Poland's iQ Module is Expanding What's Possible with Modular Construction
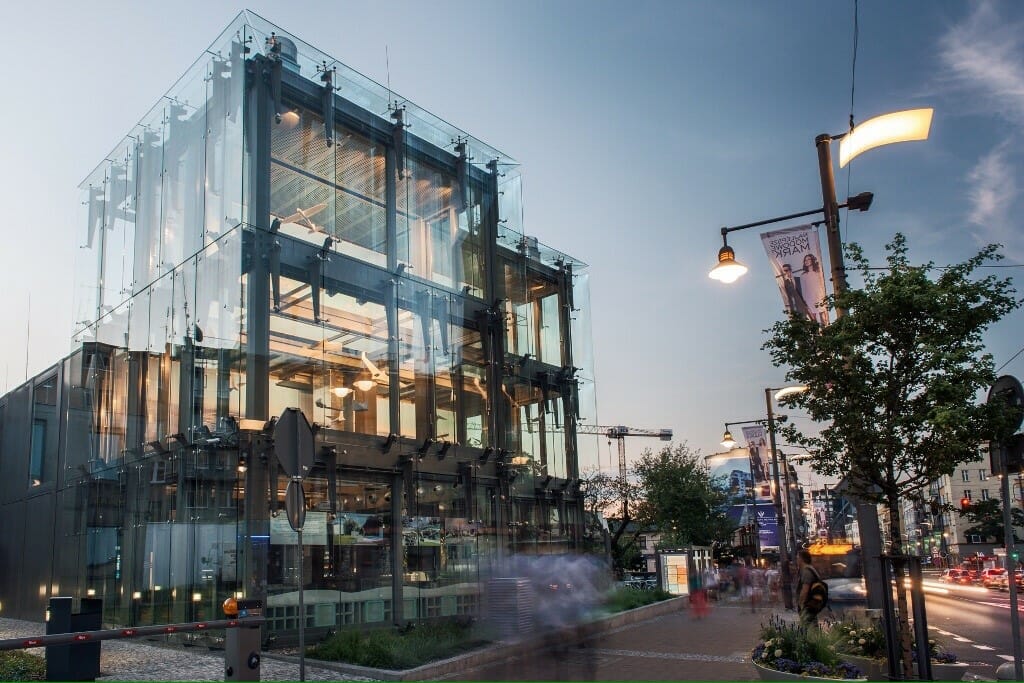
Located in Gdynia, Poland, the InfoBox—built by iQ Module— is Gdynia InfoBox is a center for information about urban developments and projects being implemented in the city. It also serves as a tourist attraction and features a 22-meter lookout tower.
The modular industry is expanding globally with considerable growth in Europe. iQ Module, headquartered in Gdansk, Poland, has contributed to that industry growth. MBI caught up with iQ Module co-founder Krzysztof Droszcz and talked to him about what iQ Module is doing and how the modular industry is growing in Europe.
MBI: What notable projects are you currently/have you recently worked on that you’d like to share?
KD: There are a few but the most significant has been InfoBox in Gdynia, Poland. This building was raised on steel frame modules using mostly glass structure facades as walls. The building itself is a city tourist Info Center with conference space, two restaurants, a few modular galleries, and a viewing tower that overlooks the city and the sea. It’s situated in the Gdynia city center and has become an iconic, well-known building..
We were the designers as well as the builders of that magnificent structure. The building itself got a few national and international awards and distinctions.
Another notable project is a single house in Sopot, Poland. It received an award for the best project in Sopot in 2019. The house represents simplicity in architecture. The whole roof and facade are made from fiber cement boards decorated with subtle wood finishing, making that project interesting to see and touch.
MBI: How has COVID-19 affected your business this year? How have you had to adapt?
KD: That’s a question we are still answering. Everything has changed and we’ve had to adapt to the new order of the world. We have recently been preparing iQ for global market expansion and we have been concentrating on the US, UK, and Germany especially. We have developed some paths to the hotel and residential market. After the COVID-19 lockdown, we were forced to diversify our production targets and modify our products.
We have also been involved in creating quarantine and isolation units. We have to produce to keep the company rolling but we’re also trying to get involved in stopping the pandemic as that’s in all of our interest to take it down. It’s a hard time but we try to use it most effectively.
MBI: What’s been the biggest benefit of being an MBI member?
We were looking for a wider view on the modular market and possibilities. Entering the US market as a member of MBI gives us much more contact with fellow modular producers, designers, and specialists so we can get involved in the global modular market. Another great thing about membership is getting to meet industry pioneers, experienced investors, and architects with whom we are happy to work. As we expand outside of Europe, we’re seeking to be a part of a global modular family. Being an MBI member is proving to be a great value for us.
MBI: Have you noticed the industry change since you became part of it? How so?
KD: Since the COVID-19 pandemic hit, the changes have been significant. We’ve seen how members of MBI have been developing new ideas to keep the industry well. The situation we are all affected by is also a time of opportunity. The trick is to use wisdom and convince more stakeholders to trust modular technology.
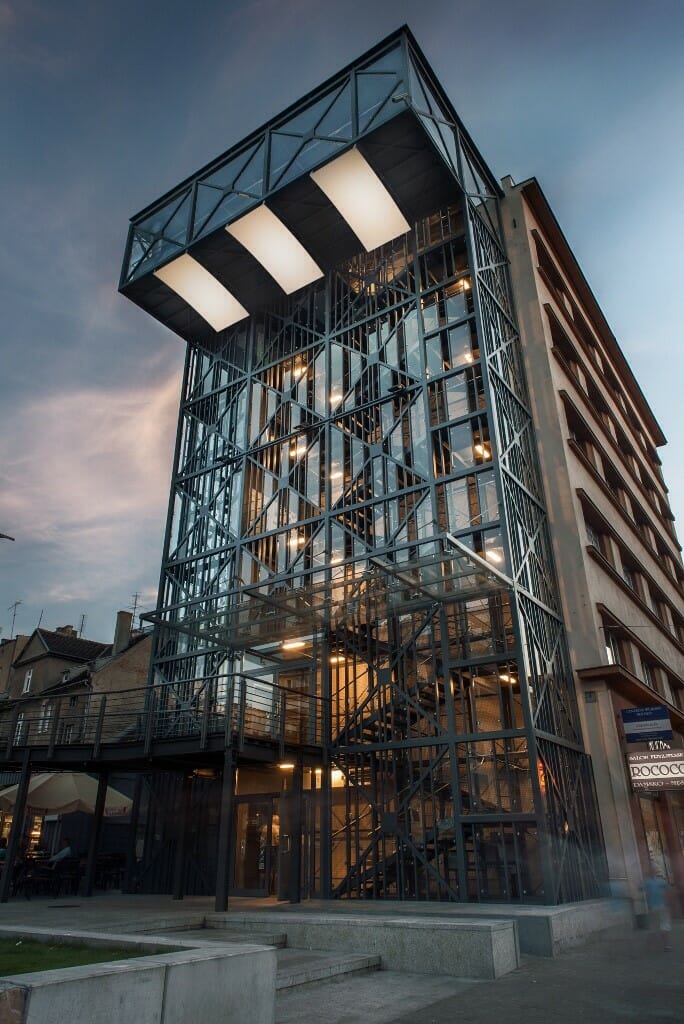
MBI: How would you describe the modular construction industry in Europe overall?
KD: There is tremendous potential for modular construction in Europe. On the one hand, there is a lot of tradition on our continent, but on the other hand, there is a huge need for new technologies.
For example, one of the most interesting markets we have experienced is in Scandinavia. Our wood modules fit in that environment perfectly and it’s eco-friendly. Norway and Sweden have a long history of building modules and wood structure buildings. That market is still developing. Steel structure modules are not as popular yet but they’re almost a necessity to use for higher structures. The market is beginning to realize that modular technology is a solution yet there is still a lot to do to encourage clients to think modular.
More from Modular Advantage
Oregon’s Prevailing Wage Proposal: A Wake-Up Call for Modular Construction
In early February, 2024, the Massachusetts Board of Building Regulations and Standards (BBRS) released its proposed 10th Edition building codes. This draft included several amendments targeting modular construction that would have created an extremely difficult environment for the entire modular industry and could have eliminated the industry entirely in the state.
Behind the Design of Bethany Senior Terraces, NYC’s First Modular Passive House Senior Housing Project
As more developers seek to meet new regulations for energy efficiency, the team at Murray Engineering has set a new record. With the Bethany Senior Terraces project, Murray Engineering has helped to develop NYC’s first modular structure that fully encompasses passive house principles — introducing a new era of energy efficiency in the energy-conscious city that never sleeps.
How LAMOD is Using Modular to Address Inefficiency, Sustainability, and the Future of Construction
As developers, designers, and contractors seek to understand the evolving needs of the modular industry, no one is as well-versed in the benefits of going modular as Mārcis Kreičmanis. As the co-founder and CBDO of LAMOD in Riga, Latvia, Mārcis has made it his ultimate goal to address the inefficiencies of traditional construction.
From Furniture Builder to ‘Activist Architect’: Stuart Emmons’ Unique Journey
Stuart Emmons was fascinated by buildings at a young age. He remembers building sand cities with his brother during trips to the Jersey shore. His father gave him his first drawing table at the age of ten. Today, he is an experienced architect who received his FAIA in June 2025. The road he took is unique, to say the least.
Forge Craft Architecture + Design: Codes, Contracts, and Intellectual Property
Founding Principal and Director of Modular Practice for Forge Craft Architecture + Design, Rommel Sulit, discusses the implications of codes, contracts, and intellectual property on
modular construction.
Eisa Lee, the “Bilingual” Architect
Now as the founder of XL
Architecture and Modular Design in Ontario, Canada, she applies not just her education as a traditional architect but an entire holistic view on modular design. It’s this expansive view that guides her work on being a true partner that bridges the gap between architects and modular factories as they collaborate on the design process.
Tamarack Grove Engineering: Designing for the Modular Sector
The role of a structural engineer is crucial to the success of a modular project, from initial analysis to construction administration. Tamarack Grove offers structural engineering services — project analysis, plan creation, design creation, and construction administration — for commercial, manufacturing, facilities, public services, and modular. Modular is only one market sector the company serves but it is an increasingly popular one.
Engineer Masters the Art of Listening to His Customers
Since founding Modular Structural Consultants, LLC. in 2014, Yurianto has established a steady following of modular and container-based construction clients, primarily manufacturers. His services often include providing engineering calculations, reviewing drawings, and engineering certification
Inside College Road: Engineering the Modules of One of the World’s Tallest Modular Buildings
College Road is a groundbreaking modular residential development in East Croydon, South London by offsite developer and contractor, Tide, its modular company Vision Volumetric (VV), and engineered by MJH Structural Engineers.
Design for Flow: The Overlooked Power of DfMA in Modular Construction
Unlocking higher throughput, lower costs, and fewer redesigns by aligning Lean production flow with design for manufacturing and assembly.