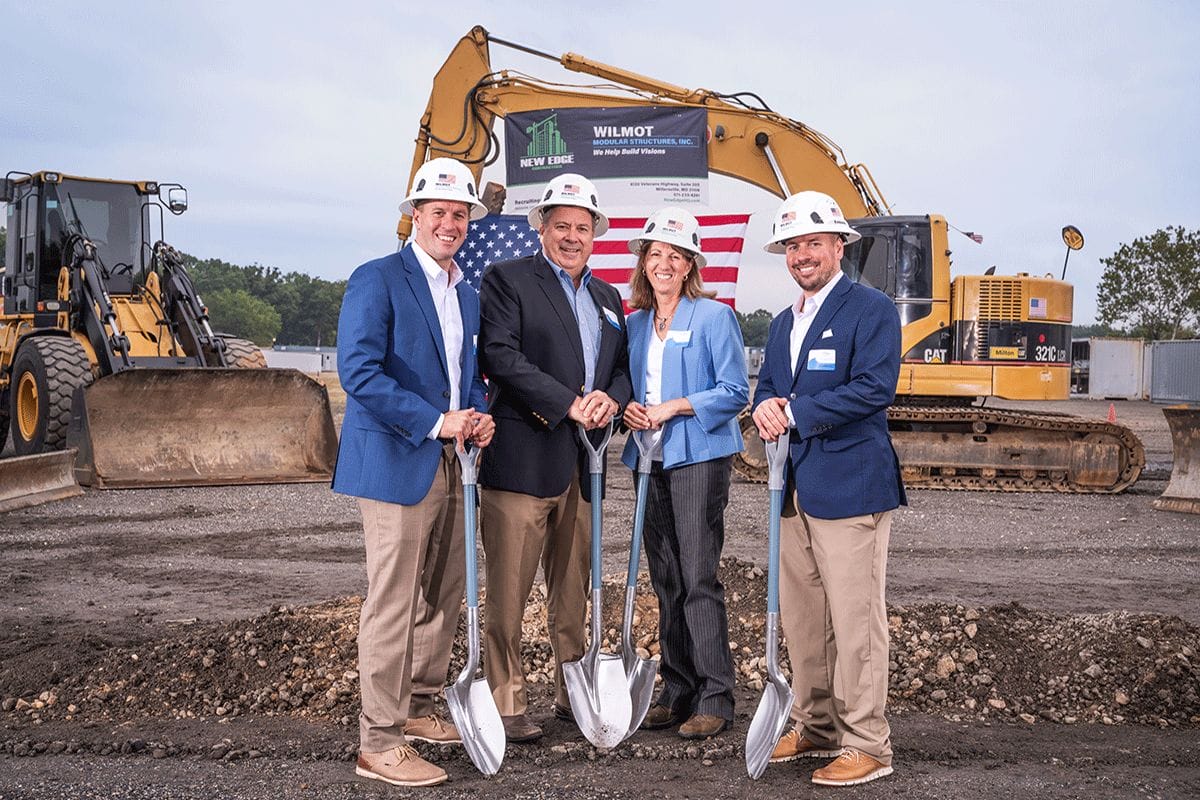
About the Author: Dawn Killough is a freelance construction writer with over 25 years of experience working with construction companies, subcontractors and general contractors. Her published work can be found at dkilloughwriter.com.
More from Modular Advantage
Oregon’s Prevailing Wage Proposal: A Wake-Up Call for Modular Construction
In early February, 2024, the Massachusetts Board of Building Regulations and Standards (BBRS) released its proposed 10th Edition building codes. This draft included several amendments targeting modular construction that would have created an extremely difficult environment for the entire modular industry and could have eliminated the industry entirely in the state.
Behind the Design of Bethany Senior Terraces, NYC’s First Modular Passive House Senior Housing Project
As more developers seek to meet new regulations for energy efficiency, the team at Murray Engineering has set a new record. With the Bethany Senior Terraces project, Murray Engineering has helped to develop NYC’s first modular structure that fully encompasses passive house principles — introducing a new era of energy efficiency in the energy-conscious city that never sleeps.
How LAMOD is Using Modular to Address Inefficiency, Sustainability, and the Future of Construction
As developers, designers, and contractors seek to understand the evolving needs of the modular industry, no one is as well-versed in the benefits of going modular as Mārcis Kreičmanis. As the co-founder and CBDO of LAMOD in Riga, Latvia, Mārcis has made it his ultimate goal to address the inefficiencies of traditional construction.
From Furniture Builder to ‘Activist Architect’: Stuart Emmons’ Unique Journey
Stuart Emmons was fascinated by buildings at a young age. He remembers building sand cities with his brother during trips to the Jersey shore. His father gave him his first drawing table at the age of ten. Today, he is an experienced architect who received his FAIA in June 2025. The road he took is unique, to say the least.
Forge Craft Architecture + Design: Codes, Contracts, and Intellectual Property
Founding Principal and Director of Modular Practice for Forge Craft Architecture + Design, Rommel Sulit, discusses the implications of codes, contracts, and intellectual property on
modular construction.
Eisa Lee, the “Bilingual” Architect
Now as the founder of XL
Architecture and Modular Design in Ontario, Canada, she applies not just her education as a traditional architect but an entire holistic view on modular design. It’s this expansive view that guides her work on being a true partner that bridges the gap between architects and modular factories as they collaborate on the design process.
Tamarack Grove Engineering: Designing for the Modular Sector
The role of a structural engineer is crucial to the success of a modular project, from initial analysis to construction administration. Tamarack Grove offers structural engineering services — project analysis, plan creation, design creation, and construction administration — for commercial, manufacturing, facilities, public services, and modular. Modular is only one market sector the company serves but it is an increasingly popular one.
Engineer Masters the Art of Listening to His Customers
Since founding Modular Structural Consultants, LLC. in 2014, Yurianto has established a steady following of modular and container-based construction clients, primarily manufacturers. His services often include providing engineering calculations, reviewing drawings, and engineering certification
Inside College Road: Engineering the Modules of One of the World’s Tallest Modular Buildings
College Road is a groundbreaking modular residential development in East Croydon, South London by offsite developer and contractor, Tide, its modular company Vision Volumetric (VV), and engineered by MJH Structural Engineers.
Design for Flow: The Overlooked Power of DfMA in Modular Construction
Unlocking higher throughput, lower costs, and fewer redesigns by aligning Lean production flow with design for manufacturing and assembly.