Pushing the Boundaries of Perception
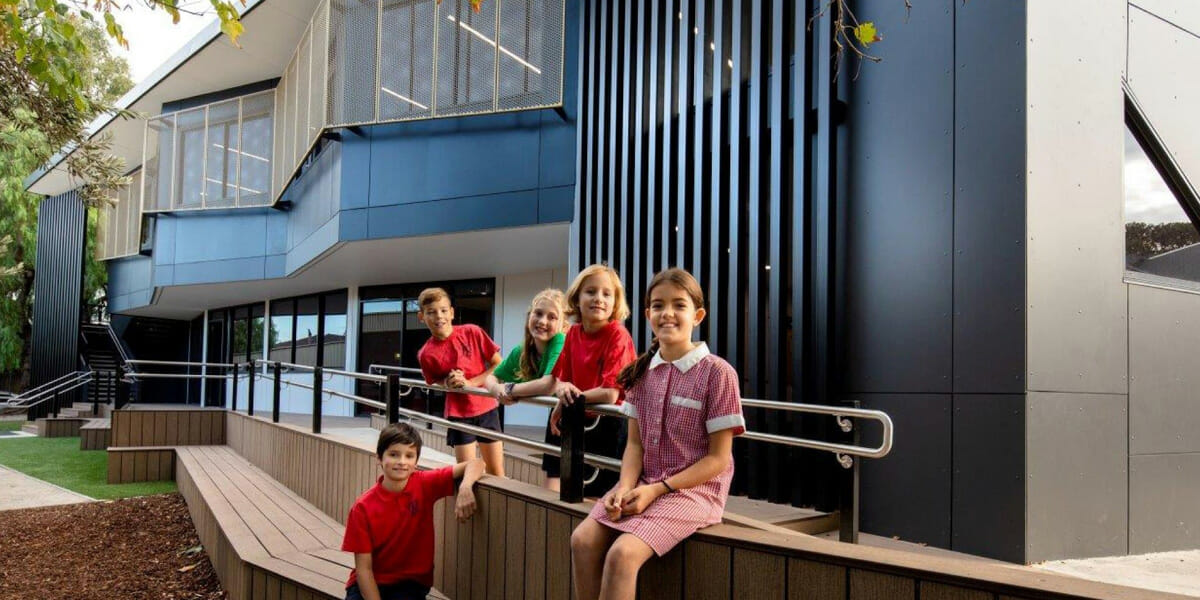
MBI member Fleetwood Building Solutions has pushed boundaries and challenged perceptions regarding modular construction. The Australian modular construction company recently constructed and delivered an architectural centerpiece for Fairfield Primary School in Melbourne, Australia. The dedicated Years 5 & 6 learning communities are housed in a contemporary 2-storey building that pushes the boundaries of perception around design for modular construction.
The building replaces an existing permanent facility that had reached the end of its life. The project delivered resilience through its design and maximized the value of the new building through a collaborative process. Structural and spatial solutions that enabled cost-effective refurbishment of the first-floor space allows this modular building to meet the changing future needs of a growing and vibrant school.
The building was constructed offsite in 16 modules (733 square meters), which were then separately transported to the site and installed. The project delivered extensive integrated outdoor spaces and decking areas to link learning areas with new social settings. This supports further learning opportunities!
The project not only maximized the established benefits of offsite construction: time, quality, and cost, it also explored further opportunities to leverage other industry best practices. This resulted in a “hybrid” approach to the precast lift core. The deliberate evaluation of construction and factory build tolerances ensured a seamless delivery and installation process.
The first floor of the building has been innovatively designed for both the current educational needs and a potential future use as a library and education resource center. The cost-effective refurbishment of the first floor extends the building’s useful life. This enhanced the project’s sustainability credentials beyond current best practice energy and operating cost control measures (e.g. the use of prefinished panel cladding which reduces ongoing school maintenance, eliminating the safety risks associated with working at heights during the project life.)
The project was procured through offsite construction because of the inability of traditional construction practices to deliver a cost-effective solution. Working with a significant government agency, Fleetwood Building Solutions validated prefabrication and modular construction with a pilot demonstration showcasing the high-quality design and built form outcomes that could be achieved. The adoption of a mass-customization strategy yielded a cost-effective manufacturing platform approach, tailored to the project brief.
The final project outcome is an architecture without compromise that delivers a high caliber spatial experience which is fit for purpose. Modular construction allows for the harnessing of supply chain efficiencies, the maximizing of local materials, and certainty and control over supply and material sources.
This project was completed in just 166 days and won First Place in MBI’s 2020 Awards of Distinction contest in the Education Under 10,000 Sq. Ft. category.
This article was adapted from an Awards of Distinction entry. Browse more projects.
More from Modular Advantage
Oregon’s Prevailing Wage Proposal: A Wake-Up Call for Modular Construction
In early February, 2024, the Massachusetts Board of Building Regulations and Standards (BBRS) released its proposed 10th Edition building codes. This draft included several amendments targeting modular construction that would have created an extremely difficult environment for the entire modular industry and could have eliminated the industry entirely in the state.
Behind the Design of Bethany Senior Terraces, NYC’s First Modular Passive House Senior Housing Project
As more developers seek to meet new regulations for energy efficiency, the team at Murray Engineering has set a new record. With the Bethany Senior Terraces project, Murray Engineering has helped to develop NYC’s first modular structure that fully encompasses passive house principles — introducing a new era of energy efficiency in the energy-conscious city that never sleeps.
How LAMOD is Using Modular to Address Inefficiency, Sustainability, and the Future of Construction
As developers, designers, and contractors seek to understand the evolving needs of the modular industry, no one is as well-versed in the benefits of going modular as Mārcis Kreičmanis. As the co-founder and CBDO of LAMOD in Riga, Latvia, Mārcis has made it his ultimate goal to address the inefficiencies of traditional construction.
From Furniture Builder to ‘Activist Architect’: Stuart Emmons’ Unique Journey
Stuart Emmons was fascinated by buildings at a young age. He remembers building sand cities with his brother during trips to the Jersey shore. His father gave him his first drawing table at the age of ten. Today, he is an experienced architect who received his FAIA in June 2025. The road he took is unique, to say the least.
Forge Craft Architecture + Design: Codes, Contracts, and Intellectual Property
Founding Principal and Director of Modular Practice for Forge Craft Architecture + Design, Rommel Sulit, discusses the implications of codes, contracts, and intellectual property on
modular construction.
Eisa Lee, the “Bilingual” Architect
Now as the founder of XL
Architecture and Modular Design in Ontario, Canada, she applies not just her education as a traditional architect but an entire holistic view on modular design. It’s this expansive view that guides her work on being a true partner that bridges the gap between architects and modular factories as they collaborate on the design process.
Tamarack Grove Engineering: Designing for the Modular Sector
The role of a structural engineer is crucial to the success of a modular project, from initial analysis to construction administration. Tamarack Grove offers structural engineering services — project analysis, plan creation, design creation, and construction administration — for commercial, manufacturing, facilities, public services, and modular. Modular is only one market sector the company serves but it is an increasingly popular one.
Engineer Masters the Art of Listening to His Customers
Since founding Modular Structural Consultants, LLC. in 2014, Yurianto has established a steady following of modular and container-based construction clients, primarily manufacturers. His services often include providing engineering calculations, reviewing drawings, and engineering certification
Inside College Road: Engineering the Modules of One of the World’s Tallest Modular Buildings
College Road is a groundbreaking modular residential development in East Croydon, South London by offsite developer and contractor, Tide, its modular company Vision Volumetric (VV), and engineered by MJH Structural Engineers.
Design for Flow: The Overlooked Power of DfMA in Modular Construction
Unlocking higher throughput, lower costs, and fewer redesigns by aligning Lean production flow with design for manufacturing and assembly.