2025 AOD Innovative Product Entries
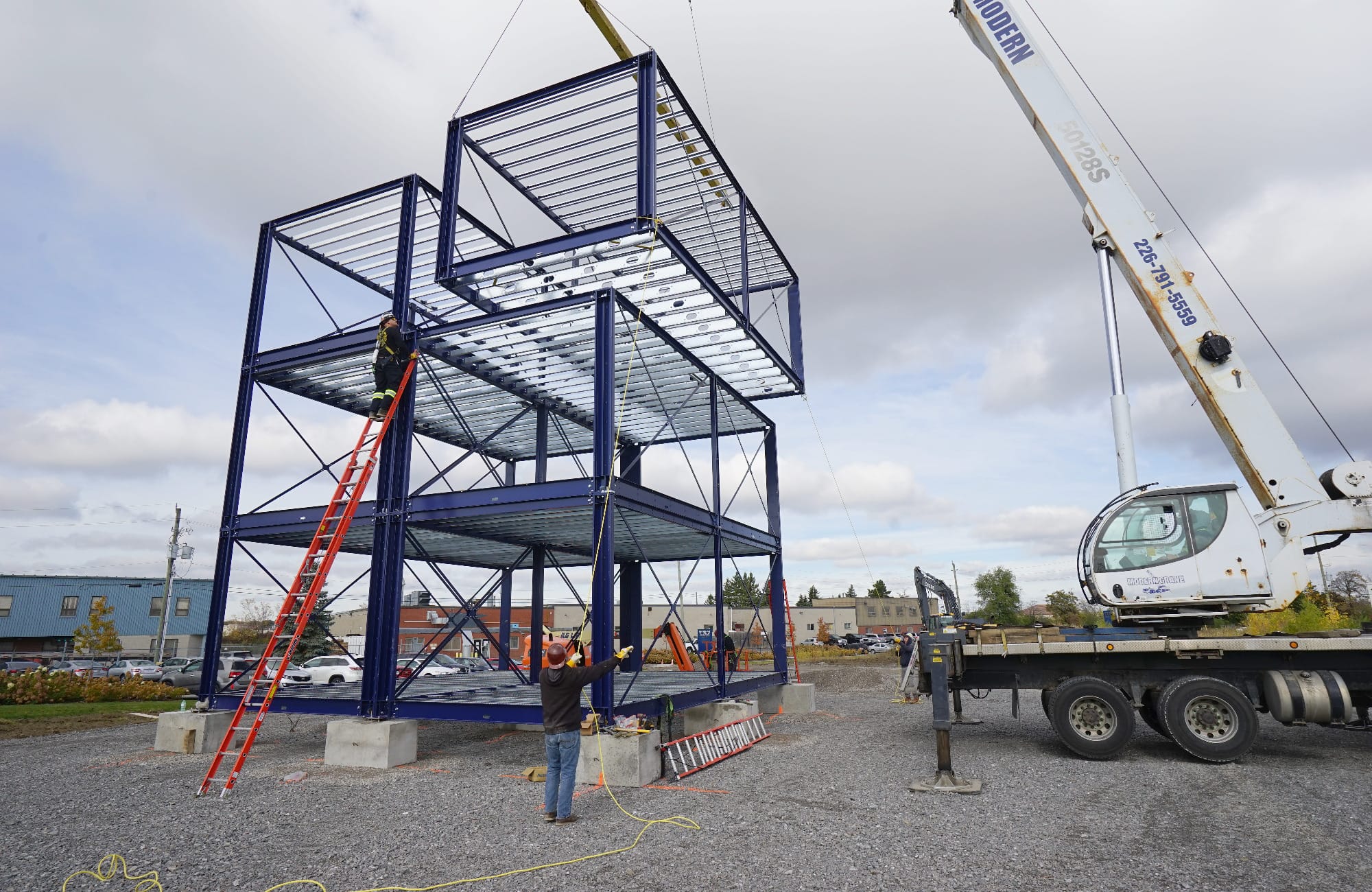
Purpose in Modular Construction
The METALOQ system is the world’s 1st integrated system for the design, fabrication and assembly of modular buildings by semi-autonomous means. All phases of the production, transportation, erection and completion of a building are accelerated by the advanced features in the METALOQ system. Manufacturing is by model controlled CNC-controlled LASER and cold forming processes, resulting in high-precision and design flexibility. Components ship to production facilities at the lowest possible cost. Modules autonomously lock and unlock from cranes, vehicles, handling systems and to each other via externally-controlled means. Modules incorporate autonomously connecting MEP systems, eliminating MEP sitework.
Innovation in Productivity, Safety, and Product Installation
The METALOQ system is advanced across all categories, achieving the lowest use of steel per square foot of built space and the least welding hours, resulting in the lowest feasible cost. Its coil-based supply chain delivers 95%+ material utilization efficiency, while high precision enables a six-sigma-capable production ecosystem supporting CNC production of subassemblies. As the first production-optimized steel frame system, METALOQ frames assemble as sub-units traveling down a wood or steel assembly line as panels, supporting multiple parallel processes and minimizing takt times. The system ships flat and assembles in less than two hours, eliminating the need for modular builders to capitalize and operate steel fabricating capability. The steerable halo, self-locking module interconnections, and autonomous MEP connections comprise the world’s first advanced building assembly system, representing a clear safety advance over conventional labor-intensive methods.
Innovation in Usability, Durability, and Cost-Effectiveness
Steel-framed systems are dramatically superior to wood in both operational durability and earthquake, fire and wind resistance.
Innovation in Sustainability
As mentioned above, the use of coil as a production feedstock, instead of the structural steel and HSS used in the majority of frames, reduces waste to the lowest possible value. Additionally, most coil produced in canada and much of what is produced in the USA is derived from scrap, and steel coming online from Algoma and Dofasco is ”Green” owing to the shift to electric melting with renewable and zero-emission electrical sources.
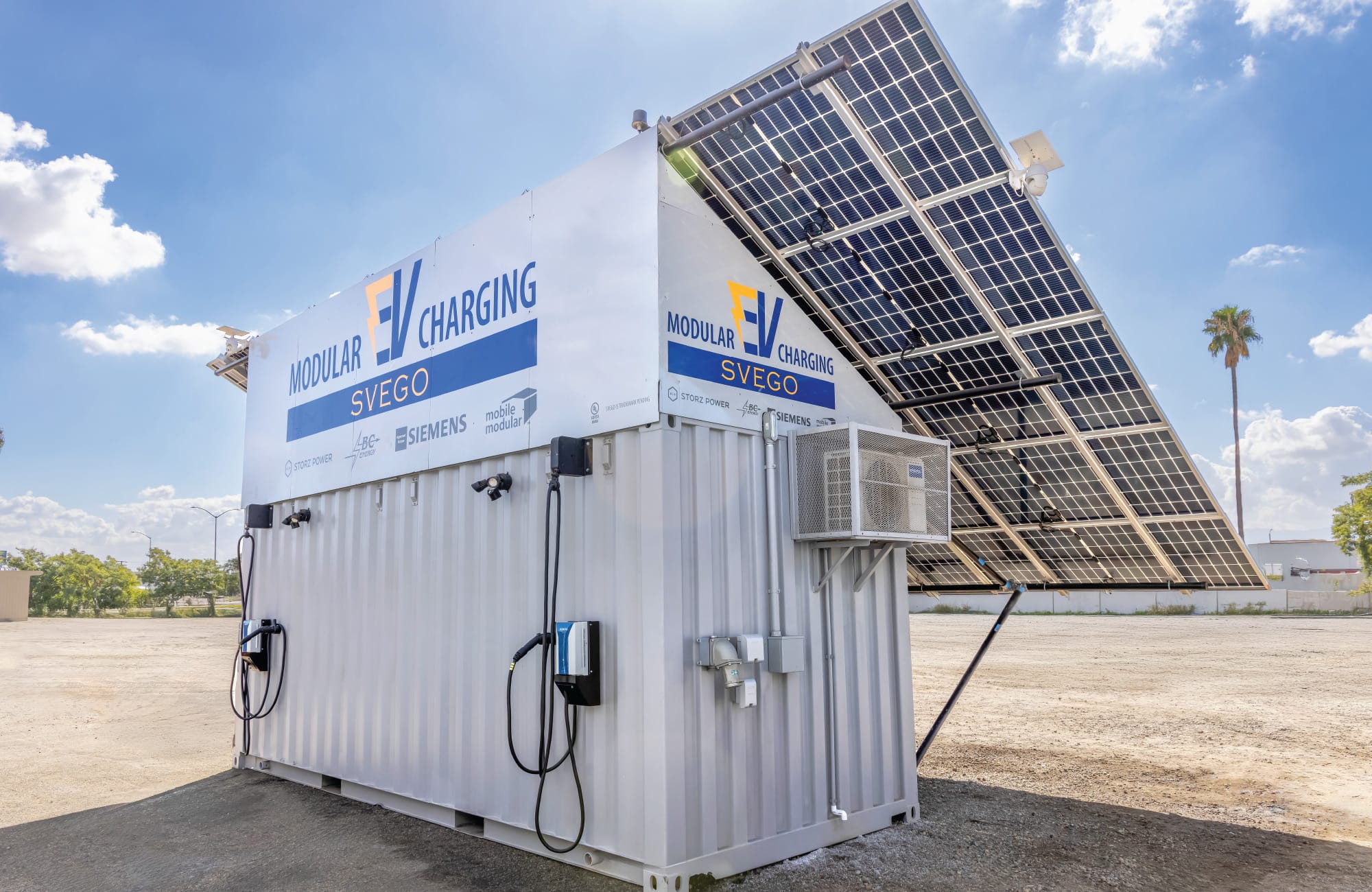
Purpose in Modular Construction
SVEGO is a modular OFF GRID Hybrid Renewable clean energy supply and Electric Vehicle charging Solution that is housed in a shipping container that can be used as a clean energy power source to put together modular units during the manufacturing process and the installation process.
Innovation in Productivity, Safety, and Product Installation
Eliminates the need for power or back up emergency power during manufacturing and/or installation processes and is not impacted by grid power outages. SVEGO provides 200 amps of green, clean renewable energy and offers Level 2 Electric Vehicle charging while meeting with wind loads up to 180 mph. It also works as its own hotspot. SVEGO also can double as a Job Shack that is temperature controlled and weather resistant.
SVEGO safety components are preinstalled prior to receipt with minimal onsite assembly. The solar installation is prepackaged within the unit and will require minimal amount of time to set up. This keeps the onsite hazardous risk exposure to a minimum.
Once the SVEGO unit is in its location within the hour it has the capabilities to be used as a power source or begin charging a vehicle. SVEGO can also supply the employees with the needed WIFI for referencing plans and drawings. Temporary or onsite modular buildings can be powered up, tested and run off of the Solution.
Innovation in Usability, Durability, and Cost-Effectiveness
SVEGO is a simple solution to a complex electrification issue. Offering drop ship 200 Amps of power anywhere in the world. A renewable clean energy hybrid power generating supply using 11.4 kWh solar as the main source of renewable energy able to charge the contained batteries inside of the unit. Solution has many features including, a climate-controlled interior, 72-hour reserve, two Siemens Level 2 electric vehicle chargers, 20’ x 10’ footprint, relocatable, and works in temperatures from 0 – 130 degrees, built in generator assist connection, 110 v outlet, and 50-amp plug.
The longevity is contained inside of a shipping container. The container unit can withstand up to 180 MPH wind loads which allow the drop shipping of the 200 Amps of power to anywhere in the world. In 2 hours, the fully relocatable SVEGO can be demobilized. SVEGO is a cost-effective Solution providing a hybrid solution of clean green energy which results in saving valuable dollars in the short term and long run.
Innovation in Sustainability
SVEGO is as an OFF-GRID hybrid renewable self-sustained power source and electric vehicle charging Solution. SVEGO has the capability to relocate with a minimal effort, be located in locations of up to 180 MPH wind loads where there is little to no infrastructure in place and is ready provide power and electric vehicle charging services.
SVEGO can supplement or replace generators in the emergency and electrification plans. Resulting in cleaner energy, less fossil fuels being used, reuseable containers, from a clean manufacturing provider.
As the Country and World go to cleaner energy and look for Solutions, SVEGO will be a leader in the Clean Energy Leasing Movement and will be adaptable as the technology changes and as the geography changes, by using the existing base model units and upgrading as technology changes, scaling where needed, and relocating as the pain points change in location with the improvements of infrastructure.
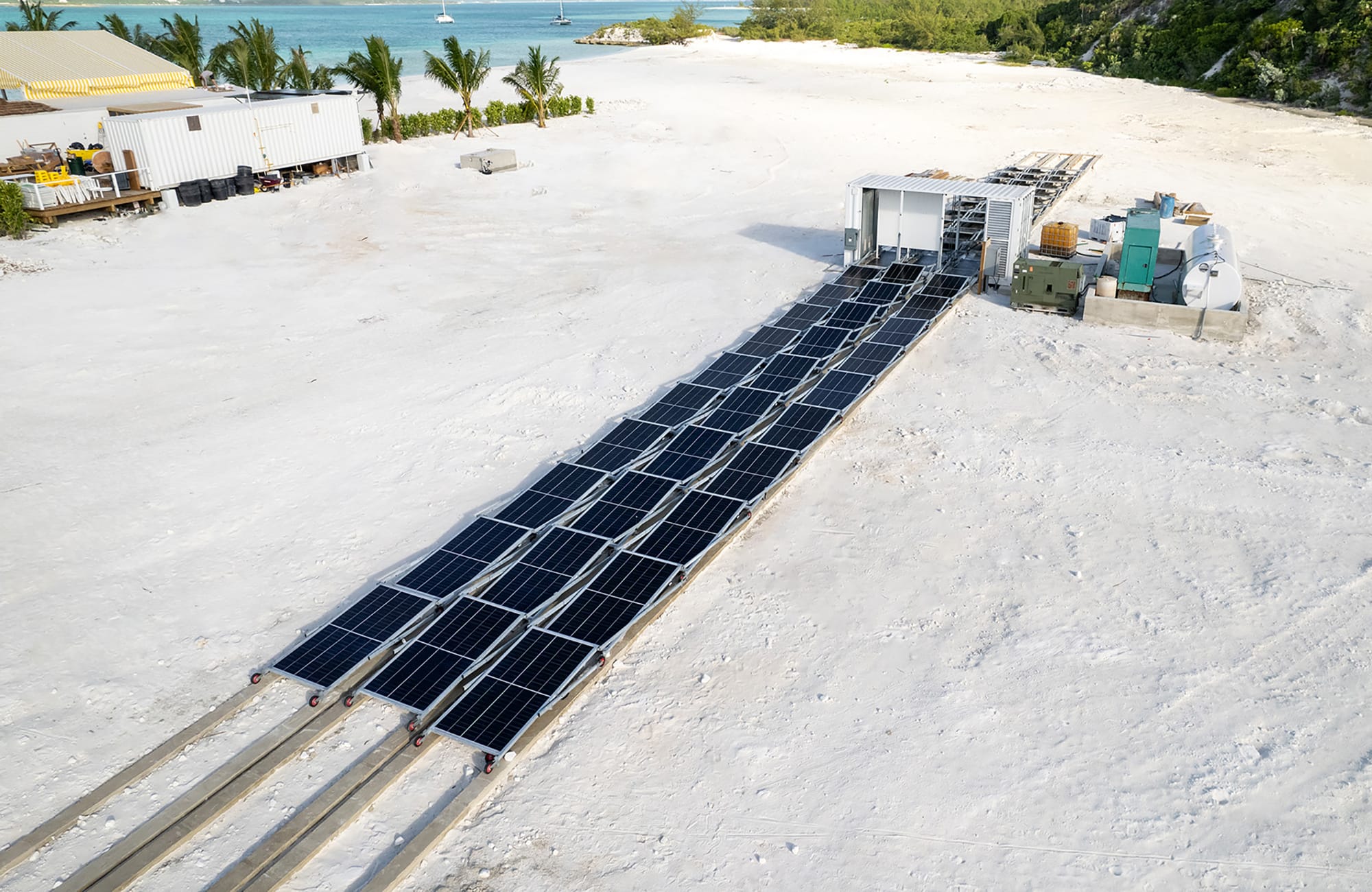
Purpose in Modular Construction
The Solarator™ Fold-Out 60+ kW is a solar-powered renewable generator with a deployable microgrid and battery bank, providing continuous power 365 days a year, 24/7. Built out of new 20’ shipping containers, this generator is designed for sites that are remote and need secure power. Each unit is transportable, securable, and can be fully customized to a customer’s specific needs, including hybrid and microgrid compatibility. An optional and redundant (bio)diesel generator offers backup power to ensure an uninterrupted power supply.
Typically, a Solarator™ can power numerous modular buildings, such as several ground-level offices and/or workforce housing structures.
Innovation in Productivity, Safety, and Product Installation
Installation: The Solarator™ is easily transportable by road, rail, or sea, and can be deployed in remote, regional, and urban environments based on a customer’s demand and energy requirements.
The Solarator™ can be rapidly deployed by 1 to 2 individuals within 30 minutes.
The fold-out solar array can be quickly closed during harsh weather conditions and then quickly redeployed once the storm passes.
Safety: The Solarator™ provides a safe, clean, and secure solar-powered alternative to standard diesel generators.
Productivity: The Solarator™ eliminates diesel fuel requirements from sites, saving teams a considerable amount of time and energy - especially as diesel fuel costs rise. Once the unit is deployed, the customer can expect continuous power, 365 days a year, 24/7, with minimal maintenance required.
All Solarators® utilize real-time data and performance tracking to produce CO2 & cost-saving reports, and can be remotely monitored and controlled.
Innovation in Usability, Durability, and Cost-Effectiveness
Built out of a new corten steel 20’ shipping container, our Solarators are as durable as they get. The corrugated walls provide additional strength and rigidity, enabling the container to easily handle all weather conditions, which are often found in many of the harsh environments in which these units are placed.
The fold-out solar array can be quickly closed during harsh weather conditions and then quickly redeployed once the storm passes, allowing our customers to protect the solar arrays and racking system inside the durable container. The built-in battery bank allows the unit to continue providing power to the site even while the solar arrays are packed up.
Solarators enable businesses and communities to save significantly on fuel and operating costs (compared to diesel alternatives). The ROI of a Solarator compared to diesel alternatives is typically around 18-24 months.
Real-time carbon emission data & reporting help firms easily conform to ESG and CSR goals & requirements.
Innovation in Sustainability
The Solarator™ meets the emission standards set by the EPA to be classified as a Tier III and Tier IV generator.
Our HELIOS Solarator™ solutions are 100% U.S.-made, something that is becoming rarer in the solar & sustainability industries.
The mission of our HELIOS Solarator™ product range is clear: to replace diesel-generated power. Since our Solarator™ renewable generators are 100% solar-powered renewable energy systems, these products eliminate the need for diesel, therefore significantly reducing our customers’ emission outputs.
Our Solarator™ products offer a reliable replacement for diesel generators & diesel reefer containers, which are extremely common in many industries where our Solarators™ are found, including (but not limited to): Infrastructure & Construction, Mining, Government, Defense, Aid & Development, Agriculture, Aquaculture & Fisheries, and Events.
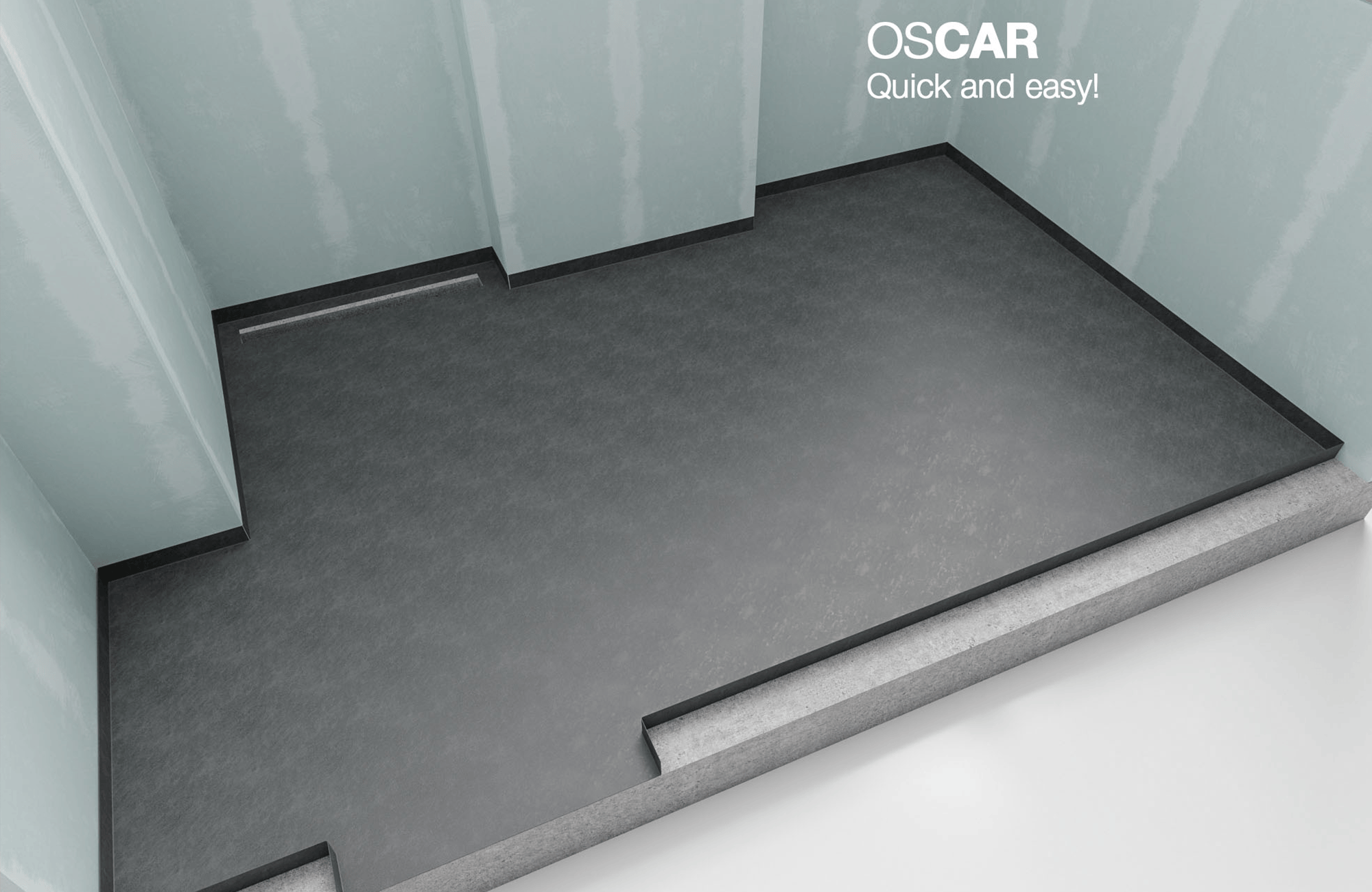
Purpose in Modular Construction
OSCAR (One Seal CollAR) is a tailor-made, all-in-one waterproofing solution for prefabricated bathroom modules. Instead of waterproofing by using sheet membranes, tapes, and accessory items, it is now possible to seal the entire floor, including the wall-to-floor joints and corners, with only one piece of waterproof membrane. This solution is unique and patented.
Innovation in Productivity, Safety, and Product Installation
Because it is only one piece of waterproofing membrane, there are no overlaps. This reduces the risk of water leakages tremendously, as the overlapping areas are usually the most critical. It is almost impossible for applicators to make any mistakes with this system.
Innovation in Usability, Durability, and Cost-Effectiveness
Oscar saves time during installation, as there is no cutting or any other preparation necessary. Secondly, because it’s easy to use and it is almost impossible to make any mistakes, it can be installed even by unskilled workers. It comes precut and tailor-made, according to the dimensions of the bathroom module, and can simply be fixed with tile adhesive. There is no waterproof adhesive necessary (which would need time to dry), so tiling can start immediately after installation.
Innovation in Sustainability
It is tailor-made and will fit perfectly into the module, so there won’t be any waste material, as there would be when using a conventional waterproofing system.
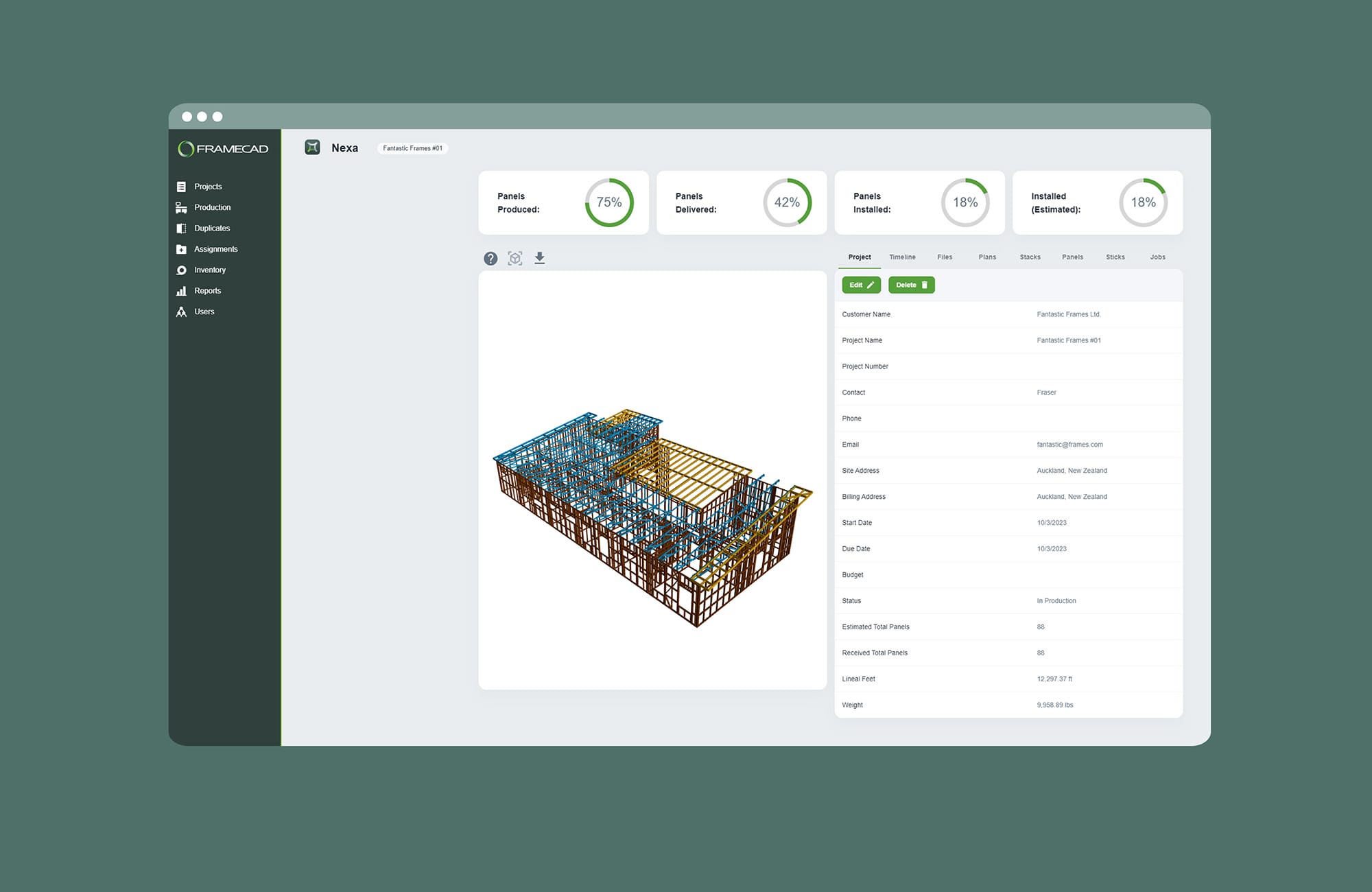
Purpose in Modular Construction
Part of the FRAMECAD end-to-end steel framing system, Nexa is the first production management platform designed specifically for cold-formed steel (CFS). With Nexa’s centralized platform, modular manufacturers and contractors benefit from visibility to production scheduling and monitoring, traceability of materials and better coordination through a continuous, real-time flow
of project data from the factory to the jobsite.
With a single platform for project management, factory operations and jobsite efficiency, manufacturers can deliver projects faster, with less waste and more predictability. Nexa provides visibility for seamless communication and collaboration with contractors and owners, building trust from start to finish.
Nexa includes a free, entry-level version that allows production-ready files to be brought into the FRAMECAD manufacturing process from any design software.
Innovation in Productivity, Safety, and Product Installation
FRAMECAD’s precision-manufactured cold-formed steel (CFS) frames enable faster assembly and simultaneous site preparation. Because they are manufactured with precision, FRAMECAD CFS modular panels and components are easy to assemble and come together seamlessly with less reliance on expensive skilled labor required in the factory and on site.
With Nexa, the FRAMECAD system accelerates project completion by up to 50 percent so that buildings can be sold and occupied faster.
Nexa streamlines workflows and resource management, reducing downtime and maximizing productivity on the jobsite. Manufacturers can pre-plan stacking and packing processes and coordinate and stage deliveries to optimize logistics and minimize delays. The Nexa mobile app allows field workers to access project drawings and models for accurate, fast assembly with minimal labor resources.
Innovation in Usability, Durability, and Cost-Effectiveness
Until now, cold-formed steel manufacturers had to rely on numerous disconnected solutions to manage their operations, resulting in a lack of visibility into project progress, ineffective communication and time-consuming, costly processes. By unlocking access to critical data, Nexa reduces waste, eliminates inefficiencies and rework and minimizes the need for onsite labor – which lead to more profitable construction. Nexa provides real-time insights and analytics that empower modular manufacturers to make data-driven decisions, understand performance and plan for growth.
Additionally, CFS framing ensures resistance to mold, rot, termites and fire, for durability that translates into reduced long-term maintenance costs. CFS’ resilience is particularly beneficial as climate events increase and residential construction projects become challenging to insure. FRAMECAD systems output durable structures that resistant to the elements and require less maintenance over time.
Innovation in Sustainability
Made from the most recycled material on earth, the FRAMECAD framing system utilizes cold-formed steel, an eco-friendly choice that generates 0% waste to landfills. The FRAMECAD system’s manufacturing techniques enable accurate and custom fabrication of components, which reduces waste and optimizes material usage. The design-led process and precision manufacturing of CFS framing components minimize waste and allow for a more sustainable construction process with lower material costs.
CFS structures are highly energy-efficient, reducing environmental impact over their lifespan. The durability of CFS ensures long-term sustainability by requiring fewer repairs or replacements. This resilience reduces resource consumption and helps buildings maintain their performance for decades.
Additionally, steel is 100% recyclable and can be repurposed to create new structures, contributing to a circular economy and reducing the need for new raw materials.
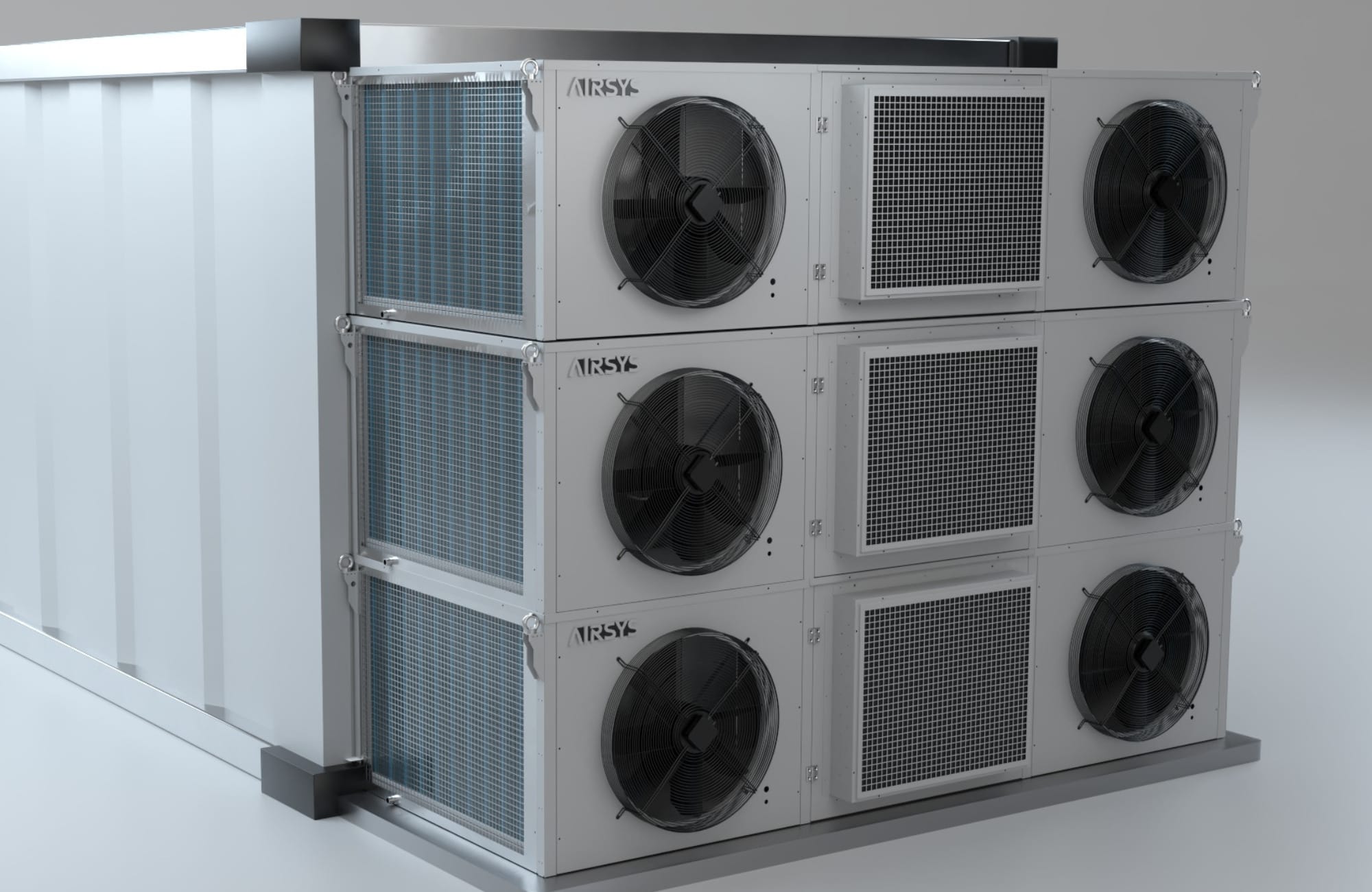
Purpose in Modular Construction
The AIRSYS UniCool™ Edge is designed to provide efficient cooling for modular buildings, ensuring optimal performance for temperature-sensitive equipment like telecom hardware and IT systems. In the design phase, its stackable and scalable design allows for flexible integration into various modular environments, accommodating cooling needs from 7kW to 240kW. During manufacture, its compact, energy-efficient cooling system is pre-fabricated and tested for quick deployment. The transportation process is streamlined thanks to its modular structure, with up to six units easily connected to a single control panel. For installation, the UniCool™ Edge is designed for rapid setup, using a plug-and-play system that requires minimal tools, reducing downtime. Its outdoor wall-mounted package frees up space, and integrated free cooling and VFD technology ensure sustainable, cost-effective operation, making it an ideal solution for cooling in modular telecom stations, data centers, and more.
Innovation in Productivity, Safety, and Product Installation
Productivity: Its stackable, compact design maximizes space and allows for efficient deployment of multiple units. The energy-efficient system ensures powerful cooling with minimal energy consumption, improving operational efficiency in telecom stations and data centers.
Safety: The UniCool™ Edge protects temperature-sensitive equipment from overheating, preventing potential damage and ensuring long-term reliability. Its durable construction ensures safe transport and installation, minimizing risk during handling.
Installation: Designed for quick, hassle-free setup, the UniCool™ Edge integrates easily into existing systems without specialized infrastructure. Its flexible design allows for seamless deployment in remote or time-sensitive locations, reducing downtime and improving operational efficiency.
Innovation in Usability, Durability, and Cost-Effectiveness
The AIRSYS UniCool™ Edge offers innovative usability, durability, and cost-effectiveness. Its stackable, scalable design accommodates 7kW to 240kW cooling loads and rack densities up to 20kW. With up to six units connected to a single intelligent control panel, it allows seamless deployment in modular environments. The compact, wall-mounted outdoor package frees up interior space for more servers, and the pre-fabricated rapid deployment package ensures quick installation. Built with high-quality components, the UniCool™ Edge guarantees 24/7/365 operation, offering proven reliability and uptime for mission-critical applications. Its energy-efficient design and integrated free cooling minimize operational costs, and its green cooling technologies reduce environmental impact. The system also lowers utility rates through fewer on/off cycles, extending product lifespan. Scalable, space-efficient, and eco-friendly, the UniCool™ Edge offers long-term savings while ensuring optimal performance
Innovation in Sustainability
The AIRSYS UniCool™ Edge offers innovative usability, durability, and cost-effectiveness. Its stackable, scalable design accommodates 7kW to 240kW cooling loads and rack densities up to 20kW. With up to six units connected to a single intelligent control panel, it allows seamless deployment in modular environments. The compact, wall-mounted outdoor package frees up interior space for more servers, and the pre-fabricated rapid deployment package ensures quick installation. Built with high-quality components, the UniCool™ Edge guarantees 24/7/365 operation, offering proven reliability and uptime for mission-critical applications. Its energy-efficient design and integrated free cooling minimize operational costs, and its green cooling technologies reduce environmental impact. The system also lowers utility rates through fewer on/off cycles, extending product lifespan. Scalable, space-efficient, and eco-friendly, the UniCool™ Edge offers long-term savings while ensuring optimal performance
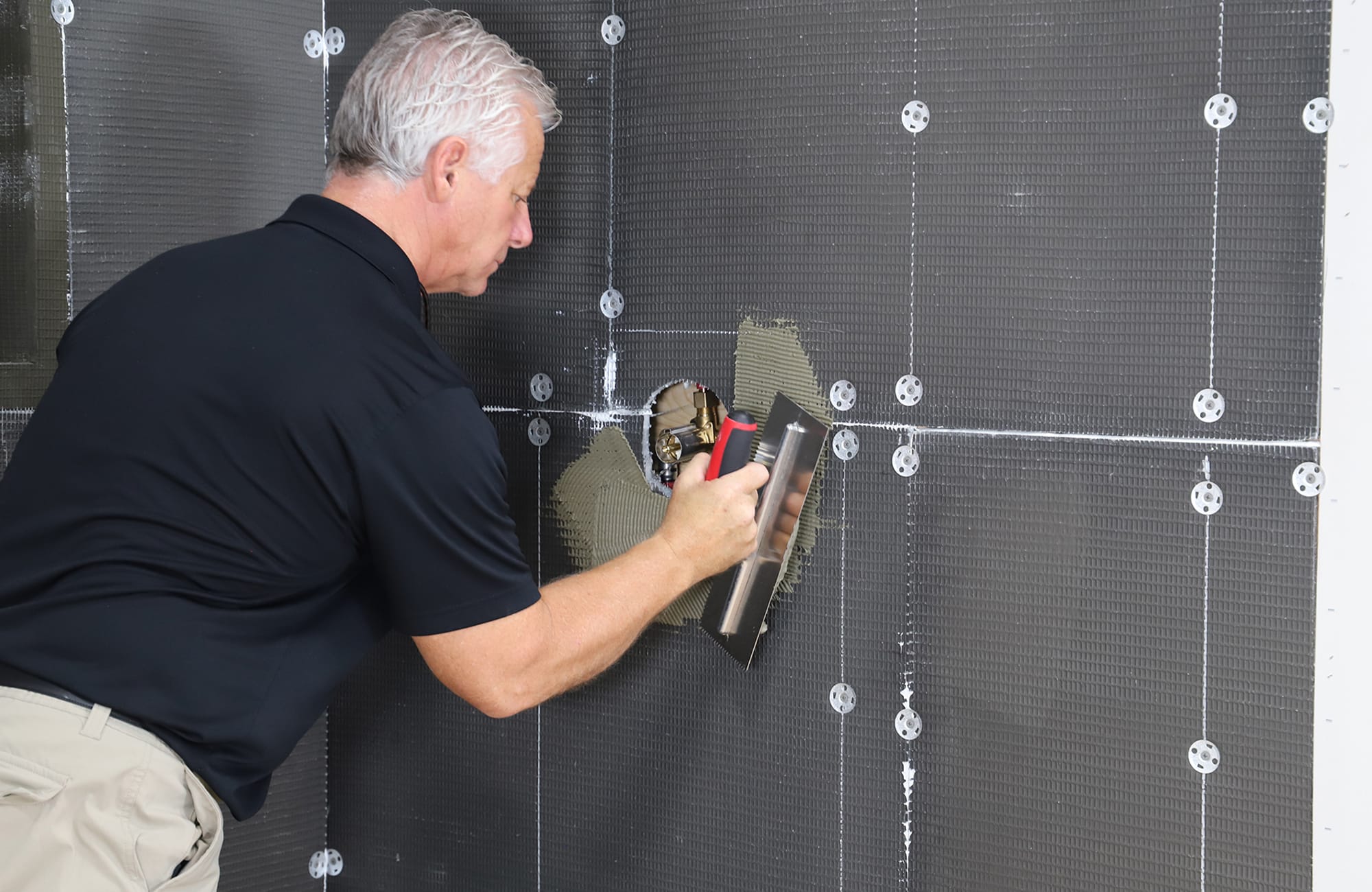
Purpose in Modular Construction
The ARDEX TLT™ Shower Systems provide a simple, all-in-one solution that sets new standards. The System can be installed easily, quickly, and securely. Leveraging sophisticated technology and high-quality materials, modular manufacturers can offer shower systems which provides both high durability and excellent sealing properties.
The highly rigid structure of the ARDEX TLT™ Building Panels include a strong, lightweight, waterproof and vapor-resistant tile base for wet areas, while the pre-sloped, waterproof shower bases are designed with a patent pending, built-in drain assembly, making tiled shower installations quicker and easier than traditional installations.
Innovation in Productivity, Safety, and Product Installation
Conventional construction practices for shower systems are time and labor-intensive, often requiring the building of custom shower pans, sloping and contouring with cement mortars; hand-applied waterproofing in multiple coats; the associated dry time in hours or days of these wet processes; the use of cement backer boards which are difficult to install, heavy and dusty. Such legacy means and methods often require highly skilled labor which may not be available in today’s market. Furthermore, the various components are sourced from multiple vendors with no system compatibility or warranty.
ARDEX TLT™ Shower Systems offer engineered assemblies with inherently waterproof, XPS building panels and prefabricated shower pans which have revolutionized the tile installation process. With multi-layer waterproof protection and various drain shapes, sizes, and colors to choose from, ARDEX TLT™ Shower Systems are designed for faster and easier installation while significantly improving performance.
Innovation in Usability, Durability, and Cost-Effectiveness
ARDEX TLT™ Shower Systems provide a solution to what can be a challenging and complicated process. Shower installations often require multiple components and suppliers, resulting in a time-consuming and confusing process.
ARDEX TLT™ Shower Systems offer pre-waterproofed system components, a patented, integrated drain assembly including the ARDEX Tile & Stone installation products, and a SystemOneTM warranty of up to 25 years!
Innovation in Sustainability
Optimal procurement process
Minimizes waste
Energy efficient
Process reduces noise, dust and debris
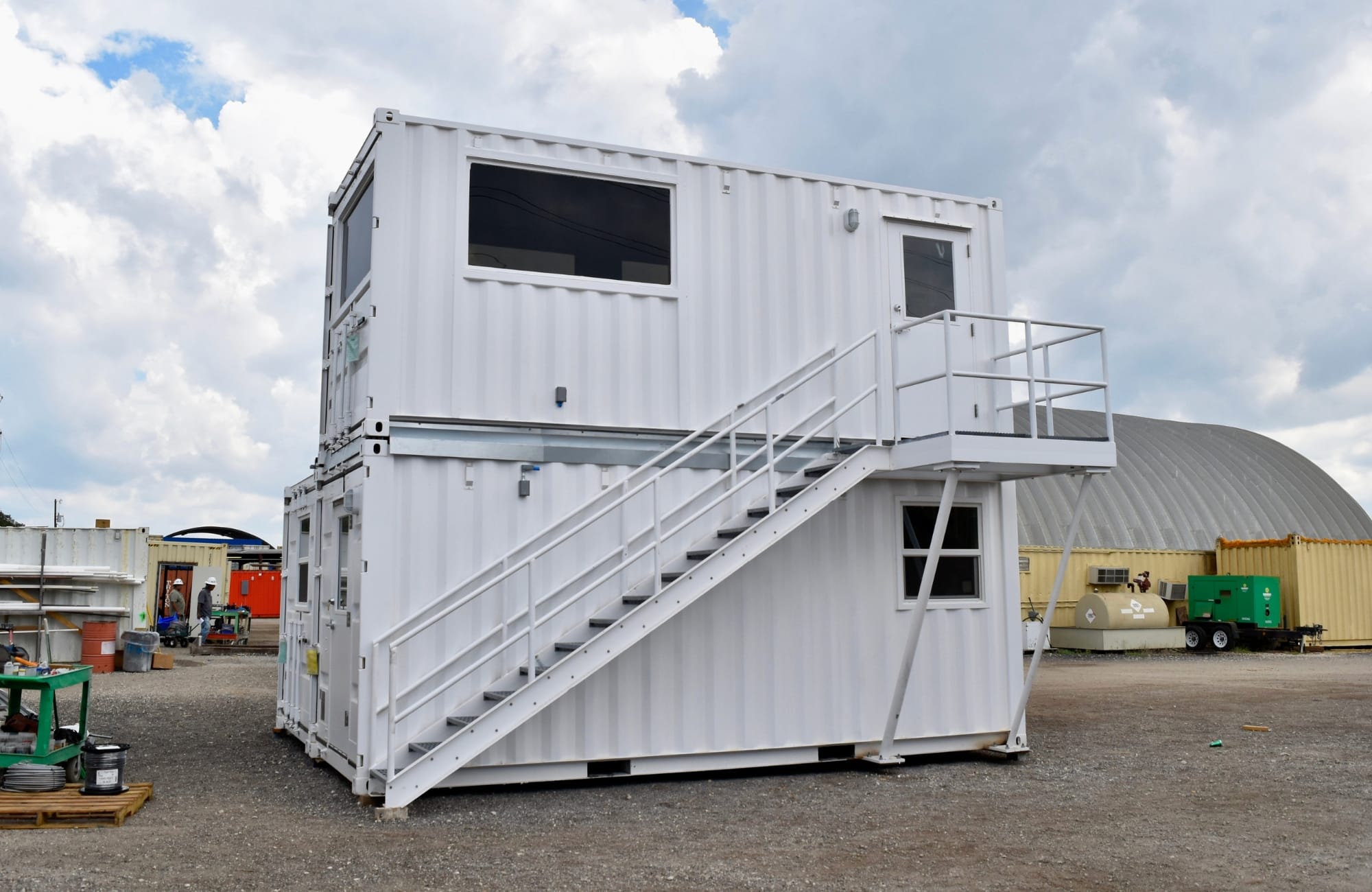
Purpose in Modular Construction
The observation stairs and platform provide access to the second-story container workspace without permanent installation methods. Designed to be independent from the ground, the platform and stairs are supported by bolted posts anchored to the bottom container, eliminating the need for special foundations, site welding, or digging.
This assembly is manufactured to be disassembled as needed for a sand mining operation in the Permian Basin, prioritizing ease of transportation and relocation. Instead of relying on permanent welds, the design uses bolted connections. This allows the system to break down into four main components: platform, steel grating, stairwell, and support posts.
Falcon’s in-house hot works team took on the fabrication. By avoiding outsourcing, they maintained quality control and streamlined production. Ultimately, this helped the team meet project deadlines while delivering a product designed for durability, transportability, and easy assembly on a remote jobsite.
Innovation in Productivity, Safety, and Product Installation
The observation stairs and platform showcase ingenuity in productivity, safety, and installation efficiency for modular workspaces. Certified by a structural engineer as OSHA-compliant, the design ensures worker safety in demanding industrial environments. The customer shared that once installed onsite in the sand hills of west Texas, their company foreman climbed to the platform, bounced a few times, and nodded appreciatively at its stability.
Designed for productivity, the assembly meets the customer’s need for a fully relocatable workspace. Unlike permanent structures, it can be taken apart and moved with the container workspace, ensuring no assets are left behind during site relocation.
Falcon Structures developed a detailed four-page installation manual, empowering the customer to assemble the components onsite without expert guidance. Future relocations will only require a forklift or crane operator, rather than welders or a full construction crew.
Innovation in Usability, Durability, and Cost-Effectiveness
Steel, galvanized steel, and stainless steel comprise the stairs and platform, including the fasteners, bolts, washers, and tread. The all-steel components are designed to thrive in rugged industrial environments where the assembly will face frequent foot traffic, heavy loads, and the arid and windy climate.
Part of the reason the customer chose the self-supported stairs and platform was for long-term cost-effectiveness. Their mining site is temporary, and they didn’t want to invest in permanent build measures only to abandon them later. Rather, they opted for this uniquely transportable yet durable fixture to streamline their site setup and teardown efforts.
Innovation in Sustainability
The observation stairs and platform contribute to sustainability by offering a reusable, transportable solution that eliminates the waste associated with permanent installations. Constructed from steel, the materials are long-lasting and won’t wear down from weather, which reduces the need for frequent part replacement or maintenance.
True to its modular design, the structure can be disassembled and relocated as needed to use across multiple mining sites. By avoiding permanent construction with its concrete foundations and notorious waste output, the stairs and platform reduce environmental disruption and wasted materials during setup and teardown.
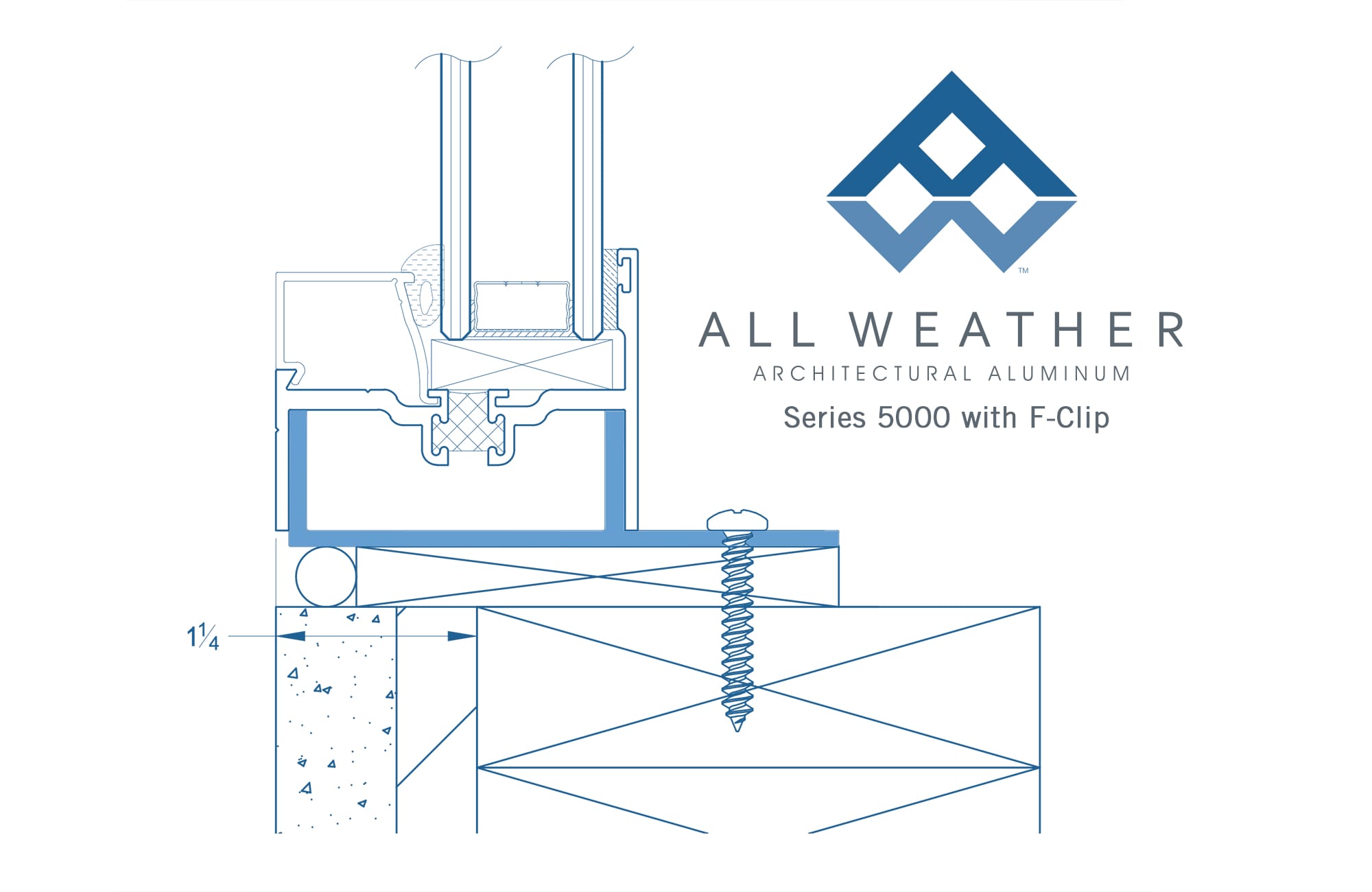
Purpose in Modular Construction
Each installation comes with its own set of challenges and All Weather’s Series 5000 F-Clip provides a unique and innovative installation solution for our modular customers.
All Weathers proprietary F-Clip is an extruded aluminum accessory piece for our equal leg window frame for the Series 5000 window that can be used for new construction or retrofit applications offering greater flexibility.
All Weather’s F-Clip allows a fully glazed window to be positioned in multiple positions including the front, center or back, not just the front which is typical of nail fin applications. Using the F-Clip can mimic a storefront / Hollow metal look with its ability to install a fully glazed window and/or window wall system while reducing costs by eliminating the need to field glaze glass. All Weather’s innovative F-Clip allows for ease of installation, reduction in costs and greater flexibility.
Innovation in Productivity, Safety, and Product Installation
All Weather’s F-Clip allows a fully glazed window to be positioned in multiple positions including the front, center or back, not just the front which is typical of nail fin applications. Using the F-Clip can also mimic a storefront /hollow metal look with its ability to install a fully glazed window and/or window wall system without the need for field glazing.
Innovation in Usability, Durability, and Cost-Effectiveness
All Weather’s Series 5000 with F Clip significantly reduces labor and material costs while decreasing the installation lead time by eliminating the need to field glaze window wall systems.
Innovation in Sustainability
Since the F Clip is made of an aluminum extrusion, it’s lightweight, energy-saving, durable, recyclable and the sustainable material of choice.
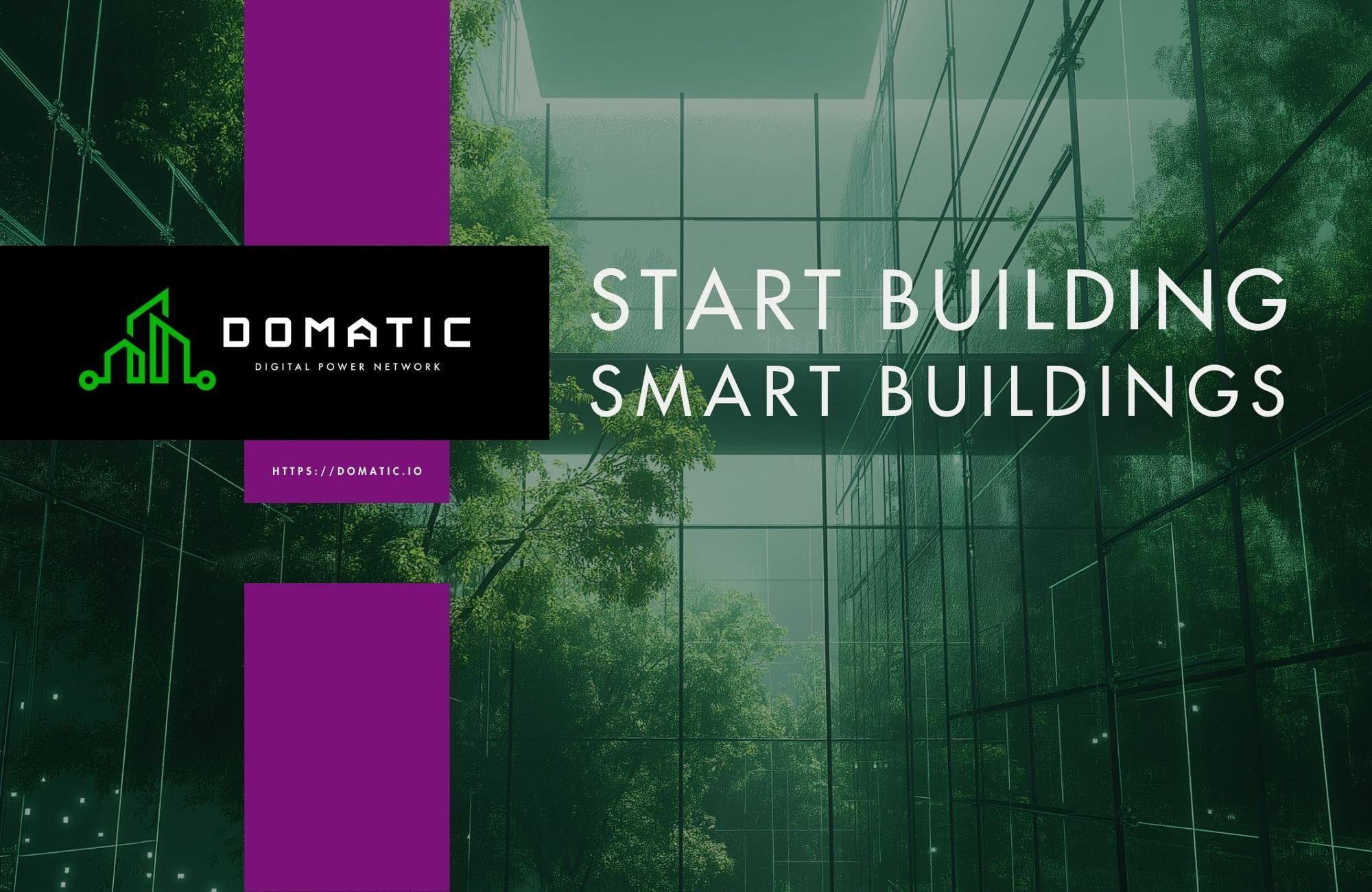
Purpose in Modular Construction
By combining low-voltage power distribution with a plug-and-play smart building network, Domatic lets builders realize smarter, better buildings for no added cost over traditional line voltage wiring.
Typical ”smart building” projects are beset with massive IT costs. Because Domatic is a plug-and-play system, no IT skills are required to install and configure any of the equipment, and these benefits accrue to both builders and owners.
Domatic makes it finally possible to create smart buildings without having to accept the high levels of cost and technical complexity that plagues the industry today.
Innovation in Productivity, Safety, and Product Installation
Domatic’s low-voltage (NEC Class 2) approach is inherently safe from fire and shock hazards, and as a result builders benefit from a reduced code regime. The elimination of 90% of the copper needed to wire the fixtures means not only material savings, but also faster installation because the 18AWG wires are easier to pull and terminate than Romex, and much simpler than running conduit or metal-clad for buildings that would require it. And because it’s a smart system, there are no switch-legs or three-way runners to install, which significantly reduces errors during installation.
In the factory, each module can be independently tested to verify correct installation, and for a multi-module unit design, a single connection can be made after the modules are set to finish the installation. No additional configuration on-site is needed.
All-told, the savings in factory time, materials, and labor yield a net savings versus all line-voltage, while enhancing the value of the final product.
Innovation in Usability, Durability, and Cost-Effectiveness
Domatic-enabled fixtures implement standard device classes, much the same way USB devices do, so installation requires no provisioning. As with USB, where plugging a webcam into a computer is automatic and requires no IT skills, Domatic devices auto-configure when they are connected.
By lowering the cost of installing components, builders are at liberty to add additional sensors that help them monitor the performance of the building over time, confirming the ROI on expected improvements.
And cost savings are yielded not only during installation, but also over the life of the building, because building managers benefit from sensors that alert them to faults that need attention, and the low-voltage nature of Domatic means normal maintenance staff can replace fixtures as needed.
Innovation in Sustainability
Copper has become a precious resource itself, and Domatic eliminated 90% of the copper required for powering fixtures.
Being a DC power system, Domatic fixtures are more efficient than line-voltage equivalents, anywhere from 10-30% improvement.
More importantly, by leveraging sensors to manage building energy use, ongoing energy savings of 30-60% can be realized by making building operations adaptive to building usage.