Modular Media Residence
As the biggest steelmaker in Korea, MBI member POSCO played a crucial part in helping PyeongChang, Korea prepare for the 2018 Olympic games. The company constructed, delivered, and, installed the International Broadcast Center (IBC), Media Residence Hotel and the Kwandong Hockey Center with its World Premium Products and innovative construction solutions.
The media hotel is particularly noteworthy as 100 percent of the building was constructed off-site via modular construction. The 110,000 sf facility was constructed and opened in just 184 days! Compared to the time it would take to build a traditional concrete building of the same scope, the construction period for the Media Residence Hotel was 18 months shorter. Since each room is a relocatable building unit, it will be moved to a different venue and recycled as another hotel or dormitory.
The building consists of various units (room units, side exterior wall units, roof units, stair units and hall units). Modular room units (size 10.8ftx23ftx10.5ft) were designed with mobility and sustainability considerations. The unit exterior was designed to minimize the decorative elements and emphasize the aesthetic of natural material's characteristic to be functional. The lobby interior was designed as class and comfortable space with texture of steel itself and emotional design. Structure in ceiling of corridor was left exposed as an architecture design element. Performance and design were enhanced by adopting the unique texture of steel; high corrosion-proof steel instead of tile for high-grade unit bath system, fabric textured color-printed steel plate for system interior wall and clear color steel plate for the fire door. Free from potential nailing and taping scratches, artwork or photo frames can be posted on the wall magnetically.
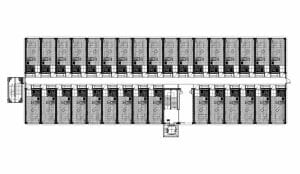
According to the International Forum World Design Guide: “Most buildings created for the Winter Olympic Games have ultimately become “white elephants”. To avoid this problem, the PyeongChang Winter Olympics media residence was designed using relocatable building (RB) units as the media residence during the Games. Afterwards, the buildings were dismantled, and the site was restored to its original condition. Best of all, the RB units will be relocated and reused. To achieve this, the building design followed a fourfold concept: relocatable; reusable; recyclable (steel-based design); and reduced (100% factory made).
This article was adapted from an Awards of Distinction entry. Browse more projects.
More from Modular Advantage
Oregon’s Prevailing Wage Proposal: A Wake-Up Call for Modular Construction
In early February, 2024, the Massachusetts Board of Building Regulations and Standards (BBRS) released its proposed 10th Edition building codes. This draft included several amendments targeting modular construction that would have created an extremely difficult environment for the entire modular industry and could have eliminated the industry entirely in the state.
Behind the Design of Bethany Senior Terraces, NYC’s First Modular Passive House Senior Housing Project
As more developers seek to meet new regulations for energy efficiency, the team at Murray Engineering has set a new record. With the Bethany Senior Terraces project, Murray Engineering has helped to develop NYC’s first modular structure that fully encompasses passive house principles — introducing a new era of energy efficiency in the energy-conscious city that never sleeps.
How LAMOD is Using Modular to Address Inefficiency, Sustainability, and the Future of Construction
As developers, designers, and contractors seek to understand the evolving needs of the modular industry, no one is as well-versed in the benefits of going modular as Mārcis Kreičmanis. As the co-founder and CBDO of LAMOD in Riga, Latvia, Mārcis has made it his ultimate goal to address the inefficiencies of traditional construction.
From Furniture Builder to ‘Activist Architect’: Stuart Emmons’ Unique Journey
Stuart Emmons was fascinated by buildings at a young age. He remembers building sand cities with his brother during trips to the Jersey shore. His father gave him his first drawing table at the age of ten. Today, he is an experienced architect who received his FAIA in June 2025. The road he took is unique, to say the least.
Forge Craft Architecture + Design: Codes, Contracts, and Intellectual Property
Founding Principal and Director of Modular Practice for Forge Craft Architecture + Design, Rommel Sulit, discusses the implications of codes, contracts, and intellectual property on
modular construction.
Eisa Lee, the “Bilingual” Architect
Now as the founder of XL
Architecture and Modular Design in Ontario, Canada, she applies not just her education as a traditional architect but an entire holistic view on modular design. It’s this expansive view that guides her work on being a true partner that bridges the gap between architects and modular factories as they collaborate on the design process.
Tamarack Grove Engineering: Designing for the Modular Sector
The role of a structural engineer is crucial to the success of a modular project, from initial analysis to construction administration. Tamarack Grove offers structural engineering services — project analysis, plan creation, design creation, and construction administration — for commercial, manufacturing, facilities, public services, and modular. Modular is only one market sector the company serves but it is an increasingly popular one.
Engineer Masters the Art of Listening to His Customers
Since founding Modular Structural Consultants, LLC. in 2014, Yurianto has established a steady following of modular and container-based construction clients, primarily manufacturers. His services often include providing engineering calculations, reviewing drawings, and engineering certification
Inside College Road: Engineering the Modules of One of the World’s Tallest Modular Buildings
College Road is a groundbreaking modular residential development in East Croydon, South London by offsite developer and contractor, Tide, its modular company Vision Volumetric (VV), and engineered by MJH Structural Engineers.
Design for Flow: The Overlooked Power of DfMA in Modular Construction
Unlocking higher throughput, lower costs, and fewer redesigns by aligning Lean production flow with design for manufacturing and assembly.