The Growth of Remote Virtual Inspections
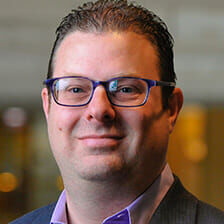
About the Author: Ryan M. Colker is Vice President, Innovation, at the International Code Council.
The COVID-19 pandemic has brought lots of change to the construction industry—particularly for building code and fire safety departments. Most states and the federal government declared code administration and enforcement essential services. However, many departments were faced with the need to implement new policies and procedures to assure their work could continue safely.
The International Code Council conducted a survey of code departments in March and April of 2020 to gauge their virtual capabilities. Based on over 1,150 responses from all 50 states and Washington, DC, the survey found that the majority of departments (93%) were still doing inspections either remotely or in person. About two-thirds (65%) of jurisdictions reported that some or all employees that conduct plan review or inspections are working remotely. While many jurisdictions made the switch to electronic processes, a large percentage still did not have the capacity to go virtual—for example, 61% did not have the capability to do electronic or remote inspections.1
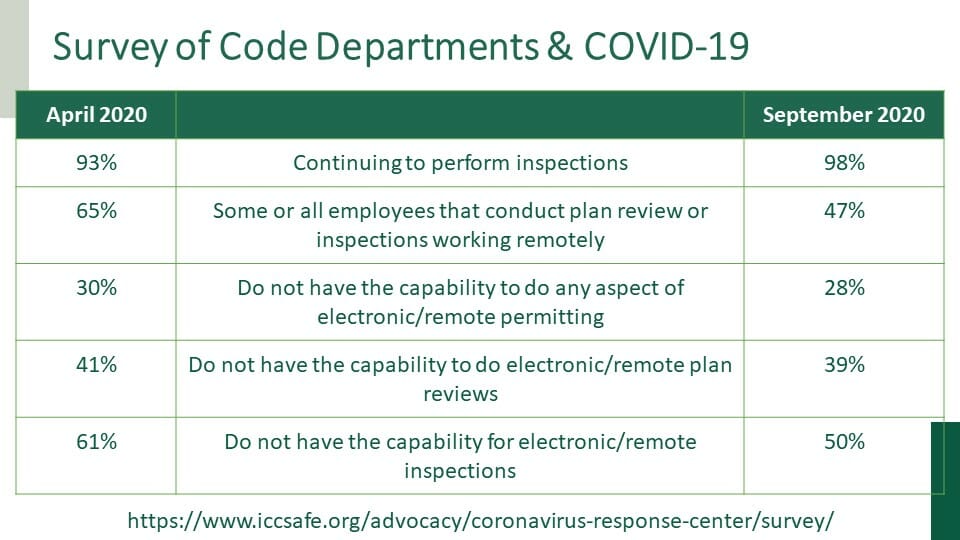
In August and September 2020, the Code Council again surveyed code departments to see how their processes and practices changed given a little time to adapt. By September nearly all departments were performing inspections (98% versus 93% in April) while nearly half still had key staff working remotely (47% versus 65% in April). In September 53% of departments still did not have the capability to do remote virtual inspections (down from 61% in April).
While remote virtual inspection (RVI) was seen by many as an opportunity to reduce exposure to the virus, many departments were unsure of where to start. Some larger jurisdictions including Los Angeles City and County and North Las Vegas, Nevada already had virtual inspection programs for many small or routine projects and were willing to share their lessons learned with others. Smaller, rural jurisdictions like Miami, Ohio were using remote virtual inspections to cut down on travel times. The Code Council produced a series of documents and held webinars to help provide guidance and get departments up to speed.2 The most recent publication, Model Program for Online Services: Permitting, Plan Review and Remote Inspections, captures best practices from building officials, industry professionals and inspection agencies.3
Remote virtual inspections and off-site construction
The two Code Council surveys primarily captured results in the context of inspections at the job site, but could provide insight into the potential for growth in remote virtual inspections for off-site construction. As code departments become more comfortable with the technology that comfort may spread to state industrialized building programs. The recently released off-site construction standards developed by the Code Council and the Modular Building Institute (MBI) allows for the use of remote virtual inspections at the discretion of the Authority Having Jurisdiction.4
One off-site construction project taking advantage of remote virtual inspection is a 296-room, 105-foot-tall modular citizenM hotel going up in Washington, DC. As COVID-19 threatened to slow construction, the hotel chain, local development manager Altus Realty and third party inspection agency ICC-NTA looked for solutions to mitigate the risk. They approached the District’s Department of Consumer and Regulatory Affairs (DCRA) about the possibility of using remote virtual inspection within the factory in Poland. After a few practice inspections to test out the technology and to ensure DCRA and NTA approved of the procedures, a formal all-virtual inspection process was underway. To assure the same level of quality and compliance as an on-site inspection, NTA personnel developed remote virtual inspection procedures that mirrored NTA’s in-plant inspection procedures and the DCRA Third-Party Program Procedure Manual requirements.
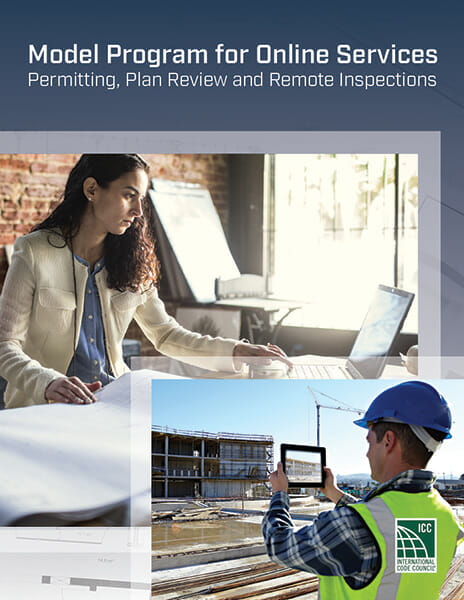
In addition to ramping up the virtual inspection program at NTA the manufacturer also needed to prepare for the virtual inspection process. Quality assurance personnel were assigned to assist with inspections. In advance of the inspection on-site personnel provide NTA with copies of all material listings for each module. During the inspection plant personnel show the serial number for the unit being inspected and walk through an inspection checklist with the NTA inspector. Close ups or more focused videos can be requested by the NTA inspector.
Using the remote virtual inspection process NTA inspectors can monitor testing of modules including water testing of window installation, pressure testing of plumbing systems and other important procedures.
While it took some getting used to for the inspectors, a good rapport with the quality assurance personnel in the factory and comfort on the part of DCRA with the protocols put in place by NTA, the remote virtual inspection process provided some valuable lessons for the project team and may open opportunities for further use of remote virtual inspections in the future.
Endnotes
1 International Code Council, Building Safety and COVID-19: Analysis of U.S. Code Department Responses to the Pandemic. July 1, 2020. https://www.iccsafe.org/wp-content/uploads/20-18952_GR_Survey_Analysis_RPT_FINAL_HIRES.pdf
2 See https://www.iccsafe.org/advocacy/coronavirus-response-center/virtual/ for access to virtual resources.
3 International Code Council, Model Program for Online Services: Permitting, Plan Review and Remote Inspections. April 2021. https://shop.iccsafe.org/model-program-for-online-services-permitting-plan-review-and-remote-inspections.html
4 ICC/MBI 1205-2021 Standard for Off-Site Construction: Inspection and Regulatory Compliance, Section 301.2. https://codes.iccsafe.org/content/ICC12052021P1/chapter-3-plan-approvals-and-inspection-procedures
More from Modular Advantage
Oregon’s Prevailing Wage Proposal: A Wake-Up Call for Modular Construction
In early February, 2024, the Massachusetts Board of Building Regulations and Standards (BBRS) released its proposed 10th Edition building codes. This draft included several amendments targeting modular construction that would have created an extremely difficult environment for the entire modular industry and could have eliminated the industry entirely in the state.
Behind the Design of Bethany Senior Terraces, NYC’s First Modular Passive House Senior Housing Project
As more developers seek to meet new regulations for energy efficiency, the team at Murray Engineering has set a new record. With the Bethany Senior Terraces project, Murray Engineering has helped to develop NYC’s first modular structure that fully encompasses passive house principles — introducing a new era of energy efficiency in the energy-conscious city that never sleeps.
How LAMOD is Using Modular to Address Inefficiency, Sustainability, and the Future of Construction
As developers, designers, and contractors seek to understand the evolving needs of the modular industry, no one is as well-versed in the benefits of going modular as Mārcis Kreičmanis. As the co-founder and CBDO of LAMOD in Riga, Latvia, Mārcis has made it his ultimate goal to address the inefficiencies of traditional construction.
From Furniture Builder to ‘Activist Architect’: Stuart Emmons’ Unique Journey
Stuart Emmons was fascinated by buildings at a young age. He remembers building sand cities with his brother during trips to the Jersey shore. His father gave him his first drawing table at the age of ten. Today, he is an experienced architect who received his FAIA in June 2025. The road he took is unique, to say the least.
Forge Craft Architecture + Design: Codes, Contracts, and Intellectual Property
Founding Principal and Director of Modular Practice for Forge Craft Architecture + Design, Rommel Sulit, discusses the implications of codes, contracts, and intellectual property on
modular construction.
Eisa Lee, the “Bilingual” Architect
Now as the founder of XL
Architecture and Modular Design in Ontario, Canada, she applies not just her education as a traditional architect but an entire holistic view on modular design. It’s this expansive view that guides her work on being a true partner that bridges the gap between architects and modular factories as they collaborate on the design process.
Tamarack Grove Engineering: Designing for the Modular Sector
The role of a structural engineer is crucial to the success of a modular project, from initial analysis to construction administration. Tamarack Grove offers structural engineering services — project analysis, plan creation, design creation, and construction administration — for commercial, manufacturing, facilities, public services, and modular. Modular is only one market sector the company serves but it is an increasingly popular one.
Engineer Masters the Art of Listening to His Customers
Since founding Modular Structural Consultants, LLC. in 2014, Yurianto has established a steady following of modular and container-based construction clients, primarily manufacturers. His services often include providing engineering calculations, reviewing drawings, and engineering certification
Inside College Road: Engineering the Modules of One of the World’s Tallest Modular Buildings
College Road is a groundbreaking modular residential development in East Croydon, South London by offsite developer and contractor, Tide, its modular company Vision Volumetric (VV), and engineered by MJH Structural Engineers.
Design for Flow: The Overlooked Power of DfMA in Modular Construction
Unlocking higher throughput, lower costs, and fewer redesigns by aligning Lean production flow with design for manufacturing and assembly.