By the Numbers
Assessing MBI Member Training, Professional Development & Workforce Needs
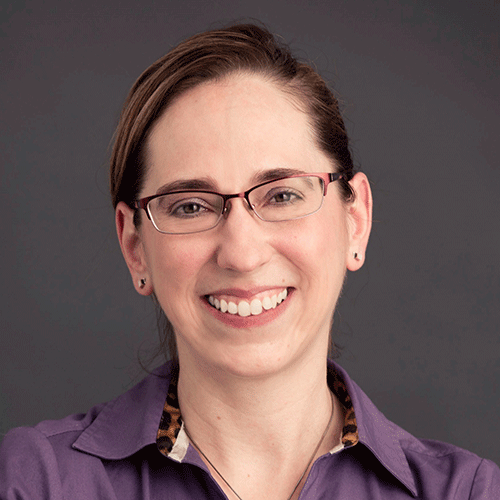
Heather Packard is the Workforce & Professional Development Director for the Modular Building Institute
As part of MBI’s continuing efforts to expand the footprint of the commercial modular construction industry, we launched an intelligence gathering process in mid-September 2023 to collect information on member companies’ challenges and needs with respect to training, professional development, and workforce. The purpose of this process was to identify critical needs to support development of a near- and long-term strategy to address these needs.
Intelligence Gathering Process
The intelligence gathering process included two phases: a qualitative phase consisting of one-on-one conversations with representative member companies and a quantitative phase consisting of a survey instrument distributed to all MBI contacts.
To ensure a representative set of data for the first, qualitative, phase, conversations were held across member company types including manufacturers (5 direct and 3 wholesale), dealers/fleet owners (3), owners/developers (2), contractors/builders (3), design professionals (3), suppliers of services (1), and suppliers of materials (2).
This phase probed challenges member companies are experiencing at an industry-wide, company-specific, and partner-specific level as well as ideas on how MBI could support attracting new entrants to our industry along with training and professional development opportunities for staff.
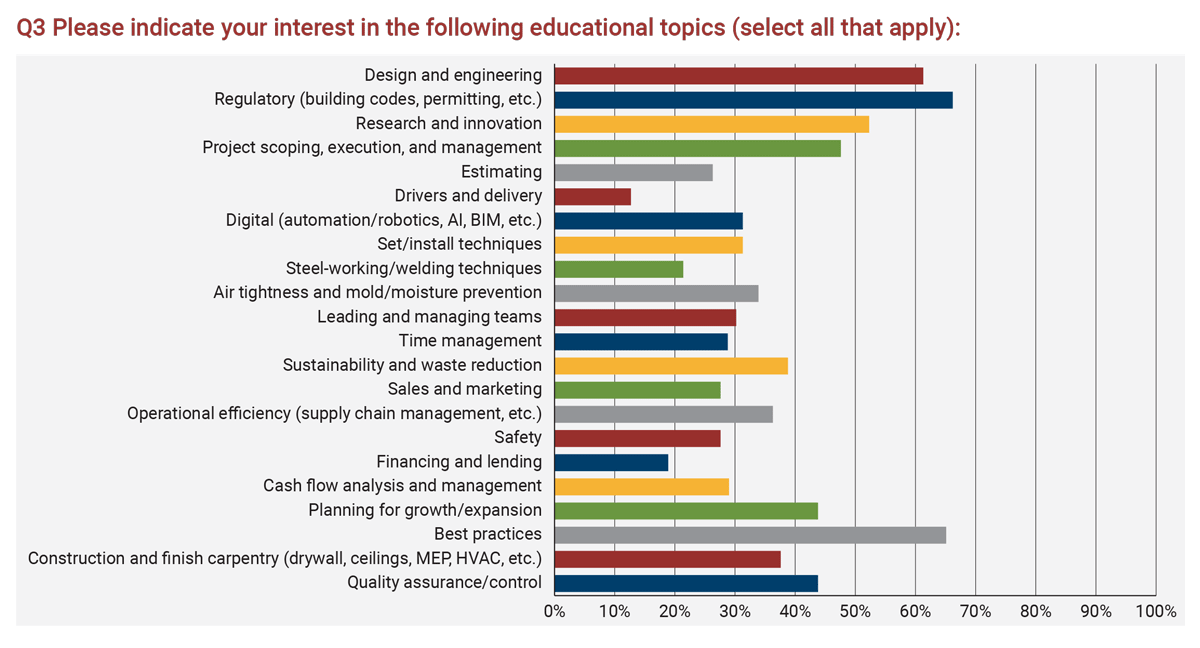
Visualized results from one question of MBI's Workforce and Professional Development survey from September 2023.
Qualitative Outcomes
Challenges at an industry-wide level uncovered during the qualitative phase included labor – limited supply of skilled tradespeople as well as experienced architects, engineers, and project managers – along with a lack of stakeholder awareness of modular capabilities, including clients, architects, and financial institutions.
Company-specific challenges also included labor – difficulties in attracting tradespeople, backfilling at mid and senior levels, and small talent pools for design, drafting, estimating, and purchasing – along with market supply and demand and finding new areas of growth.
Partner-specific challenges uncovered insufficient production capacity at the manufacturer level and a need for increased awareness and education amongst stakeholders including developers, lenders, building inspectors, general contractors, and clients.
Training and professional development ideas discussed included opportunities to leverage Introduction to Commercial Modular Construction for employee on-boarding and developing training for commercial modular set and install staff, sales staff, project management staff, and market-facing individuals. The one-on-one conversations also uncovered a need for building code-based training and refreshers for MBI member companies, government officials, and financial institutions.
Ideas for attracting new entrants centered on increasing youth awareness of the commercial modular construction industry’s opportunities and advantages over traditional construction. These discussions included potential outreach and engagement opportunities directed towards high-school level groups promoting trades and with vocational technology centers in an effort towards increasing the future talent pipeline for labor and trades. Outreach and engagement with universities offering a construction-related degree was another hallmark of these conversations, with a goal towards increasing university program curriculum focus on modular in the hope that this could lead to better-trained and more well-rounded future designers, architects, engineers, and project managers.
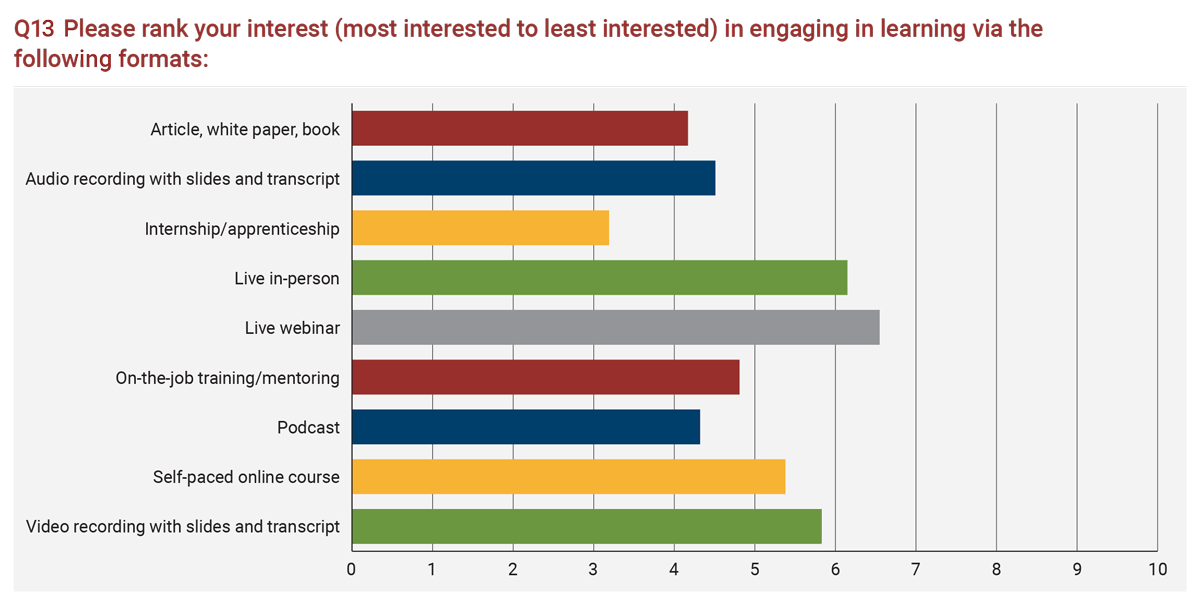
Quantitative Phase
We used a survey instrument for the second, quantitative, phase, which was distributed to all MBI contacts. To date, we have received responses from 68 unique organizations across all MBI membership categories and affiliations, a roughly 12% response rate. The survey instrument addressed the following topics:
- Estimated workforce needs over the next 1-3 years
- Most difficult roles to fill within the past 1-2 years
- Longest time it has taken to fill vacant roles
- Most useful recruiting methods
- Educational topics of interest
- Learning format preferences
Quantitative Outcomes: Estimated Workforce Needs
Current responses to estimated workforce needs across administrative and office professional staff demonstrate a near-term (next 1-3 years) need for the following roles:
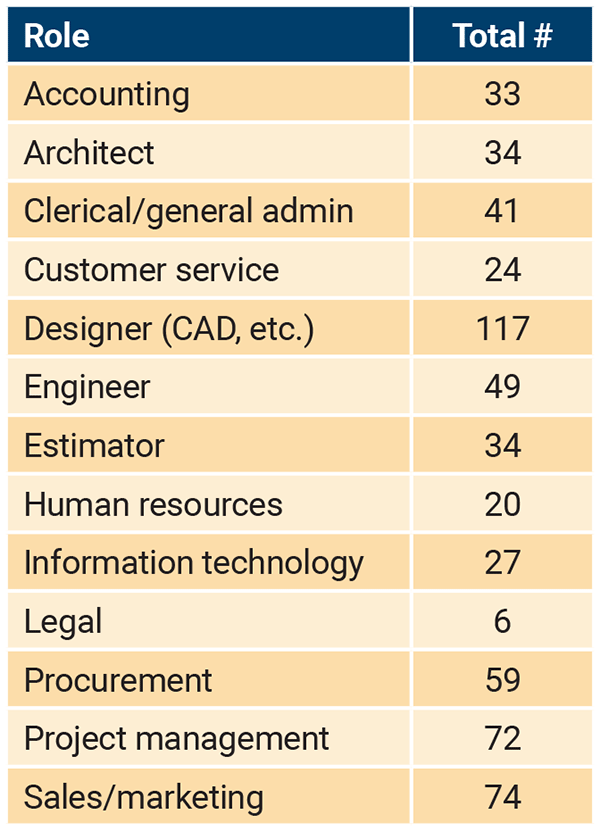
Current responses to estimated workforce needs across labor, trades, and delivery staff demonstrate a near-term (next 1-3 years) need for the following roles:
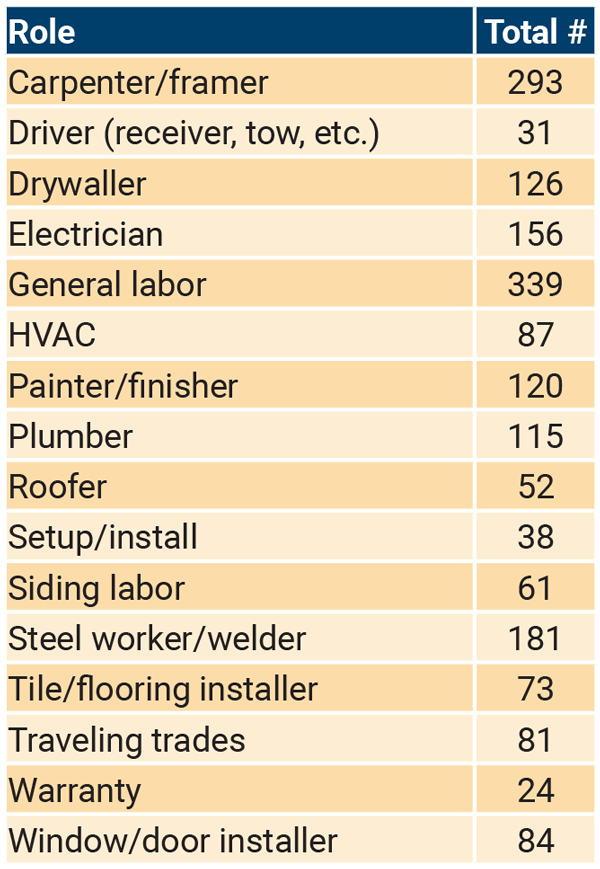
Current responses to estimated workforce needs across safety, compliance, and quality assurance/control staff demonstrate a near-term (next 1-3 years) need for the following roles:
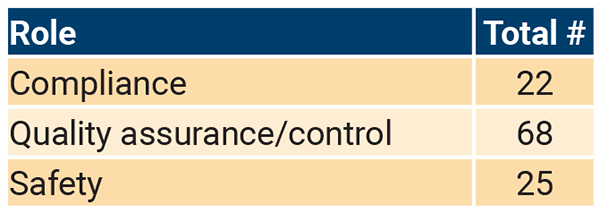
Quantitative Outcomes: Most Difficult Roles to Fill, Longest Time to Fill Vacant Roles, and Most Useful Recruiting Methods
The most difficult roles to fill within the last 1-2 years echoed the small talent pools uncovered in the first, qualitative, phase, and included tradespeople of all types, general and skilled labor, carpenters/framers, drywall finishers, experienced production and plant workers, architects, designers, engineers, and project managers – with experience in modular – as well as drafters, BIM experts/managers, sales professionals, customer service, and estimators.
Responses to the longest time to fill vacant roles further demonstrate the talent shortage our industry is experiencing. Roles for CAD operators and designers, electricians, plumbers, welders, and quality control staff were reported to take greater than 1 year to 2 years to fill.
Members reported word of mouth and referrals from current employees as the most useful recruiting method, followed closely by social media efforts and job boards (typically Indeed for labor and trades). The full list of recruiting methods, their current rankings, and responses to “other, please specify” is below.
Quantitative Outcomes: Topics of Interest and Learning Format Preferences
In terms of learning topics of interest, members reported an interest in regulatory topics including building codes and permitting, best practices in the industry, design and engineering, research and innovation, project scoping, execution and management, planning for growth and expansion, and quality assurance and control. The full list of learning topics of interest and their current rankings is below.
Lastly, members expressed a preference for live webinars, live in-person events, video recordings with slides and transcripts, and self-paced online courses. The full list of learning formats and their current rankings is below.
Make Your Voice Heard
The survey instrument will remain open so that we can continue to collect member needs and preferences and take these into account for further strategy development and execution. Please visit MBI's online survey and make your voice heard!
If you have any questions about the process or have other feedback or suggestions for MBI to consider, please contact Heather Packard, Professional & Workforce Development Director, at heather@modular.org.
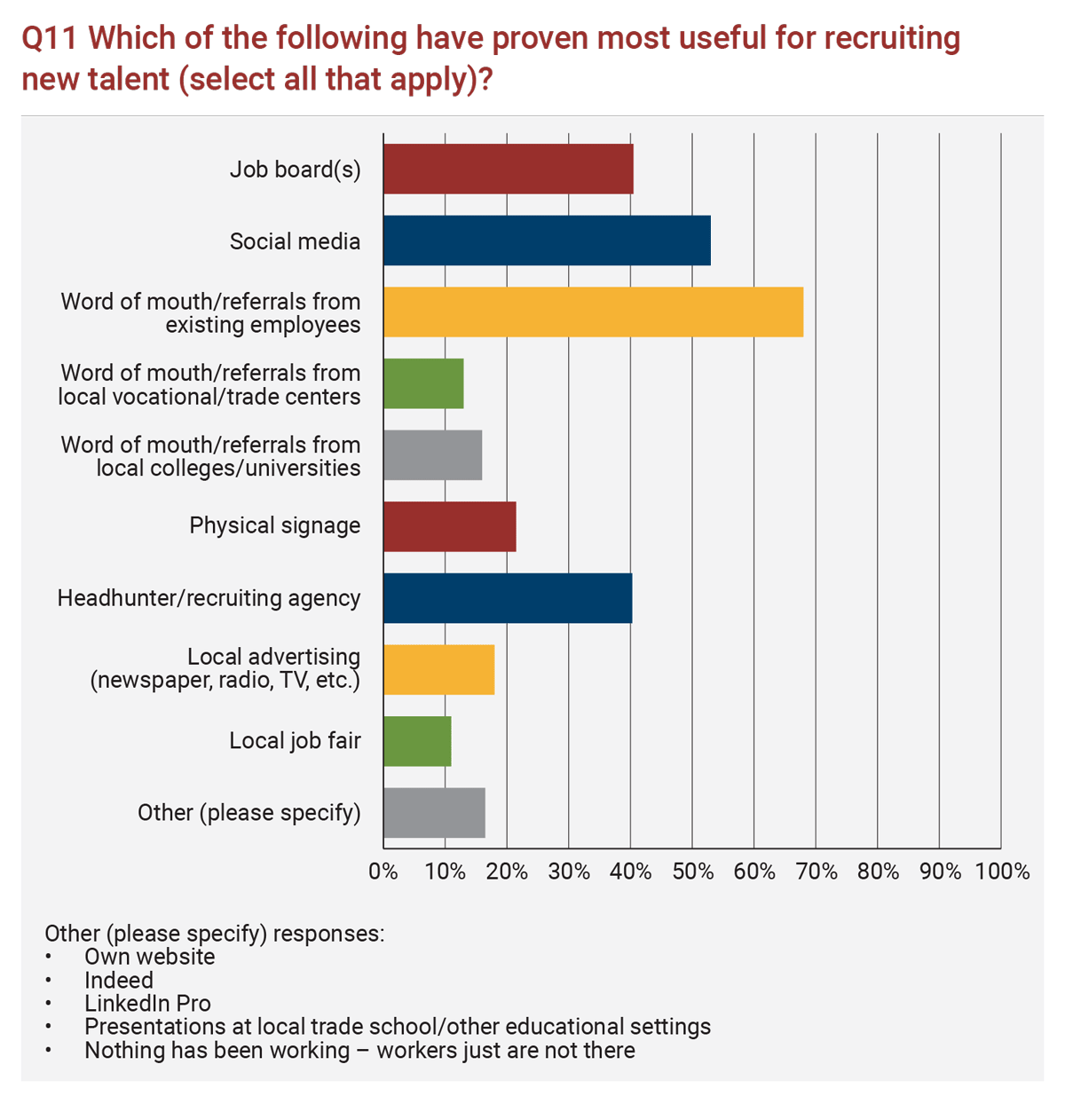
More from Modular Advantage
Oregon’s Prevailing Wage Proposal: A Wake-Up Call for Modular Construction
In early February, 2024, the Massachusetts Board of Building Regulations and Standards (BBRS) released its proposed 10th Edition building codes. This draft included several amendments targeting modular construction that would have created an extremely difficult environment for the entire modular industry and could have eliminated the industry entirely in the state.
Behind the Design of Bethany Senior Terraces, NYC’s First Modular Passive House Senior Housing Project
As more developers seek to meet new regulations for energy efficiency, the team at Murray Engineering has set a new record. With the Bethany Senior Terraces project, Murray Engineering has helped to develop NYC’s first modular structure that fully encompasses passive house principles — introducing a new era of energy efficiency in the energy-conscious city that never sleeps.
How LAMOD is Using Modular to Address Inefficiency, Sustainability, and the Future of Construction
As developers, designers, and contractors seek to understand the evolving needs of the modular industry, no one is as well-versed in the benefits of going modular as Mārcis Kreičmanis. As the co-founder and CBDO of LAMOD in Riga, Latvia, Mārcis has made it his ultimate goal to address the inefficiencies of traditional construction.
From Furniture Builder to ‘Activist Architect’: Stuart Emmons’ Unique Journey
Stuart Emmons was fascinated by buildings at a young age. He remembers building sand cities with his brother during trips to the Jersey shore. His father gave him his first drawing table at the age of ten. Today, he is an experienced architect who received his FAIA in June 2025. The road he took is unique, to say the least.
Forge Craft Architecture + Design: Codes, Contracts, and Intellectual Property
Founding Principal and Director of Modular Practice for Forge Craft Architecture + Design, Rommel Sulit, discusses the implications of codes, contracts, and intellectual property on
modular construction.
Eisa Lee, the “Bilingual” Architect
Now as the founder of XL
Architecture and Modular Design in Ontario, Canada, she applies not just her education as a traditional architect but an entire holistic view on modular design. It’s this expansive view that guides her work on being a true partner that bridges the gap between architects and modular factories as they collaborate on the design process.
Tamarack Grove Engineering: Designing for the Modular Sector
The role of a structural engineer is crucial to the success of a modular project, from initial analysis to construction administration. Tamarack Grove offers structural engineering services — project analysis, plan creation, design creation, and construction administration — for commercial, manufacturing, facilities, public services, and modular. Modular is only one market sector the company serves but it is an increasingly popular one.
Engineer Masters the Art of Listening to His Customers
Since founding Modular Structural Consultants, LLC. in 2014, Yurianto has established a steady following of modular and container-based construction clients, primarily manufacturers. His services often include providing engineering calculations, reviewing drawings, and engineering certification
Inside College Road: Engineering the Modules of One of the World’s Tallest Modular Buildings
College Road is a groundbreaking modular residential development in East Croydon, South London by offsite developer and contractor, Tide, its modular company Vision Volumetric (VV), and engineered by MJH Structural Engineers.
Design for Flow: The Overlooked Power of DfMA in Modular Construction
Unlocking higher throughput, lower costs, and fewer redesigns by aligning Lean production flow with design for manufacturing and assembly.