Rise Modular: On the Rise in the Upper Midwest
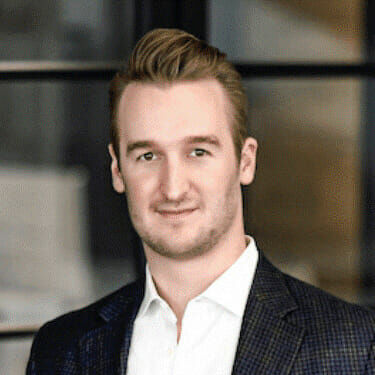
Christian Lawrence graduated from Yale with an Economics degree, and then worked in the financial industry for several years. He is the Founder and Chief Executive Officer of the modular construction start-up, Rise Modular, LLC. The company was founded in 2018 and is based in Minnesota, USA.
First in the Market
Although there are modular builders in the Upper Midwest building single family homes, Rise Modular is the first large scale, commercial modular manufacturer in the region. (For readers outside the United States: Roughly, the Upper Midwest consists of the states North Dakota, South Dakota, Minnesota, Iowa, Wisconsin, and Michigan.)
Rise Modular bought a 140,000+ square foot facility in October 2019 and invested millions of dollars to retrofit the building and install state-of-the-art, customized, manufacturing equipment. The factory opened in April 2020, and the company already has a number of firsts to its name — including the completion of Minneapolis’ first modular multi-family or commercial building. This is Mod42, an urban infill, market rate, 30-unit apartment building.
“A lot of developers want to be the second, rather than the first to undertake a commercial modular project. Completing this project is a big milestone for us,” says Lawrence. “Now there’s a successful project that our future customers can see and touch — not just renderings.”
The company’s now starting work on its second project — a 192-unit apartment building, which will be another first. It’ll be the first modular multi-family or commercial building ever built in Minnesota’s state capital, St. Paul.
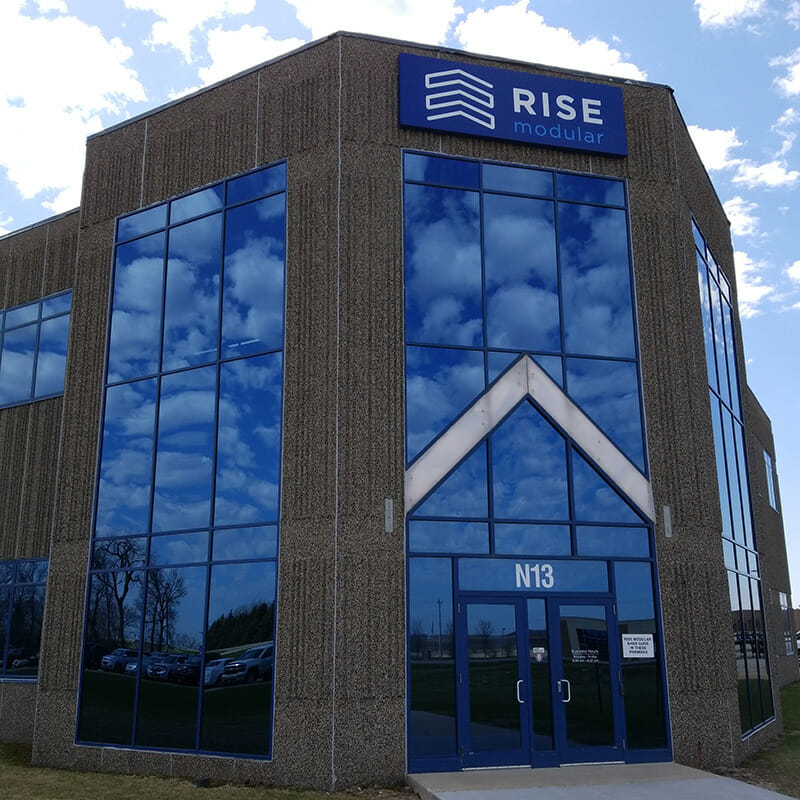
Embracing Challenges
Lawrence explains that the St. Paul site is very tight and oddly-shaped — challenges demanding design creativity. “The building is designed with the unusual architectural feature of triangular end cap units. We pride ourselves on using modular technology to help save cost and time for the developer, but without sacrificing design intent,” says Lawrence. “As well as being architecturally
interesting, net rentable square footage is maximized.”
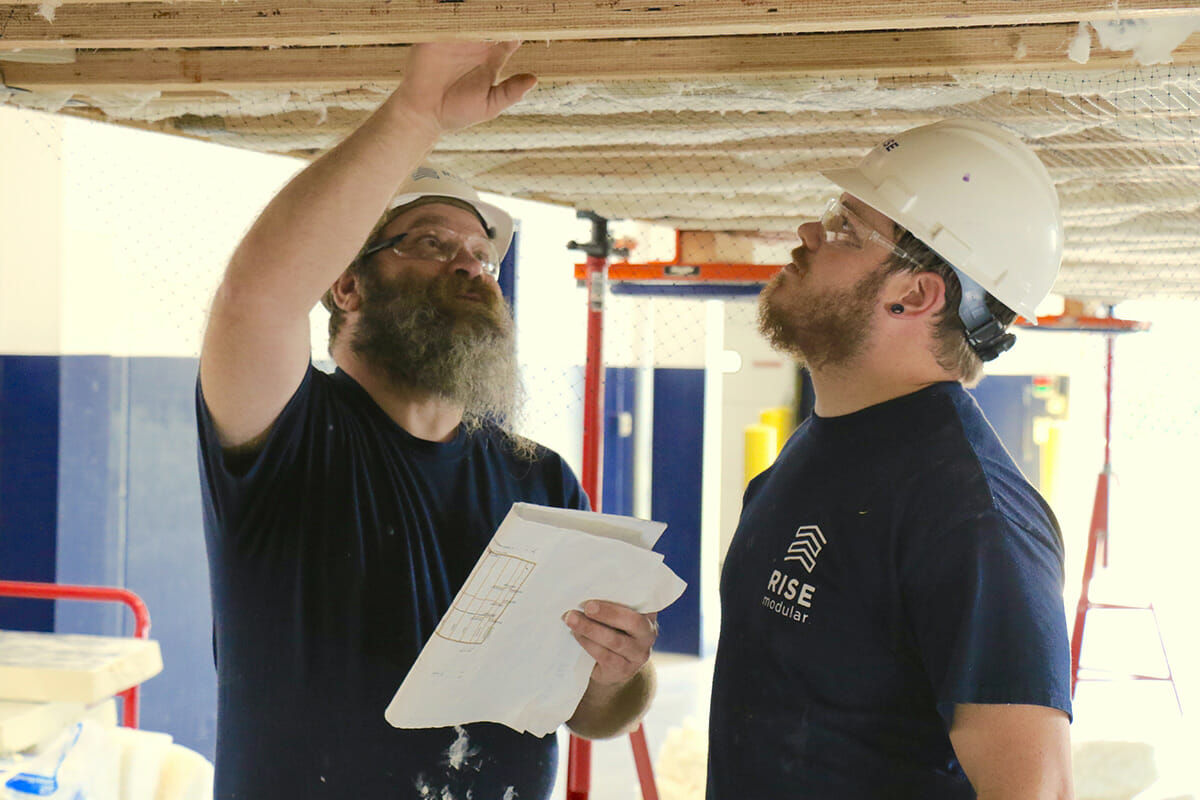
Lawrence explains it’s an innovative, five-over-two building, “probably one of the more architecturally-interesting modular apartment buildings ever built in this country. Certainly, it’s the first of its kind in the Upper Midwest, due to its size, shape, and architectural features.”
The project demonstrates the flexibility of modular design and construction. “Modular buildings can be so much more than perfectly stacked, uniform boxes,” says Lawrence.
“We want these buildings to be really beautiful and to contribute to the built environment.”
Modular and Market Research
Lawrence has always had a passion for real estate and design. After getting his economics degree, and working in the financial sector for a few years, he bought an acreage near his hometown of Minneapolis, Minnesota. His goal was to develop a multi-family apartment complex.
As he worked through the project details, Lawrence researched the viability of using modular construction. He reached out to modular manufacturers in the area, but none of them were set up to build that kind of project. They were builders of single-family homes and they “respectfully declined my apartment project”.
As Lawrence continued his research, touring more modular plants throughout the US, he became ever more convinced that the construction method was sound. “And, from a financial perspective, using a factory assembly line process — like we do for manufacturing so many other products — just makes sense.”
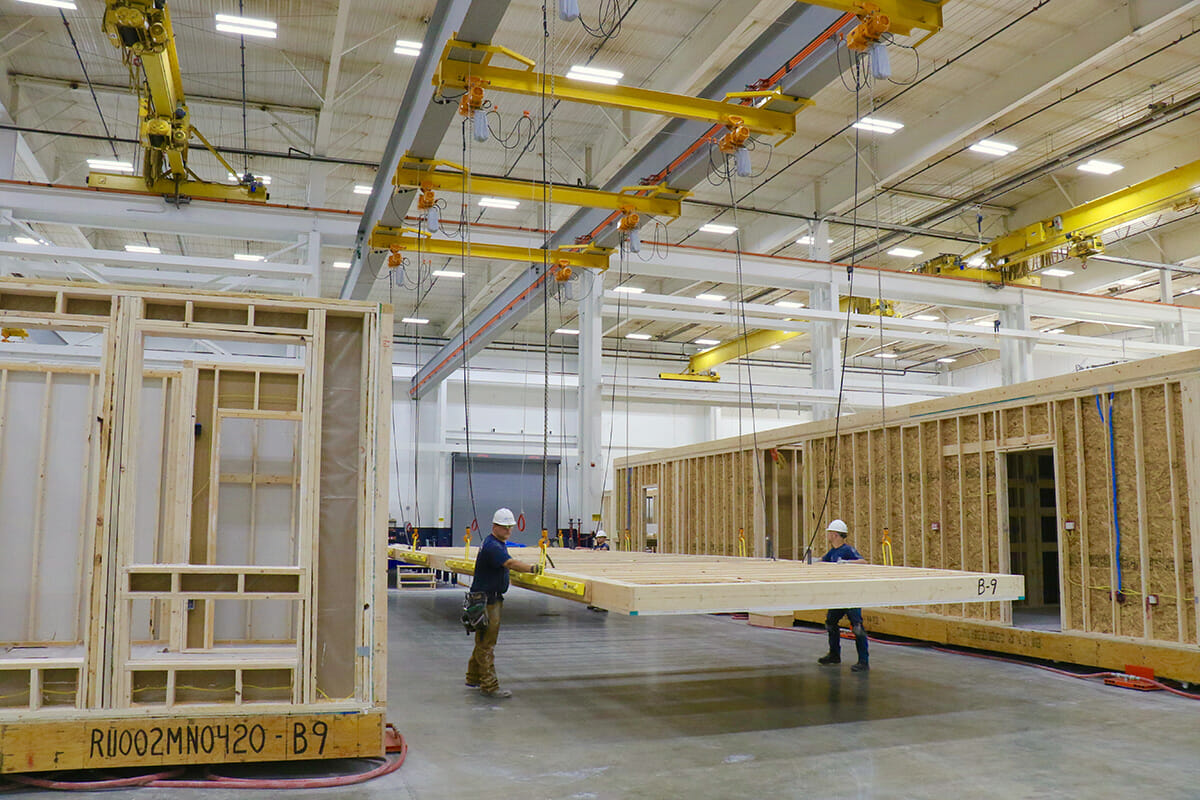
Related Listening:
The "Rise" of Modular Construction in the Upper Midwest w/ Rise Modular
In this episode of Inside Modular, Christian Lawrence, founder and CEO of RISE Modular in Minneapolis, talks about the creation of RISE, meeting demand in the Upper Midwest, the value of wood-based construction, modular construction's role in affordable housing, and the future of the industry.
While searching for a solution to the problems of rapidly increasing construction costs and shrinking labor availability, Lawrence learned that modular construction has been successfully used for decades and is increasing in popularity on the coasts of the United States.
“When I realized there was demand, but no supply, for large-scale modular buildings in the upper Midwest, I began focusing on starting my own modular construction company, rather than simply building a project.”
Market research has led the company to focus on low- to mid-rise, wood-framed, multi-family (apartments, condos, student housing, and senior living) and hospitality modular manufacturing and construction — the sectors the company anticipates will generate the most robust demand.
Lawrence discovered that within 750 miles of his Minnesota location, 85% of all modular units delivered for hospitality and multi-family were wood and that whether modular, panel-built, or stick-built, regulations limit wood construction to five stories over two stories of Type I podium.
“Unlike places like New York City or Boston or Chicago, there isn’t great demand for high-rise buildings that require steel framed construction, which is more expensive than wood,” explains Lawrence. “Low- to mid-rise, wood-based construction dominates the multi-family and hospitality sectors in the Upper Midwest.”
The Future
For the time being, Lawrence says the company is focused on treating its clients well, and building successful projects. “We want our clients to become long-term partners that build projects with us every year — not just customers.”
And the near future is looking very bright. “We have 20 to 25 projects, representing over 3000 units, that are in various stages of feasibility analysis and pre-construction. We’re very excited about the short- to medium-term pipeline.”
Longer term, Lawrence says he’d like the company to expand geographically into regions of the US that either don’t have a modular supplier, or are under-supplied.
“Rise Modular wants to help grow the broader industry. This construction methodology makes a lot of sense and it can help address the affordable housing crisis in this country,” says Lawrence. “We’d like to play a role in helping to increase the housing supply, both market rate and affordable.”
About the Author: Zena Ryder is a freelance writer, specializing in writing about construction and for construction companies. You can find her at Zena, Freelance Writer or on LinkedIn.
More from Modular Advantage
Oregon’s Prevailing Wage Proposal: A Wake-Up Call for Modular Construction
In early February, 2024, the Massachusetts Board of Building Regulations and Standards (BBRS) released its proposed 10th Edition building codes. This draft included several amendments targeting modular construction that would have created an extremely difficult environment for the entire modular industry and could have eliminated the industry entirely in the state.
Behind the Design of Bethany Senior Terraces, NYC’s First Modular Passive House Senior Housing Project
As more developers seek to meet new regulations for energy efficiency, the team at Murray Engineering has set a new record. With the Bethany Senior Terraces project, Murray Engineering has helped to develop NYC’s first modular structure that fully encompasses passive house principles — introducing a new era of energy efficiency in the energy-conscious city that never sleeps.
How LAMOD is Using Modular to Address Inefficiency, Sustainability, and the Future of Construction
As developers, designers, and contractors seek to understand the evolving needs of the modular industry, no one is as well-versed in the benefits of going modular as Mārcis Kreičmanis. As the co-founder and CBDO of LAMOD in Riga, Latvia, Mārcis has made it his ultimate goal to address the inefficiencies of traditional construction.
From Furniture Builder to ‘Activist Architect’: Stuart Emmons’ Unique Journey
Stuart Emmons was fascinated by buildings at a young age. He remembers building sand cities with his brother during trips to the Jersey shore. His father gave him his first drawing table at the age of ten. Today, he is an experienced architect who received his FAIA in June 2025. The road he took is unique, to say the least.
Forge Craft Architecture + Design: Codes, Contracts, and Intellectual Property
Founding Principal and Director of Modular Practice for Forge Craft Architecture + Design, Rommel Sulit, discusses the implications of codes, contracts, and intellectual property on
modular construction.
Eisa Lee, the “Bilingual” Architect
Now as the founder of XL
Architecture and Modular Design in Ontario, Canada, she applies not just her education as a traditional architect but an entire holistic view on modular design. It’s this expansive view that guides her work on being a true partner that bridges the gap between architects and modular factories as they collaborate on the design process.
Tamarack Grove Engineering: Designing for the Modular Sector
The role of a structural engineer is crucial to the success of a modular project, from initial analysis to construction administration. Tamarack Grove offers structural engineering services — project analysis, plan creation, design creation, and construction administration — for commercial, manufacturing, facilities, public services, and modular. Modular is only one market sector the company serves but it is an increasingly popular one.
Engineer Masters the Art of Listening to His Customers
Since founding Modular Structural Consultants, LLC. in 2014, Yurianto has established a steady following of modular and container-based construction clients, primarily manufacturers. His services often include providing engineering calculations, reviewing drawings, and engineering certification
Inside College Road: Engineering the Modules of One of the World’s Tallest Modular Buildings
College Road is a groundbreaking modular residential development in East Croydon, South London by offsite developer and contractor, Tide, its modular company Vision Volumetric (VV), and engineered by MJH Structural Engineers.
Design for Flow: The Overlooked Power of DfMA in Modular Construction
Unlocking higher throughput, lower costs, and fewer redesigns by aligning Lean production flow with design for manufacturing and assembly.