Wilmot Modular: Always Willing to Help Out
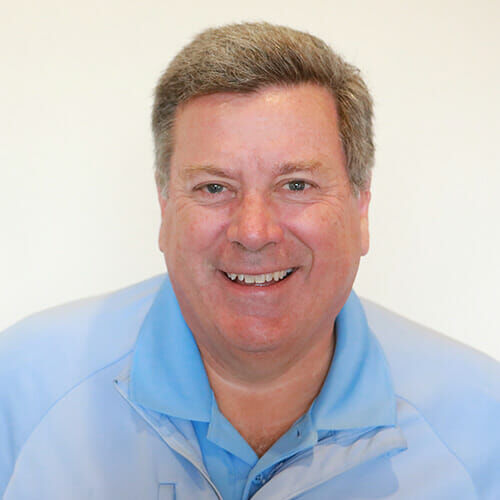
Mike Wilmot is the co-founder, co-owner, and president of Maryland-based Wilmot Modular. For over 30 years, Wilmot Modular has been building rapid and innovative modular building space solutions. In this article, Mike describes his company's experience responding to natural disasters and offers advice to other companies looking to help during the next disaster.
Based in Maryland, Wilmot Modular has been in business for over three decades and the company has responded to a number of disasters and emergencies over the years. Mike Wilmot is the Co-Founder, Co-Owner, and President of Wilmot Modular.
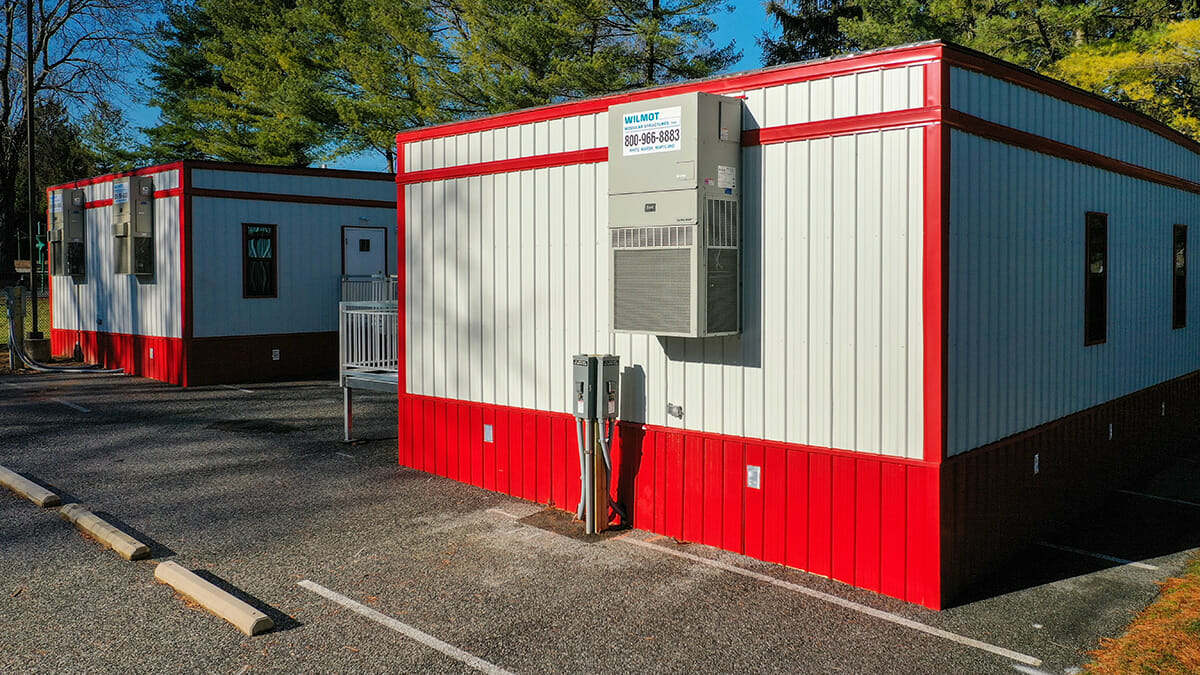
Following the outbreak of COVID-19, the Boys’ Latin School of Maryland wanted a separate space where students could wait until their parents picked them up. Wilmot Modular delivered these spaces in addition to an extra classroom.
COVID-19 emergency response
In April 2020, a makeshift hospital was being set up in a Washington, D.C. convention center. Before the building could begin treating COVID patients, the medical staff needed access to showers so they could properly decontaminate after their shifts.
“The convention center contacted us to see if we’d be able to help them out,” Wilmot says. “By hiring extra people and working around the clock, we retrofitted six buildings in about three weeks and delivered them to the temporary hospital. It allowed them to get up and running to take care of COVID patients.”
Hiring can be a challenge in the best of times but Wilmot says, “it was especially difficult at short notice and during COVID. But we tapped into our network of contacts and got it done.”
They’ve completed many other facilities related to the COVID-19 pandemic, including health suites and check-in stations for screening and testing students, employees, or visitors for COVID at various schools and businesses.
For example, for students who showed COVID symptoms or tested positive from a rapid test, the Boys’ Latin School of Maryland wanted a separate space where students could wait until their parents picked them up. They also installed an additional classroom, which allowed them greater flexibility to physically distance students. “By taking those steps, the school was able to re-open earlier than most other schools in the area. Many private schools, like Boys’ Latin, experienced an increase in attendance this past year because they found ways to provide in-person teaching,” Wilmot says.
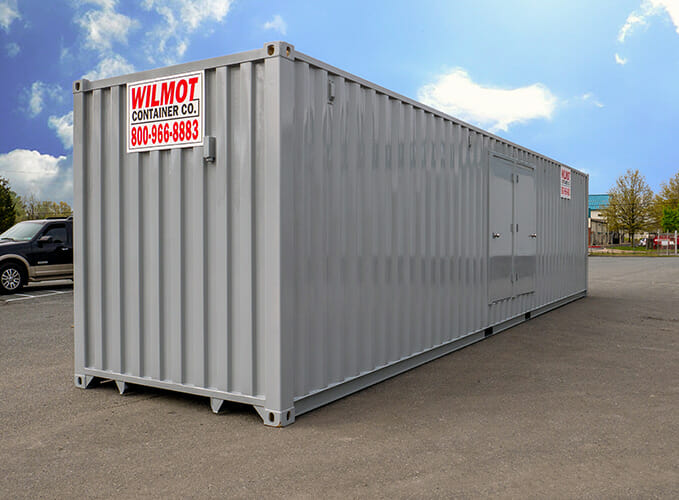
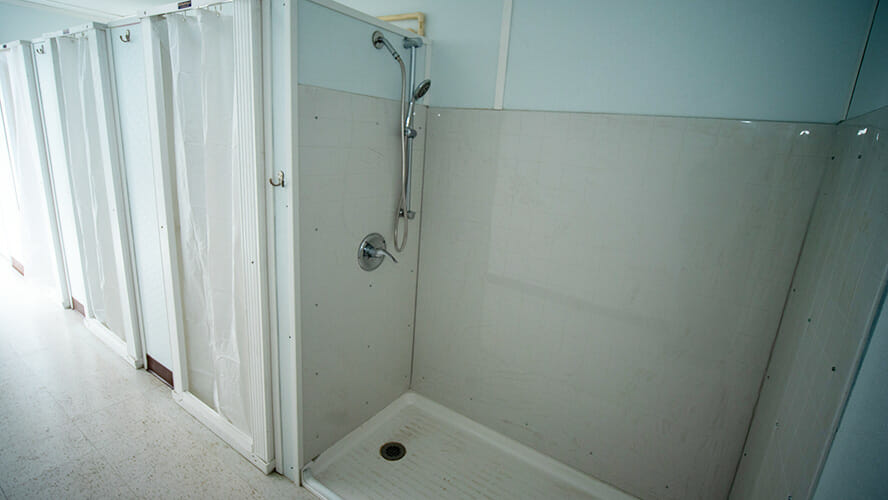
Before a Washington, DC-area temporary hospital could begin treating COVID patients in 2020, the medical staff needed access to showers so they could properly decontaminate after their shifts. Wilmot Modular delivered these retrofitted container structures for hospital staff.
Other disaster relief projects
Tessco is a distributor of wireless communications products based in Hunt Valley, Maryland. A broken water main caused a fire hydrant to shoot water through the side of their building in 2002. Suddenly, 145 employees had no place to go to work. “So we worked day and night, mobilized our existing fleet, and deployed 13 buildings within a week to get 145 people back to work,” Wilmot says.
A New Orleans medical facility was destroyed by Hurricane Katrina in 2005. Wilmot Modular was able to retrofit a building at their Maryland location and ship it to New Orleans — filled with supplies donated by their employees and suppliers. It took only one week to retrofit and ship the building. “Medical staff used the building while a new permanent facility was built. Apparently, the building was moved after the disaster clean-up because it was spotted in a different Louisiana city a few years later.”
On President’s Day weekend in 2008, the Bennett Middle School in Wicomico County, Maryland lost several classrooms in a fire. They called Wilmot Modular’s Emergency Response line and reached one of the company’s sales representatives. She contacted the fleet manager, who arranged for a crew to retrofit one of Wilmot Modular’s buildings that could serve as classroom space. “It was a holiday weekend, but our dispatcher pulled in a favor from a friend in the Maryland Department of Transportation,” Wilmot recalls. “She got us permission to haul the modular units on the highway and to go over a toll bridge that’s usually closed to truck traffic on a holiday. The classrooms were delivered and installed by Tuesday morning when students returned
to school.”
Advice to other modular businesses looking to help out in disasters
Obviously, speed is critically important in an emergency situation, so Wilmot says it helps if modular business owners are “tuned into what’s going on the news.” If they know that a hurricane is on its way, they can respond more quickly in its aftermath if necessary. The same point applies even to relatively small, local disasters. A flood in one small area might not make the national news, but if it’s in a state you can service, it’s news you should be aware of.
Once someone has reached out for help, Wilmot advises rapid communication with decision-makers and getting details of what the client is looking for in writing as soon as possible. “Then you can get materials and labor more quickly.”
Furthermore, Wilmot says, it really helps to speed things up if you already have relationships with companies, organizations, and governmental agencies involved in disaster relief. It also speeds things up if modular businesses already have relevant information about their current clients. For example, knowing how many employees the client has and understanding their day-to-day business operations can help with a rapid response if disaster strikes.
If a company is looking to get involved and help out when there’s a disaster, they need to be realistic. Not every team has what it takes. “You have to have people on your team who are willing to go the extra mile, because disaster relief work tends to involve a lot of intense, hard work at very odd hours. At Wilmot, we’ve been able to do that.”
Finally, Wilmot advises modular businesses to simply talk with their customers: “Make sure you’re on their radar as a source for quick building space, if needed.”
“You have to have people on your team who are willing to go the extra mile, because disaster relief work tends to involve a lot of intense, hard work at very odd hours. At Wilmot, we’ve been able to do that.”
Wilmot Modular’s Rapid Response Program
To help speed things up in an emergency, Wilmot Modular has instituted its own Rapid Response Program. Any organization, whether a current client or not, can sign up. Clients enter information about their location, all the necessary contact information, details about what the business does, square footage and other details regarding their current space, and so on. This means that the information is at the fingertips of Wilmot’s 24/7 on-call space planners.
The Program guarantees:
- 24 hour response to an emergency space requirement
- Fully wired, climate-controlled, functional sites ready for occupancy
- Emergency storage containers to secure critical property
Preparing for future disasters
When asked how the industry could better prepare to respond to future emergencies, Wilmot suggested, “It would be good to
create a centralized system that FEMA, or anybody else involved in an emergency, could use. Perhaps this could be created through MBI.” The idea is that if there was a disaster in North Carolina, say, it would be easy to look up the operators that serve North Carolina and see what inventory they have available for lease. “Then buildings could get shipped to where they’re needed more quickly.”
About the Author: Zena Ryder is a freelance writer, specializing in writing about construction and for construction companies. You can find her at Zena, Freelance Writer or on LinkedIn.
More from Modular Advantage
Oregon’s Prevailing Wage Proposal: A Wake-Up Call for Modular Construction
In early February, 2024, the Massachusetts Board of Building Regulations and Standards (BBRS) released its proposed 10th Edition building codes. This draft included several amendments targeting modular construction that would have created an extremely difficult environment for the entire modular industry and could have eliminated the industry entirely in the state.
Behind the Design of Bethany Senior Terraces, NYC’s First Modular Passive House Senior Housing Project
As more developers seek to meet new regulations for energy efficiency, the team at Murray Engineering has set a new record. With the Bethany Senior Terraces project, Murray Engineering has helped to develop NYC’s first modular structure that fully encompasses passive house principles — introducing a new era of energy efficiency in the energy-conscious city that never sleeps.
How LAMOD is Using Modular to Address Inefficiency, Sustainability, and the Future of Construction
As developers, designers, and contractors seek to understand the evolving needs of the modular industry, no one is as well-versed in the benefits of going modular as Mārcis Kreičmanis. As the co-founder and CBDO of LAMOD in Riga, Latvia, Mārcis has made it his ultimate goal to address the inefficiencies of traditional construction.
From Furniture Builder to ‘Activist Architect’: Stuart Emmons’ Unique Journey
Stuart Emmons was fascinated by buildings at a young age. He remembers building sand cities with his brother during trips to the Jersey shore. His father gave him his first drawing table at the age of ten. Today, he is an experienced architect who received his FAIA in June 2025. The road he took is unique, to say the least.
Forge Craft Architecture + Design: Codes, Contracts, and Intellectual Property
Founding Principal and Director of Modular Practice for Forge Craft Architecture + Design, Rommel Sulit, discusses the implications of codes, contracts, and intellectual property on
modular construction.
Eisa Lee, the “Bilingual” Architect
Now as the founder of XL
Architecture and Modular Design in Ontario, Canada, she applies not just her education as a traditional architect but an entire holistic view on modular design. It’s this expansive view that guides her work on being a true partner that bridges the gap between architects and modular factories as they collaborate on the design process.
Tamarack Grove Engineering: Designing for the Modular Sector
The role of a structural engineer is crucial to the success of a modular project, from initial analysis to construction administration. Tamarack Grove offers structural engineering services — project analysis, plan creation, design creation, and construction administration — for commercial, manufacturing, facilities, public services, and modular. Modular is only one market sector the company serves but it is an increasingly popular one.
Engineer Masters the Art of Listening to His Customers
Since founding Modular Structural Consultants, LLC. in 2014, Yurianto has established a steady following of modular and container-based construction clients, primarily manufacturers. His services often include providing engineering calculations, reviewing drawings, and engineering certification
Inside College Road: Engineering the Modules of One of the World’s Tallest Modular Buildings
College Road is a groundbreaking modular residential development in East Croydon, South London by offsite developer and contractor, Tide, its modular company Vision Volumetric (VV), and engineered by MJH Structural Engineers.
Design for Flow: The Overlooked Power of DfMA in Modular Construction
Unlocking higher throughput, lower costs, and fewer redesigns by aligning Lean production flow with design for manufacturing and assembly.