The Bones of Modular Construction: Benefits and Challenges of 3 Common Building Materials
Wood, steel, and concrete: Each has been used in various forms of traditional construction for centuries (with steel being the most recent addition), and each provides specific benefits and challenges to consider. In a nutshell, wood is light and moderately strong, ideal for small and medium-sized buildings. Steel is heavier but stronger and perfect for taller, more complex frameworks. Concrete is the heaviest and is best suited for foundations and reinforced structures.
Each of these materials has its use in modular construction, as well. The modular construction process, however, allows for a slightly different set of benefits and challenges, and the design of the modular project can determine which materials need to be used during construction.
Below, we break open the nutshell and explore each material’s use in modular construction.
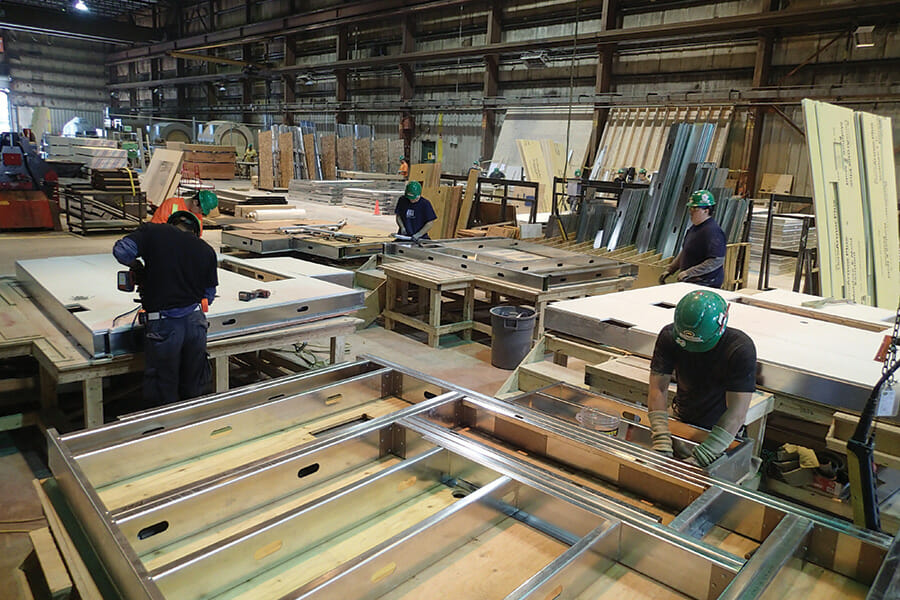
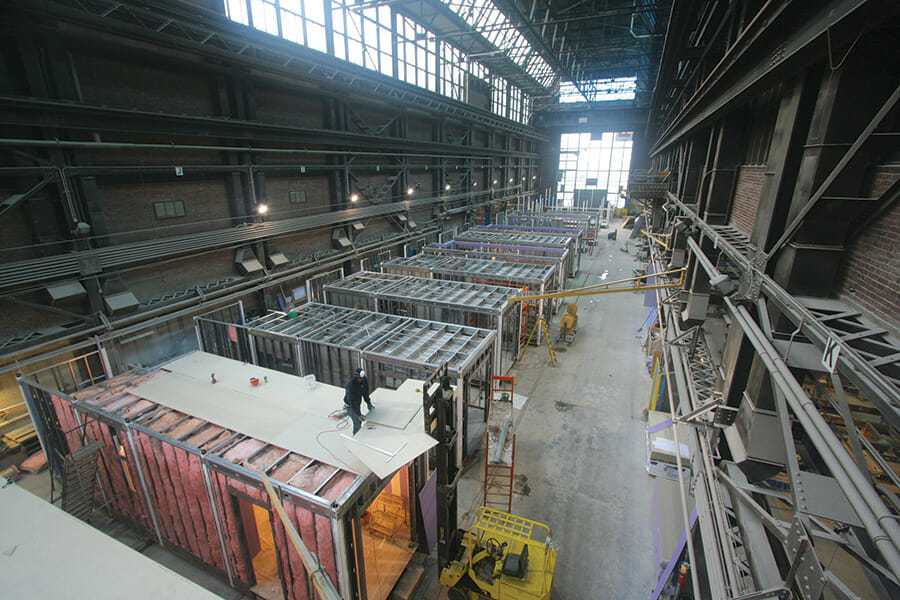

Modular Construction with Wood
According to Allison Arieff & Bryan Burkhart, the authors of the book “Prefab”, use of wood in modular construction is the most common practice since the seventeenth century. Using wood in modular construction is very beneficial due to its properties as a construction material. Wood is easy to manipulate by hand or with machinery, has low toxicity, is biodegradable, is easy to reuse and recycle, and is affordable. Wood is a combustible material that has an important thermal property in that it does not expand against heat. In fact, it gains strength when it dries out with more heat. Wood is also a good insulator against electricity (helps to minimize electrical shocks) and energy loss.
Common structural members used include 2X individual pieces used in roof trusses, floor trusses, walls; wood I-joists, engineered glue-laminated beams, plywood, oriented strand board (OSB) and composite panels. Wood is being used in the modular fabrication shop to create exterior wall panels that include additional layers for waterproofing, insulation, vapor barrier, drywall and siding.
Prefabrication in a factory allows the wood to stay dry and at a constant temperature while being precisely cut and fitted to exacting tolerances. Prefabrication minimizes waste, saves resources, and simplifies recycling of waste. Factory-produced components or modules can be transported to the site and assembled with extremely tight tolerances. With its ability to be manipulated, laminated and reused, wood will continue to be a sustainable material source for modular construction.
Modular Construction with Steel/Aluminum
Metals can be described as ductile, hard, conductive, precise, and strong. They are classified as ferrous and non-ferrous metals. Ferrous metals are primarily used in structural applications because they are strong, ductile and durable due to their high iron content. They can be treated with coatings such as galvanizing to prevent corrosion when exposed to weather and manipulated easily to create a variety of shapes and sizes. Non-ferrous are used in roofing and cladding applications and are natural corrosion-resistant metals.
Although steel is an expensive material when compared to wood and concrete, steel is the more economical choice if building long-span structures, high-rise structures and unique geometric designs because of its strength and speed of construction. Steel is inorganic and non-combustible material, therefore it has an advantage against fire. Another advantage of steel structures is that they are very strong and can survive even in the most critical weather conditions. It can be used for a long time due to its strength and durability. It can be transported easily and can be reused by unbolting its components.
Aluminum is a non-ferrous alloy that is ductile and well-known for its corrosion-resistance. It can be recycled repeatedly with little energy or loss of its material properties. Because aluminum is light and durable, it can be easily assembled into panels and modules, shipped and erected quickly and accurately.
Light-gauge steel components (which have a higher strength-to weight ratio) can be used in place of 2X lumber or in tandem with wood framing. For studs and rafters, members are formed into C-shaped sections. For top and bottom wall plates and joist headers, channel sections are used. Holes are placed in them every two feet to accommodate wiring and plumbing.
Modular Construction with Concrete
Traditional onsite construction involves concrete that is mixed from Portland cement, sand, aggregate (small gravel of various sizes) and water in a process called hydration which hardens (cures) the concrete to its specified strength (i.e., 3000 psi). Concrete relies on fiber and steel reinforcing for its tensile strength. The material is labor intensive because formwork must be erected, concrete placed (poured into the formwork), and then finished (troweled and smoothed).
Modular construction with concrete typically consists of buildings such as restrooms, concession buildings, shower facilities, shelters, utility buildings, etc. in which the walls are fabricated with high strength precast concrete or concrete masonry units (CMUs) and the roof can be constructed of lightweight precast concrete panels, metal panels, concrete tiles, or traditional architectural shingles. The buildings are designed and constructed to meet all local building codes. They can have a variety of color and texture options such as brick, stone, stucco, split-face block, board and bat siding, or horizontal lap siding. The buildings are prefabricated and delivered complete and ready-to-use, including plumbing and electrical where applicable. Modular concrete buildings can also be constructed on permanent, poured-in-place reinforced concrete foundations. These buildings are permanently anchored to a massive foundation with a deep footing designed for heavy seismic loads to ensure stability and integrity of the entire structure.
More from Modular Advantage
Oregon’s Prevailing Wage Proposal: A Wake-Up Call for Modular Construction
In early February, 2024, the Massachusetts Board of Building Regulations and Standards (BBRS) released its proposed 10th Edition building codes. This draft included several amendments targeting modular construction that would have created an extremely difficult environment for the entire modular industry and could have eliminated the industry entirely in the state.
Behind the Design of Bethany Senior Terraces, NYC’s First Modular Passive House Senior Housing Project
As more developers seek to meet new regulations for energy efficiency, the team at Murray Engineering has set a new record. With the Bethany Senior Terraces project, Murray Engineering has helped to develop NYC’s first modular structure that fully encompasses passive house principles — introducing a new era of energy efficiency in the energy-conscious city that never sleeps.
How LAMOD is Using Modular to Address Inefficiency, Sustainability, and the Future of Construction
As developers, designers, and contractors seek to understand the evolving needs of the modular industry, no one is as well-versed in the benefits of going modular as Mārcis Kreičmanis. As the co-founder and CBDO of LAMOD in Riga, Latvia, Mārcis has made it his ultimate goal to address the inefficiencies of traditional construction.
From Furniture Builder to ‘Activist Architect’: Stuart Emmons’ Unique Journey
Stuart Emmons was fascinated by buildings at a young age. He remembers building sand cities with his brother during trips to the Jersey shore. His father gave him his first drawing table at the age of ten. Today, he is an experienced architect who received his FAIA in June 2025. The road he took is unique, to say the least.
Forge Craft Architecture + Design: Codes, Contracts, and Intellectual Property
Founding Principal and Director of Modular Practice for Forge Craft Architecture + Design, Rommel Sulit, discusses the implications of codes, contracts, and intellectual property on
modular construction.
Eisa Lee, the “Bilingual” Architect
Now as the founder of XL
Architecture and Modular Design in Ontario, Canada, she applies not just her education as a traditional architect but an entire holistic view on modular design. It’s this expansive view that guides her work on being a true partner that bridges the gap between architects and modular factories as they collaborate on the design process.
Tamarack Grove Engineering: Designing for the Modular Sector
The role of a structural engineer is crucial to the success of a modular project, from initial analysis to construction administration. Tamarack Grove offers structural engineering services — project analysis, plan creation, design creation, and construction administration — for commercial, manufacturing, facilities, public services, and modular. Modular is only one market sector the company serves but it is an increasingly popular one.
Engineer Masters the Art of Listening to His Customers
Since founding Modular Structural Consultants, LLC. in 2014, Yurianto has established a steady following of modular and container-based construction clients, primarily manufacturers. His services often include providing engineering calculations, reviewing drawings, and engineering certification
Inside College Road: Engineering the Modules of One of the World’s Tallest Modular Buildings
College Road is a groundbreaking modular residential development in East Croydon, South London by offsite developer and contractor, Tide, its modular company Vision Volumetric (VV), and engineered by MJH Structural Engineers.
Design for Flow: The Overlooked Power of DfMA in Modular Construction
Unlocking higher throughput, lower costs, and fewer redesigns by aligning Lean production flow with design for manufacturing and assembly.