How Modular Construction Will Get You a Better Return on Investment
Modular buildings are created in a factory and then shipped piece by piece to their final resting spot, at which point a team of builders and architects finishes assembling them efficiently. Though there are a number of benefits to constructing buildings offsite rather than onsite, one of the greatest benefits is the phenomenal return on investment associated with modular construction. In this guide, we'll show you the many cost savings associated with modular construction and showcase why you'll get a better return on investment with a modular building.
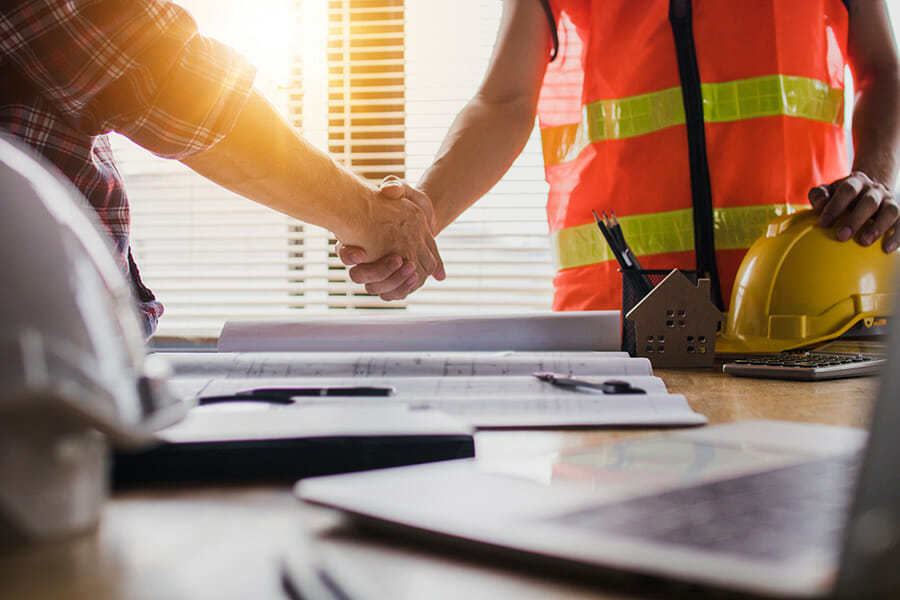
Faster Construction Times
If you've ever tried to build a custom building in the dead of winter or during hurricane season, you understand that the weather has a huge effect on how long it takes your building to be constructed. Inclement weather can cause traditionally constructed buildings to take months longer than anticipated.
Time is money, especially where construction is concerned. If you're creating a business, delays in construction equal delays in revenue. Hotel rooms can't be rented, hospital equipment can't be installed, and inventory can't be stocked until your building is completely constructed.
Modular buildings are significantly faster to build than traditionally crafted buildings. In fact, studies show that modular buildings take 25-50% less time to build than traditional buildings. Regardless of your situation, that saved time equals money in your pocket.
Cost Certainty
Unlike with on-site construction, off-site construction designers and architects are required to finalize their plans before they start working on your building. Changing plans is difficult once construction begins because there are so many moving parts involved. Additionally, once you've signed off on a project, the rates are set. This means no weather-related price hikes and no paying for laborers to undo or redo work. You know from the moment you sign your contract exactly what the cost will be for your business.
Fewer On-the-Job Injuries
There are a number of factors that can lead to on-the-job injuries with traditional construction. Working to a deadline despite poor weather conditions, for example, can cause workers to slip and injure themselves. On-the-job injuries can be cause for lawsuits or sudden unexpected expenses on your bill as a result of the construction company trying to recuperate their costs. Modular buildings are built in factories with stringent safety requirements during predictable business hours. This reduces the chances of on-the-job injuries and any related costs.
Reduced Waste
Traditionally constructed buildings suffer from construction waste as a result of human error. Builders might cut planks to the wrong length, for example, and have to cut them again, or it might rain when they weren't expecting it to, ruining building materials. When a building is built in a factory, a lot of this waste is eliminated. Environmental factors are a non-issue with offsite construction, and the industrialization process leads to fewer errors.
Additionally, factories are able to order materials in bulk for many orders at a time rather than just purchasing materials for your building. This means that the cost per unit of the material may be lower and they don't waste as much material on individual projects.
Conclusion
When you're creating your business, you want predictable costs so that you can plan your budget appropriately. Modular buildings build that predictability in at the beginning of the project rather than making you estimate total costs. Additionally, prefab structures allow you to have your building constructed sooner than on-site construction projects. This can provide a significant return on investment because you can open your business's doors sooner and begin making profits earlier.
More from Modular Advantage
Oregon’s Prevailing Wage Proposal: A Wake-Up Call for Modular Construction
In early February, 2024, the Massachusetts Board of Building Regulations and Standards (BBRS) released its proposed 10th Edition building codes. This draft included several amendments targeting modular construction that would have created an extremely difficult environment for the entire modular industry and could have eliminated the industry entirely in the state.
Behind the Design of Bethany Senior Terraces, NYC’s First Modular Passive House Senior Housing Project
As more developers seek to meet new regulations for energy efficiency, the team at Murray Engineering has set a new record. With the Bethany Senior Terraces project, Murray Engineering has helped to develop NYC’s first modular structure that fully encompasses passive house principles — introducing a new era of energy efficiency in the energy-conscious city that never sleeps.
How LAMOD is Using Modular to Address Inefficiency, Sustainability, and the Future of Construction
As developers, designers, and contractors seek to understand the evolving needs of the modular industry, no one is as well-versed in the benefits of going modular as Mārcis Kreičmanis. As the co-founder and CBDO of LAMOD in Riga, Latvia, Mārcis has made it his ultimate goal to address the inefficiencies of traditional construction.
From Furniture Builder to ‘Activist Architect’: Stuart Emmons’ Unique Journey
Stuart Emmons was fascinated by buildings at a young age. He remembers building sand cities with his brother during trips to the Jersey shore. His father gave him his first drawing table at the age of ten. Today, he is an experienced architect who received his FAIA in June 2025. The road he took is unique, to say the least.
Forge Craft Architecture + Design: Codes, Contracts, and Intellectual Property
Founding Principal and Director of Modular Practice for Forge Craft Architecture + Design, Rommel Sulit, discusses the implications of codes, contracts, and intellectual property on
modular construction.
Eisa Lee, the “Bilingual” Architect
Now as the founder of XL
Architecture and Modular Design in Ontario, Canada, she applies not just her education as a traditional architect but an entire holistic view on modular design. It’s this expansive view that guides her work on being a true partner that bridges the gap between architects and modular factories as they collaborate on the design process.
Tamarack Grove Engineering: Designing for the Modular Sector
The role of a structural engineer is crucial to the success of a modular project, from initial analysis to construction administration. Tamarack Grove offers structural engineering services — project analysis, plan creation, design creation, and construction administration — for commercial, manufacturing, facilities, public services, and modular. Modular is only one market sector the company serves but it is an increasingly popular one.
Engineer Masters the Art of Listening to His Customers
Since founding Modular Structural Consultants, LLC. in 2014, Yurianto has established a steady following of modular and container-based construction clients, primarily manufacturers. His services often include providing engineering calculations, reviewing drawings, and engineering certification
Inside College Road: Engineering the Modules of One of the World’s Tallest Modular Buildings
College Road is a groundbreaking modular residential development in East Croydon, South London by offsite developer and contractor, Tide, its modular company Vision Volumetric (VV), and engineered by MJH Structural Engineers.
Design for Flow: The Overlooked Power of DfMA in Modular Construction
Unlocking higher throughput, lower costs, and fewer redesigns by aligning Lean production flow with design for manufacturing and assembly.