What the Inflation Reduction Act Means for Modular Builders
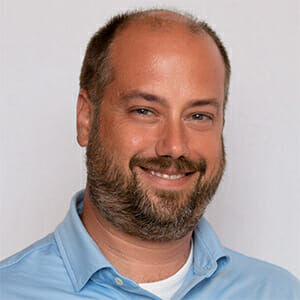
John Tienken is the regional sales manager for vertical markets at Mitsubishi Electric Trane HVAC US
Signed into law last August, the Inflation Reduction Act (IRA) is the country’s largest climate investment initiative. Hundreds of millions of dollars will be funneled into rebates and tax credits for greener and more energy-efficient building upgrades.
With space heating, air conditioning and water heating accounting for significant percentages of a building’s energy consumption, modular builders who want to take advantage of the IRA incentives should look closely at their HVAC and water heater technology and explore more energy-efficient options.
How Modular Builders Can Take Advantage of the IRA
Depending on the types of buildings they develop, modular builders can take advantage of IRA initiatives including:
- The updated 179D commercial buildings energy-efficiency tax deduction, which now offers base tax deductions to commercial building owners and designers of buildings meeting certain energy-efficiency standards.
Using a sliding scale, tax deduction levels are being increased to $.50 per square foot for energy savings of 25% and up to $1 per square foot for energy savings of 50% or greater. If a building meets certain prevailing wage requirements, bonus deductions are also available. These are determined based on a sliding scale of $2.50 per square foot for energy savings of 25% and up to $5 per square foot of energy savings of 50% or greater.
- The 45L investment tax credit (ITC), targeted towards single-family and multifamily building contractors who meet specified energy-efficiency requirements.
- For single-family residences, contractors can receive $2,500 for homes that meet ENERGY STAR standards and $5,000 for zero energy ready homes.
- For multifamily dwellings, contractors can receive $500 per unit that meets ENERGY STAR standards and $1,000 per unit for zero energy ready units. Modular builders meeting certain labor requirements can increase that amount.
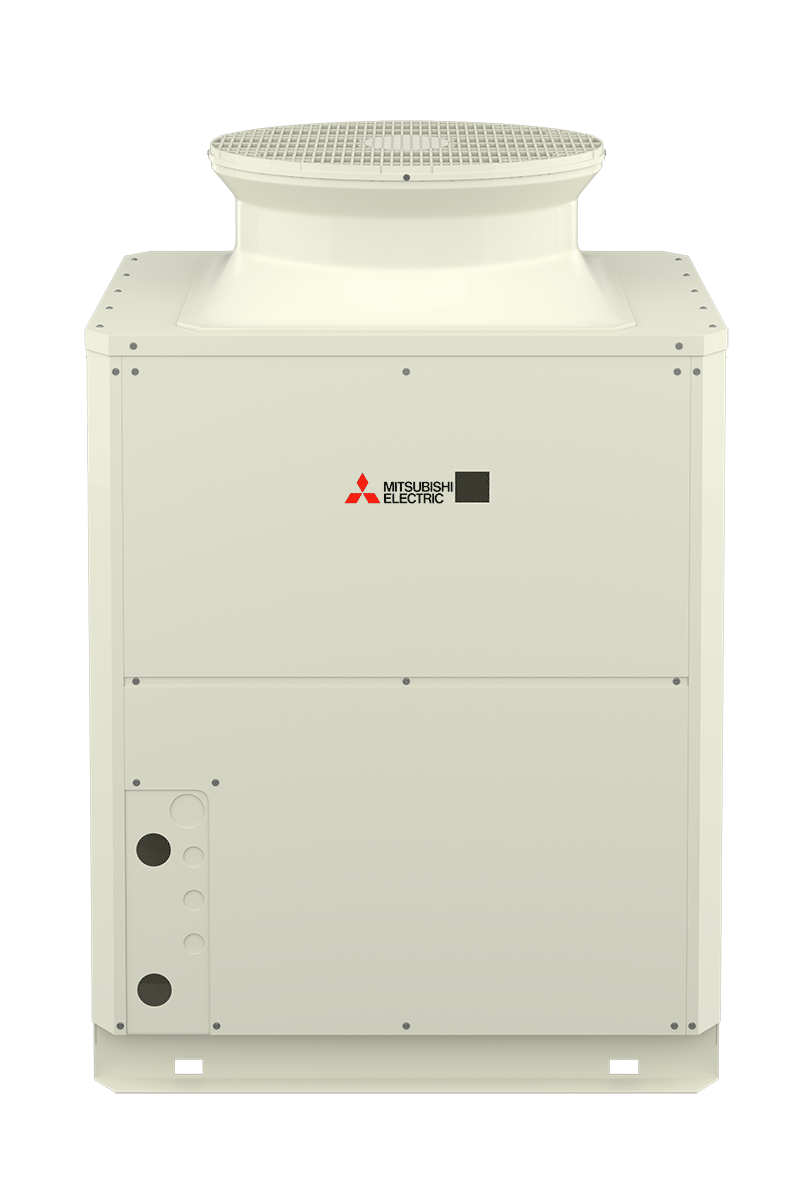
Issa Nesheiwat and Apex Modular Solutions participate in the “Tiny Home Experience” Event with Ulster Saving Bank.
Energy efficiency is clearly key to qualifying for 179D tax deductions and 45L ITCs. A joint 2022 report from the National Renewable Energy Laboratory, Oregon State University, Momentum Innovation Group and the U.S. Department of Energy laid out five key strategies for how modular builders can improve energy efficiency.
Modular builders can reach peak efficiency by focusing on envelope thermal control, envelope infiltration control, mechanical, electrical and plumbing (MEP) systems, smart controls and solar-plus-storage services.
HVAC & Water Heating Technology Plays a Crucial Energy-Usage Role
Next, we explore energy-efficient MEP system technology, such as HVAC and water heaters, and smart controls available for modular builders.
Space heating, air conditioning and water heating comprise the most significant percentages of buildings’ energy consumption. Seventy percent of energy consumption in single-family and multifamily residential buildings goes toward space heating, air conditioning and water heating. In multifamily buildings, domestic hot water accounts for roughly 25% of annual energy usage.
Natural gas continues to play a big role in powering these systems, but electric solutions are becoming more popular. The U.S. Energy Information Administration reports that 31% of commercial buildings use electricity as their primary space-heating source, while 35% of single-family and multifamily homes use electricity for space-heating.
To help reduce reliance on fossil fuels, electrification initiatives in the United States are starting to heat up. For instance, New York is the first state to ban natural gas and other fossil fuels in many new buildings. The state will prohibit gas-powered stoves, furnaces and propane heating and encourage climate-friendly, all-electric heat pumps, stoves and ovens in new structures less than seven stories by 2026 and for taller buildings by 2029. Washington and California have rules restricting the use of natural gas in commercial buildings, while several cities have similar rules – for new commercial and residential construction. Others are expected to follow suit.
The push for electrification extends beyond new construction. For instance, the Department of Energy’s Building Technologies Office in 2022 announced the Home Electrification Prize to fund innovative solutions to retrofit homes to eliminate using fossil fuels and accelerate electrification, including the installation of energy-efficient heat pumps.
A popular conventional electric system used by many modular builders is a relatively inexpensive packaged terminal air conditioner (PTAC). However, PTACs are no longer the most energy-efficient option as they are usually fixed speed, constantly cycle on and off to reach a desired set point and require 30 to 40-amp electrical strip circuits.
Newer tech, like all-electric heat pumps, use more energy-efficient compressors that greatly reduce the amount of energy needed to keep a space comfortable. With features like zoned heating and cooling and smart controls, heat pumps can make a world of difference in a modular building’s energy consumption.
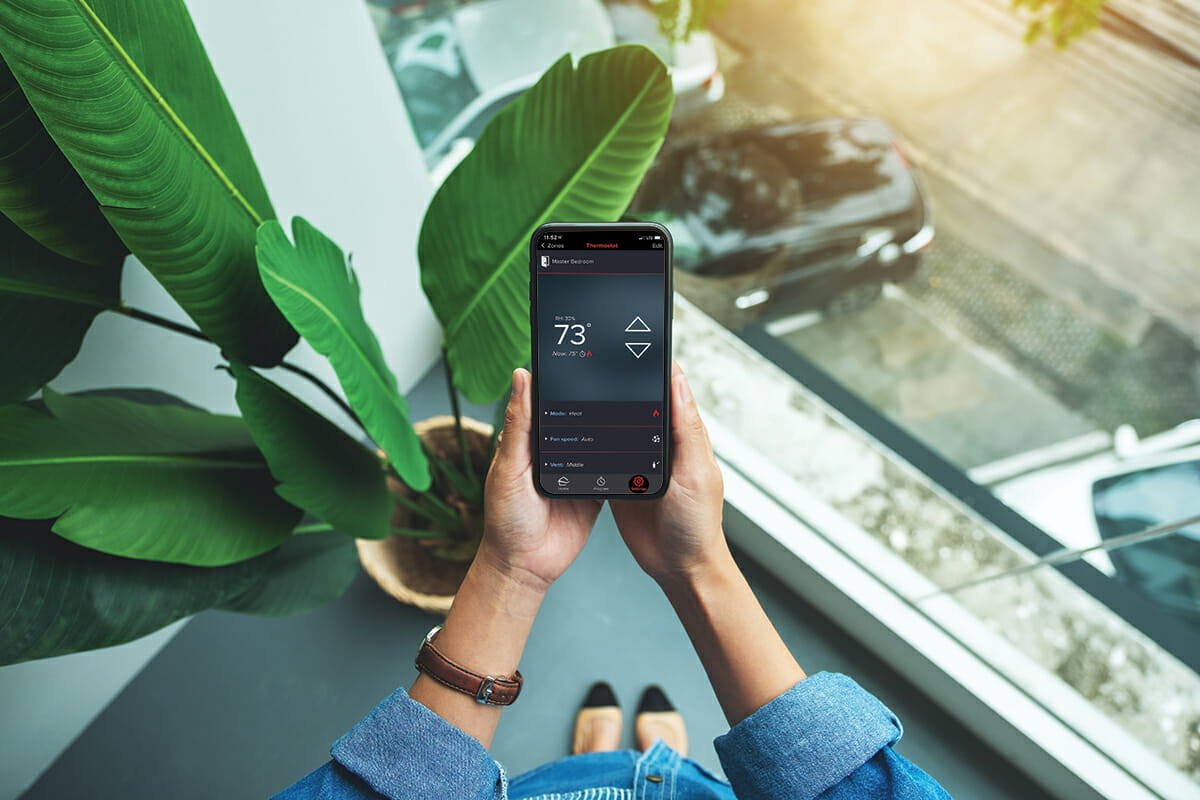
Smart controls allow users to monitor and control their HVAC systems remotely, through a building control panel, wireless controllers, or smartphones.
Why Heat Pumps Are Energy Efficient
Heat pumps are somewhat of a misnomer since they heat and air-condition spaces efficiently. For warmth, the outdoor heat pump absorbs heat energy from the outside air and transfers it to the inside unit via the refrigerant. The refrigerant is compressed, increasing its temperature significantly when it reaches the indoor coil. A fan blows air over the heated coil to deliver warm air to the room. To provide cooling, the process reverses.
Commercial and multifamily modular buildings are implementing all-electric heat pump technology called Variable Refrigerant Flow (VRF), the fastest-growing segment of the commercial HVAC industry. VRF compressors eliminate the wasteful start-and-stop cycle of conventional systems. The compressor motor varies its speed, regulating the amount of refrigerant delivered to the indoor units to match demand.
Through continuous operation, indoor unit fans help maintain an even, constant flow of filtered and conditioned air. VRF technology also divides a building into zones customized for comfort and energy efficiency, allowing the air to be easily turned off in certain spaces when unoccupied.
The compressors in single-family modular heat pumps work similarly.
For domestic hot water, multifamily modular builders should look at tech like electric heat pump water heaters since they offer energy savings of up to 70% compared to electric-resistance water heaters. Consider options with compressors that modulate refrigerant flow and heating capacity to match loads, thus improving energy efficiency.
How Smart Controls Improve Energy Efficiency
To better monitor and manage the energy usage of HVAC systems, modular builders should consider integrating energy-efficient smart thermostat controls in their buildings. Doing so makes it easier for building staff and tenants to maintain comfort settings in high-traffic spaces while conserving energy in unused spaces.
Smart controls allow users to monitor and control their HVAC systems remotely, through a building control panel, wireless controllers, or smartphones. Smart controls are even integrable with Amazon Alexa or Google Home smart home devices for a seamless, unified experience
Energy-Efficient Building Systems Are the Future
Energy-efficient buildings are now table stakes for savvy modular builders looking to attract investors, buyers and tenants. Energy efficiency means end-user cost savings, greener buildings, and IRA tax incentives for builders.
Savvy modular builders across commercial, multifamily, and single-family sectors who revamp their HVAC and water heating systems with more energy-efficient technology like heat pumps, zoning and smart controls will be well-positioned for a sustainable future.
More from Modular Advantage
Oregon’s Prevailing Wage Proposal: A Wake-Up Call for Modular Construction
In early February, 2024, the Massachusetts Board of Building Regulations and Standards (BBRS) released its proposed 10th Edition building codes. This draft included several amendments targeting modular construction that would have created an extremely difficult environment for the entire modular industry and could have eliminated the industry entirely in the state.
Behind the Design of Bethany Senior Terraces, NYC’s First Modular Passive House Senior Housing Project
As more developers seek to meet new regulations for energy efficiency, the team at Murray Engineering has set a new record. With the Bethany Senior Terraces project, Murray Engineering has helped to develop NYC’s first modular structure that fully encompasses passive house principles — introducing a new era of energy efficiency in the energy-conscious city that never sleeps.
How LAMOD is Using Modular to Address Inefficiency, Sustainability, and the Future of Construction
As developers, designers, and contractors seek to understand the evolving needs of the modular industry, no one is as well-versed in the benefits of going modular as Mārcis Kreičmanis. As the co-founder and CBDO of LAMOD in Riga, Latvia, Mārcis has made it his ultimate goal to address the inefficiencies of traditional construction.
From Furniture Builder to ‘Activist Architect’: Stuart Emmons’ Unique Journey
Stuart Emmons was fascinated by buildings at a young age. He remembers building sand cities with his brother during trips to the Jersey shore. His father gave him his first drawing table at the age of ten. Today, he is an experienced architect who received his FAIA in June 2025. The road he took is unique, to say the least.
Forge Craft Architecture + Design: Codes, Contracts, and Intellectual Property
Founding Principal and Director of Modular Practice for Forge Craft Architecture + Design, Rommel Sulit, discusses the implications of codes, contracts, and intellectual property on
modular construction.
Eisa Lee, the “Bilingual” Architect
Now as the founder of XL
Architecture and Modular Design in Ontario, Canada, she applies not just her education as a traditional architect but an entire holistic view on modular design. It’s this expansive view that guides her work on being a true partner that bridges the gap between architects and modular factories as they collaborate on the design process.
Tamarack Grove Engineering: Designing for the Modular Sector
The role of a structural engineer is crucial to the success of a modular project, from initial analysis to construction administration. Tamarack Grove offers structural engineering services — project analysis, plan creation, design creation, and construction administration — for commercial, manufacturing, facilities, public services, and modular. Modular is only one market sector the company serves but it is an increasingly popular one.
Engineer Masters the Art of Listening to His Customers
Since founding Modular Structural Consultants, LLC. in 2014, Yurianto has established a steady following of modular and container-based construction clients, primarily manufacturers. His services often include providing engineering calculations, reviewing drawings, and engineering certification
Inside College Road: Engineering the Modules of One of the World’s Tallest Modular Buildings
College Road is a groundbreaking modular residential development in East Croydon, South London by offsite developer and contractor, Tide, its modular company Vision Volumetric (VV), and engineered by MJH Structural Engineers.
Design for Flow: The Overlooked Power of DfMA in Modular Construction
Unlocking higher throughput, lower costs, and fewer redesigns by aligning Lean production flow with design for manufacturing and assembly.