Tiny Cabins Offer Minimalist Getaways
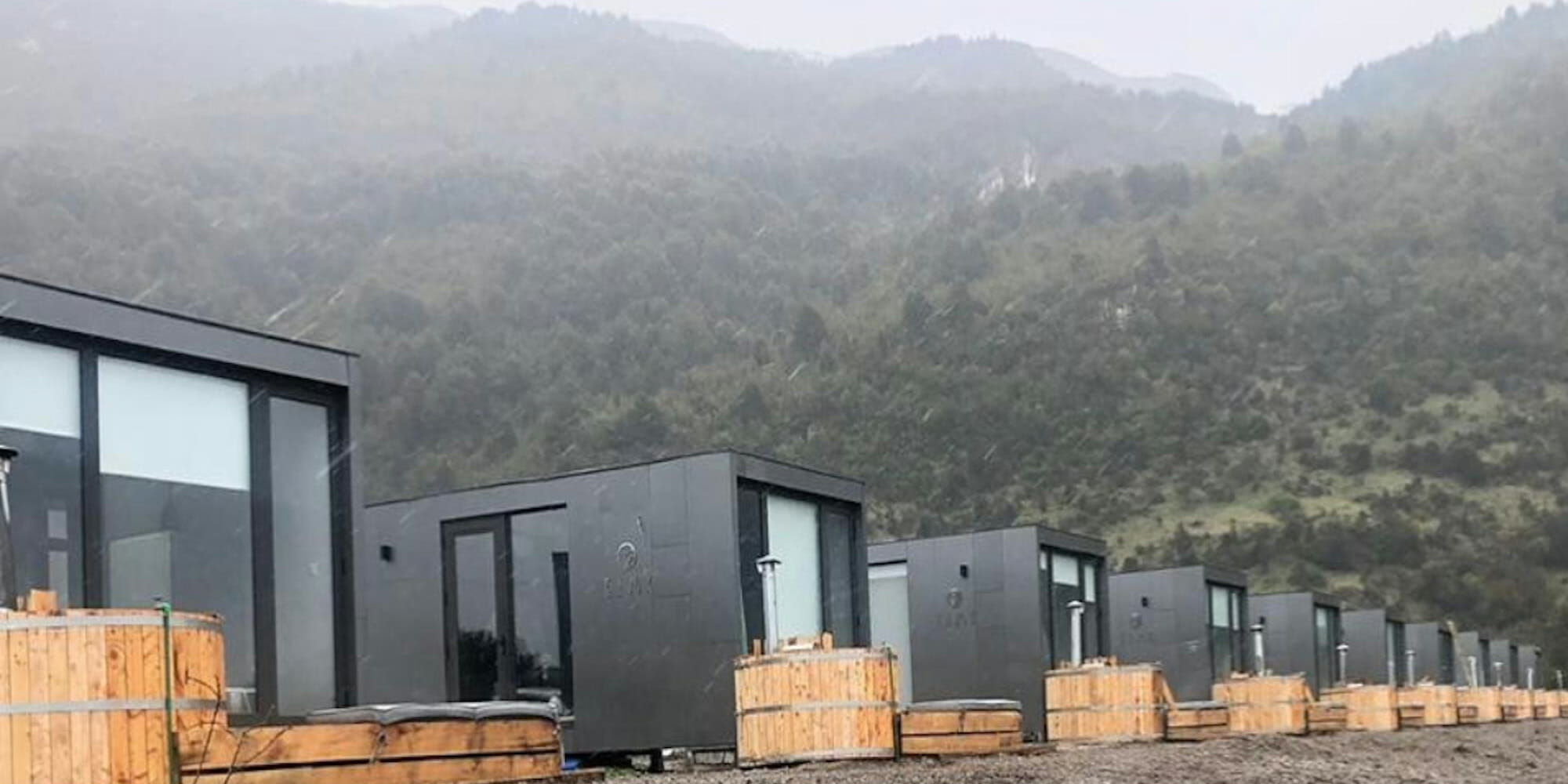
The concept of Tiny Homes is widespread in the United States, given its size and mobility advantages. This has generated a tendency to live with the essentials and at lower costs than maintaining large homes. The popularity of Tiny Homes isn’t confined to the United States, however.
MBI member Tecno Fast S.A. utilized this principle for the creation of their “Tiny Cabin by Tecno Fast” in Chile, South America. Technically the Tiny Cabin is a house with approximately 80 square meters of surface, with an efficient, minimalist, and high-quality design. Each cabin has a bedroom, kitchen, bathroom, closet, and additional services such as an electric lock and alarm.
The plans come in two modern designs from renowned Chilean architects Mathias Klotz and Felipe Assadi. Conceptually, the Tiny Cabin designed by Mathias Klotz is designed to share and enjoy with the family, with a living room that connects with a natural environment. Felipe Assadi’s creation is a space that prioritizes resting with a privileged view from the bedroom. The purpose is to create a minimalist and sustainable space.
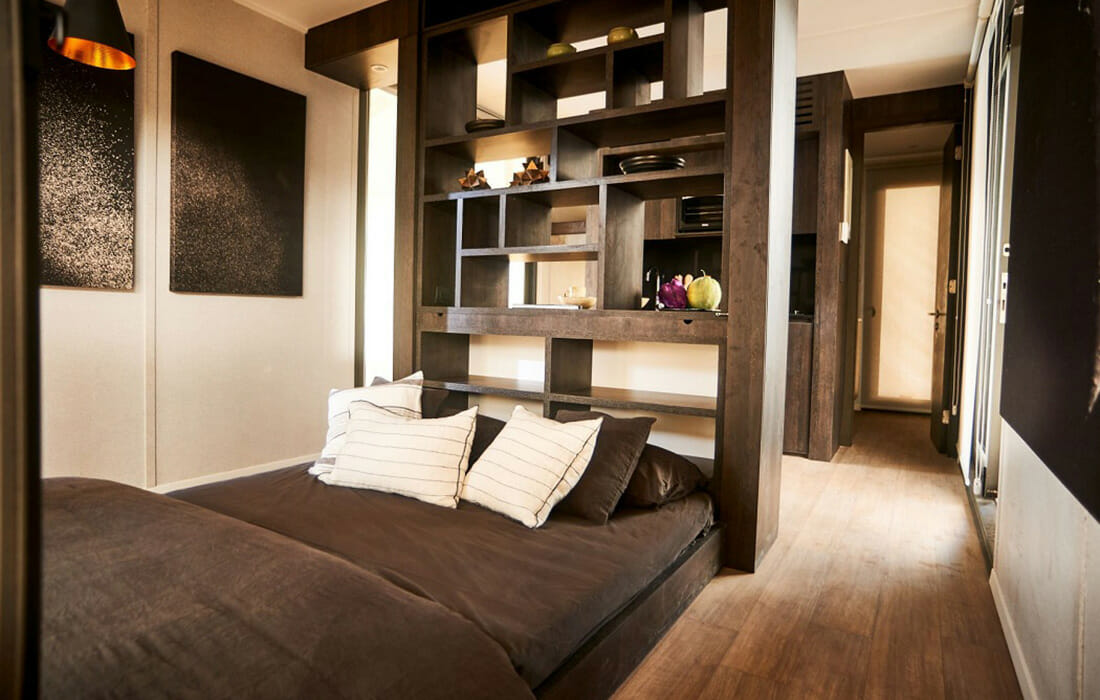
The Tiny Cabins are prefabricated transportable steel structure modules and can be arranged adjacently to generate a single-family home. The modules have the following exterior measurements: width of 3.44 m; length of 6.94 m; height of 2.80 m, and dimensional tolerances of +/- 1cm.
The partitions and walls consist of plasterboard, glass wool and OSB. This ensures excellent acoustic measures, protection against fire and, above all, temperature, providing a module manufactured and designed for harsh weather conditions. The exterior cladding consists of a panel made of 2 aluminum sheets and a plastic core, giving it a modern and minimalist look. The roof is covered in liquid membrane, making it difficult to reach complicated and complex places such as the 2-channel canals, providing maximum impermeability. The windows, thermo panel with aluminum frames, provide a good seal to the outside while maintaining the indoor temperature, either cold or hot.
Tecno Fast launched this program in the Spring of 2019 by calling on those who have land in areas with high tourism potential. The methodology was based on registering on the company’s website www.tinycabin.cl, completing the application form and submitting a series of documents. Tecno Fast received over 1,000 applications from all over our country, from the most extreme zone to the most deserted area. The company selected the 50 best project locations and have installed Tiny Cabins throughout Chile including 10 located 1,897 km from the Tecno Fast factory, on the shore of General Carrera Lake in Chilean Patagonia.
This article was adapted from an Awards of Distinction entry. Browse more projects.
More from Modular Advantage
Oregon’s Prevailing Wage Proposal: A Wake-Up Call for Modular Construction
In early February, 2024, the Massachusetts Board of Building Regulations and Standards (BBRS) released its proposed 10th Edition building codes. This draft included several amendments targeting modular construction that would have created an extremely difficult environment for the entire modular industry and could have eliminated the industry entirely in the state.
Behind the Design of Bethany Senior Terraces, NYC’s First Modular Passive House Senior Housing Project
As more developers seek to meet new regulations for energy efficiency, the team at Murray Engineering has set a new record. With the Bethany Senior Terraces project, Murray Engineering has helped to develop NYC’s first modular structure that fully encompasses passive house principles — introducing a new era of energy efficiency in the energy-conscious city that never sleeps.
How LAMOD is Using Modular to Address Inefficiency, Sustainability, and the Future of Construction
As developers, designers, and contractors seek to understand the evolving needs of the modular industry, no one is as well-versed in the benefits of going modular as Mārcis Kreičmanis. As the co-founder and CBDO of LAMOD in Riga, Latvia, Mārcis has made it his ultimate goal to address the inefficiencies of traditional construction.
From Furniture Builder to ‘Activist Architect’: Stuart Emmons’ Unique Journey
Stuart Emmons was fascinated by buildings at a young age. He remembers building sand cities with his brother during trips to the Jersey shore. His father gave him his first drawing table at the age of ten. Today, he is an experienced architect who received his FAIA in June 2025. The road he took is unique, to say the least.
Forge Craft Architecture + Design: Codes, Contracts, and Intellectual Property
Founding Principal and Director of Modular Practice for Forge Craft Architecture + Design, Rommel Sulit, discusses the implications of codes, contracts, and intellectual property on
modular construction.
Eisa Lee, the “Bilingual” Architect
Now as the founder of XL
Architecture and Modular Design in Ontario, Canada, she applies not just her education as a traditional architect but an entire holistic view on modular design. It’s this expansive view that guides her work on being a true partner that bridges the gap between architects and modular factories as they collaborate on the design process.
Tamarack Grove Engineering: Designing for the Modular Sector
The role of a structural engineer is crucial to the success of a modular project, from initial analysis to construction administration. Tamarack Grove offers structural engineering services — project analysis, plan creation, design creation, and construction administration — for commercial, manufacturing, facilities, public services, and modular. Modular is only one market sector the company serves but it is an increasingly popular one.
Engineer Masters the Art of Listening to His Customers
Since founding Modular Structural Consultants, LLC. in 2014, Yurianto has established a steady following of modular and container-based construction clients, primarily manufacturers. His services often include providing engineering calculations, reviewing drawings, and engineering certification
Inside College Road: Engineering the Modules of One of the World’s Tallest Modular Buildings
College Road is a groundbreaking modular residential development in East Croydon, South London by offsite developer and contractor, Tide, its modular company Vision Volumetric (VV), and engineered by MJH Structural Engineers.
Design for Flow: The Overlooked Power of DfMA in Modular Construction
Unlocking higher throughput, lower costs, and fewer redesigns by aligning Lean production flow with design for manufacturing and assembly.