Maximizing Modular Fabrication
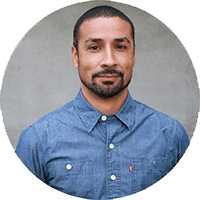
About the Author: Nick Gomez of Lowney Architecture has more than 15 years of experience working on multi-family housing and modular projects for nonprofit and for-profit clients. As the Oakland, Calif.-based firm’s Multi-family Studio Director, Nick has managed award-winning projects from design development through construction administration.
An increasing number of projects across different markets use modular construction. The modular building approach allows projects to capture the efficiencies gained by integrating design, manufacturing, and construction technologies without compromising aesthetic intent. When working toward a successful modular project, it is ideal to have experienced architecture, engineering, and contractor team members.
Projects using off-site modular construction must comply with the same building codes as conventional on-site construction. However, many states require separate permitting for the off-site factory and the on-site work. This process involves coordination between the architecture, engineering team, and factory.
Respect The Timelines And Deliverables
Modular buildings are similar to traditional on-site buildings in appearance and performance. One significant advantage of modular buildings is the shortened timeline, which delivers cost savings. This is because the modular pieces are constructed in a climate-controlled factory, which removes the possibility of weather-related delays.
This protected working environment increases efficiency allowing the structure to be built faster and cost less. Also, having a separate workspace from the building site allows for concurrent building. While the site foundation or podium is being constructed, the building components are simultaneously built at the off-site factory.
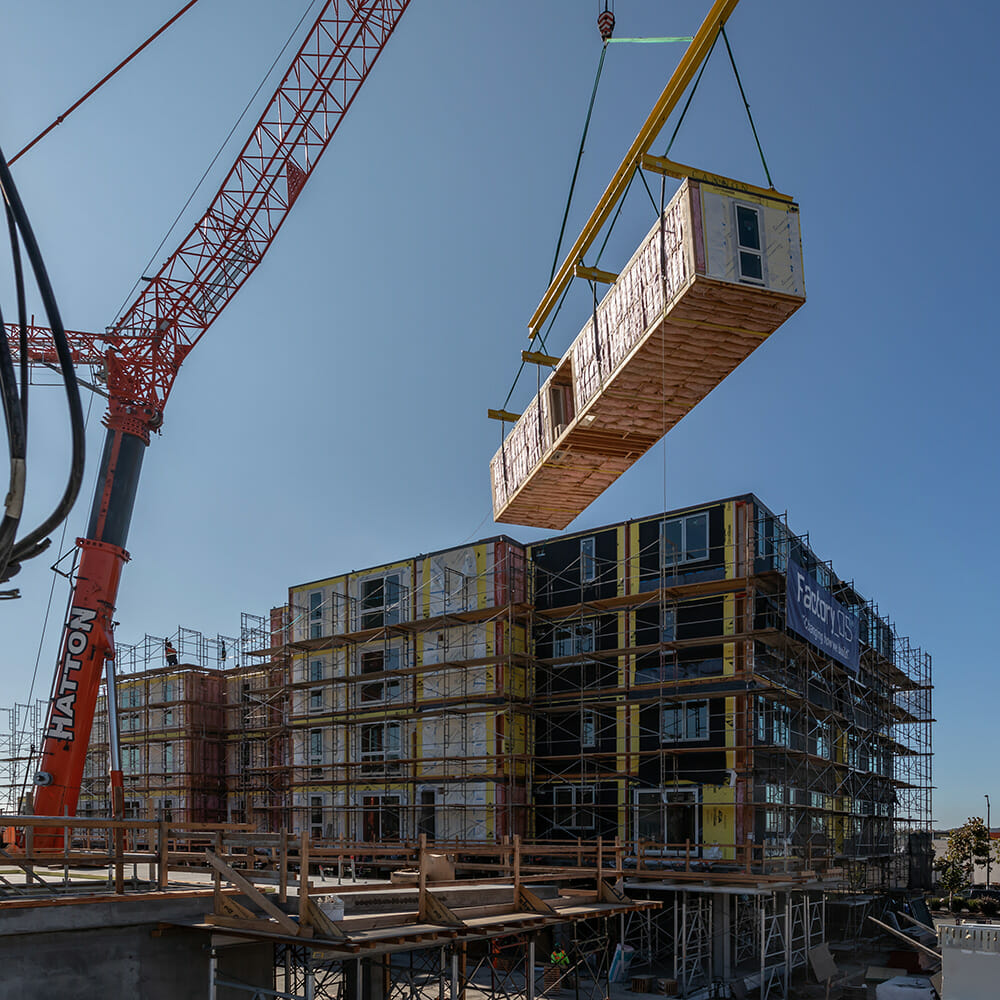
It is essential to establish a design freeze using a modular construction approach because of the factory production schedule and process. Design changes late in the process can be costly and require permit drawings modification and impact factory shop drawings. Unlike traditional construction processes, up-front decision-making and design freezes are critical for the modular construction processes, leaving little time in the schedule for alterations.
The modular prototype phase allows the owner, architect, and factory to set the basis of the design for production. This happens ahead of full production and enables the team to review, approve the design, and make small minor modifications to finish details and materials before the start of procurement and full production. With the fast pace of factory production, the design team is not often capable of reviewing every module. It relies on the contractor or third-party reviewer to inspect, so having the approved prototype is critical as a basis to review mods while in production.
Parameters
When designing a modular building, architects should address not just the design of a structure and its constitutive components; they should also be intentional about the process by which these are fabricated, transported, and connected. The design of individual modules may be affected by the manufacturing standards and assembly process of a particular facility. At the same time, the parameters of the design will dictate the ideal execution of those processes. For example, designers must look at the size of individual unit types and modules and how those sizes can be optimized across multiple unit and module types to increase production efficiencies.
When designing for modular construction, the project team should shift perspective to the building as a connected component system. This can help open more modularization possibilities, leading to a more iterative and less linear design process. The modularity concept should ideally be embedded in and inform all phases of a project, not just the construction phase and lead to a more collaborative design and delivery method.
Warranty And Liability
When implementing modular construction, project teams will consider some unique issues related to financing and liability. For example, factories want a warranty to start when production is complete and not building assembly. It always becomes a negotiating point with the contractor and owner.
Most vertical construction takes place off-site, which shifts the typical construction project balance based on the expected percentage of labor versus material. Modular construction also involves particular risks that need to be considered and insured against.
Understanding The Timeline For Deliverables
As outlined, modular construction is a primary benefit because it allows for building components to be constructed simultaneously that site work is being completed. Once the fabrication of the modules and site operations begin, the contractor should maintain regular communication with the modular manufacturer to ensure the schedule is maintained. According to the schedule, this early communication will ensure that the parallel processes are closely coordinated and proceed in step with each other.
Suppose the team respects the early decision making and design freezes set by the factory schedule. In that case, all of these factors are understood and met, depending on the project’s complexity. In that case, the team should see a construction schedule reduction of 20-40 percent.
More from Modular Advantage
Oregon’s Prevailing Wage Proposal: A Wake-Up Call for Modular Construction
In early February, 2024, the Massachusetts Board of Building Regulations and Standards (BBRS) released its proposed 10th Edition building codes. This draft included several amendments targeting modular construction that would have created an extremely difficult environment for the entire modular industry and could have eliminated the industry entirely in the state.
Behind the Design of Bethany Senior Terraces, NYC’s First Modular Passive House Senior Housing Project
As more developers seek to meet new regulations for energy efficiency, the team at Murray Engineering has set a new record. With the Bethany Senior Terraces project, Murray Engineering has helped to develop NYC’s first modular structure that fully encompasses passive house principles — introducing a new era of energy efficiency in the energy-conscious city that never sleeps.
How LAMOD is Using Modular to Address Inefficiency, Sustainability, and the Future of Construction
As developers, designers, and contractors seek to understand the evolving needs of the modular industry, no one is as well-versed in the benefits of going modular as Mārcis Kreičmanis. As the co-founder and CBDO of LAMOD in Riga, Latvia, Mārcis has made it his ultimate goal to address the inefficiencies of traditional construction.
From Furniture Builder to ‘Activist Architect’: Stuart Emmons’ Unique Journey
Stuart Emmons was fascinated by buildings at a young age. He remembers building sand cities with his brother during trips to the Jersey shore. His father gave him his first drawing table at the age of ten. Today, he is an experienced architect who received his FAIA in June 2025. The road he took is unique, to say the least.
Forge Craft Architecture + Design: Codes, Contracts, and Intellectual Property
Founding Principal and Director of Modular Practice for Forge Craft Architecture + Design, Rommel Sulit, discusses the implications of codes, contracts, and intellectual property on
modular construction.
Eisa Lee, the “Bilingual” Architect
Now as the founder of XL
Architecture and Modular Design in Ontario, Canada, she applies not just her education as a traditional architect but an entire holistic view on modular design. It’s this expansive view that guides her work on being a true partner that bridges the gap between architects and modular factories as they collaborate on the design process.
Tamarack Grove Engineering: Designing for the Modular Sector
The role of a structural engineer is crucial to the success of a modular project, from initial analysis to construction administration. Tamarack Grove offers structural engineering services — project analysis, plan creation, design creation, and construction administration — for commercial, manufacturing, facilities, public services, and modular. Modular is only one market sector the company serves but it is an increasingly popular one.
Engineer Masters the Art of Listening to His Customers
Since founding Modular Structural Consultants, LLC. in 2014, Yurianto has established a steady following of modular and container-based construction clients, primarily manufacturers. His services often include providing engineering calculations, reviewing drawings, and engineering certification
Inside College Road: Engineering the Modules of One of the World’s Tallest Modular Buildings
College Road is a groundbreaking modular residential development in East Croydon, South London by offsite developer and contractor, Tide, its modular company Vision Volumetric (VV), and engineered by MJH Structural Engineers.
Design for Flow: The Overlooked Power of DfMA in Modular Construction
Unlocking higher throughput, lower costs, and fewer redesigns by aligning Lean production flow with design for manufacturing and assembly.