BECC Modular: Manufacturing for Future Generations Through Industrialization and Improvement
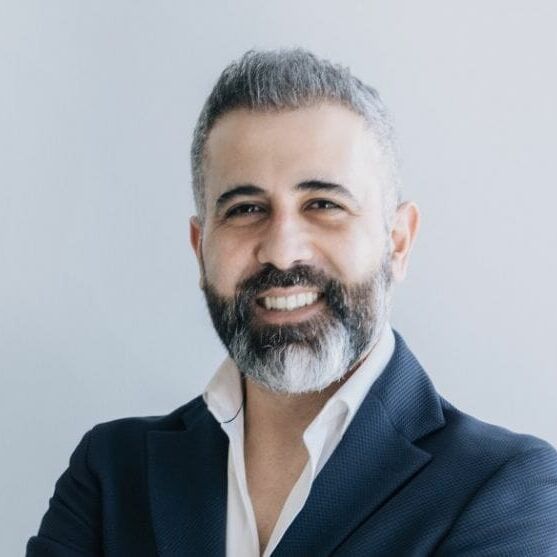
Ali Ozden is the CEO of BECC Modular
The Toronto-based modular manufacturer BECC Modular has made a name for itself by championing sustainable structures that are not only efficient, but resilient, and future-proof. CEO Ali Ozden’s background as a carpenter only helps solidify the company’s stance. The company aims for constant improvements via build time, developing an industrialized “library” of parts, and cost, but also in creating structures that can withstand the changing times. It’s a lofty goal—and something that you might think is more for a sci-fi novel—but it’s all for his children, he says.
“I was talking with my wife one day, and I just asked her, ‘what would be our legacy for our kids?’” said Ali. “What would be something they can talk about and they could be proud of us?” His personal legacy complements BECC Modular’s ethos and dedication to building everything right from the bottom up. So how did this carpenter end up dedicating a business to sustainable building and manufacturing efficient, future-proofed structures?
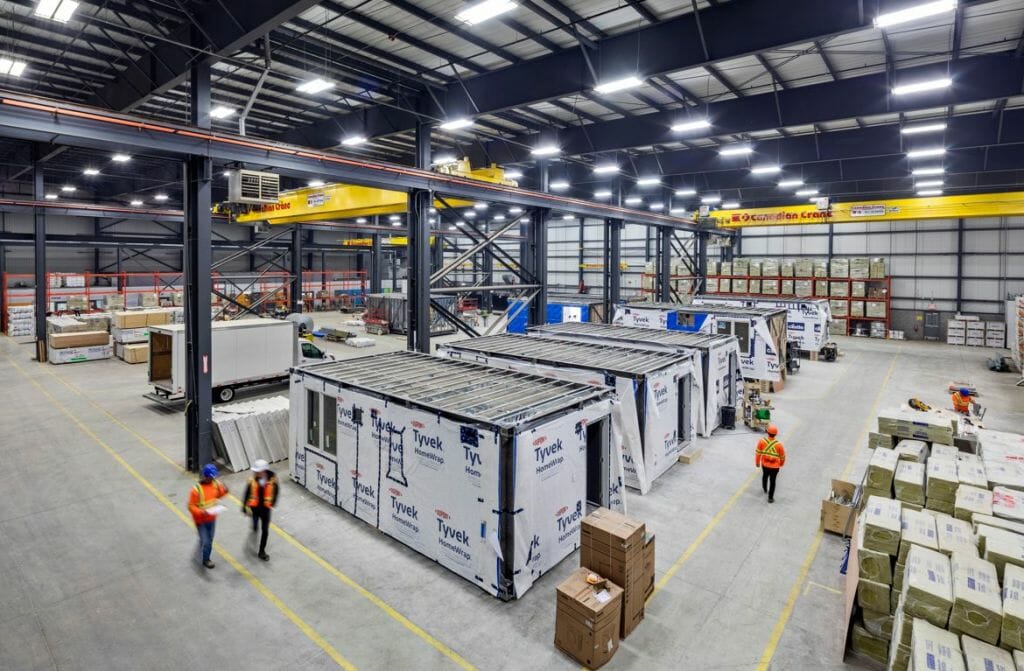
"BECC Modular said the dwellings we are building should be bult to Net Zero standards, " said Ali. "You know, basically building a development that would offset the energy that's used or needed to heat or cool. But then once we realized that the smartest way to attain Net Zero is basically build developments with higher standards."
Setting the Foundation With Steel
Ali started off his career as a red seal carpenter over 20 years ago, building his own steel business with the goal to eventually bring turnkey solutions to customers. In fact, he’s had a hand in building over 500 structures since then. “Be Creative and Be Capable” was the impetus and eventual motto for the name of BECC Construction Ltd., which was originally focused on building two-dimensional panelized structures.
Ali’s company expanded and created BECC Modular in 2020 to focus on volumetric structures. To date, BECC Modular has built just over 250 modules in Canada, with goals to expand in the U.S. But Ali hammers out BECC Modular’s mission down to one sentence. “I would say that we are in the business of manufacturing industrialized developments for future generations.” This mission is something that’s also baked into their structures, which follow Net Zero and Passive House design principles to create carbon neutral buildings.
The Goal of Passive House Principles and Net Zero
You can’t build a future-forward structure that meets Net Zero ambitions without first applying Passive House Principles, says Ali. “People say they know because they hear about it,” said Ali. “But hearing it is something else, and knowing is something else. These are flashy words, you know, but what are they?” For Ali, it’s about addressing emissions problems head on across the industry. According to the UN Environment Programme, about 39 percent of CO2 emissions come from the building and construction industry as of 2022. Of that 39 percent, 11 comes from the construction industry and 28 is contributed by building operations, says the World Green Building Council. These numbers weigh on him.
“We [BECC Modular] said the dwellings we are building should be built to Net Zero standards,” said Ali. “You know, basically building a development that would offset the energy that’s used or needed to heat or cool. But then once we started getting into it, we realized that the smartest way to attain Net Zero is basically build developments with higher standards.” This is why Passive House comes first for BECC Modular. It’s about making sure modules are created with up-to-date glycol-based heating and cooling systems; triple-paned windows; airtight construction; and other things. Only when these principles are met, can a building’s foundation be set for achieving Net Zero. That’s the sustainable value, but not the only reason why BECC Modular wants to achieve these ambitions.
“Government agencies and municipalities have requirements and a preference for buildings with standards ready for net zero,” said Ali. These building codes and goals trickle down from governments to municipalities, providing a win-win situation for both the country, and companies like BECC Modular that win those contracts. “It allows us to be a preferred vendor,” he said. “But it does require a lot of R&D, as you have these principles to meet. It all just comes in handy when you’re combining these goals.” And the other part? The technology. Ali puts it simply: “When one builds a cell phone or an iPad, they don’t build with technology from the 1950s and 60s. They build on today’s [tech] or the projected technology of a year, two years down the road,” he said. “What’s the life cycle of that? If the lifecycle of the phone is three years, you know, they basically projected and built it on those requirements. It would be a shame for us to build developments with the requirements from the 1980s or 90s. So I think we need to build our buildings with the future in mind. We’re talking 50 or 70 years. We need to build with technology that is future-forward. And that’s the conviction that drives us."
Hiring Quick to Build Quick? Listen to Advice, Says Ali
In 2020, amidst the pandemic, BECC Modular was in a position to hire—and hire quickly—for its factory and overall focus on volumetric structures. In fact, their first design project was awarded in 2020 and finished in 2021. From 2020 to now, BECC Modular grew to a team of over 100, bringing the total number
of people to just over 250 across all three of Ali’s companies. But hiring for a modular manufacturing business was new for Ali. He asked for advice around the industry on how to start, how to hire, and what kind of skills to focus on first.
“I was lucky enough to meet with some of the leading consultants that have been in the industry,” said Ali. “I was very humbled by some of the things that I’ve heard, seen, and what they shared with me. And I think one good thing for me was that I actually listened to what they said. A lot of the people coming from a construction background, when they get into modular manufacturing, they’re like, ‘no, that’s not how I’m gonna do it.’ But I would say you should listen to those people, that’s the best thing that you can do for yourself.” After hiring these crucial leaders, he highlighted what he considers three key positions for anyone starting a modular manufacturing company:
• VP of Design
• A plant manager
• A sales leader
His first hire was a strong VP of design and a design team. For general construction, design was relegated to outside consulting— which was what Ali was used to. But modular manufacturing is nothing without a strong designer. So he went ahead, hired his head of design, and then they hired their team–another 20 to 30 people.
The second necessary hire? A plant manager. “We needed someone that understood how to set up the plant, and that’s not something that exists in general contracting or in the commercial construction world,” said Ali. “So we needed to learn, but again, we hired one person, and then they hired 50 or 60 from then onward."
And lastly, having a sales team and executive that could act as a bridge and fill in the knowledge gaps between the plant, the designers, and the clients. “You have an estimating team [in construction], so that’s your sales team,” said Ali. “But here we figured out that you really need a different type of sales team that could basically go out and do outreach and educate the client base."
Improvement Through Experience, Iterations, and Efficiencies
With the goal of industrializing modular manufacturing comes a lot of lessons in efficiency, says Ali. “There’s a flow and I would say it took us a year and a half to get that flow,” says Ali. “But I think it’s a Kaizen concept, right? You have to keep improving all the time.” Over the years, BECC has been able to improve in two significant areas: cost and time. Ali says they have reduced the cost of their chassis by a significant amount. And in terms of time? While he says that they aren’t quite there yet with the ideal amount of hours spent on completing a module, the company has reduced manufacturing hours by over 40 percent thanks to efficiencies. For example, the chassis is now on its fourth or fifth iteration, with major changes made to the corners and welding time. BECC Modular made the decision to move their steel manufacturing from cutting and welding steel plates together to bending larger sheets of steel at specific angles.
“That didn’t just save us money in terms of the material cost, but it also saved us a tremendous amount of time on labor, in welding it and putting it together,” said Ali. “And simpler designs are more elegant and efficient."
5 Practices to Build Your Foundation for Modular Manufacturing
While you can’t beat experience, Ali says there are five things you should keep in mind when building a modular factory or entering the manufacturing industry:
1. Precise design: “Precision comes from design and product for us,” says Ali. His product choice is steel, but it doesn’t matter what you pick. It’s about knowing the ins and outs of your choice of product and how it will affect your design.
2. Climate-controlled construction: It’s about managing time when building your design in the factory, and making sure you are prepared for delivery (i.e., weatherproofing any sensitive points) so there are no issues when it comes to installing on-site.
3. Unifying your industrial design processes: Build your industrial library as best you can. While there is no set industry standard for sizes of modules, Ali encourages you to figure out what your best sizes are for walls, how to streamline your product choices, and create a repeatable manufacturing process.
4. High level of quality control: Make sure you introduce quality control into your process early and consistently. This means not only meeting CSA standards, but also having in-house QA staff that can answer and educate various stakeholders during any factory visit.
5. Speed: Manufacturing modules is not a linear process, unlike on-site construction. “A module manufacturer can actually be building all these things at the factory while you are doing the on-site work, excavating and more.” It comes down to the industrialization and automation of manufacturing modules and speeding up those processes through constant improvement.
About the Author: Karen P. Rivera is a freelance writer and editor with a passion for storytelling. She is a former United Nations-based reporter, with experience covering international breaking news, venture capital, emerging healthcare tech, and the video game industry.
More from Modular Advantage
Oregon’s Prevailing Wage Proposal: A Wake-Up Call for Modular Construction
In early February, 2024, the Massachusetts Board of Building Regulations and Standards (BBRS) released its proposed 10th Edition building codes. This draft included several amendments targeting modular construction that would have created an extremely difficult environment for the entire modular industry and could have eliminated the industry entirely in the state.
Behind the Design of Bethany Senior Terraces, NYC’s First Modular Passive House Senior Housing Project
As more developers seek to meet new regulations for energy efficiency, the team at Murray Engineering has set a new record. With the Bethany Senior Terraces project, Murray Engineering has helped to develop NYC’s first modular structure that fully encompasses passive house principles — introducing a new era of energy efficiency in the energy-conscious city that never sleeps.
How LAMOD is Using Modular to Address Inefficiency, Sustainability, and the Future of Construction
As developers, designers, and contractors seek to understand the evolving needs of the modular industry, no one is as well-versed in the benefits of going modular as Mārcis Kreičmanis. As the co-founder and CBDO of LAMOD in Riga, Latvia, Mārcis has made it his ultimate goal to address the inefficiencies of traditional construction.
From Furniture Builder to ‘Activist Architect’: Stuart Emmons’ Unique Journey
Stuart Emmons was fascinated by buildings at a young age. He remembers building sand cities with his brother during trips to the Jersey shore. His father gave him his first drawing table at the age of ten. Today, he is an experienced architect who received his FAIA in June 2025. The road he took is unique, to say the least.
Forge Craft Architecture + Design: Codes, Contracts, and Intellectual Property
Founding Principal and Director of Modular Practice for Forge Craft Architecture + Design, Rommel Sulit, discusses the implications of codes, contracts, and intellectual property on
modular construction.
Eisa Lee, the “Bilingual” Architect
Now as the founder of XL
Architecture and Modular Design in Ontario, Canada, she applies not just her education as a traditional architect but an entire holistic view on modular design. It’s this expansive view that guides her work on being a true partner that bridges the gap between architects and modular factories as they collaborate on the design process.
Tamarack Grove Engineering: Designing for the Modular Sector
The role of a structural engineer is crucial to the success of a modular project, from initial analysis to construction administration. Tamarack Grove offers structural engineering services — project analysis, plan creation, design creation, and construction administration — for commercial, manufacturing, facilities, public services, and modular. Modular is only one market sector the company serves but it is an increasingly popular one.
Engineer Masters the Art of Listening to His Customers
Since founding Modular Structural Consultants, LLC. in 2014, Yurianto has established a steady following of modular and container-based construction clients, primarily manufacturers. His services often include providing engineering calculations, reviewing drawings, and engineering certification
Inside College Road: Engineering the Modules of One of the World’s Tallest Modular Buildings
College Road is a groundbreaking modular residential development in East Croydon, South London by offsite developer and contractor, Tide, its modular company Vision Volumetric (VV), and engineered by MJH Structural Engineers.
Design for Flow: The Overlooked Power of DfMA in Modular Construction
Unlocking higher throughput, lower costs, and fewer redesigns by aligning Lean production flow with design for manufacturing and assembly.