Collaboration — How to Do It Right
Collaboration in the Modular Construction Industry
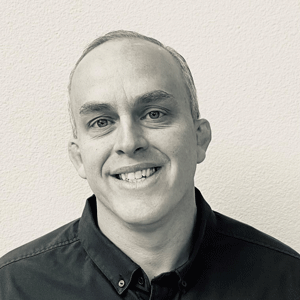
Landon Boucher is the Director of Business Design and Innovations at MiTek Inc.
So much is said in the world of construction regarding the need to collaborate, particularly in off-site construction. Anyone experienced with successful project execution will tell you that good collaboration amongst project team members, will yield quantitative results. Some in our industry have taken the time to dive deeper into exactly what that means and the impact it can have on a project. What seems to be missing often from these presentations and marketing campaigns is real, tangible direction on, “how” – how to collaborate. I have witnessed many project teams miss the intended results of a project due to a poorly guided, albeit well intended, attempt at collaboration. Usually, these failed projects start with a lot of enthusiasm from the team members to share respective knowledge and insights in their aim toward a successful outcome. The definition of success can vary depending on the expectations laid out by the customer, but regardless of how its defined, success can subtly slip away from the team without a clear understanding of “how.”
There are several high-quality tools and resources on the market that can aid a team in their collaborative efforts, including some from MiTek regarding structural building components. Still, no matter how great these tools are, if little is understood about how to extract all capabilities from these tools and maximize outputs, even if improved results are seen, the full potential is missed. One obvious solution is including someone on the team who has advanced level expertise in this area. Sometimes however, that just isn’t available. In those cases, a representative from the company that developed and maintains that tool, is a necessary member to add, even if it is someone only available remotely to troubleshoot as needed. Still, even more important than understanding how to take full advantage of the capabilities available within the many tools and resources our industry provides, is an understanding of how to apply the general principles of collaboration. More than just another industry buzzword, collaboration is a process that requires leadership to maintain its implementation through project completion.
So how can you establish good collaboration? First you must determine what sort of collaboration your project will benefit from most. The two main types are Open and Closed. Open collaboration involves utilizing people from inside and outside your organization to generate ideas or solve problems. This type of collaboration usually involves a large number of participants. A common use of this type of collaboration would be market research. Closed collaboration, however, involves using a relatively small group of specialists working toward a common goal. Closed collaboration is what you would typically see on a construction project team. A relatively small group of specialists, working toward a common goal, to design, make and build a high performing building that produces a financial net gain for the owner.
Once you’ve defined the type of collaboration you will need, you must select the right people and begin building your team. Take careful consideration of the value of the work they provide, not just the bid. A good structural engineer for instance can spend twice the amount of time to complete a project but in that time, remove 100’s of 1,000’s of dollars from your construction budget. What matters more? The cost to design a project or the cost to build it? Even though in a collaborative environment, you want to have equal participation amongst all members of the team, it is important to still assign leadership roles to ensure the project stays on track. This is particularly important in our industry where the options can often seem endless regarding design choices and construction methodologies.
Now that your team is selected, its time to define your purpose. We can’t be successful in our “how” without defining our “why”. Share your mission and vision for the project and have it written down as the header of all communications going forward. A shared mission will keep the team together and a shared vision will help them arrive at the right destination.
Lastly, once the mission and vision have been identified, you will need to deliver it with conviction to generate buy-in from all participants. If you believe it, make it known and make it owned! As the leader of the project, you will need to set the example, build trust, and show consistency if you are going to be successful in establishing a creative and supportive culture that is rooted in the principals of collaboration.
I’ll share one final thought about leadership. While this article is focused on collaboration, the success of collaboration relies on leadership. Everything rises and falls on leadership! There is an old paradox known as Buridan’s Donkey. It’s named after the author, Jean Buridan who was a 14th century philosopher and a student of Aristotle. Buridan’s Donkey is an illustration of a paradox in philosophy regarding the concept of free will or the power to make choices. It refers to a hypothetical situation wherein a donkey that is equally parts hungry and thirsty is placed exactly midway between its food source and its water source. The paradox assumes that the donkey will always default to whatever is closest (or easiest to access). Ultimately, it dies of both hunger and thirst since it cannot make a rational decision between the food or the water. Jean Buridan was a great humorist and would regularly use humor to illustrate his philosophical teachings. While humorous, this paradox of the donkey, holds a lot of wisdom. We have all experienced the famous “analysis paralysis” dilemma on project teams. I think the point Buridan is making here in this paradox, is choices must be made. Sometimes, the easy choice isn’t the best. Regardless, you have to take decisive action. You have to move. You have to lead.
So, don’t be a donkey! Make decisions and lead your team to success through collaboration.
If you are interested in collaborating with MiTek, contact me at Landon.Boucher@mii.com
More from Modular Advantage
Oregon’s Prevailing Wage Proposal: A Wake-Up Call for Modular Construction
In early February, 2024, the Massachusetts Board of Building Regulations and Standards (BBRS) released its proposed 10th Edition building codes. This draft included several amendments targeting modular construction that would have created an extremely difficult environment for the entire modular industry and could have eliminated the industry entirely in the state.
Behind the Design of Bethany Senior Terraces, NYC’s First Modular Passive House Senior Housing Project
As more developers seek to meet new regulations for energy efficiency, the team at Murray Engineering has set a new record. With the Bethany Senior Terraces project, Murray Engineering has helped to develop NYC’s first modular structure that fully encompasses passive house principles — introducing a new era of energy efficiency in the energy-conscious city that never sleeps.
How LAMOD is Using Modular to Address Inefficiency, Sustainability, and the Future of Construction
As developers, designers, and contractors seek to understand the evolving needs of the modular industry, no one is as well-versed in the benefits of going modular as Mārcis Kreičmanis. As the co-founder and CBDO of LAMOD in Riga, Latvia, Mārcis has made it his ultimate goal to address the inefficiencies of traditional construction.
From Furniture Builder to ‘Activist Architect’: Stuart Emmons’ Unique Journey
Stuart Emmons was fascinated by buildings at a young age. He remembers building sand cities with his brother during trips to the Jersey shore. His father gave him his first drawing table at the age of ten. Today, he is an experienced architect who received his FAIA in June 2025. The road he took is unique, to say the least.
Forge Craft Architecture + Design: Codes, Contracts, and Intellectual Property
Founding Principal and Director of Modular Practice for Forge Craft Architecture + Design, Rommel Sulit, discusses the implications of codes, contracts, and intellectual property on
modular construction.
Eisa Lee, the “Bilingual” Architect
Now as the founder of XL
Architecture and Modular Design in Ontario, Canada, she applies not just her education as a traditional architect but an entire holistic view on modular design. It’s this expansive view that guides her work on being a true partner that bridges the gap between architects and modular factories as they collaborate on the design process.
Tamarack Grove Engineering: Designing for the Modular Sector
The role of a structural engineer is crucial to the success of a modular project, from initial analysis to construction administration. Tamarack Grove offers structural engineering services — project analysis, plan creation, design creation, and construction administration — for commercial, manufacturing, facilities, public services, and modular. Modular is only one market sector the company serves but it is an increasingly popular one.
Engineer Masters the Art of Listening to His Customers
Since founding Modular Structural Consultants, LLC. in 2014, Yurianto has established a steady following of modular and container-based construction clients, primarily manufacturers. His services often include providing engineering calculations, reviewing drawings, and engineering certification
Inside College Road: Engineering the Modules of One of the World’s Tallest Modular Buildings
College Road is a groundbreaking modular residential development in East Croydon, South London by offsite developer and contractor, Tide, its modular company Vision Volumetric (VV), and engineered by MJH Structural Engineers.
Design for Flow: The Overlooked Power of DfMA in Modular Construction
Unlocking higher throughput, lower costs, and fewer redesigns by aligning Lean production flow with design for manufacturing and assembly.