Relocatable Buildings vs. Permanent Modular Construction: What's the Difference?
Modular construction is revolutionizing the construction industry as a super-efficient and sustainable solution for building faster, stronger, and more predictably.
There are two types of modular structures- Relocatable Buildings and Permanent Modular Construction. While both construction types offer a plethora of benefits, there are distinct differences.
In this article, we'll help you understand the differences between permanent modular construction and relocatable buildings.
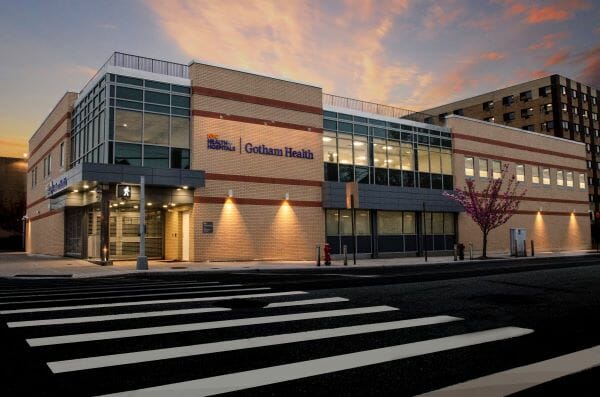
This hospital in New York is an MBI Awards of Distinction-winning example of permanent modular construction.
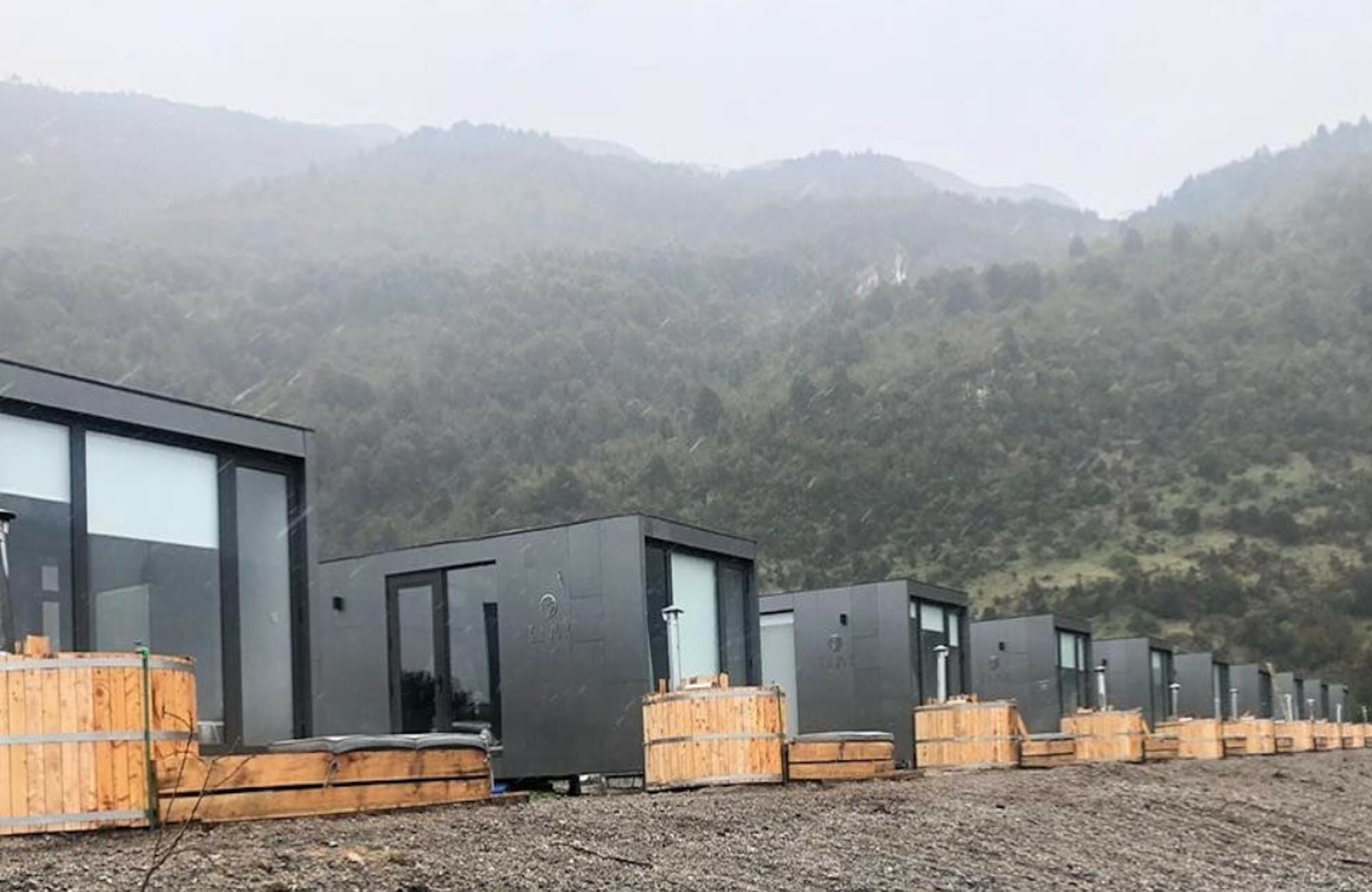
These luxury cabins are an MBI Awards of Distinction-winning example of relocatable buildings.
What is Modular Construction?
Also known as volumetric construction, modular construction uses individual sections or modules, which are assembled off-site in factories under controlled conditions, to create complete structures of all shapes and sizes.
The modules themselves use the same designs and materials as traditional construction and meet all the same building standards and codes. The modules are then transported and put together at the final construction site.
There are two main methods of modular construction:
Permanent Modular Construction (PMC)
PMC is a sustainable and innovative building technique that utilizes offsite and lean manufacturing methods to prefabricate either single or multi-story structures in modular sections. PMC can be integrated into an existing structure or can be built to stand independently. The modules can then be completed with MEP interior finishes, fixtures, and appliances. The Hawaii Film Studio, for example, used PMC to meet strict timeline and budget requirements. Other examples of permanent modular construction include healthcare facilities, hotels, schools, and restaurants.
Relocatable Buildings
Also known as portable buildings, RBs are partially or completely constructed structures that also abide by set building codes and are assembled in a controlled manufacturing facility through the modular construction process.
Relocatable buildings are made to be repurposed and transported to various building sites. They can be used for medical clinics, schools, sales centers, and construction sites, among others.
The Differences Between Relocatable and Permanent Modular
1. Duration Of Use
Permanent modular structures are fabricated and installed for long-term use. They are designed to be durable, just like conventional buildings, and can last just as long (or longer) than traditionally-constructed buildings.
Relocatable buildings, on the other hand, are installed for a shorter intended duration; a few months or a year, for instance. They are also designed durable enough to withstand several relocations and installations.
2. Types of Materials Used
Because permanent modular structures are intended for longer use, they are typically constructed with wood, steel, and/or concrete. Relocatable buildings, on the other hand, are usually made of wood to make them lightweight and easier to transport and reinstall.
3. Building Purpose
Permanent modular buildings are designed to remain in one location for an extended period of time.
Temporary modular buildings are ideal for situations that demand quick construction and future relocation and repurposing. They are mostly built to offer temporary housing such as, construction sites, or mobile showrooms, as well as for some commercial purposes.
4. Architecture
When it comes to architecture options, temporary modular structures offer less design and layout choices. They also offer fewer options for customization.
Though the architect's plans for PMC must be settled well before construction begins, permanent modular buildings offer nearly endless options. From the addition of lobbies to elevators and stairwells, these structures offer construction engineers and consumers alike countless design possibilities.
5. Construction Duration
While the duration of construction will depend on the scope of work, relocatable buildings have the potential to be on-site and ready to use within weeks.
On the other hand, permanent modular buildings may take months or more to construct and assemble on-site based on the structure's size and design. Despite the differences between the two types of modular construction, both types offer owners many benefits. The benefits include: less material waste, faster completion of projects because of indoor construction, safer construction, and a quicker return on investment. For a complete list of the Modular Building Institute's PMC and RB manufacturers, click here.
More from Modular Advantage
Oregon’s Prevailing Wage Proposal: A Wake-Up Call for Modular Construction
Should House Bill 2688A become law, building projects would increase in price, face longer completion timelines, and produce significantly more waste. The bill also incentivizes contract awards to out of state businesses who would not reinvest their earnings into the local Oregon economy.
Behind the Design of Bethany Senior Terraces, NYC’s First Modular Passive House Senior Housing Project
As more developers seek to meet new regulations for energy efficiency, the team at Murray Engineering has set a new record. With the Bethany Senior Terraces project, Murray Engineering has helped to develop NYC’s first modular structure that fully encompasses passive house principles — introducing a new era of energy efficiency in the energy-conscious city that never sleeps.
How LAMOD is Using Modular to Address Inefficiency, Sustainability, and the Future of Construction
As developers, designers, and contractors seek to understand the evolving needs of the modular industry, no one is as well-versed in the benefits of going modular as Mārcis Kreičmanis. As the co-founder and CBDO of LAMOD in Riga, Latvia, Mārcis has made it his ultimate goal to address the inefficiencies of traditional construction.
From Furniture Builder to ‘Activist Architect’: Stuart Emmons’ Unique Journey
Stuart Emmons was fascinated by buildings at a young age. He remembers building sand cities with his brother during trips to the Jersey shore. His father gave him his first drawing table at the age of ten. Today, he is an experienced architect who received his FAIA in June 2025. The road he took is unique, to say the least.
Forge Craft Architecture + Design: Codes, Contracts, and Intellectual Property
Founding Principal and Director of Modular Practice for Forge Craft Architecture + Design, Rommel Sulit, discusses the implications of codes, contracts, and intellectual property on
modular construction.
Eisa Lee, the “Bilingual” Architect
Now as the founder of XL
Architecture and Modular Design in Ontario, Canada, she applies not just her education as a traditional architect but an entire holistic view on modular design. It’s this expansive view that guides her work on being a true partner that bridges the gap between architects and modular factories as they collaborate on the design process.
Tamarack Grove Engineering: Designing for the Modular Sector
The role of a structural engineer is crucial to the success of a modular project, from initial analysis to construction administration. Tamarack Grove offers structural engineering services — project analysis, plan creation, design creation, and construction administration — for commercial, manufacturing, facilities, public services, and modular. Modular is only one market sector the company serves but it is an increasingly popular one.
Engineer Masters the Art of Listening to His Customers
Since founding Modular Structural Consultants, LLC. in 2014, Yurianto has established a steady following of modular and container-based construction clients, primarily manufacturers. His services often include providing engineering calculations, reviewing drawings, and engineering certification
Inside College Road: Engineering the Modules of One of the World’s Tallest Modular Buildings
College Road is a groundbreaking modular residential development in East Croydon, South London by offsite developer and contractor, Tide, its modular company Vision Volumetric (VV), and engineered by MJH Structural Engineers.
Design for Flow: The Overlooked Power of DfMA in Modular Construction
Unlocking higher throughput, lower costs, and fewer redesigns by aligning Lean production flow with design for manufacturing and assembly.